- お役立ち記事
- Multiphysics Analysis: A New Method for Manufacturing Process Optimization
月間76,176名の
製造業ご担当者様が閲覧しています*
*2025年3月31日現在のGoogle Analyticsのデータより
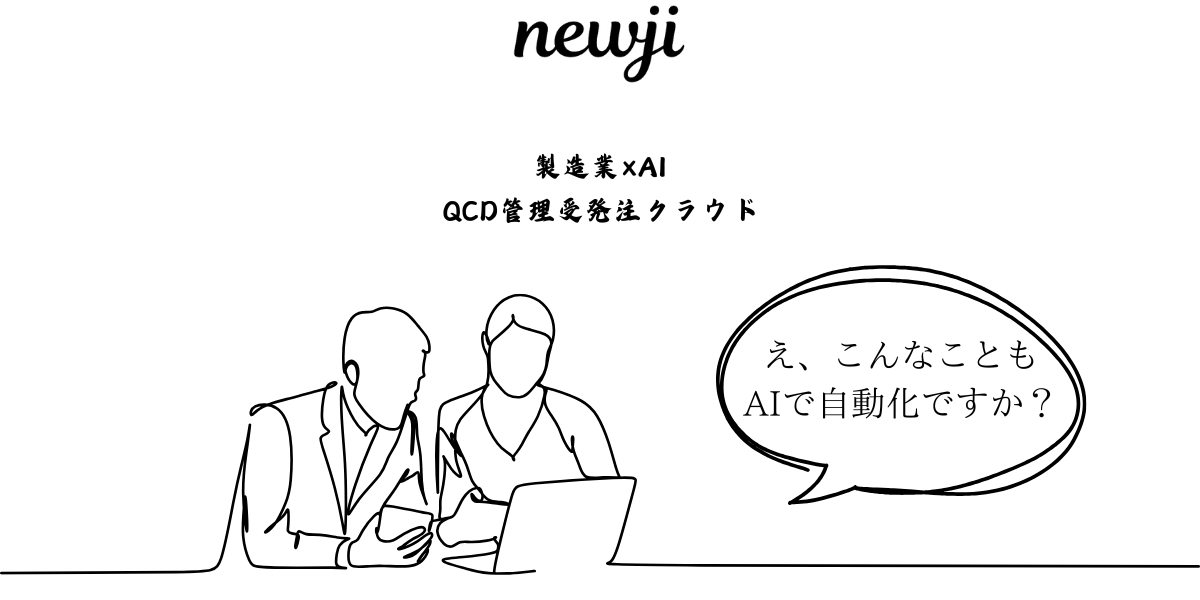
Multiphysics Analysis: A New Method for Manufacturing Process Optimization
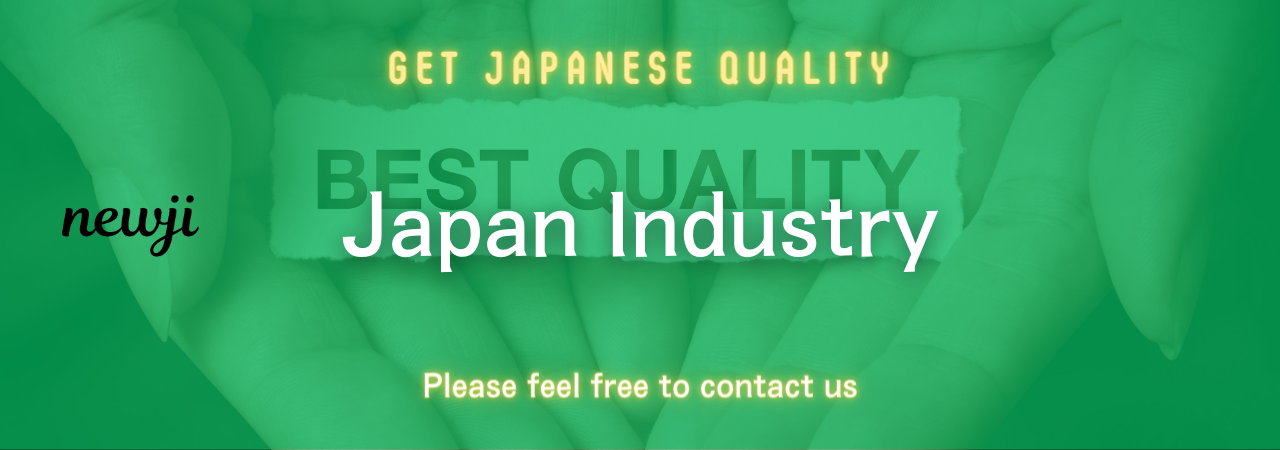
In the world of modern manufacturing, optimizing processes is key to ensuring efficiency, quality, and cost-effectiveness.
One innovative approach in achieving these goals is through multiphysics analysis.
This method involves the study and simulation of multiple physical phenomena simultaneously.
The new method is revolutionizing the way industries approach problem-solving and product development.
目次
Understanding Multiphysics Analysis
What is Multiphysics Analysis?
Multiphysics analysis is a computational technique that allows engineers and scientists to model and simulate different physical interactions within a system.
These physical interactions could include thermal, structural, fluid, and electromagnetic phenomena.
By considering all relevant physical factors, multiphysics analysis provides a more comprehensive understanding of a system’s behavior under various conditions.
Traditionally, engineers would analyze these phenomena separately.
However, real-world scenarios often involve complex interactions between different physical fields.
Multiphysics analysis bridges this gap by integrating these interactions into a single simulation framework.
This holistic approach yields more accurate and reliable results.
Why is Multiphysics Analysis Important?
In manufacturing, the optimization of processes is crucial for improving product quality, minimizing waste, and reducing production costs.
Multiphysics analysis plays a significant role in achieving these objectives.
1. **Increased Accuracy:** By considering multiple physical interactions, multiphysics analysis provides more accurate simulations compared to single-physics approaches.
This accuracy is essential for predicting the behavior of complex systems.
2. **Cost Reduction:** Accurate simulations can reduce the need for physical prototypes and extensive testing.
This leads to significant cost savings and shorter development cycles.
3. **Improved Product Quality:** With a deeper understanding of how different factors affect the manufacturing process, engineers can make better-informed decisions.
This results in higher-quality products and fewer defects.
Applications of Multiphysics Analysis in Manufacturing
Design and Development
During the design phase, engineers can use multiphysics analysis to simulate how a product will perform under various conditions.
For example, in the automotive industry, a car engine must withstand thermal, mechanical, and fluid dynamics forces.
By simulating these interactions, engineers can optimize the engine’s design for better performance and durability.
Process Optimization
Manufacturing processes often involve multiple stages, each affecting the final product’s quality.
Multiphysics analysis can help optimize these stages by analyzing the interplay between different physical factors.
For instance, in metal casting, temperature distribution, fluid flow, and solidification processes must be precisely controlled.
Simulating these factors together ensures a defect-free final product.
Failure Analysis
Understanding why a product fails is crucial for improving future designs.
Multiphysics analysis helps identify the root causes of failures by simulating different stressors and environmental conditions.
For example, in electronic devices, thermal and mechanical stresses can lead to component failure.
By analyzing these stresses together, engineers can pinpoint weaknesses and enhance product reliability.
Quality Control
Maintaining consistent quality in manufacturing is essential.
Multiphysics analysis enables real-time monitoring and control of manufacturing processes.
By simulating the entire process, engineers can identify potential issues and make adjustments before they lead to defects.
This proactive approach ensures high-quality outputs and reduces waste.
Implementing Multiphysics Analysis
Choosing the Right Software
Several software tools are available for multiphysics analysis, each with its strengths and weaknesses.
Selecting the right software depends on the specific needs of the manufacturing process.
Popular options include ANSYS, COMSOL Multiphysics, and Autodesk CFD.
These tools provide a range of simulation capabilities, from basic to advanced, allowing engineers to choose the level of complexity they require.
Integrating Data
Successful multiphysics analysis relies on accurate data from various sources.
Integrating data from different physical domains (thermal, structural, fluid, etc.) is essential for precise simulations.
Manufacturers should invest in robust data acquisition systems to gather reliable inputs for their simulations.
Collaborative Approach
Multiphysics analysis often requires collaboration among experts from different disciplines.
For instance, a thermal engineer might need to work with a structural engineer to simulate the thermal stresses on a component.
Encouraging interdisciplinary collaboration ensures comprehensive analysis and better optimization of manufacturing processes.
Validation and Testing
While simulations provide valuable insights, validation through physical testing is still necessary.
Comparing simulation results with actual test data helps identify any discrepancies and refine the simulation models.
This iterative process enhances the accuracy and reliability of multiphysics analysis.
Challenges and Future Trends
Challenges
Implementing multiphysics analysis comes with its set of challenges.
Complex simulations require significant computational power, which can be expensive.
Another challenge is the integration of data from various sources, which requires meticulous planning and execution.
Additionally, ensuring collaboration between different disciplines can sometimes be difficult, especially in large organizations.
Future Trends
Despite the challenges, the future of multiphysics analysis is promising.
Advancements in computing power and software capabilities are making simulations faster and more accessible.
The rise of artificial intelligence (AI) and machine learning (ML) is also expected to enhance multiphysics analysis.
AI and ML can help automate the process of data integration and simulation, making it easier for engineers to obtain accurate results.
Another trend is the use of cloud-based platforms for multiphysics analysis.
These platforms offer scalable computing resources, reducing the need for expensive hardware.
They also facilitate collaboration by providing a centralized repository for simulation data and results.
In conclusion, multiphysics analysis represents a significant advancement in manufacturing process optimization.
By considering multiple physical interactions, it provides more accurate and reliable simulations, leading to improved product quality, cost savings, and efficiency.
As technology continues to evolve, the adoption of multiphysics analysis is expected to grow, driving further innovations in the manufacturing sector.
資料ダウンロード
QCD管理受発注クラウド「newji」は、受発注部門で必要なQCD管理全てを備えた、現場特化型兼クラウド型の今世紀最高の受発注管理システムとなります。
ユーザー登録
受発注業務の効率化だけでなく、システムを導入することで、コスト削減や製品・資材のステータス可視化のほか、属人化していた受発注情報の共有化による内部不正防止や統制にも役立ちます。
NEWJI DX
製造業に特化したデジタルトランスフォーメーション(DX)の実現を目指す請負開発型のコンサルティングサービスです。AI、iPaaS、および先端の技術を駆使して、製造プロセスの効率化、業務効率化、チームワーク強化、コスト削減、品質向上を実現します。このサービスは、製造業の課題を深く理解し、それに対する最適なデジタルソリューションを提供することで、企業が持続的な成長とイノベーションを達成できるようサポートします。
製造業ニュース解説
製造業、主に購買・調達部門にお勤めの方々に向けた情報を配信しております。
新任の方やベテランの方、管理職を対象とした幅広いコンテンツをご用意しております。
お問い合わせ
コストダウンが利益に直結する術だと理解していても、なかなか前に進めることができない状況。そんな時は、newjiのコストダウン自動化機能で大きく利益貢献しよう!
(β版非公開)