- お役立ち記事
- Navigating the Competitive Edge: Insights from the Japanese Manufacturing Excellence for the UK’s Pharmaceutical Industry
月間77,185名の
製造業ご担当者様が閲覧しています*
*2025年2月28日現在のGoogle Analyticsのデータより
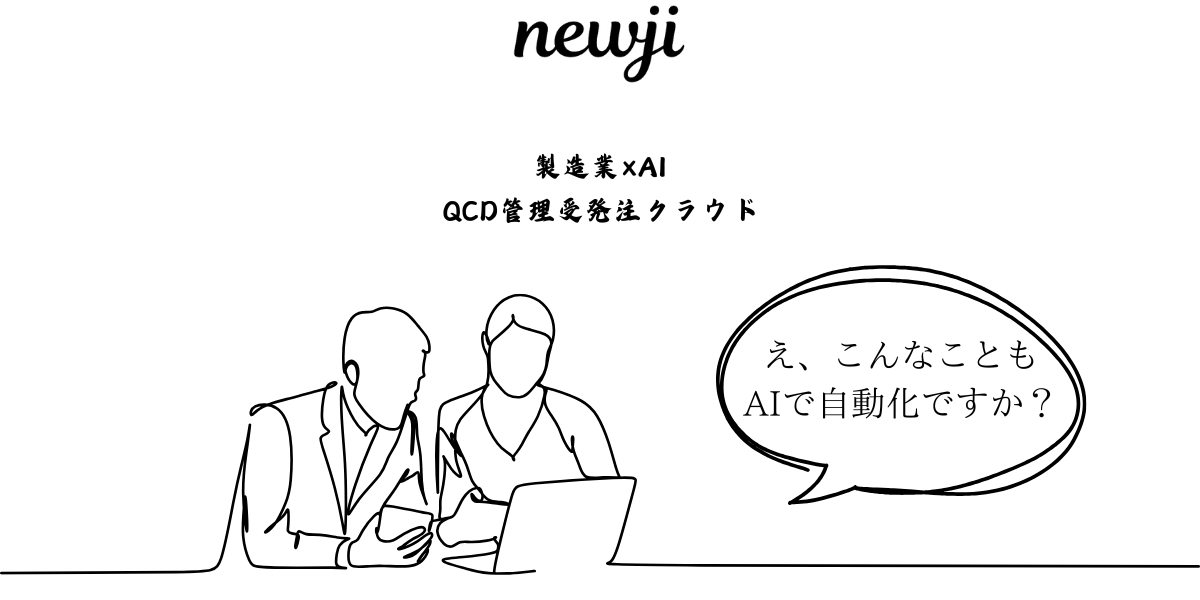
Navigating the Competitive Edge: Insights from the Japanese Manufacturing Excellence for the UK’s Pharmaceutical Industry
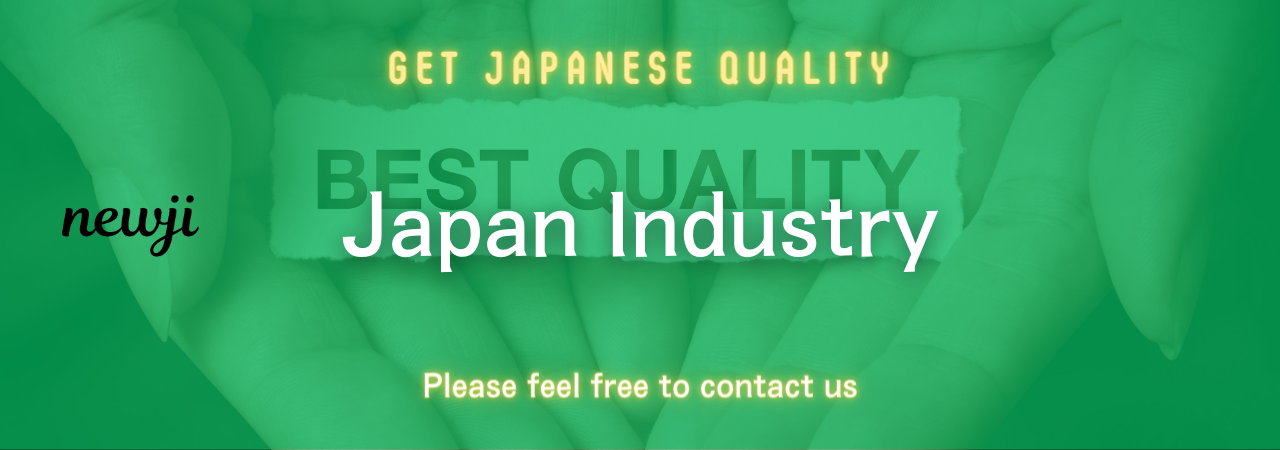
目次
Introduction to Japanese Manufacturing Excellence
Japanese manufacturing has long been synonymous with quality, precision, and innovation. These attributes have not only cemented Japan’s position in the global market but have also provided invaluable lessons for industries worldwide. The UK’s pharmaceutical industry, known for its rigorous standards and competitive nature, stands to benefit significantly from adopting Japanese manufacturing practices. This article explores how insights from Japanese manufacturing excellence can offer a competitive edge to the UK pharmaceutical sector.
Understanding the UK Pharmaceutical Landscape
The UK pharmaceutical industry is a key player in the global market, renowned for its research and development capabilities. However, the sector faces challenges such as increasing competition, stringent regulatory requirements, and the need for cost-effective production methods. To navigate these challenges, UK pharmaceutical companies can look towards Japanese manufacturing practices for strategies that enhance efficiency, quality, and innovation.
Key Principles of Japanese Manufacturing
Japanese manufacturing excellence is built on several core principles that collectively drive efficiency and quality.
Kaizen: Continuous Improvement
Kaizen, which means “continuous improvement,” is a cornerstone of Japanese manufacturing. It involves making incremental changes to processes to enhance efficiency and quality. In the pharmaceutical industry, Kaizen can lead to more effective production processes, reduced waste, and improved product quality.
Just-In-Time (JIT) Production
JIT production focuses on reducing inventory levels by receiving goods only as they are needed in the production process. This approach minimizes waste and reduces costs. For pharmaceutical companies, implementing JIT can lead to more streamlined supply chains and better resource management.
Lean Manufacturing
Lean manufacturing emphasizes maximizing value while minimizing waste. This involves optimizing processes, improving workflow, and eliminating non-essential activities. In the context of pharmaceuticals, lean practices can enhance operational efficiency and ensure that resources are allocated effectively.
Quality Control and Total Quality Management (TQM)
Japanese manufacturers prioritize quality at every stage of production. TQM involves a company-wide commitment to quality, ensuring that every employee is responsible for maintaining high standards. For the UK pharmaceutical industry, adopting TQM can lead to superior product quality and increased customer trust.
Advantages of Adopting Japanese Manufacturing Practices
Implementing Japanese manufacturing practices offers several benefits to the UK pharmaceutical industry.
Enhanced Efficiency
Japanese methodologies like JIT and lean manufacturing streamline production processes. This results in faster production times, reduced costs, and the ability to respond more swiftly to market demands.
Improved Quality
With a strong emphasis on quality control and continuous improvement, Japanese practices ensure that products meet high standards consistently. This is particularly crucial in the pharmaceutical industry, where product efficacy and safety are paramount.
Cost Reduction
By minimizing waste and optimizing resource use, Japanese manufacturing practices help reduce operational costs. This allows pharmaceutical companies to allocate resources more effectively, potentially lowering prices and increasing competitiveness.
Innovation and Flexibility
The emphasis on continuous improvement fosters a culture of innovation. Pharmaceutical companies can adapt more readily to changing market conditions and emerging technologies, maintaining a competitive edge.
Challenges and Considerations
While the benefits are substantial, there are challenges associated with adopting Japanese manufacturing practices.
Cultural Differences
Japanese manufacturing practices are deeply rooted in Japanese culture. Translating these practices into a different cultural context, such as the UK, may require careful adaptation to ensure they align with local work environments and employee expectations.
Initial Implementation Costs
Transitioning to Japanese manufacturing methodologies can involve significant initial investment in training, process redesign, and technology upgrades. Companies must weigh these upfront costs against the long-term benefits.
Resistance to Change
Employees and management may resist changes to established processes. Effective change management strategies are essential to facilitate a smooth transition and ensure buy-in from all stakeholders.
Supplier Negotiation Techniques Inspired by Japanese Practices
Effective supplier negotiations are critical in the pharmaceutical industry. Japanese practices offer several techniques that can enhance negotiation outcomes.
Building Long-Term Relationships
Japanese manufacturers prioritize long-term relationships with suppliers. This approach fosters trust, mutual respect, and collaboration, which can lead to more favorable terms and better cooperation in addressing challenges.
Emphasis on Mutual Benefits
Negotiations are viewed as opportunities for both parties to benefit. By focusing on win-win scenarios, UK pharmaceutical companies can create sustainable partnerships that support long-term success.
Clear Communication and Transparency
Effective communication is vital in Japanese negotiation practices. Being transparent about needs, expectations, and constraints helps in building trust and finding common ground.
Flexibility and Adaptability
Japanese negotiation strategies often involve flexibility and adaptability. Being open to adjusting terms and finding creative solutions can lead to more successful negotiations and stronger supplier relationships.
Market Conditions and Trends
Understanding current market conditions is essential for applying Japanese manufacturing insights effectively.
Global Supply Chain Disruptions
Recent global events have highlighted the vulnerabilities in supply chains. Japanese practices like JIT can help mitigate these risks by enhancing supply chain resilience and responsiveness.
Technological Advancements
Advancements in automation, data analytics, and artificial intelligence are transforming manufacturing. Integrating these technologies with Japanese methodologies can further enhance efficiency and quality in pharmaceutical production.
Regulatory Changes
The pharmaceutical industry is subject to stringent regulations that are continually evolving. Adopting Japanese quality management practices can help companies stay compliant and adapt to regulatory changes more smoothly.
Sustainability and Environmental Concerns
There is a growing emphasis on sustainability in manufacturing. Japanese practices that focus on waste reduction and resource optimization align well with sustainability goals, helping pharmaceutical companies reduce their environmental footprint.
Best Practices for Implementation
To successfully integrate Japanese manufacturing excellence into the UK pharmaceutical industry, companies should follow these best practices.
Comprehensive Training Programs
Investing in training ensures that employees understand and can effectively implement Japanese methodologies. Ongoing education and skill development are crucial for maintaining high standards.
Incremental Implementation
Gradually introducing Japanese practices allows companies to manage changes effectively and minimize disruptions. Starting with pilot projects can help in refining processes before a full-scale rollout.
Leadership Commitment
Strong leadership is essential to drive the adoption of Japanese practices. Leaders should embody the principles of continuous improvement and quality management to inspire their teams.
Employee Involvement
Engaging employees in the transformation process fosters ownership and accountability. Encouraging feedback and collaborative problem-solving enhances the effectiveness of implemented practices.
Continuous Monitoring and Evaluation
Regularly assessing the impact of Japanese manufacturing practices helps in identifying areas for further improvement. Metrics and key performance indicators (KPIs) should be established to track progress and ensure objectives are met.
Case Studies: Success Stories from the Pharmaceutical Industry
Examining real-world examples can provide valuable insights into the successful application of Japanese practices in the pharmaceutical sector.
Case Study 1: Streamlining Production Processes
A leading UK pharmaceutical company adopted lean manufacturing principles to streamline its production processes. By eliminating non-value-added activities and optimizing workflow, the company reduced production time by 15% and lowered operational costs by 10%. This improvement not only enhanced productivity but also allowed for greater flexibility in responding to market demands.
Case Study 2: Enhancing Quality Management
Another UK-based pharmaceutical firm implemented Total Quality Management (TQM) inspired by Japanese practices. This involved comprehensive training for employees and the establishment of quality control checkpoints at every stage of production. As a result, the company saw a 20% reduction in product defects and an increase in customer satisfaction ratings.
Case Study 3: Strengthening Supplier Relationships
A pharmaceutical company focused on building long-term relationships with its suppliers, following the Japanese approach. This led to more reliable supply chains, better negotiation terms, and collaborative problem-solving. The company experienced fewer supply disruptions and improved overall efficiency in its procurement processes.
Future Outlook: Integrating Japanese Excellence with Emerging Trends
The convergence of Japanese manufacturing excellence and emerging industry trends presents exciting opportunities for the UK pharmaceutical sector.
Digital Transformation
Integrating digital technologies with Japanese practices can further enhance efficiency and quality. Implementing advanced data analytics, automation, and Internet of Things (IoT) solutions can optimize production processes and enable real-time monitoring and adjustments.
Personalized Medicine
As the pharmaceutical industry moves towards personalized medicine, manufacturing processes must become more flexible and adaptive. Japanese practices that emphasize continuous improvement and lean operations can support the customization and scalability required for personalized treatments.
Global Collaboration
Collaborating with Japanese firms and suppliers can facilitate knowledge transfer and the adoption of best practices. Such partnerships can lead to innovative solutions and shared expertise that drive mutual growth and success.
Sustainability Initiatives
Combining Japanese waste reduction techniques with sustainability initiatives can help pharmaceutical companies achieve their environmental goals. Implementing eco-friendly practices not only benefits the environment but also meets the growing consumer demand for sustainable products.
Conclusion
Japanese manufacturing excellence offers a wealth of strategies that can significantly enhance the UK pharmaceutical industry’s competitive edge. By embracing principles such as continuous improvement, lean manufacturing, and total quality management, pharmaceutical companies can improve efficiency, reduce costs, and maintain high-quality standards. Additionally, adopting effective supplier negotiation techniques and fostering long-term relationships can strengthen supply chains and support sustainable growth. While challenges such as cultural differences and initial implementation costs exist, the long-term benefits make the integration of Japanese practices a worthwhile investment. As the pharmaceutical industry continues to evolve, the insights gained from Japanese manufacturing will remain invaluable in driving innovation and maintaining excellence.
資料ダウンロード
QCD管理受発注クラウド「newji」は、受発注部門で必要なQCD管理全てを備えた、現場特化型兼クラウド型の今世紀最高の受発注管理システムとなります。
ユーザー登録
受発注業務の効率化だけでなく、システムを導入することで、コスト削減や製品・資材のステータス可視化のほか、属人化していた受発注情報の共有化による内部不正防止や統制にも役立ちます。
NEWJI DX
製造業に特化したデジタルトランスフォーメーション(DX)の実現を目指す請負開発型のコンサルティングサービスです。AI、iPaaS、および先端の技術を駆使して、製造プロセスの効率化、業務効率化、チームワーク強化、コスト削減、品質向上を実現します。このサービスは、製造業の課題を深く理解し、それに対する最適なデジタルソリューションを提供することで、企業が持続的な成長とイノベーションを達成できるようサポートします。
製造業ニュース解説
製造業、主に購買・調達部門にお勤めの方々に向けた情報を配信しております。
新任の方やベテランの方、管理職を対象とした幅広いコンテンツをご用意しております。
お問い合わせ
コストダウンが利益に直結する術だと理解していても、なかなか前に進めることができない状況。そんな時は、newjiのコストダウン自動化機能で大きく利益貢献しよう!
(β版非公開)