- お役立ち記事
- Navigating the Intricacies of SCCR Response: A Deep Dive into Japanese Manufacturing Excellence
月間77,185名の
製造業ご担当者様が閲覧しています*
*2025年2月28日現在のGoogle Analyticsのデータより
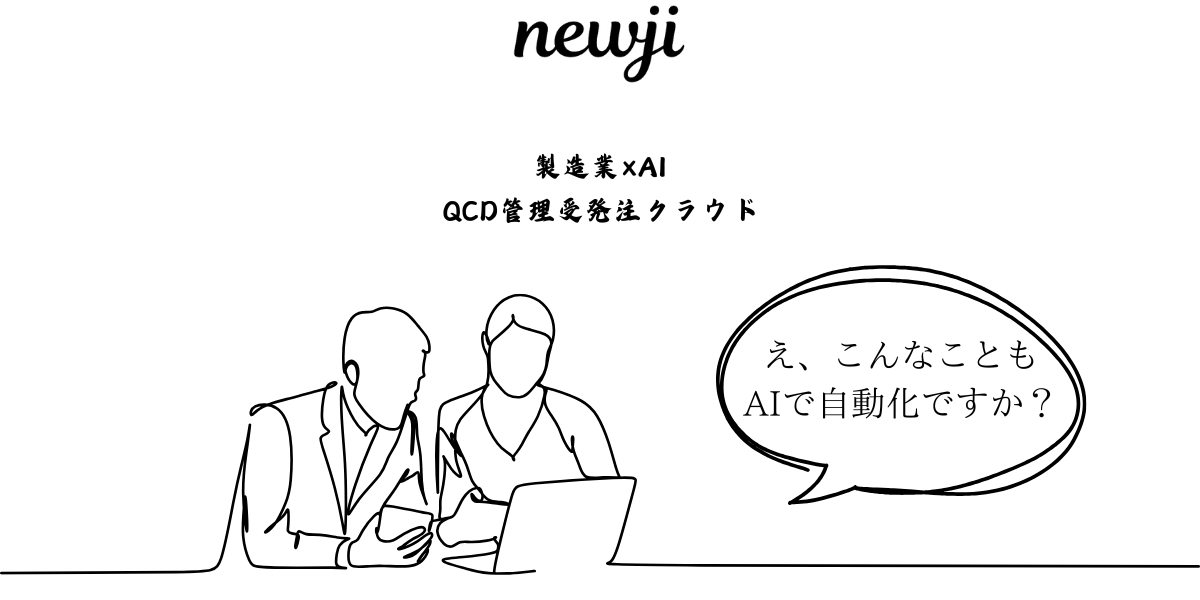
Navigating the Intricacies of SCCR Response: A Deep Dive into Japanese Manufacturing Excellence
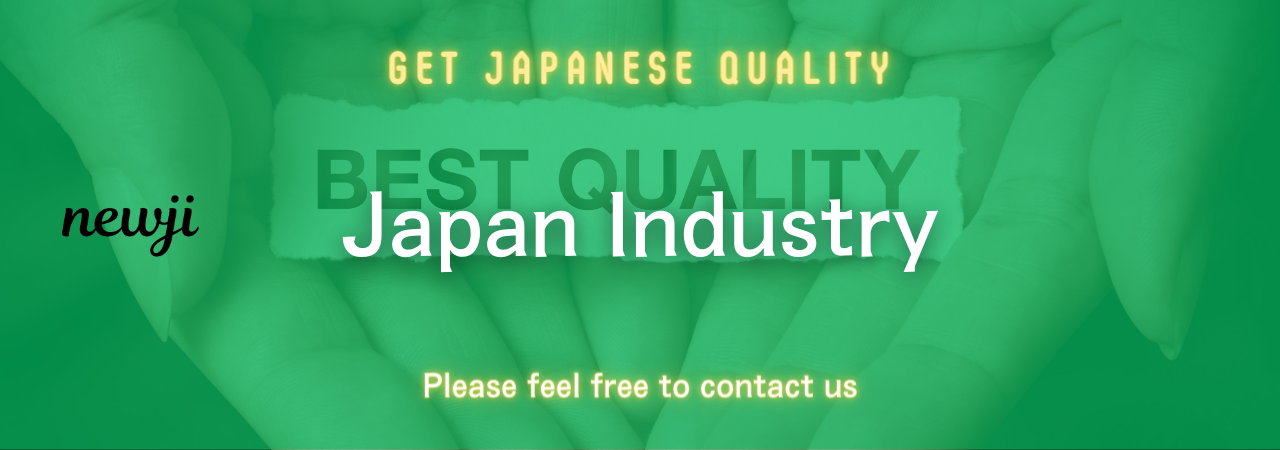
目次
Understanding SCCR in Japanese Manufacturing
SCCR stands for Sustainable, Circular, and Resilient manufacturing.
Japanese manufacturers have been pioneers in integrating SCCR principles.
These principles are essential in today’s global market.
They contribute to long-term business success.
SCCR focuses on sustainability, circularity, and resilience.
Sustainability ensures that manufacturing processes do not deplete resources.
Circularity emphasizes recycling and reusing materials.
Resilience involves the ability to adapt to changes and disruptions.
Japanese companies excel in implementing SCCR strategies.
Their approach serves as a model for global manufacturing excellence.
The Importance of SCCR in Modern Manufacturing
SCCR is critical for achieving environmental and economic goals.
It helps companies minimize waste and reduce costs.
Implementing SCCR practices can lead to innovation.
Companies can develop new products and processes.
SCCR enhances a company’s reputation and brand value.
Consumers increasingly prefer sustainable products.
Regulations are becoming stricter on environmental standards.
Adopting SCCR ensures compliance and avoids penalties.
Resilient manufacturing ensures business continuity.
It prepares companies to handle unexpected challenges.
Advantages of Japanese SCCR Practices
Japanese manufacturers offer several advantages in SCCR implementation.
They have a deep-rooted culture of continuous improvement.
Kaizen, the practice of ongoing improvement, is central to their operations.
This mindset drives efficiency and waste reduction.
Japanese companies prioritize quality control.
High-quality standards reduce defects and material waste.
They utilize advanced technology for automation and efficiency.
Automation enhances precision and consistency in manufacturing.
Japanese manufacturers are leaders in lean manufacturing.
Lean practices eliminate unnecessary steps and optimize processes.
Commitment to Innovation
Innovation is a cornerstone of Japanese manufacturing.
Companies invest heavily in research and development.
They collaborate with universities and research institutions.
This leads to cutting-edge technologies and processes.
Innovative solutions enhance SCCR implementation.
Companies can develop sustainable products with minimal environmental impact.
Continuous innovation keeps Japanese manufacturers competitive globally.
Strong Supplier Relationships
Japanese companies maintain strong relationships with suppliers.
They foster long-term partnerships based on trust and mutual success.
Collaborative relationships lead to better quality and reliability.
Suppliers are involved in the development process.
This ensures that materials meet high standards.
Strong supplier relationships facilitate efficient supply chains.
Efficient supply chains reduce lead times and costs.
Challenges in Implementing SCCR Practices
Despite their strengths, Japanese manufacturers face challenges in SCCR implementation.
Global competition puts pressure on maintaining high standards.
Cost management is crucial in sustaining SCCR practices.
Balancing sustainability with profitability can be difficult.
Technological advancements require continuous adaptation.
Companies must stay updated with the latest innovations.
Workforce skills need to match evolving manufacturing processes.
Training and development are essential for maintaining expertise.
Cultural barriers may arise when implementing new practices.
Adapting to different cultural norms can impact global operations.
Economic Fluctuations
Economic downturns can affect investment in SCCR initiatives.
Companies may prioritize short-term gains over long-term sustainability.
Maintaining SCCR practices during economic uncertainty is challenging.
Long-term commitment is necessary for sustained success.
Economic stability supports ongoing SCCR efforts.
Regulatory Compliance
Navigating international regulations is complex.
Different countries have varying environmental standards.
Japanese manufacturers must ensure compliance across markets.
Non-compliance can lead to legal issues and fines.
Staying informed about regulatory changes is vital.
Adaptable strategies help manage regulatory challenges.
Supplier Negotiation Techniques
Effective negotiation with Japanese suppliers is crucial for successful procurement.
Understanding cultural nuances is key to building strong relationships.
Japanese business culture emphasizes respect and harmony.
Negotiations should be approached with patience and formality.
Building trust takes time and consistent communication.
Clear communication of expectations ensures mutual understanding.
Flexibility and adaptability are important in negotiations.
Being open to compromise can lead to win-win outcomes.
Transparency in dealings fosters trust and reliability.
Long-term relationships are valued over short-term gains.
Leveraging Mutual Benefits
Negotiations should focus on mutual benefits.
Highlighting how both parties can gain creates a cooperative atmosphere.
Collaborative problem-solving strengthens partnerships.
Emphasizing shared goals aligns interests and objectives.
Effective Communication
Clear and concise communication is essential.
Using appropriate language and terminology avoids misunderstandings.
Active listening demonstrates respect and attentiveness.
Feedback should be encouraged to ensure alignment.
Non-verbal communication also plays a significant role.
Understanding body language and cues can aid negotiations.
Market Conditions and Their Impact on SCCR
Market conditions significantly impact SCCR implementation.
Economic trends influence investment in sustainability initiatives.
Consumer preferences shift towards sustainable products.
Japanese manufacturers must adapt to changing market demands.
Global supply chain disruptions affect manufacturing processes.
Resilient supply chains are essential for maintaining SCCR practices.
Technological advancements drive market competitiveness.
Staying ahead of market trends ensures continued success.
Environmental concerns shape consumer and regulatory landscapes.
Japanese companies must anticipate and respond to market changes.
Globalization and Competition
Globalization increases competition among manufacturers.
Japanese companies must maintain excellence to stay competitive.
Adopting SCCR practices can differentiate them in the market.
Sustainability is a key factor in consumer purchasing decisions.
Competitive advantage is gained through superior SCCR implementation.
Technological Innovations
Technological innovations enable more efficient SCCR practices.
Automation and artificial intelligence enhance production processes.
Advanced materials contribute to sustainable manufacturing.
Digitalization improves supply chain management.
Investing in technology supports continuous improvement and innovation.
Best Practices in Japanese Procurement and Purchasing
Japanese procurement strategies offer valuable lessons for global manufacturers.
Emphasis on quality is paramount in Japanese supply chains.
Strict quality control ensures high standards throughout the process.
Just-in-time inventory management minimizes waste and optimizes resources.
This approach reduces storage costs and enhances efficiency.
Collaboration with suppliers fosters innovation and quality.
Shared goals and open communication strengthen partnerships.
Continuous improvement practices enhance procurement processes.
Kaizen principles drive ongoing optimization and waste reduction.
Strategic Sourcing
Strategic sourcing involves selecting suppliers based on long-term goals.
Japanese companies focus on supplier reliability and quality.
Evaluating suppliers’ capabilities ensures alignment with company standards.
Building strategic partnerships leads to better procurement outcomes.
Long-term sourcing strategies support sustained SCCR practices.
Risk Management
Effective risk management is crucial in procurement.
Identifying potential risks in the supply chain prevents disruptions.
Contingency planning ensures business continuity.
Diversifying suppliers reduces dependency and mitigates risks.
Proactive risk management supports resilient manufacturing.
Implementing SCCR: Step-by-Step Guide
Implementing SCCR practices requires a structured approach.
Japanese manufacturers follow a systematic methodology.
This ensures comprehensive integration of sustainability, circularity, and resilience.
The following steps outline the implementation process.
1. Assess Current Practices
Evaluate existing manufacturing processes.
Identify areas for improvement in sustainability and efficiency.
Conduct audits to assess resource usage and waste generation.
Benchmark against industry standards and best practices.
2. Define SCCR Goals
Set clear and measurable objectives.
Align SCCR goals with overall business strategy.
Prioritize initiatives based on impact and feasibility.
Ensure goals are achievable and time-bound.
3. Develop a Strategic Plan
Create a roadmap for SCCR implementation.
Outline specific actions and responsibilities.
Allocate resources and budget for initiatives.
Establish timelines and milestones for tracking progress.
4. Engage Stakeholders
Involve all relevant parties in the implementation process.
Communicate the importance of SCCR practices.
Provide training and support to employees.
Foster a culture of continuous improvement and sustainability.
5. Implement Initiatives
Execute the planned actions and projects.
Monitor progress and adjust strategies as needed.
Ensure adherence to quality and sustainability standards.
Collaborate with suppliers and partners to achieve goals.
6. Monitor and Evaluate
Track performance against SCCR goals.
Use key performance indicators to measure success.
Conduct regular reviews and assessments.
Identify areas for further improvement and optimization.
7. Continuous Improvement
Adopt a mindset of ongoing enhancement.
Incorporate feedback and lessons learned.
Stay updated with industry advancements and innovations.
Adapt strategies to evolving market and environmental conditions.
Case Studies: Japanese Manufacturing Excellence
Examining real-world examples highlights the effectiveness of Japanese SCCR practices.
Several companies demonstrate exceptional performance in sustainability and resilience.
Toyota Motor Corporation
Toyota is renowned for its lean manufacturing principles.
The Toyota Production System emphasizes efficiency and waste reduction.
Their sustainability initiatives include energy-efficient production and recycling programs.
Toyota’s commitment to continuous improvement drives their SCCR success.
They collaborate closely with suppliers to maintain high quality and sustainability standards.
Panasonic Corporation
Panasonic integrates SCCR practices across its operations.
They focus on energy conservation and reducing carbon emissions.
Their circular economy initiatives include recycling and repurposing materials.
Panasonic invests in innovative technologies to enhance sustainability.
They engage stakeholders to promote sustainability throughout their supply chain.
Fanuc Corporation
Fanuc specializes in automation and robotics.
Their products enhance manufacturing efficiency and precision.
Fanuc implements SCCR principles in their production processes.
They prioritize renewable energy and resource conservation.
Fanuc’s resilient manufacturing systems ensure minimal disruptions and sustained operations.
Future Trends in SCCR and Japanese Manufacturing
The future of SCCR in Japanese manufacturing looks promising.
Several trends will shape the landscape in the coming years.
Digital Transformation
Digital technologies will further enhance SCCR practices.
Integration of IoT and big data analytics improves efficiency and monitoring.
Digital twins and simulation technologies optimize production processes.
Automation and robotics contribute to sustainable manufacturing.
Renewable Energy Integration
Japanese manufacturers will increasingly adopt renewable energy sources.
Solar, wind, and other renewable energies reduce carbon footprints.
Energy-efficient technologies support sustainable operations.
Integration of renewable energies enhances resilience against energy disruptions.
Advanced Materials and Recycling
Development of advanced materials contributes to circular manufacturing.
Lightweight and durable materials enhance product sustainability.
Innovative recycling technologies enable efficient material recovery.
Japanese companies lead in developing and implementing recycling solutions.
Global Collaboration and Standards
Collaborative efforts will drive global SCCR standards.
Japanese manufacturers will work with international partners to set benchmarks.
Global standards ensure consistency and quality in sustainable practices.
Collaboration facilitates knowledge sharing and innovation.
Conclusion
Navigating the intricacies of SCCR response is essential for achieving manufacturing excellence.
Japanese manufacturers exemplify the successful integration of sustainability, circularity, and resilience.
Their practices offer valuable lessons for global industries.
By adopting Japanese SCCR strategies, companies can enhance efficiency, reduce costs, and promote long-term success.
Continuous improvement, innovation, and strong supplier relationships are key to sustaining SCCR initiatives.
As market conditions evolve, Japanese manufacturers remain adaptable and forward-thinking.
Embracing SCCR principles ensures competitiveness and resilience in an ever-changing global landscape.
Adopting these practices not only benefits businesses but also contributes to a sustainable future for the planet.
資料ダウンロード
QCD管理受発注クラウド「newji」は、受発注部門で必要なQCD管理全てを備えた、現場特化型兼クラウド型の今世紀最高の受発注管理システムとなります。
ユーザー登録
受発注業務の効率化だけでなく、システムを導入することで、コスト削減や製品・資材のステータス可視化のほか、属人化していた受発注情報の共有化による内部不正防止や統制にも役立ちます。
NEWJI DX
製造業に特化したデジタルトランスフォーメーション(DX)の実現を目指す請負開発型のコンサルティングサービスです。AI、iPaaS、および先端の技術を駆使して、製造プロセスの効率化、業務効率化、チームワーク強化、コスト削減、品質向上を実現します。このサービスは、製造業の課題を深く理解し、それに対する最適なデジタルソリューションを提供することで、企業が持続的な成長とイノベーションを達成できるようサポートします。
製造業ニュース解説
製造業、主に購買・調達部門にお勤めの方々に向けた情報を配信しております。
新任の方やベテランの方、管理職を対象とした幅広いコンテンツをご用意しております。
お問い合わせ
コストダウンが利益に直結する術だと理解していても、なかなか前に進めることができない状況。そんな時は、newjiのコストダウン自動化機能で大きく利益貢献しよう!
(β版非公開)