- お役立ち記事
- Necessary Equipment and Supplier Selection for Realizing Smart Factories
Necessary Equipment and Supplier Selection for Realizing Smart Factories
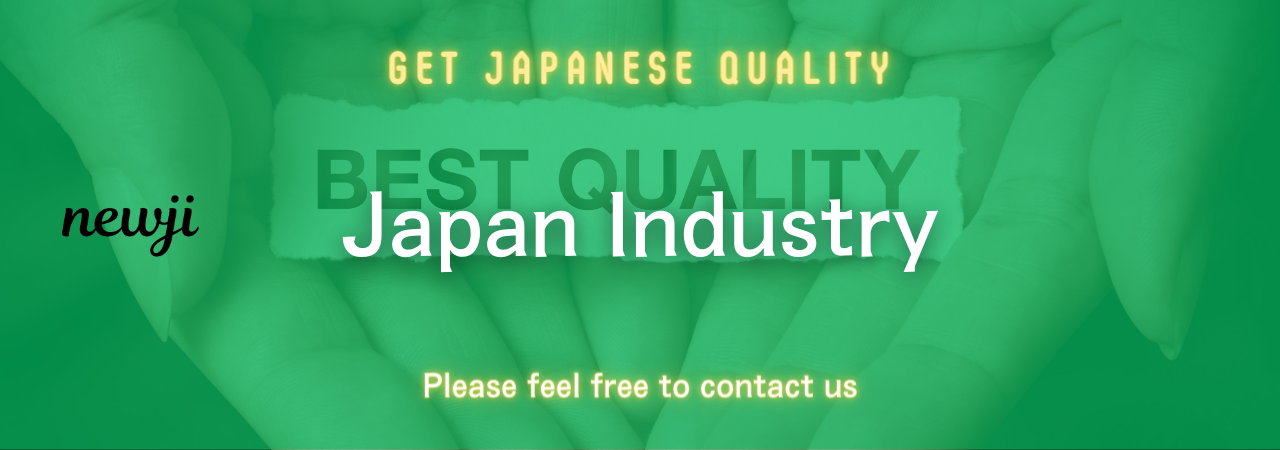
In today’s rapidly evolving industrial landscape, the concept of smart factories is gaining significant traction.
Smart factories leverage advanced technologies such as the Internet of Things (IoT), artificial intelligence (AI), and robotics to create highly efficient, automated, and interconnected manufacturing environments.
Implementing a smart factory requires careful planning, the right equipment, and selecting the appropriate suppliers.
Let’s delve into the essentials for making smart factories a reality.
目次
Understanding Smart Factories
Smart factories represent a new generation of manufacturing systems that use interconnected digital technologies to optimize production processes.
These systems are capable of self-optimizing performance across a broader network, adapting to production needs, and autonomously running entire production processes.
The goal is to greatly enhance efficiency, flexibility, and responsiveness in manufacturing.
Key Components of Smart Factories
Industrial IoT Devices
The backbone of any smart factory is the Industrial Internet of Things (IIoT).
These devices collect, share, and analyze data from various parts of the manufacturing process.
Sensors, actuators, and other IoT-enabled devices provide real-time data that plants need to make intelligent decisions.
Automation Technologies
Automation in smart factories includes robotics, automated guided vehicles (AGVs), and conveyor systems.
These machines can handle repetitive tasks with precision and consistency, freeing human workers to focus on more complex tasks.
Robotic arms, for instance, can perform tasks such as welding, painting, and assembly with high accuracy.
Data Analytics and AI
Data analytics and AI play a crucial role in interpreting the massive amounts of data generated within a smart factory.
Advanced algorithms can predict maintenance needs, optimize supply chains, and improve overall decision-making.
Machine learning models are essential for predicting equipment failures before they happen, minimizing downtime, and maintaining smooth operations.
Cloud Computing and Edge Computing
Cloud computing provides a scalable platform for storing and processing data.
It allows for real-time data analysis and remote monitoring of factory equipment.
Edge computing complements cloud computing by processing data closer to the source, reducing latency and bandwidth usage.
Together, they enable complex computations and data-driven decision-making in real-time.
Cybersecurity Measures
With the increased connectivity and data exchange in smart factories, cybersecurity becomes paramount.
Implementing robust cybersecurity measures ensures that sensitive data and critical infrastructure are protected from unauthorized access and cyberattacks.
This includes using encryption, firewalls, and regular security audits.
Selecting the Right Suppliers
Choosing the right suppliers is a critical step in the journey toward realizing a smart factory.
The suppliers will provide the necessary equipment, software, and expertise to ensure successful implementation.
Assessing Supplier Capabilities
Knowing a supplier’s capabilities and experience in the industry is essential.
Look for suppliers with a proven track record in providing equipment and solutions tailored to smart manufacturing needs.
Evaluate their ability to offer scalable and flexible solutions that can grow with your business.
Evaluating Technological Integration
Ensure that the supplier’s technologies can seamlessly integrate with existing systems and infrastructure.
Compatibility with your current IT environment will reduce implementation time and costs.
Suppliers should offer comprehensive support for integrating new solutions with minimal disruption to your operations.
Service and Support
Reliable service and support are crucial when selecting suppliers for smart factories.
Look for suppliers who offer robust customer support and are readily available to assist with troubleshooting and maintenance.
Having a supplier who can provide timely support minimizes downtime and ensures smooth operations.
Cost Considerations
While cost is a significant factor, it shouldn’t be the only consideration.
Evaluate the total cost of ownership, including initial investment, maintenance, and operational costs.
Sometimes, higher upfront costs can result in long-term savings through increased efficiency and reduced downtime.
Future-Proofing Capabilities
Choose suppliers who are committed to innovation and continuous improvement.
Their products and solutions should be adaptable to future technological advancements.
Future-proofing ensures that your smart factory remains competitive and can adapt to new industry trends and demands.
Implementing Smart Factory Solutions
Once the necessary equipment and suppliers are in place, the next step is the actual implementation of smart factory solutions.
Pilot Projects
Start with pilot projects to test the new technologies in a controlled environment.
Pilot projects help identify potential issues and allow for necessary adjustments before a full-scale rollout.
Evaluate the performance, scalability, and integration of the technologies during this phase.
Employee Training
Training employees is crucial for the successful implementation of smart factory solutions.
Employees should be well-versed in using new technologies and understanding their role in the overall system.
Continual learning and development programs should be established to keep employees updated on the latest advancements.
Continuous Monitoring and Improvement
After implementation, continuous monitoring and improvement are essential.
Use data analytics to assess the performance of the smart factory and identify areas for improvement.
Regularly review processes, gather feedback from employees, and make data-driven decisions to optimize operations.
Smart factories represent the future of manufacturing, offering unprecedented levels of efficiency, flexibility, and productivity.
By understanding the key components, carefully selecting the right suppliers, and implementing solutions strategically, businesses can successfully transition to a smart factory environment.
The journey towards a smart factory is an ongoing process that requires continuous innovation, adaptation, and improvement.
資料ダウンロード
QCD調達購買管理クラウド「newji」は、調達購買部門で必要なQCD管理全てを備えた、現場特化型兼クラウド型の今世紀最高の購買管理システムとなります。
ユーザー登録
調達購買業務の効率化だけでなく、システムを導入することで、コスト削減や製品・資材のステータス可視化のほか、属人化していた購買情報の共有化による内部不正防止や統制にも役立ちます。
NEWJI DX
製造業に特化したデジタルトランスフォーメーション(DX)の実現を目指す請負開発型のコンサルティングサービスです。AI、iPaaS、および先端の技術を駆使して、製造プロセスの効率化、業務効率化、チームワーク強化、コスト削減、品質向上を実現します。このサービスは、製造業の課題を深く理解し、それに対する最適なデジタルソリューションを提供することで、企業が持続的な成長とイノベーションを達成できるようサポートします。
オンライン講座
製造業、主に購買・調達部門にお勤めの方々に向けた情報を配信しております。
新任の方やベテランの方、管理職を対象とした幅広いコンテンツをご用意しております。
お問い合わせ
コストダウンが利益に直結する術だと理解していても、なかなか前に進めることができない状況。そんな時は、newjiのコストダウン自動化機能で大きく利益貢献しよう!
(Β版非公開)