- お役立ち記事
- New approach and improved accuracy of high-resolution resist evaluation method
月間77,185名の
製造業ご担当者様が閲覧しています*
*2025年2月28日現在のGoogle Analyticsのデータより
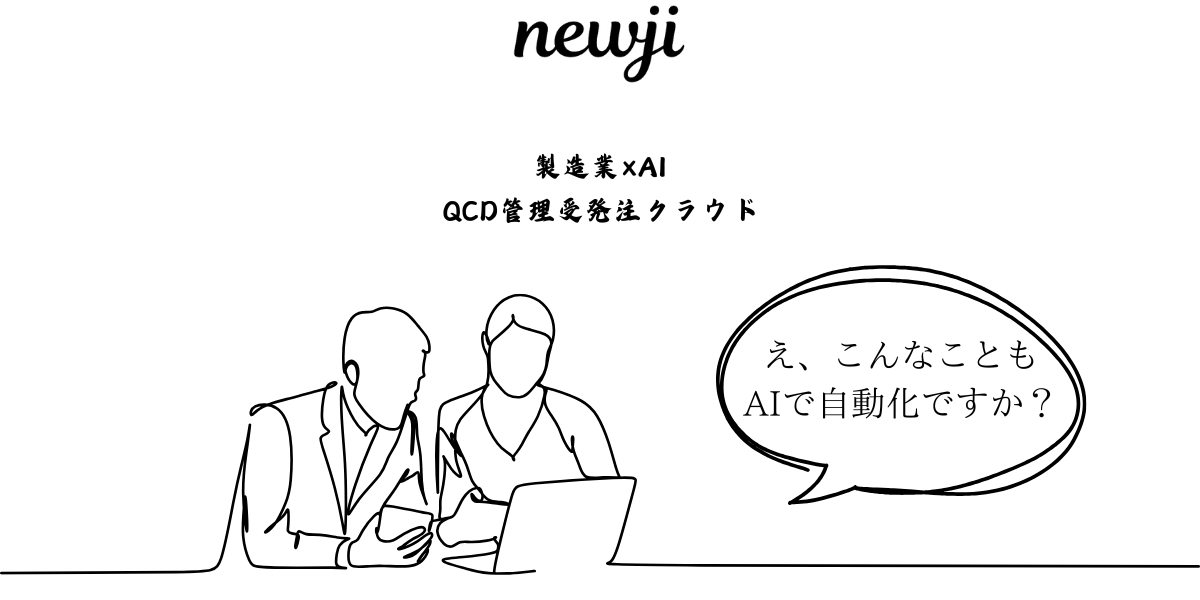
New approach and improved accuracy of high-resolution resist evaluation method
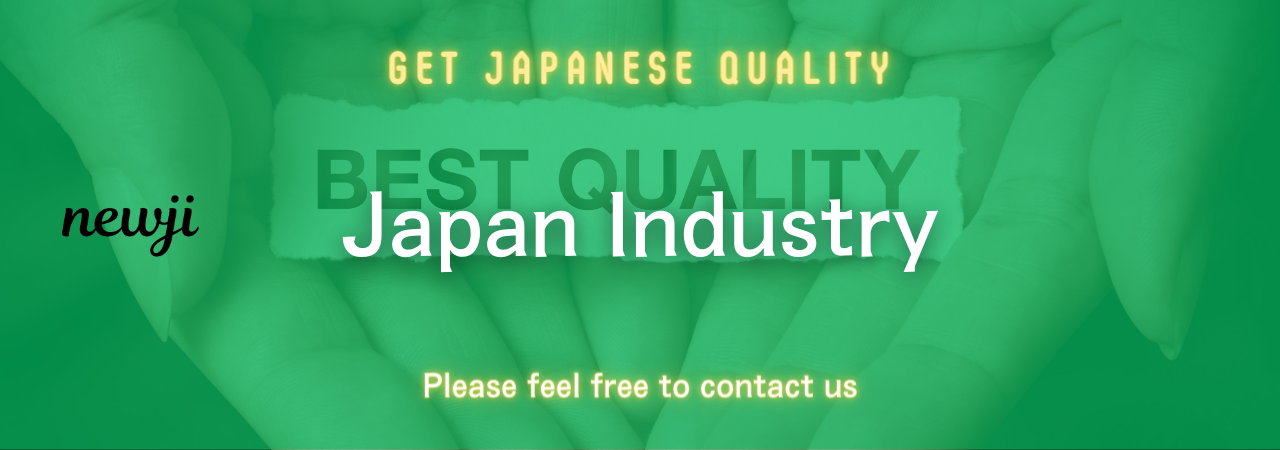
目次
Understanding High-Resolution Resist Evaluation
High-resolution resist evaluation is a critical process in various industries, particularly in the field of semiconductor manufacturing.
This process involves assessing the performance and capabilities of resist materials used to create intricate patterns on semiconductor wafers.
The accuracy of this evaluation is vital as it directly impacts the quality and efficiency of the final products.
In recent years, a new approach has emerged, offering improved accuracy and reliability in the evaluation process.
What is Resist in Semiconductor Manufacturing?
In the context of semiconductor manufacturing, resist refers to a light-sensitive material used to transfer a pattern onto a substrate.
This material is applied to the surface of a silicon wafer, which is then exposed to light or electron beam lithography.
The areas of the resist exposed to light become soluble, allowing for selective removal.
This process leaves behind a specific pattern that can be used to etch circuits into the silicon wafer.
Challenges in Resist Evaluation
Evaluating resist performance is a complex task due to the microscopic scale at which semiconductor patterns are created.
Some of the key challenges include:
1. **Resolution Limitations**: As device dimensions shrink, achieving higher resolution patterns becomes necessary, demanding more accurate evaluation methods.
2. **Material Variability**: Slight changes in resist formulation can significantly impact performance, requiring precise characterization techniques.
3. **Process Consistency**: Ensuring consistent results across different batches and manufacturing environments is crucial for maintaining quality control.
The Need for Improved Accuracy
The ever-evolving demand for smaller, faster, and more efficient electronic devices means that the accuracy of resist evaluation methods needs continuous improvement.
Traditional methods, while effective to some extent, often fall short in addressing the demands of modern semiconductor manufacturing.
An inaccurate evaluation can lead to defects in the semiconductor devices, which can be costly and time-consuming to rectify.
Therefore, adopting new approaches with enhanced accuracy is a priority for manufacturers aiming to stay competitive and innovative.
The New Approach to Resist Evaluation
In response to these challenges, researchers and engineers are developing new methodologies for high-resolution resist evaluation.
This new approach integrates advanced technologies and analytical techniques to enhance accuracy and reliability.
Advanced Imaging Techniques
One of the major improvements in the new evaluation method is the use of state-of-the-art imaging techniques.
High-resolution microscopes, such as atomic force microscopes (AFM) and scanning electron microscopes (SEM), provide detailed images of the resist patterns.
These images enable engineers to assess even the smallest features and imperfections with unprecedented clarity.
Enhanced Software Analysis
Complementing advanced imaging is the implementation of sophisticated software tools for data analysis.
Machine learning algorithms can now analyze large datasets of imaging results, identifying patterns and trends that human analysts might overlook.
This automation not only speed up the evaluation process but also reduces the risk of human error, leading to more consistent and accurate outcomes.
Integration of Metrology and Simulation
Another critical component of the new approach is the integration of metrology techniques with simulation modeling.
By simulating the lithographic process, engineers can predict how different resist materials will behave under various conditions.
This predictive capability allows for optimization of the resist formulation and process parameters before actual manufacturing, saving both time and resources.
Real-Time Monitoring
To further enhance accuracy, real-time monitoring systems are being employed.
These systems provide continuous feedback during the resist application and exposure processes, ensuring that any deviations are immediately identified and corrected.
Real-time monitoring not only improves the precision of resist evaluation but also enhances the overall efficiency of the manufacturing process.
Benefits of the Improved Resist Evaluation Method
The new approach to resist evaluation offers several significant benefits for semiconductor manufacturers:
Increased Precision
By utilizing advanced imaging and analysis techniques, the new method allows for more precise pattern evaluations.
This increased precision translates to higher-quality semiconductor devices with fewer defects, ultimately improving product reliability.
Cost-Efficiency
Although implementing new technologies and methodologies requires investment, the long-term cost savings are substantial.
With improved accuracy, the number of defective products decreases, reducing waste and lowering production costs.
Moreover, the ability to optimize processes in the simulation phase minimizes costly trial-and-error approaches in actual manufacturing.
Shorter Development Cycles
Enhanced evaluation accuracy leads to faster development cycles for new products.
By accurately predicting resist performance, manufacturers can streamline the prototyping and testing phases, bringing new products to market more quickly.
Adaptability to Advanced Technologies
As semiconductor technology continues to advance, the new approach to resist evaluation provides the flexibility needed to adapt to emerging trends and technologies.
This adaptability ensures that manufacturers can meet the evolving demands of the electronics industry without compromising on quality.
Conclusion
The new approach to high-resolution resist evaluation marks a significant advancement in the field of semiconductor manufacturing.
By leveraging advanced imaging, software analysis, metrology integration, and real-time monitoring, this method offers unparalleled accuracy and reliability.
As the demand for smaller, more efficient electronic devices continues to rise, adopting such innovative evaluation techniques will be crucial for manufacturers striving to maintain a competitive edge.
Ultimately, the improved accuracy of resist evaluation not only enhances the quality of semiconductor products but also drives progress in the broader electronics industry.
資料ダウンロード
QCD管理受発注クラウド「newji」は、受発注部門で必要なQCD管理全てを備えた、現場特化型兼クラウド型の今世紀最高の受発注管理システムとなります。
ユーザー登録
受発注業務の効率化だけでなく、システムを導入することで、コスト削減や製品・資材のステータス可視化のほか、属人化していた受発注情報の共有化による内部不正防止や統制にも役立ちます。
NEWJI DX
製造業に特化したデジタルトランスフォーメーション(DX)の実現を目指す請負開発型のコンサルティングサービスです。AI、iPaaS、および先端の技術を駆使して、製造プロセスの効率化、業務効率化、チームワーク強化、コスト削減、品質向上を実現します。このサービスは、製造業の課題を深く理解し、それに対する最適なデジタルソリューションを提供することで、企業が持続的な成長とイノベーションを達成できるようサポートします。
製造業ニュース解説
製造業、主に購買・調達部門にお勤めの方々に向けた情報を配信しております。
新任の方やベテランの方、管理職を対象とした幅広いコンテンツをご用意しております。
お問い合わせ
コストダウンが利益に直結する術だと理解していても、なかなか前に進めることができない状況。そんな時は、newjiのコストダウン自動化機能で大きく利益貢献しよう!
(β版非公開)