- お役立ち記事
- New Customer Experiences in Manufacturing Unlocked by Digital Tools
New Customer Experiences in Manufacturing Unlocked by Digital Tools
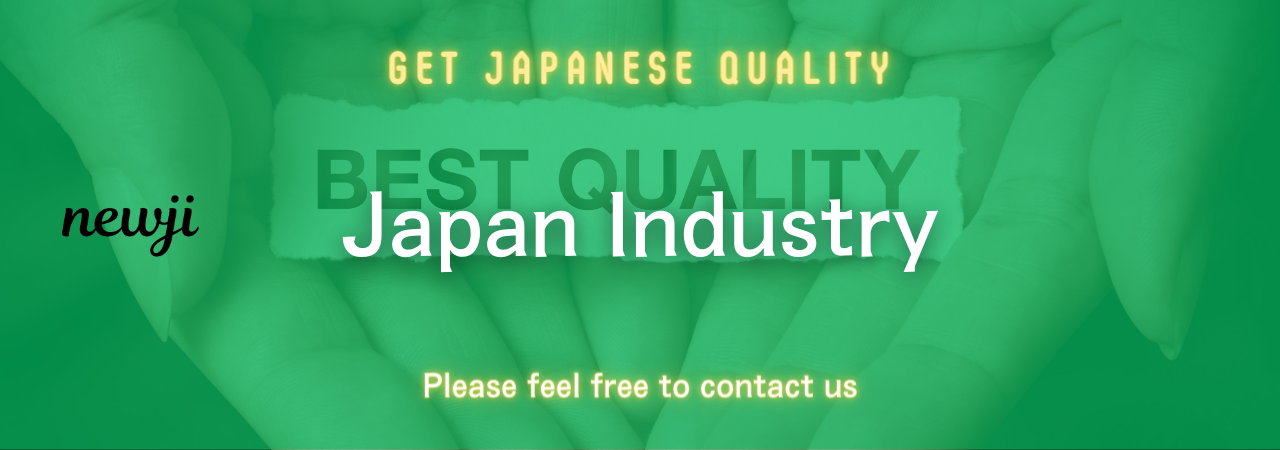
In today’s rapidly evolving world, the manufacturing industry is experiencing a transformation driven by digital tools.
These tools are not just improving efficiency and productivity, but they are also unlocking new customer experiences.
In this article, we will explore how digital tools are changing the landscape of manufacturing and creating novel customer interactions.
目次
Understanding Digital Tools in Manufacturing
Digital tools encompass a broad spectrum of technologies ranging from advanced robotics to cloud computing.
They also include artificial intelligence (AI), machine learning (ML), and the Internet of Things (IoT).
These technologies, when integrated into manufacturing processes, provide a wealth of data and insights that drive smarter decisions and more efficient operations.
Artificial Intelligence and Machine Learning
AI and ML are revolutionizing manufacturing by enabling predictive maintenance, quality control, and optimization of processes.
Predictive maintenance uses AI algorithms to analyze data from manufacturing equipment to predict failures before they occur.
This minimizes downtime and keeps production lines running smoothly.
Quality control is another area where AI and ML shine.
By inspecting products in real-time, these technologies ensure that only high-quality products reach the customer.
This not only improves customer satisfaction but also reduces waste and costs.
Internet of Things
IoT refers to the interconnection of physical devices through the internet.
In manufacturing, IoT systems collect and share data from various sensors and equipment.
This data provides real-time insights into factory operations, enabling manufacturers to respond swiftly to any issues.
For example, if a machine in a production line is operating outside of its specified parameters, IoT sensors can alert the maintenance team immediately.
This proactive approach prevents small issues from escalating into bigger problems.
Cloud Computing
Cloud computing facilitates the storage and analysis of large volumes of data generated by digital tools.
It provides a scalable and flexible platform for manufacturers to run complex algorithms and simulations.
Additionally, cloud-based systems enable seamless collaboration between different departments and even across different geographical locations.
With cloud computing, manufacturers can access vital information from anywhere, at any time.
This level of accessibility enhances decision-making processes and drives innovation.
Enhancing Customer Experiences
The integration of digital tools in manufacturing isn’t just about improving operational efficiency.
It’s also about creating richer, more personalized experiences for customers.
Here are some ways digital tools are reshaping customer interactions:
Customization and Personalization
Digital tools allow for greater customization and personalization of products.
Customers can now influence the design, features, and specifications of the products they purchase.
For instance, through advanced CAD software and 3D printing, manufacturers can create bespoke products that meet individual customer preferences.
Improved Quality and Reliability
By using AI-driven quality control systems, manufacturers are able to consistently produce high-quality products.
This reliability builds customer trust and satisfaction.
When customers know they can depend on a product, they are more likely to become repeat buyers.
Faster Production and Delivery Times
Digital tools streamline manufacturing processes, reducing production times and speeding up delivery.
IoT and cloud computing enable real-time tracking of orders, giving customers greater transparency and assurance about their purchases.
Fast and reliable delivery times enhance the overall customer experience.
Enhanced After-Sales Services
Digital tools also improve after-sales services.
Predictive maintenance can extend the lifespan of products and ensure they function optimally.
Manufacturers can use AI to offer smart troubleshooting and support, providing customers with quick and effective solutions to any issues they may encounter.
Eco-friendly Manufacturing
Sustainability is increasingly important to customers.
Digital tools help manufacturers adopt more eco-friendly practices by optimizing resource use and reducing waste.
For example, IoT sensors can monitor energy consumption and suggest ways to improve efficiency, leading to lower carbon footprints.
Challenges and Future Prospects
Despite the many benefits, there are challenges in the adoption of digital tools in manufacturing.
Cybersecurity concerns, high implementation costs, and the need for skilled personnel can be barriers to adoption.
However, the long-term benefits far outweigh these challenges.
Overcoming Cybersecurity Concerns
As manufacturing systems become more interconnected, they also become more susceptible to cyber threats.
It’s crucial for manufacturers to invest in robust cybersecurity measures.
Regular updates, employee training, and adopting best practices can safeguard against potential attacks.
Managing Implementation Costs
While the initial cost of implementing digital tools can be high, the return on investment is significant.
Manufacturers should view this cost as a long-term investment that will lead to increased efficiency, reduced waste, and higher customer satisfaction.
Skilled Workforce
The integration of digital tools requires a skilled workforce.
Manufacturers need to invest in training and development programs to equip their employees with the necessary skills.
Collaborations with educational institutions and industry bodies can also help bridge the skills gap.
The Road Ahead
The future of manufacturing is undoubtedly digital.
As technologies continue to evolve, we can expect even more innovative solutions that will further enhance customer experiences.
Virtual reality (VR) and augmented reality (AR) are poised to play a big role in product design and customization.
Blockchain technology can enhance transparency and traceability in supply chains, boosting customer confidence.
In conclusion, digital tools are unlocking new customer experiences in manufacturing by enabling customization, ensuring quality, and improving service delivery.
While there are challenges to be addressed, the potential benefits make it a worthwhile endeavor.
Manufacturers that embrace these technologies will not only thrive in a competitive market but also build lasting relationships with their customers.
資料ダウンロード
QCD調達購買管理クラウド「newji」は、調達購買部門で必要なQCD管理全てを備えた、現場特化型兼クラウド型の今世紀最高の購買管理システムとなります。
ユーザー登録
調達購買業務の効率化だけでなく、システムを導入することで、コスト削減や製品・資材のステータス可視化のほか、属人化していた購買情報の共有化による内部不正防止や統制にも役立ちます。
NEWJI DX
製造業に特化したデジタルトランスフォーメーション(DX)の実現を目指す請負開発型のコンサルティングサービスです。AI、iPaaS、および先端の技術を駆使して、製造プロセスの効率化、業務効率化、チームワーク強化、コスト削減、品質向上を実現します。このサービスは、製造業の課題を深く理解し、それに対する最適なデジタルソリューションを提供することで、企業が持続的な成長とイノベーションを達成できるようサポートします。
オンライン講座
製造業、主に購買・調達部門にお勤めの方々に向けた情報を配信しております。
新任の方やベテランの方、管理職を対象とした幅広いコンテンツをご用意しております。
お問い合わせ
コストダウンが利益に直結する術だと理解していても、なかなか前に進めることができない状況。そんな時は、newjiのコストダウン自動化機能で大きく利益貢献しよう!
(Β版非公開)