- お役立ち記事
- New employees in the rotating stopper manufacturing industry for processing machines should learn about selecting materials that have both wear resistance and stability.
New employees in the rotating stopper manufacturing industry for processing machines should learn about selecting materials that have both wear resistance and stability.
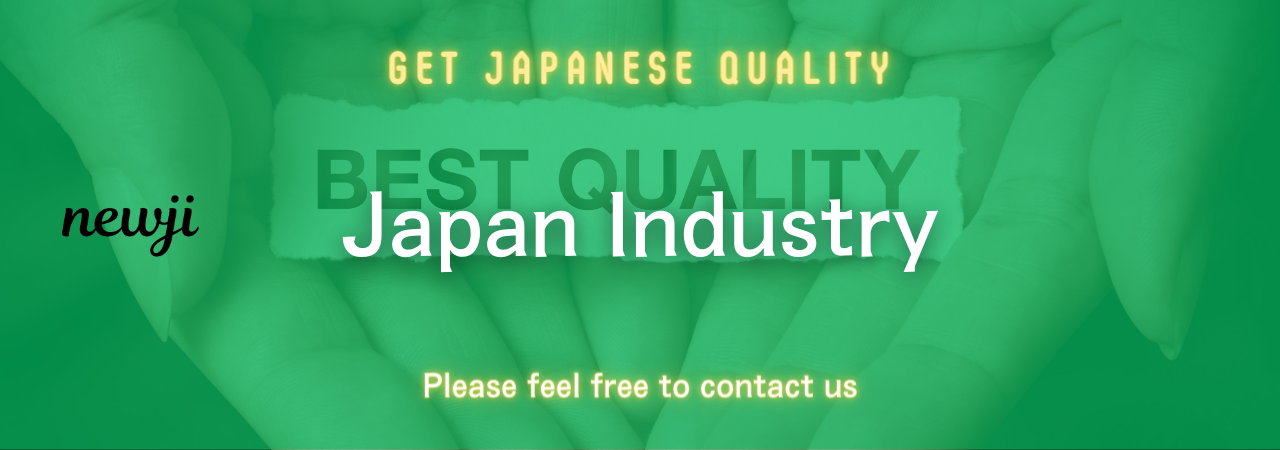
目次
Understanding the Basics of Rotating Stopper Manufacturing
When starting a career in rotating stopper manufacturing for processing machines, it’s essential to grasp the fundamentals of material selection.
The rotating stopper serves a crucial role in the function of processing machines.
These components are responsible for ensuring precision, safety, and efficiency.
Choosing the right materials is vital to achieving high performance and longevity.
The selected materials must withstand the demanding conditions these stoppers are subjected to.
As a new employee, learning about the importance of wear resistance and stability in the materials will set a foundation for future success.
Significance of Wear Resistance
Wear resistance is perhaps one of the most crucial factors when selecting materials for rotating stoppers.
These components are often exposed to friction and abrasion during their operation.
If the material lacks wear resistance, it will quickly degrade, resulting in frequent replacements, machine downtimes, and increased maintenance costs.
Understanding wear resistance requires an examination of how materials behave under stress.
Materials like high-carbon steel, ceramics, and specific alloys are often chosen for their exceptional wear-resisting properties.
These materials can endure prolonged exposure to friction without losing their structural integrity.
New employees should familiarize themselves with the wear rates of different materials.
This knowledge helps in predicting the lifespan of a component and aids in the decision-making process for material selection.
The Role of Stability in Material Selection
Besides wear resistance, stability is another critical factor to consider.
Stability refers to a material’s ability to maintain its desired properties under various operating conditions such as temperature fluctuations, load variations, and chemical exposures.
Materials that lack stability can lead to unpredictable performance, compromised safety, and operational inefficiencies.
For example, a material that is susceptible to thermal expansion could misalign during operation, causing friction and wear, negatively impacting the machine’s performance.
Knowing how materials react under different conditions allows new employees to make informed decisions about material selections and design considerations.
Stable materials like stainless steel and certain composites offer excellent resistance to environmental changes, ensuring consistent performance.
Balancing Wear Resistance and Stability
Finding the right balance between wear resistance and stability can be challenging but is essential for optimal component performance.
A highly wear-resistant material might be too rigid and lack the necessary stability, leading to potential brittleness and failure under stress.
Conversely, highly stable materials might offer less wear resistance, requiring a different approach or design to achieve the desired performance.
New employees should understand the importance of conducting comprehensive material evaluations.
This involves considering application-specific factors, such as the operational environment, rotational speed, mechanical load, and exposure to corrosive elements.
Collaborating with experienced engineers and material scientists will provide insights into achieving the desired balance between these two key properties.
Understanding Material Testing and Evaluation
A significant component of material selection involves testing and evaluation.
New employees need to become familiar with testing protocols that assess material properties such as hardness, toughness, and fatigue resistance.
These tests help determine whether a material meets the required standards for use in rotating stoppers.
Material testing might include simulated wear conditions, thermal cycle testing, and stress analysis.
Understanding the results of these tests is crucial for making informed decisions on material suitability and potential trade-offs between wear resistance and stability.
Investing time in learning about these testing methodologies will empower new employees to make data-driven choices in the manufacturing process.
This knowledge helps in finding innovative solutions to challenging design and application problems.
Collaboration with Suppliers and Experts
Building strong relationships with material suppliers and industry experts is another vital step for new employees.
These partnerships provide access to a wealth of knowledge and experience in material technology and advances in manufacturing processes.
Suppliers can offer valuable insights into the latest materials and coatings available, which can enhance wear resistance and stability.
Consulting with experts helps in understanding the trade-offs involved and finding the best solutions to meet design specifications and operational requirements.
Attending industry conferences, trade shows, and seminars is an excellent way for new employees to stay updated on trends and innovations in material science and manufacturing technology.
Continuous Learning and Adaptation
The rotating stopper manufacturing industry is continually evolving, driven by advancements in material science and engineering practices.
New employees should approach their careers with a commitment to continuous learning.
This continuously expanding knowledge base allows them to adapt to new challenges and leverage technological advancements effectively.
Taking part in training programs, seeking mentorship, and engaging in cross-functional projects encourage skill development.
This ensures that employees remain effective contributors to the field.
Staying informed about emerging materials and technologies will keep them at the forefront of the industry.
It provides opportunities to drive innovation within their organizations.
Conclusion
Material selection in the rotating stopper manufacturing industry is a complex yet rewarding task.
New employees entering this field must focus on gaining a deep understanding of the properties of wear resistance and stability.
Balancing these properties plays a critical role in producing high-quality components.
Such components contribute significantly to the overall efficiency and reliability of processing machines.
Through continuous learning, testing, and collaboration with experts, new employees can excel in selecting the appropriate materials.
They will play a key role in helping their companies push the boundaries of machine efficiency and performance.
資料ダウンロード
QCD調達購買管理クラウド「newji」は、調達購買部門で必要なQCD管理全てを備えた、現場特化型兼クラウド型の今世紀最高の購買管理システムとなります。
ユーザー登録
調達購買業務の効率化だけでなく、システムを導入することで、コスト削減や製品・資材のステータス可視化のほか、属人化していた購買情報の共有化による内部不正防止や統制にも役立ちます。
NEWJI DX
製造業に特化したデジタルトランスフォーメーション(DX)の実現を目指す請負開発型のコンサルティングサービスです。AI、iPaaS、および先端の技術を駆使して、製造プロセスの効率化、業務効率化、チームワーク強化、コスト削減、品質向上を実現します。このサービスは、製造業の課題を深く理解し、それに対する最適なデジタルソリューションを提供することで、企業が持続的な成長とイノベーションを達成できるようサポートします。
オンライン講座
製造業、主に購買・調達部門にお勤めの方々に向けた情報を配信しております。
新任の方やベテランの方、管理職を対象とした幅広いコンテンツをご用意しております。
お問い合わせ
コストダウンが利益に直結する術だと理解していても、なかなか前に進めることができない状況。そんな時は、newjiのコストダウン自動化機能で大きく利益貢献しよう!
(Β版非公開)