- お役立ち記事
- New exploration methods and technological approaches in chemical processing of powders and granules
月間77,185名の
製造業ご担当者様が閲覧しています*
*2025年2月28日現在のGoogle Analyticsのデータより
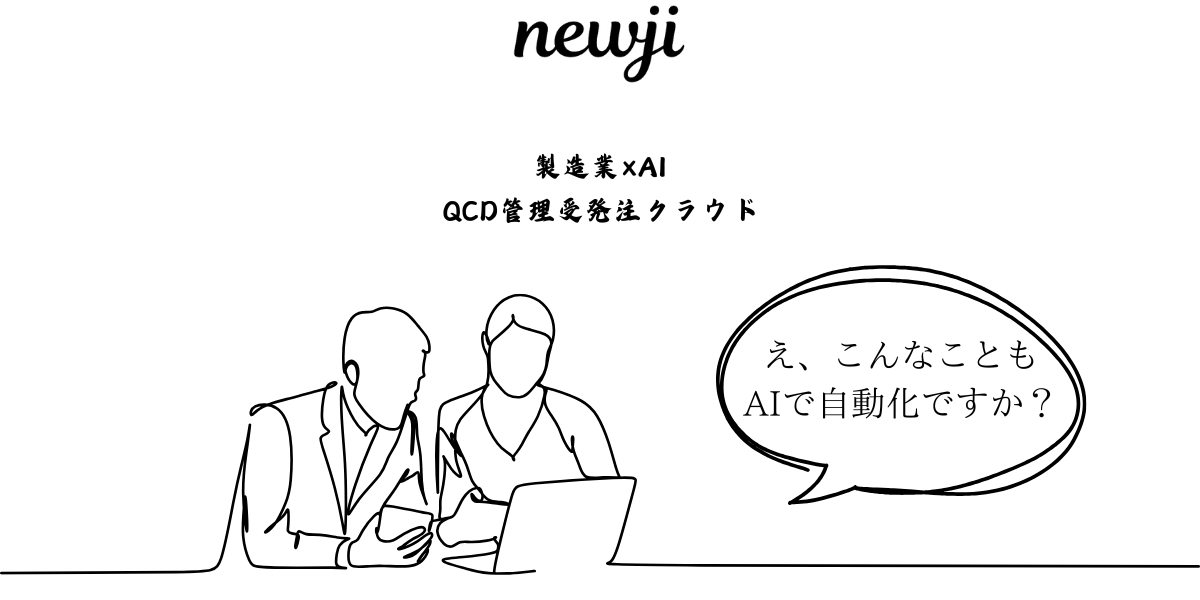
New exploration methods and technological approaches in chemical processing of powders and granules
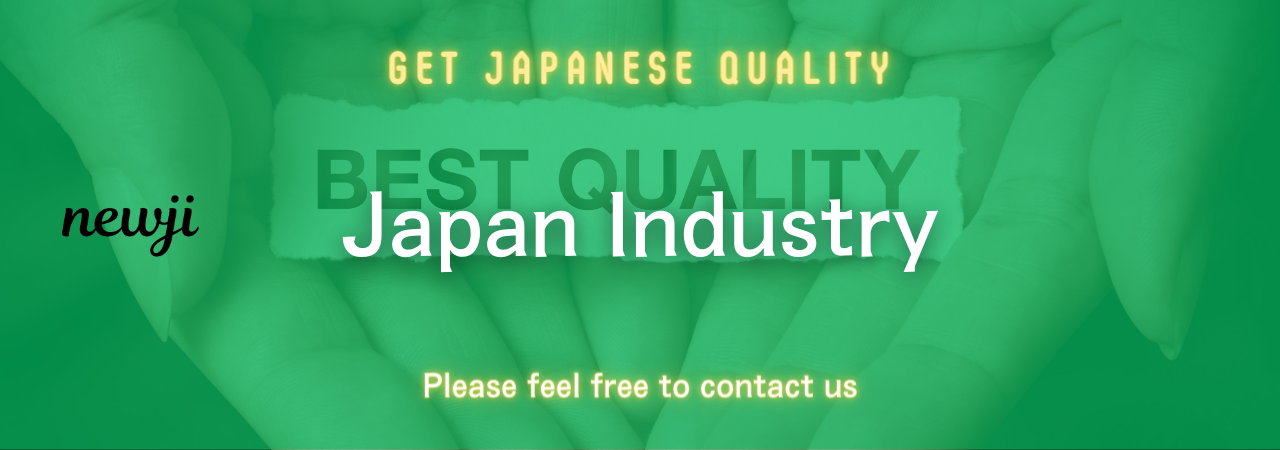
目次
Introduction to Chemical Processing of Powders and Granules
The chemical processing of powders and granules plays a pivotal role in various industries, including pharmaceuticals, food, and materials engineering.
These processes are essential for transforming raw materials into finer and more usable forms, ensuring enhanced quality and efficiency in production cycles.
In recent years, the evolution of new exploration methods and technological approaches has revolutionized how these materials are processed.
In this article, we will explore these innovative methods and technologies that have significantly improved chemical processing.
Understanding Chemical Processing in Powder and Granule Form
Chemical processing involves the transformation of raw materials into desired end products through various chemical reactions and physical alterations.
In the context of powders and granules, this processing requires precision and specificity to ensure optimal results.
Powders are finely ground particles, while granules are aggregates of powders often formed into larger shapes for specific applications.
These materials are widely used across industries like medicine, where the size and consistency of powder can affect drug delivery efficiency.
Traditional Methods in Chemical Processing
Historically, chemical processing relied heavily on mechanical methods, such as grinding and milling, to achieve the desired consistency in powders and granules.
These conventional methods, though effective, often faced limitations regarding energy consumption, material waste, and environmental impact.
Traditional grinding and milling processes may produce excessive dust or require high energy input, which can lead to inefficiencies and additional costs.
Moreover, these methods may not always deliver the necessary precision, resulting in variance in particle size distribution and impacting the overall quality of the processed material.
New Exploration Methods and Technological Advances
Nanotechnology
Nanotechnology has emerged as a groundbreaking advancement in the chemical processing of powders and granules.
By manipulating materials at the molecular or atomic level, this technology facilitates precise control over particle size and distribution.
It allows for the creation of nanoparticles that possess unique properties, enhancing the efficiency and functionality of the end product.
In pharmaceuticals, for instance, nanotechnology enables the development of drugs with controlled release mechanisms, improving therapeutic outcomes and patient compliance.
3D Printing
3D printing, or additive manufacturing, offers a novel approach to processing powdered materials.
This technology involves the layer-by-layer construction of objects, directly utilizing powdered materials.
3D printing provides a high degree of customization and precision, enabling the fabrication of complex shapes and structures that were previously challenging to achieve.
Applications of 3D printing in sectors such as aerospace and healthcare are expanding, allowing for the production of lightweight, yet robust components with excellent precision and reduced waste.
Advanced Milling Techniques
Advanced milling techniques, such as jet milling and cryogenic milling, have significantly improved the efficiency and effectiveness of powder processing.
Jet milling utilizes high-velocity air streams to grind materials, achieving ultra-fine powders without the need for mechanical grinding implements.
This reduces contamination and energy consumption, making the process more sustainable.
Cryogenic milling, on the other hand, involves the use of liquid nitrogen to cool materials before pulverizing them.
This technique is particularly useful for processing materials that are heat-sensitive, preventing thermal degradation and preserving material integrity.
Environmental and Economic Benefits
The adoption of new exploration methods and technological approaches in chemical processing offers significant environmental and economic benefits.
These methods often reduce energy consumption and minimize waste, leading to more sustainable manufacturing practices.
For example, the precision offered by nanotechnology and 3D printing minimizes excess material use, which in turn reduces waste production and environmental impact.
Additionally, these advances can lead to cost savings due to increased efficiency and reduced resource requirements.
Industries that incorporate these innovations may benefit from lowered operational costs, improved product quality, and a competitive edge in the market.
Challenges and Considerations
Despite the numerous advantages, there are challenges and considerations associated with the adoption of new exploration methods in chemical processing.
For one, the initial cost of implementing advanced technologies like nanotechnology and 3D printing can be high, potentially deterring smaller enterprises.
Furthermore, these technologies require skilled personnel for operation and maintenance, necessitating investment in training and development.
Regulatory considerations also play a crucial role, especially in industries like pharmaceuticals, where stringent standards must be met to ensure product safety and efficacy.
Future Directions in Chemical Processing
The future of chemical processing in powders and granules is promising, with ongoing research directed toward further innovations.
Potential areas of growth include the development of more environmentally friendly processing techniques and the integration of artificial intelligence (AI) for predictive modeling and process optimization.
AI can provide insights into the most efficient processing conditions, enabling real-time adjustments and enhancing process control.
Moreover, the continuous exploration of hybrid technologies that combine existing methods with new innovations is likely to drive further improvements in processing efficiency and quality.
Conclusion
The chemical processing of powders and granules is undergoing significant transformation due to new exploration methods and technological advances.
From nanotechnology and 3D printing to advanced milling techniques, these innovations offer enhanced precision, efficiency, and sustainability.
While challenges remain, the potential benefits for industries are substantial, paving the way for high-quality products and reduced environmental impact.
As these technologies continue to evolve, they will undoubtedly shape the future landscape of manufacturing, offering exciting possibilities for further exploration and advancement.
資料ダウンロード
QCD管理受発注クラウド「newji」は、受発注部門で必要なQCD管理全てを備えた、現場特化型兼クラウド型の今世紀最高の受発注管理システムとなります。
ユーザー登録
受発注業務の効率化だけでなく、システムを導入することで、コスト削減や製品・資材のステータス可視化のほか、属人化していた受発注情報の共有化による内部不正防止や統制にも役立ちます。
NEWJI DX
製造業に特化したデジタルトランスフォーメーション(DX)の実現を目指す請負開発型のコンサルティングサービスです。AI、iPaaS、および先端の技術を駆使して、製造プロセスの効率化、業務効率化、チームワーク強化、コスト削減、品質向上を実現します。このサービスは、製造業の課題を深く理解し、それに対する最適なデジタルソリューションを提供することで、企業が持続的な成長とイノベーションを達成できるようサポートします。
製造業ニュース解説
製造業、主に購買・調達部門にお勤めの方々に向けた情報を配信しております。
新任の方やベテランの方、管理職を対象とした幅広いコンテンツをご用意しております。
お問い合わせ
コストダウンが利益に直結する術だと理解していても、なかなか前に進めることができない状況。そんな時は、newjiのコストダウン自動化機能で大きく利益貢献しよう!
(β版非公開)