- お役立ち記事
- New manufacturing technology for solvent-resistant bottles using PVDF resin
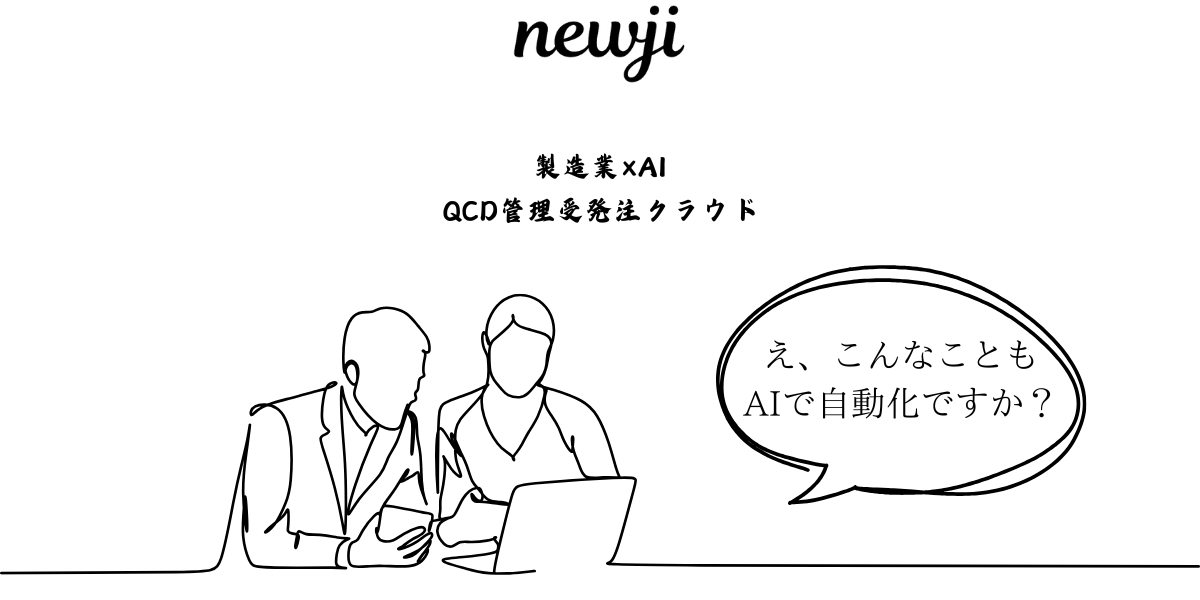
New manufacturing technology for solvent-resistant bottles using PVDF resin
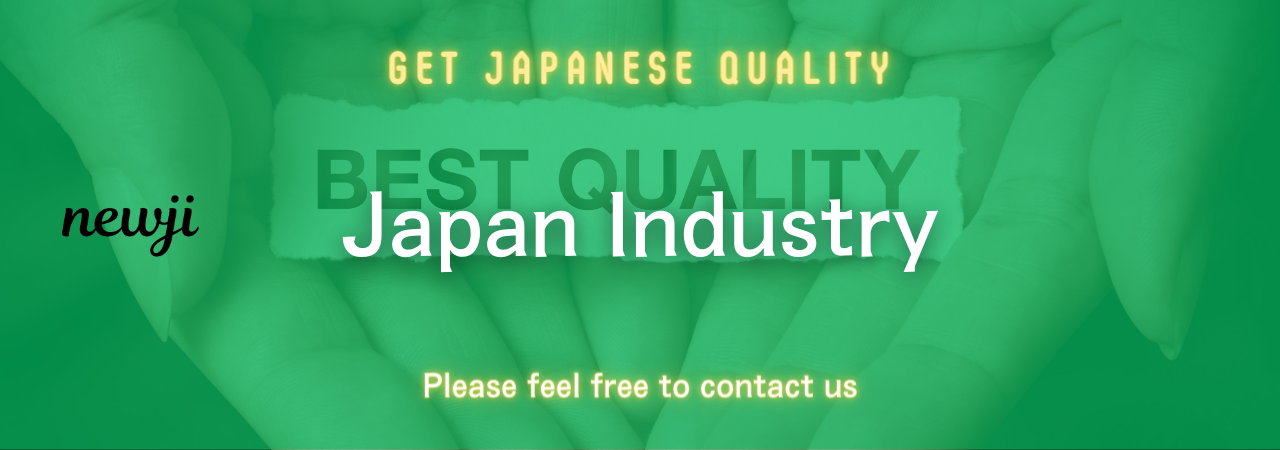
目次
Introduction to PVDF Resin in Manufacturing
Polyvinylidene fluoride (PVDF) resin is rapidly becoming a key material in the manufacturing industry due to its unique properties.
This synthetic polymer is valued for its chemical resistance, making it an ideal choice for producing solvent-resistant bottles and containers.
With increasing demands for durable and reliable packaging solutions, industries are focusing on utilizing PVDF resin in innovative ways.
The Importance of Solvent-Resistant Bottles
The need for solvent-resistant bottles arises from their application in storing and transporting aggressive chemicals and solvents.
Traditional materials often fall short, failing to provide adequate protection and risking contamination or spillage.
PVDF resin offers a robust alternative due to its superior mechanical strength and resistance to chemical degradation.
This ensures the safe handling and longevity of the products, significantly reducing the risk of leaks or damages during transport.
Advantages of Using PVDF Resin
PVDF resin is favored in manufacturing due to several intrinsic qualities.
Firstly, its remarkable chemical resistance allows it to maintain structural integrity even when exposed to harsh chemicals like acids, bases, or hydrocarbons.
Additionally, it exhibits a high thermal stability, performing well under extreme temperature conditions without deforming or losing its protective properties.
Moreover, PVDF resin is known for its excellent mechanical strength.
This means that containers made from this material are not only resilient against chemical attacks but also against physical stress, abrasions, and impacts.
Its low coefficient of friction also contributes to ease of handling and transportation, reducing wear and tear in frequently used products.
Easy Processing and Versatility
Another noteworthy advantage of PVDF resin is its adaptability in the manufacturing process.
Its thermal processing capabilities allow for various forms, such as injection molding, extrusion, and welding.
This flexibility facilitates the creation of custom-designed bottles and containers tailored to specific industrial needs.
Furthermore, PVDF resin can be easily combined with other polymers or additives to enhance its properties even further.
Such modifications can improve aspects like UV resistance, flame retardancy, and clarity, expanding the areas of application beyond chemical containment.
Innovative Manufacturing Technologies
Recent developments in technology have led to more efficient methods for producing solvent-resistant bottles using PVDF resin.
One of the key advancements is the improvement in extrusion technologies.
These allow for better control over the thickness and dimensions of the bottles, thereby enhancing their strength and durability.
Additionally, new molding techniques have been developed to minimize material waste while improving precision in the production process.
Automation and robotics have also played significant roles, ensuring consistency and reducing human error, which leads to higher quality products.
Eco-Friendly Production Methods
Manufacturers are also exploring environmentally friendly production methods.
PVDF resin’s recyclability is an attractive feature in efforts to reduce industrial waste and environmental impact.
Innovative recycling techniques are being employed to reuse PVDF components without degrading their quality, promoting sustainability in manufacturing practices.
Energy-efficient production processes are also being integrated, harnessing renewable energy sources and reducing reliance on fossil fuels.
These steps highlight the industry’s commitment to not only advancing solvent-resistant technologies but also ensuring they align with environmental goals.
Applications and Market Impact
The versatility of PVDF resin in manufacturing solvent-resistant bottles extends its applications across various sectors.
Industries such as pharmaceuticals, agriculture, and chemicals significantly benefit from the robustness and dependability of PVDF resin containers.
They provide an impermeable barrier against potential leaks and contamination, ensuring the safety and effectiveness of stored substances.
The market impact of this technology is expected to grow as more industries recognize the benefits of integrating PVDF resin into their packaging solutions.
The demand for chemical-resistant, durable packaging materials is on the rise, offering manufacturers a vast opportunity for market expansion and innovation.
Future Prospects of PVDF Resin in Manufacturing
Looking ahead, the future prospects of using PVDF resin in manufacturing solvent-resistant bottles are promising.
Continuous advancements in material science will likely enhance PVDF’s attributes, introducing new variations tailored to specific industrial challenges.
Research and development are poised to unlock new applications, potentially expanding PVDF’s reach into sectors like electronics, where its properties could benefit components that demand durability and chemical resistance.
Moreover, as global regulatory frameworks increasingly emphasize sustainability, PVDF resin’s eco-friendly properties position it advantageously.
Investments in green manufacturing technologies will likely align closely with PVDF resin’s capabilities, further driving its adoption.
Conclusion
PVDF resin stands out in the manufacturing industry as a top choice for producing solvent-resistant bottles.
Its inherent properties of chemical resistance, mechanical strength, and versatility mark it as an indispensable material in modern manufacturing.
The continued development of innovative technologies promises to enhance PVDF’s role in delivering safe, sustainable packaging solutions across industries.
With its wide range of applications and future growth prospects, PVDF resin is set to reshape the landscape of durable packaging.
It aligns with both industrial needs and environmental goals, paving the way for a safer and more sustainable future.
資料ダウンロード
QCD調達購買管理クラウド「newji」は、調達購買部門で必要なQCD管理全てを備えた、現場特化型兼クラウド型の今世紀最高の購買管理システムとなります。
ユーザー登録
調達購買業務の効率化だけでなく、システムを導入することで、コスト削減や製品・資材のステータス可視化のほか、属人化していた購買情報の共有化による内部不正防止や統制にも役立ちます。
NEWJI DX
製造業に特化したデジタルトランスフォーメーション(DX)の実現を目指す請負開発型のコンサルティングサービスです。AI、iPaaS、および先端の技術を駆使して、製造プロセスの効率化、業務効率化、チームワーク強化、コスト削減、品質向上を実現します。このサービスは、製造業の課題を深く理解し、それに対する最適なデジタルソリューションを提供することで、企業が持続的な成長とイノベーションを達成できるようサポートします。
オンライン講座
製造業、主に購買・調達部門にお勤めの方々に向けた情報を配信しております。
新任の方やベテランの方、管理職を対象とした幅広いコンテンツをご用意しております。
お問い合わせ
コストダウンが利益に直結する術だと理解していても、なかなか前に進めることができない状況。そんな時は、newjiのコストダウン自動化機能で大きく利益貢献しよう!
(Β版非公開)