- お役立ち記事
- New metrics to guide purchasing departments in optimizing the entire supply chain
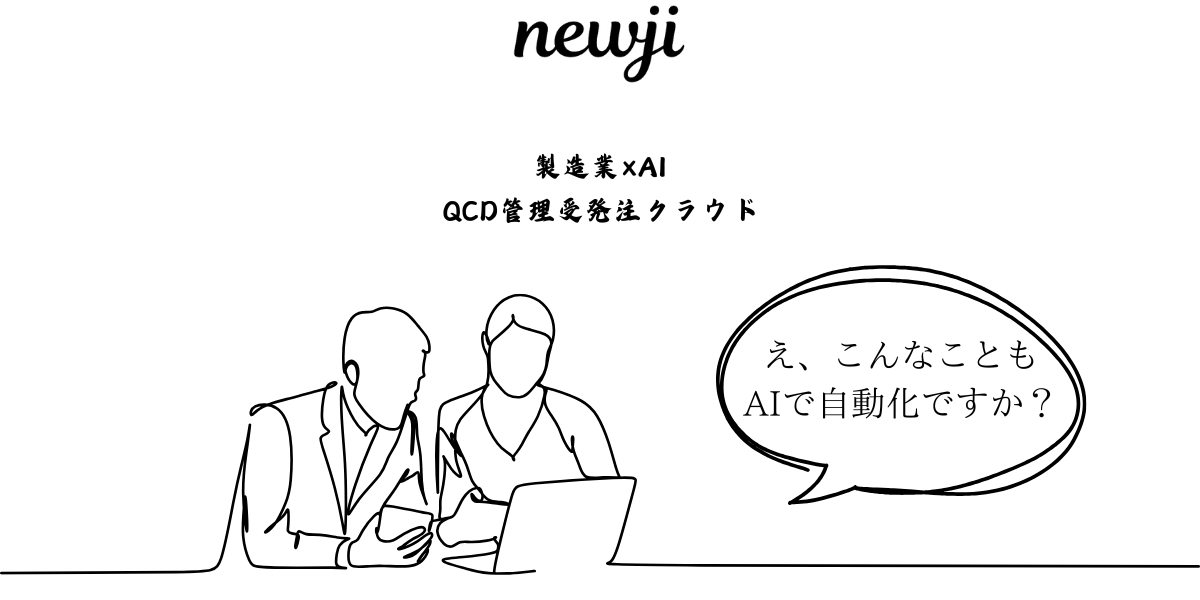
New metrics to guide purchasing departments in optimizing the entire supply chain
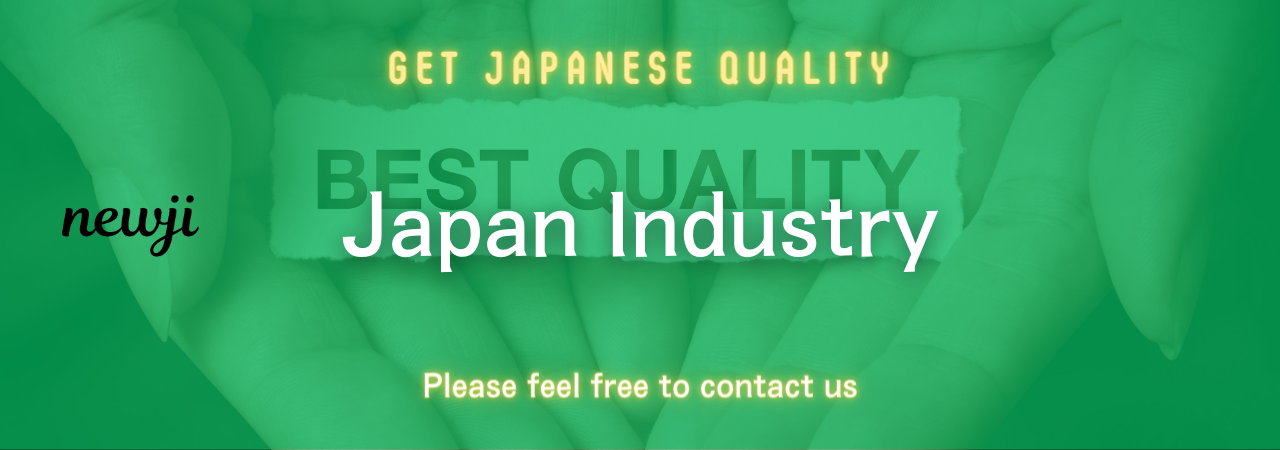
目次
Understanding Supply Chain Optimization
In today’s fast-paced global market, optimizing the supply chain is a key priority for many companies.
Purchasing departments play a crucial role in this process by managing procurement strategies and supplier relationships.
To ensure efficiency and competitiveness, new metrics are being developed to guide purchasing departments in optimizing the entire supply chain.
Why Supply Chain Optimization Matters
Supply chain optimization is critical because it helps businesses reduce costs, increase efficiency, and improve customer satisfaction.
A streamlined supply chain can result in faster delivery times, reduced inventory costs, and improved product quality.
By focusing on optimization, companies can better respond to market demands and maintain a competitive edge.
The Role of Purchasing Departments
Purchasing departments are at the forefront of supply chain management, facilitating the acquisition of goods and services needed for production.
They are responsible for selecting suppliers, negotiating contracts, and managing supplier relationships.
By optimizing these processes, purchasing departments can significantly impact the overall performance of the supply chain.
Introducing New Metrics for Optimization
To enhance the capabilities of purchasing departments, new metrics are being developed to guide decision-making and strategy.
These metrics focus on several key areas that are essential for supply chain optimization.
Supplier Performance Metrics
Supplier performance metrics are designed to evaluate the reliability and efficiency of suppliers.
These metrics might include on-time delivery rates, quality of goods received, and responsiveness to inquiries.
By tracking these metrics, purchasing departments can identify high-performing suppliers and foster strong partnerships.
Cost Efficiency Metrics
Cost efficiency metrics help purchasing departments analyze procurement costs and identify savings opportunities.
This includes tracking expenses associated with purchasing goods, managing inventory, and fulfilling orders.
By understanding these costs, departments can develop strategies to minimize expenses and maximize value.
Inventory Management Metrics
Effective inventory management is essential for supply chain optimization.
Metrics such as inventory turnover rates, order accuracy, and stockout occurrences help departments monitor inventory levels and adjust processes accordingly.
By optimizing inventory management, companies can reduce waste, avoid overstocking, and meet customer demand more effectively.
Implementing the New Metrics
Adopting new metrics requires a strategic approach and commitment from the entire organization.
Purchasing departments must collaborate with other departments to integrate these metrics into existing processes and systems.
Data Collection and Analysis
Effective metric implementation begins with accurate data collection.
Purchasing departments need access to real-time data from suppliers, financial systems, and inventory management software.
Advanced analytics tools can help interpret this data, providing insights into performance and identifying areas for improvement.
Continuous Improvement Initiatives
Metrics are most effective when used as part of a continuous improvement initiative.
Purchasing departments should regularly review metric results and use them to identify opportunities for process enhancements.
By fostering a culture of continuous improvement, companies can ensure sustained optimization and adapt to changing market conditions.
Challenges and Considerations
While implementing new metrics can lead to significant benefits, organizations may face several challenges.
Data Accuracy and Reliability
Reliable data is essential for accurate metrics.
Organizations must invest in robust data management systems to ensure data is accurate, up-to-date, and secure.
This may require additional resources and training for employees.
Integration with Existing Processes
Integrating new metrics into existing purchasing processes can be complex.
Organizations should develop a clear implementation plan that aligns with their overall supply chain goals.
This could involve updating software systems or restructuring workflows.
Cultural Resistance
Changes in metrics and processes may be met with resistance from employees.
Organizations should communicate the benefits of new metrics clearly and involve employees in the implementation process.
Training programs and open communication can help ease the transition and encourage buy-in from all stakeholders.
The Future of Supply Chain Optimization
As technology continues to advance, new opportunities for supply chain optimization will emerge.
Purchasing departments must remain agile and open to adopting new metrics and tools.
Leveraging Technology for Greater Insight
Technologies like artificial intelligence and machine learning are revolutionizing supply chain management.
By leveraging these technologies, purchasing departments can gain deeper insights into supplier performance, cost efficiency, and inventory management.
This allows for more informed decision-making and more precise optimization strategies.
Fostering Collaborative Supply Chains
The future of supply chain optimization relies on collaboration between all stakeholders, including suppliers, manufacturers, and customers.
By fostering strong, collaborative supply chains, companies can improve transparency, responsiveness, and overall performance.
New metrics can serve as a foundation for these collaborative efforts by providing a common framework for evaluating performance.
In conclusion, by adopting new metrics and embracing technology, purchasing departments can play a vital role in optimizing the entire supply chain.
This approach not only enhances efficiency and reduces costs but also leads to improved customer satisfaction and competitiveness in the global market.
資料ダウンロード
QCD調達購買管理クラウド「newji」は、調達購買部門で必要なQCD管理全てを備えた、現場特化型兼クラウド型の今世紀最高の購買管理システムとなります。
ユーザー登録
調達購買業務の効率化だけでなく、システムを導入することで、コスト削減や製品・資材のステータス可視化のほか、属人化していた購買情報の共有化による内部不正防止や統制にも役立ちます。
NEWJI DX
製造業に特化したデジタルトランスフォーメーション(DX)の実現を目指す請負開発型のコンサルティングサービスです。AI、iPaaS、および先端の技術を駆使して、製造プロセスの効率化、業務効率化、チームワーク強化、コスト削減、品質向上を実現します。このサービスは、製造業の課題を深く理解し、それに対する最適なデジタルソリューションを提供することで、企業が持続的な成長とイノベーションを達成できるようサポートします。
オンライン講座
製造業、主に購買・調達部門にお勤めの方々に向けた情報を配信しております。
新任の方やベテランの方、管理職を対象とした幅広いコンテンツをご用意しております。
お問い合わせ
コストダウンが利益に直結する術だと理解していても、なかなか前に進めることができない状況。そんな時は、newjiのコストダウン自動化機能で大きく利益貢献しよう!
(Β版非公開)