- お役立ち記事
- New Opportunities Brought to Manufacturing by Distributed Energy Resources
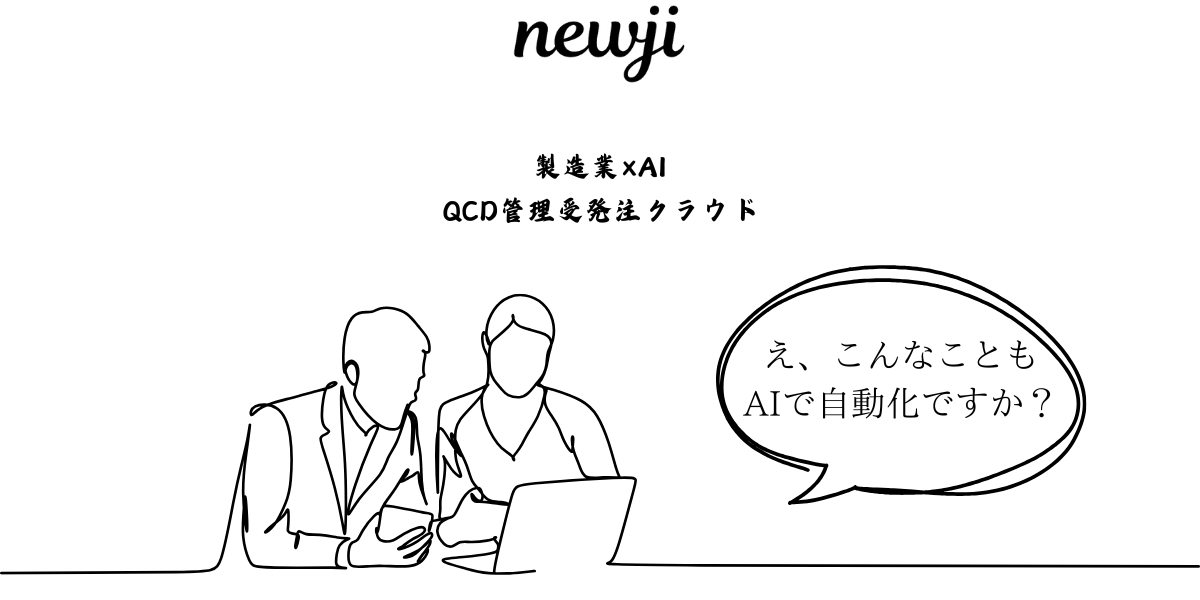
New Opportunities Brought to Manufacturing by Distributed Energy Resources
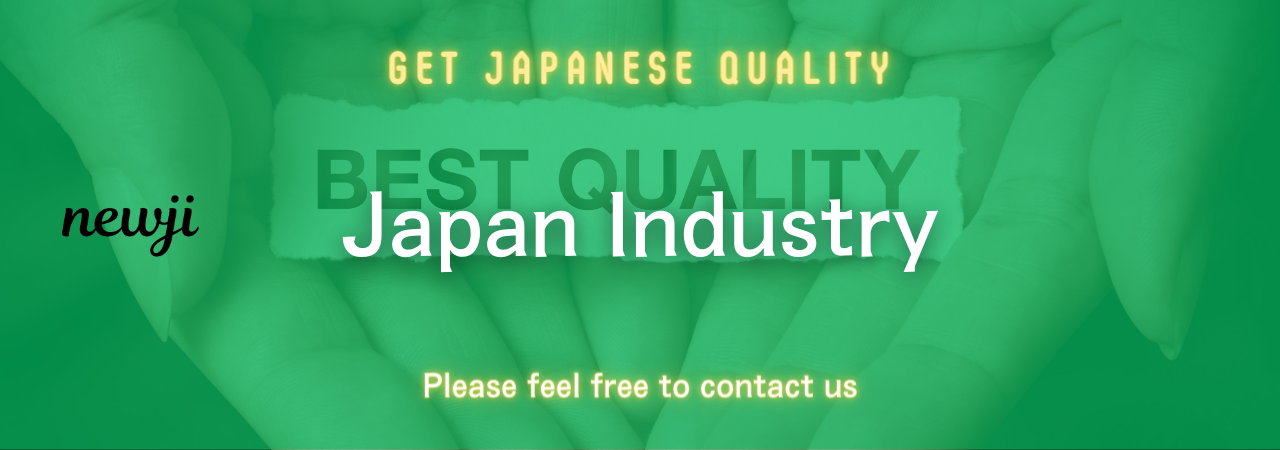
The rise of distributed energy resources (DERs) is transforming various industries, and manufacturing is one of them.
These new energy solutions are bringing numerous opportunities to the manufacturing sector, enabling industries to be more efficient, cost-effective, and environmentally friendly.
In this article, we will explore how DERs are reshaping the manufacturing landscape.
目次
Understanding Distributed Energy Resources (DERs)
Distributed Energy Resources, or DERs, refer to a variety of small-scale electricity generation and storage systems located close to where electricity is used.
Examples of DERs include solar panels, wind turbines, energy storage systems like batteries, and combined heat and power (CHP) systems.
These energy resources are decentralized, unlike traditional power plants that generate electricity at a central location and distribute it over long distances.
The Importance of DERs in Modern Manufacturing
Manufacturing facilities are large consumers of energy, which often translates to high operational costs and a substantial carbon footprint.
Integrating DERs into manufacturing processes can mitigate these challenges in several ways.
First, DERs make it possible for manufacturing plants to generate their own electricity, reducing dependency on the grid.
This not only lowers energy costs but also provides a reliable power supply that can minimize production downtime.
Second, using clean energy sources such as solar and wind reduces greenhouse gas emissions, helping companies meet sustainability goals.
Cost Savings and Efficiency Improvements
One of the most compelling benefits of DERs in manufacturing is cost savings.
By generating electricity on-site, manufacturing facilities can significantly reduce their electricity bills.
Furthermore, energy storage systems can store excess energy generated during periods of low demand and use it when energy costs are higher, optimizing energy use and lowering costs.
DERs can also improve energy efficiency by enabling the use of combined heat and power systems, which capture and use heat wasted in electricity generation.
This increases overall efficiency and cuts down on fuel costs.
Case Study: Solar Panels in Manufacturing
Many manufacturing facilities are already reaping the benefits of DERs.
For instance, a large automotive parts manufacturer installed solar panels on the roofs of its facilities.
The solar panels generated 30 percent of the factory’s electricity needs, reducing reliance on the grid and cutting energy costs.
Additionally, the company received tax incentives for using renewable energy, providing further financial benefits.
This successful implementation demonstrates how DERs can make a significant impact on the bottom line.
Enhancing Energy Resilience and Reliability
In today’s competitive market, manufacturers cannot afford production disruptions.
Power outages can lead to downtime, resulting in financial losses.
DERs offer an effective solution by providing a reliable and consistent energy supply.
For example, battery energy storage systems can provide backup power during outages, ensuring that manufacturing operations continue without interruption.
This energy resilience is crucial in regions prone to natural disasters or unstable grid conditions.
By having a dependable energy source, manufacturers can maintain continuous production and avoid costly downtimes.
Energy Management and Grid Independence
With DERs, manufacturing facilities can take advantage of advanced energy management systems.
These systems analyze energy consumption patterns and make real-time adjustments to optimize energy use.
For instance, during peak demand periods, the system can shift to using stored energy, minimizing peak demand charges.
Moreover, DERs allow for greater grid independence.
Manufacturers can decouple from the grid during periods of high electricity prices or grid instability, using their own generated and stored energy instead.
This flexibility provides significant economic advantages and enhances energy security.
Supporting Sustainability Goals
Environmental concerns are increasingly important for both businesses and consumers.
Integrating DERs in manufacturing aligns with global sustainability goals by reducing greenhouse gas emissions and reliance on non-renewable energy sources.
Using renewable energy sources like solar and wind decreases the carbon footprint of manufacturing operations.
As a result, companies can market themselves as environmentally responsible, boosting their brand image and appeal to eco-conscious consumers.
Regulatory Compliance and Incentives
Governments and regulatory bodies worldwide are implementing stricter environmental regulations and offering incentives for renewable energy adoption.
Manufacturers using DERs can comply with these regulations more easily and take advantage of financial incentives such as tax credits, grants, and rebates.
These incentives further lower the overall costs of adopting DERs, making them an attractive option for manufacturers looking to reduce their environmental impact and manage costs effectively.
Future Prospects and Innovation
The future of DERs in manufacturing looks promising, with continuous advancements in technology making these systems more efficient and affordable.
Research and development in energy storage, smart grids, and renewable energy technologies are paving the way for more innovative solutions.
Emerging technologies such as microgrids — small-scale power grids that can operate independently or in conjunction with the main grid — are gaining traction.
Microgrids offer increased control over energy use and enhance resilience against disruptions.
Conclusion: Embracing the Shift
The opportunities that Distributed Energy Resources bring to manufacturing are vast and transformative.
From cost savings and energy efficiency to sustainability and grid independence, DERs offer numerous benefits that can drive the industry forward.
As technology continues to evolve, the integration of DERs will become even more vital for manufacturers seeking to stay competitive in an increasingly eco-conscious and cost-sensitive market.
Embracing this shift not only makes good business sense but also contributes to a more sustainable future for all.
資料ダウンロード
QCD調達購買管理クラウド「newji」は、調達購買部門で必要なQCD管理全てを備えた、現場特化型兼クラウド型の今世紀最高の購買管理システムとなります。
ユーザー登録
調達購買業務の効率化だけでなく、システムを導入することで、コスト削減や製品・資材のステータス可視化のほか、属人化していた購買情報の共有化による内部不正防止や統制にも役立ちます。
NEWJI DX
製造業に特化したデジタルトランスフォーメーション(DX)の実現を目指す請負開発型のコンサルティングサービスです。AI、iPaaS、および先端の技術を駆使して、製造プロセスの効率化、業務効率化、チームワーク強化、コスト削減、品質向上を実現します。このサービスは、製造業の課題を深く理解し、それに対する最適なデジタルソリューションを提供することで、企業が持続的な成長とイノベーションを達成できるようサポートします。
オンライン講座
製造業、主に購買・調達部門にお勤めの方々に向けた情報を配信しております。
新任の方やベテランの方、管理職を対象とした幅広いコンテンツをご用意しております。
お問い合わせ
コストダウンが利益に直結する術だと理解していても、なかなか前に進めることができない状況。そんな時は、newjiのコストダウン自動化機能で大きく利益貢献しよう!
(Β版非公開)