- お役立ち記事
- New standards for quality control in material procurement Checkpoints that purchasing departments should keep in mind
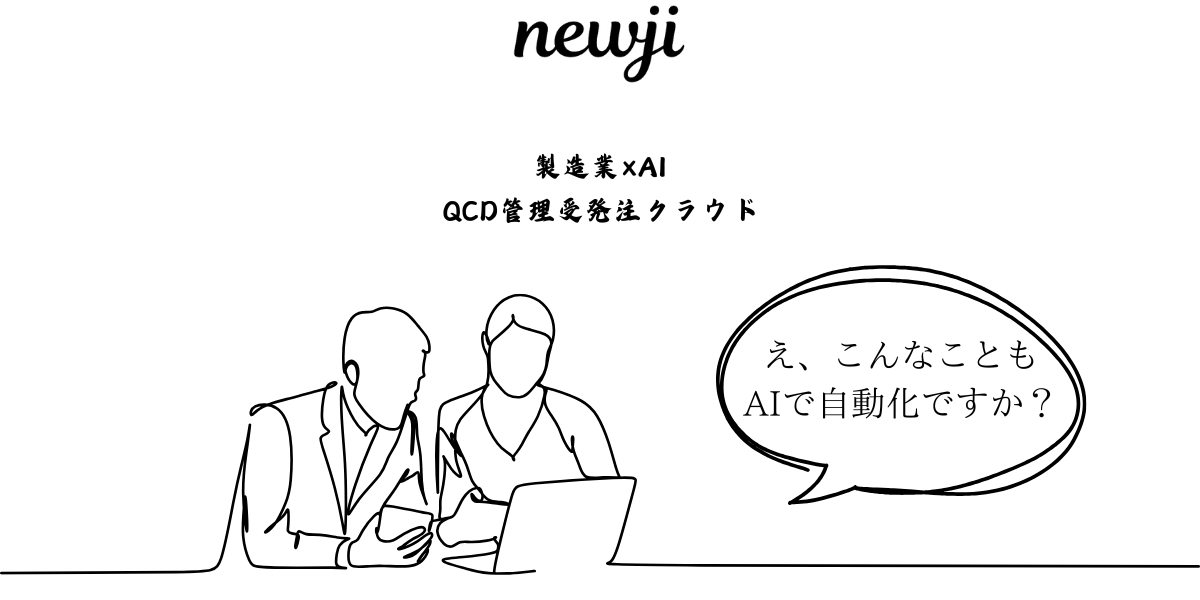
New standards for quality control in material procurement Checkpoints that purchasing departments should keep in mind
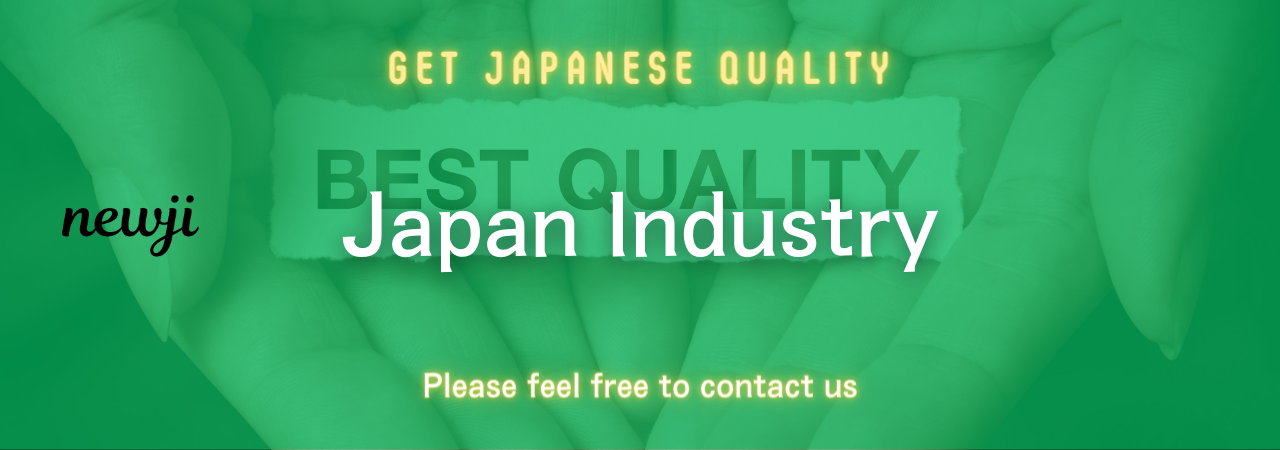
目次
Understanding the Importance of Quality Control in Material Procurement
Procurement plays a vital role in the overall success of any organization, especially when it comes to material supplies.
In recent years, the emphasis on quality control has significantly increased, leading to new standards being adopted across industries.
For the purchasing department, understanding and implementing these quality control measures is essential to ensure seamless operational flow.
When we talk about quality control in material procurement, it isn’t just about inspecting the materials once they arrive.
It’s about establishing a robust system that assures quality at every stage of the procurement process.
From selecting suppliers to receiving goods, every checkpoint is crucial in maintaining the quality standards.
Checkpoints in Material Procurement
For purchasing departments, certain checkpoints are pivotal in upholding new quality standards.
These checkpoints serve as guidelines that help in maintaining consistency and reliability in the quality of materials procured.
Supplier Selection and Evaluation
Choosing the right supplier is the first step toward ensuring quality.
The purchasing department must evaluate potential suppliers based on their track records, compliance with industry standards, and their quality management systems.
It’s important to have a supplier selection process that includes references, site visits, and conversations with other clients to assess the supplier’s credibility and capability.
Contractual Agreements and Quality Clauses
Once a supplier is selected, it is crucial to have detailed contractual agreements that include quality clauses.
These clauses should outline the material specifications, quality requirements, inspection processes, and the repercussions of not meeting these quality standards.
Clear communication and legally binding agreements help in setting clear expectations and reducing disputes.
Material Inspection and Testing
Upon receipt of materials, the purchasing department should have a well-defined process for inspection and testing.
It should involve checks to ensure that materials meet the specified quality criteria.
This can include visual inspections, quality testing, and cross-verification with purchase order specifications.
Having a dedicated team for inspection ensures that no detail is overlooked, and only materials that meet standards are approved.
Document Management and Traceability
Maintaining proper documentation is a key aspect of quality control.
This includes keeping records of purchase orders, quality inspections, test results, and supplier communications.
Having a traceability system in place allows the purchasing department to track materials from the supplier to the end product.
This traceability is crucial in case of recalls or quality disputes.
Leveraging Technology for Quality Control
The advancements in technology have revolutionized quality control processes in material procurement.
Purchasing departments can leverage technology to streamline operations and enhance quality assurance.
Use of Procurement Software
Procurement software assists purchasing departments in managing the entire procurement process efficiently.
It provides tools for supplier management, order tracking, and quality monitoring.
Using such software can help in maintaining a centralized database, offering transparency and accessibility to information when needed.
Data Analytics for Supplier Evaluation
Data analytics can play an impactful role in evaluating supplier performance over time.
By analyzing trends and patterns in supplier performance, the purchasing department can make informed decisions on whether to continue partnerships or look for new suppliers.
Metrics such as on-time delivery, defect rates, and compliance with quality standards are useful indicators that data analytics can provide.
Real-time Quality Monitoring
Integration of IoT (Internet of Things) devices allows for real-time monitoring of quality during the supply chain process.
These technologies can alert the purchasing department about potential quality issues as they happen, allowing for immediate corrective actions.
This proactive approach helps in reducing the risks associated with quality discrepancies.
The Impact of Quality Control on Business Operations
Implementing stringent quality control standards in material procurement does not just assure quality but also has a positive ripple effect across different areas of business operations.
Enhancement of Product Quality
When materials are consistently high in quality, it directly reflects in the quality of the end products.
Producing high-quality products boosts customer satisfaction and fosters brand loyalty, which is vital for long-term business success.
Reduction in Costs
Focusing on quality control reduces the expenses associated with rework, returns, and product recalls.
Identifying quality issues early in the procurement process saves a significant amount of time and money.
A reduction in material waste also contributes to lower production costs.
Building Strong Supplier Relationships
A purchasing department that actively focuses on quality control can build more substantial relationships with suppliers.
Through constant communication and collaboration on quality improvement, both parties benefit by achieving mutual goals.
Strong supplier relationships often lead to more favorable terms and collaboration on innovative solutions.
Conclusion
With the emergence of new standards in quality control, purchasing departments play an essential role in ensuring that the materials procured meet the highest quality criteria.
By meticulously observing checkpoints such as supplier evaluation, material inspection, and leveraging technology, organizations can ensure that each aspect of procurement upholds quality.
Ultimately, quality control in material procurement is not solely about preventing faulty materials but driving overall business excellence.
Ensuring quality at every point in the supply chain results in better products, cost savings, and a trustworthy brand reputation – all factors that contribute to achieving competitive advantage in the market.
資料ダウンロード
QCD調達購買管理クラウド「newji」は、調達購買部門で必要なQCD管理全てを備えた、現場特化型兼クラウド型の今世紀最高の購買管理システムとなります。
ユーザー登録
調達購買業務の効率化だけでなく、システムを導入することで、コスト削減や製品・資材のステータス可視化のほか、属人化していた購買情報の共有化による内部不正防止や統制にも役立ちます。
NEWJI DX
製造業に特化したデジタルトランスフォーメーション(DX)の実現を目指す請負開発型のコンサルティングサービスです。AI、iPaaS、および先端の技術を駆使して、製造プロセスの効率化、業務効率化、チームワーク強化、コスト削減、品質向上を実現します。このサービスは、製造業の課題を深く理解し、それに対する最適なデジタルソリューションを提供することで、企業が持続的な成長とイノベーションを達成できるようサポートします。
オンライン講座
製造業、主に購買・調達部門にお勤めの方々に向けた情報を配信しております。
新任の方やベテランの方、管理職を対象とした幅広いコンテンツをご用意しております。
お問い合わせ
コストダウンが利益に直結する術だと理解していても、なかなか前に進めることができない状況。そんな時は、newjiのコストダウン自動化機能で大きく利益貢献しよう!
(Β版非公開)