- お役立ち記事
- New standards for the purchasing department! Introduction method for material tracking using RFID tags
月間76,176名の
製造業ご担当者様が閲覧しています*
*2025年3月31日現在のGoogle Analyticsのデータより
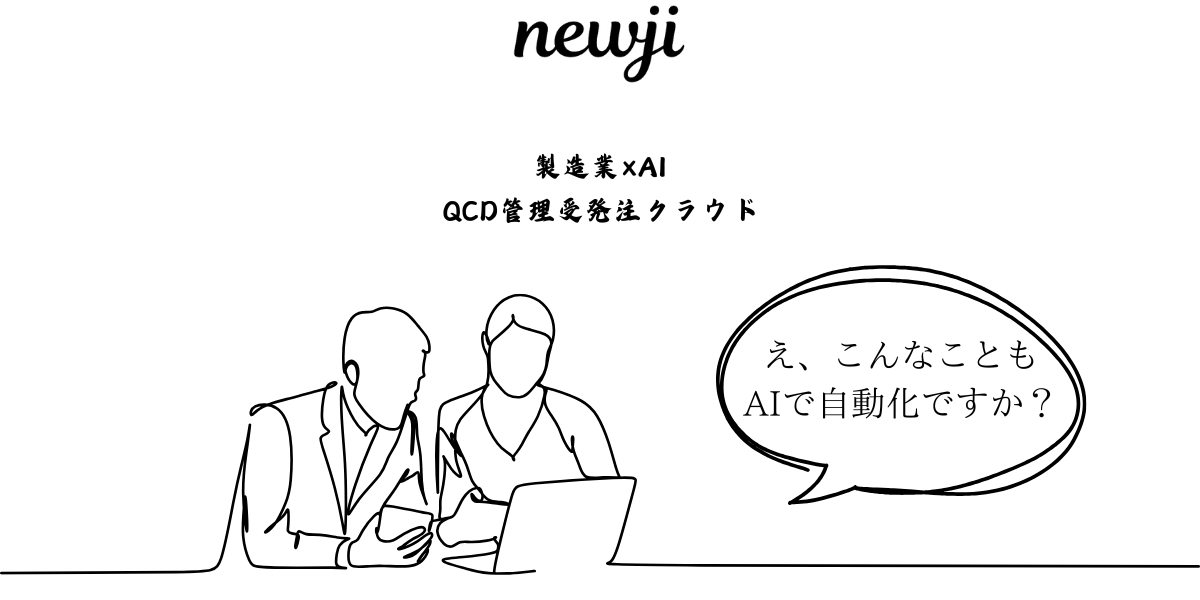
New standards for the purchasing department! Introduction method for material tracking using RFID tags
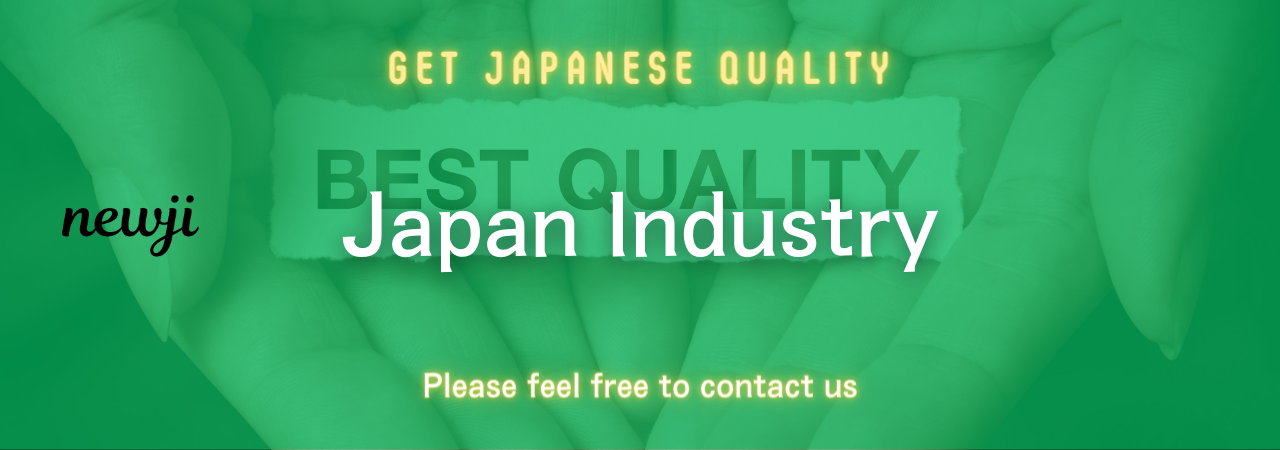
目次
Understanding RFID Technology
Radio Frequency Identification (RFID) technology has been around for several decades but is becoming increasingly popular across various industries, including the purchasing department of companies.
This technology involves using RFID tags, which are small electronic devices that can be attached to objects.
These tags consist of a tiny radio transmitter and a receiver.
The beauty of RFID technology lies in its ability to transmit data about the tagged item wirelessly, without requiring direct contact or even a line of sight, unlike barcodes.
RFID systems typically consist of three main components: the RFID tag, the RFID reader, and a backend database for storing and processing the data.
The RFID reader sends out radio waves, which are picked up by the RFID tag.
The tag then sends back radio waves with its information, such as the item’s location, type, and other attributes, which is captured by the reader and sent to the database for processing.
Advantages of Using RFID Tags in Material Tracking
Implementing RFID technology in the purchasing department offers several benefits.
Firstly, RFID tags enable real-time tracking of materials, which can significantly enhance inventory management.
Knowing the exact location and status of materials at any given time reduces the risk of overstocking or understocking, improving overall supply chain efficiency.
Secondly, RFID tags can hold much more data than traditional barcodes.
They can store information about the item’s origin, destination, expiration date, and its journey through the supply chain.
This detailed data enables better decision-making in the purchasing department and enhances traceability.
Furthermore, RFID tags improve accuracy by eliminating human error associated with manual inventory handling and tracking.
With RFID, scanning can occur automatically as items pass readers at loading bays or along conveyor belts, ensuring data accuracy and saving valuable time.
Lastly, RFID technology can lead to cost savings in the long run.
While the initial investment may be high, the efficiency, accuracy, and low labor costs associated with an RFID system can offset this, providing significant return on investment over time.
Steps to Implementing RFID for Material Tracking
Transitioning to an RFID system may seem daunting, but following a systematic approach can help ensure a smooth implementation.
1. Assess Your Needs
Begin by conducting a thorough assessment of your current material tracking processes.
Identify areas that could benefit most from the added capabilities of RFID technology.
Consider factors such as inventory types, warehouse layout, and specific pain points in your supply chain.
2. Define Your Objectives
Clearly define the goals you aim to achieve with RFID technology.
Whether it’s reducing lost inventory, increasing tracking accuracy, or improving the efficiency of purchase orders, having clear objectives will guide your implementation strategy.
3. Choose the Right RFID System
There are different types of RFID systems, such as passive, active, and semi-passive.
Passive tags are most common due to their low cost but have a shorter read range.
Active tags, while more expensive, have a longer range and can be beneficial for tracking high-value or large-volume items.
Choosing the right system will depend on your specific needs and budget.
4. Pilot the Program
Before a full-scale rollout, launch a pilot program to test the RFID system within a small segment of your operation.
This will help identify any potential issues and fine-tune processes without a significant impact on your overall operation.
5. Train Your Staff
Any new technology requires comprehensive training for your team.
Ensure that all employees involved understand how to use the RFID system effectively.
This includes reading and interpreting data from the RFID readers, as well as troubleshooting basic issues.
6. Roll Out the Full Implementation
Once the pilot program has been assessed and adjustments have been made, proceed with the full implementation of the RFID system throughout the purchasing department.
Ensure continuous monitoring and evaluation to optimize performance.
Overcoming Potential Challenges
While RFID technology offers many benefits, there are challenges to consider.
One major hurdle is the initial cost, as implementing RFID systems involves investing in tags, readers, and necessary software.
However, weighing these costs against potential long-term savings can provide perspective.
Compatibility issues can also arise, particularly in integrating the RFID system with existing enterprise software.
It’s crucial to choose RFID solutions that can interface seamlessly with current systems, ensuring smooth data exchange and process automation.
Additionally, interference from metal objects or liquids can affect RFID performance.
Selecting tags with adequate frequencies and protective measures is essential to minimize such impacts.
Finally, addressing privacy concerns related to data collection is crucial.
It’s important to establish clear guidelines on data use and access to ensure compliance with privacy laws and build trust with stakeholders.
Future Outlook of RFID in Purchasing Departments
As RFID technology continues to evolve, its applications in purchasing departments will likely expand.
The potential for integrating RFID with other technologies, such as IoT and blockchain, could revolutionize material tracking systems.
These innovations may lead to even greater efficiency and transparency in supply chain management.
Moreover, as RFID technology becomes more affordable, even small to medium-sized businesses may adopt it, leveling the playing field and enabling more companies to enjoy its benefits.
In conclusion, implementing RFID technology for material tracking in the purchasing department offers many advantages.
With careful planning and execution, businesses can enhance their inventory management systems, achieve significant cost savings, and stay ahead in the competitive market landscape.
資料ダウンロード
QCD管理受発注クラウド「newji」は、受発注部門で必要なQCD管理全てを備えた、現場特化型兼クラウド型の今世紀最高の受発注管理システムとなります。
ユーザー登録
受発注業務の効率化だけでなく、システムを導入することで、コスト削減や製品・資材のステータス可視化のほか、属人化していた受発注情報の共有化による内部不正防止や統制にも役立ちます。
NEWJI DX
製造業に特化したデジタルトランスフォーメーション(DX)の実現を目指す請負開発型のコンサルティングサービスです。AI、iPaaS、および先端の技術を駆使して、製造プロセスの効率化、業務効率化、チームワーク強化、コスト削減、品質向上を実現します。このサービスは、製造業の課題を深く理解し、それに対する最適なデジタルソリューションを提供することで、企業が持続的な成長とイノベーションを達成できるようサポートします。
製造業ニュース解説
製造業、主に購買・調達部門にお勤めの方々に向けた情報を配信しております。
新任の方やベテランの方、管理職を対象とした幅広いコンテンツをご用意しております。
お問い合わせ
コストダウンが利益に直結する術だと理解していても、なかなか前に進めることができない状況。そんな時は、newjiのコストダウン自動化機能で大きく利益貢献しよう!
(β版非公開)