- お役立ち記事
- Nickel alloy wear resistance improvement technology and usage examples in the heavy equipment market
月間76,176名の
製造業ご担当者様が閲覧しています*
*2025年3月31日現在のGoogle Analyticsのデータより
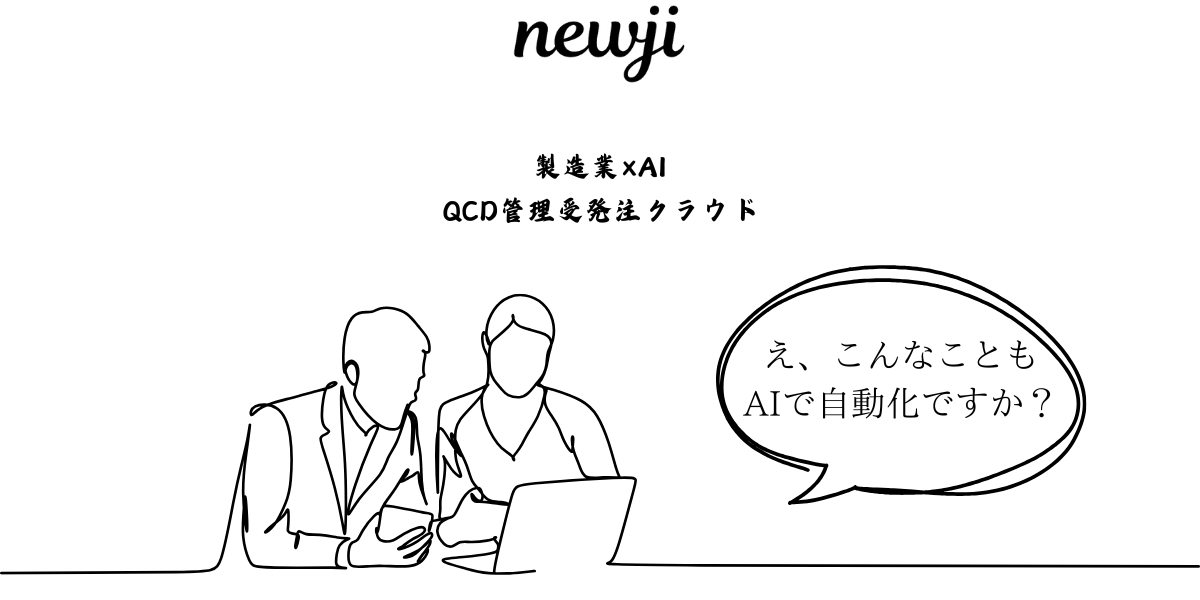
Nickel alloy wear resistance improvement technology and usage examples in the heavy equipment market
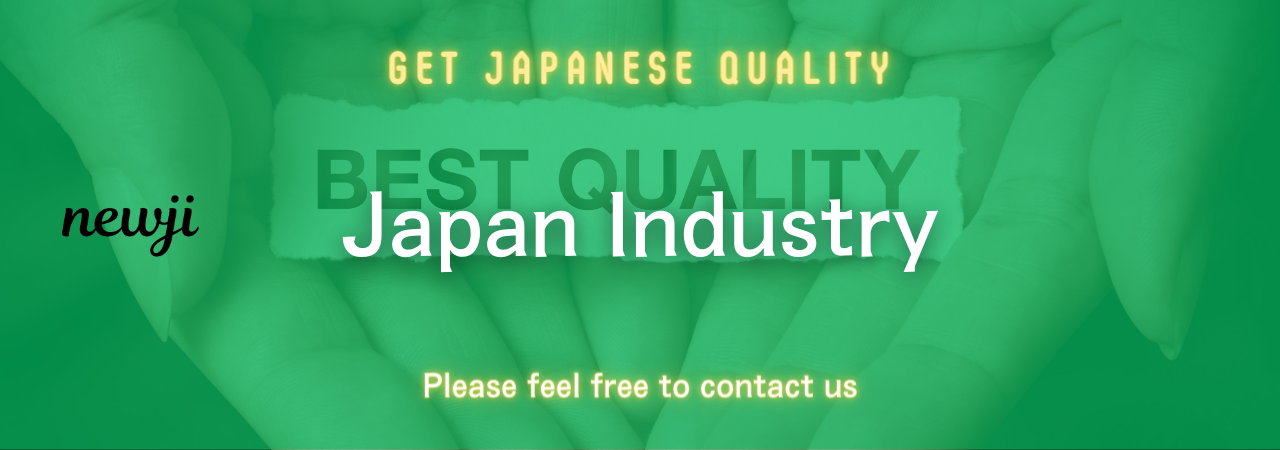
目次
Understanding Nickel Alloy and Its Importance
Nickel alloys are widely regarded for their exceptional wear resistance and durability.
These materials are used extensively in the heavy equipment market because they can withstand harsh environments and extreme conditions.
Nickel alloy offers advantages such as corrosion resistance, thermal stability, and long-lasting performance.
The unique properties of nickel alloy make it an optimal choice for industries where efficiency and longevity are crucial.
Applications in construction, mining, and manufacturing often rely on nickel alloys to ensure operational success and cost-effectiveness.
In this article, we will delve into the technology behind nickel alloy wear resistance improvement and explore practical usage examples in heavy equipment.
How Nickel Alloy Wear Resistance is Improved
Enhancing the wear resistance of nickel alloy involves several techniques that bolster its natural qualities.
These techniques address common wear factors like abrasion, erosion, and corrosion, ensuring that the alloy performs optimally in demanding environments.
Alloy Composition
The choice of alloying elements plays a critical role in improving nickel’s wear resistance.
By carefully selecting elements such as chromium, molybdenum, and tungsten, manufacturers can enhance the hardness and durability of the alloy.
These elements contribute to the formation of stable oxide layers and carbides, which act as protective barriers against wear.
Heat Treatment
Heat treatment processes like annealing, quenching, and tempering are applied to optimize the mechanical properties of nickel alloys.
These processes help refine the microstructure of the alloy, improve its hardness, and enhance its resistance to wear.
By adjusting the temperature and duration of heat treatment, manufacturers can tailor the alloy’s properties to suit specific applications.
Surface Hardening
Surface hardening techniques, such as carburizing and nitriding, enhance the wear resistance of the outer layer of nickel alloys.
Carburizing introduces carbon to the surface, while nitriding involves the diffusion of nitrogen.
Both methods increase the hardness and wear resistance of the alloy’s surface, extending its service life in abrasive environments.
Coatings and Surface Treatments
Employing coatings and surface treatments is another effective way to improve the wear resistance of nickel alloys.
Techniques like thermal spraying, physical vapor deposition (PVD), and chemical vapor deposition (CVD) apply thin, protective layers that shield the underlying metal.
These coatings provide excellent wear resistance and help prevent corrosion, further enhancing the alloy’s operational efficiency.
Real-World Applications in the Heavy Equipment Market
Nickel alloys find numerous applications in the heavy equipment market due to their enhanced wear resistance and durability.
Here are some examples of how nickel alloys are utilized in different sectors:
Construction Equipment
In the construction industry, nickel alloy is commonly used in the production of excavator and bulldozer components.
Parts such as bushings, wear plates, and pins often experience substantial friction and stress.
Utilizing nickel alloys in these components reduces wear and tear, thereby extending their lifespan and minimizing downtime.
Mining Machinery
Mining operations demand equipment that can survive abrasive and corrosive conditions.
Nickel alloys are used in the manufacturing of mining machinery components like pumps, valves, and conveyor chains.
Their exceptional wear resistance reduces the frequency of part replacements and maintenance, contributing to overall operational efficiency.
Manufacturing Systems
In manufacturing, nickel alloys are essential for producing tooling and machine parts exposed to high wear conditions.
Molds, dies, and cutting tools benefit from the alloys’ wear-resistant properties, ensuring precision and longevity in production processes.
This leads to improved product quality and cost savings over time.
Oil and Gas Industry
The oil and gas sector relies heavily on nickel alloys to combat harsh working environments.
Used in drilling equipment and pipelines, nickel alloys withstand high pressures, temperatures, and corrosive elements.
Their wear resistance is crucial for maintaining the integrity and safety of operations, reducing the risk of equipment failure.
Benefits of Using Nickel Alloys in Heavy Equipment
The advantages of using nickel alloys in heavy equipment development are numerous.
Incorporating these materials into machinery and components provides superior performance, reliability, and cost savings.
Let’s explore some of the key benefits:
Enhanced Durability
Nickel alloys provide outstanding durability, ensuring that components can withstand the rigors of heavy use.
This leads to longer equipment life and reduced need for replacements, lowering overall maintenance costs for operators.
Corrosion Resistance
The inherent corrosion resistance of nickel alloys protects machinery from environmental damage.
This is particularly important in industries where equipment is exposed to moisture, chemicals, or other corrosive agents.
Corrosion-resistant properties preserve the integrity of components and prolong their service life.
Operational Efficiency
By improving wear resistance, nickel alloys help maintain optimal functioning of heavy equipment.
Reducing wear-related breakdowns ensures consistent operational performance, minimizing interruptions and boosting productivity.
Cost-Effectiveness
While initial investment in nickel alloy components might be higher, their longevity and reliability contribute to significant cost savings in the long run.
Fewer replacements and repairs translate to reduced operational expenses and a better return on investment for heavy equipment operators.
Conclusion
Nickel alloy wear resistance improvement technology significantly enhances the performance and longevity of heavy equipment.
Through methods such as alloy composition adjustments, heat treatment, surface hardening, and coatings, manufacturers create alloys that withstand challenging conditions.
The adoption of nickel alloys in industries like construction, mining, manufacturing, and oil and gas showcases their indispensable role in advancing technology and reducing costs.
By understanding and leveraging these improvements, the heavy equipment market continues to achieve operational excellence and meet the demand for robust, high-performing machinery.
資料ダウンロード
QCD管理受発注クラウド「newji」は、受発注部門で必要なQCD管理全てを備えた、現場特化型兼クラウド型の今世紀最高の受発注管理システムとなります。
ユーザー登録
受発注業務の効率化だけでなく、システムを導入することで、コスト削減や製品・資材のステータス可視化のほか、属人化していた受発注情報の共有化による内部不正防止や統制にも役立ちます。
NEWJI DX
製造業に特化したデジタルトランスフォーメーション(DX)の実現を目指す請負開発型のコンサルティングサービスです。AI、iPaaS、および先端の技術を駆使して、製造プロセスの効率化、業務効率化、チームワーク強化、コスト削減、品質向上を実現します。このサービスは、製造業の課題を深く理解し、それに対する最適なデジタルソリューションを提供することで、企業が持続的な成長とイノベーションを達成できるようサポートします。
製造業ニュース解説
製造業、主に購買・調達部門にお勤めの方々に向けた情報を配信しております。
新任の方やベテランの方、管理職を対象とした幅広いコンテンツをご用意しております。
お問い合わせ
コストダウンが利益に直結する術だと理解していても、なかなか前に進めることができない状況。そんな時は、newjiのコストダウン自動化機能で大きく利益貢献しよう!
(β版非公開)