- お役立ち記事
- Observation of damage and fracture surfaces of metal materials, elucidation of causes of damage, and how to utilize them for countermeasures
月間77,185名の
製造業ご担当者様が閲覧しています*
*2025年2月28日現在のGoogle Analyticsのデータより
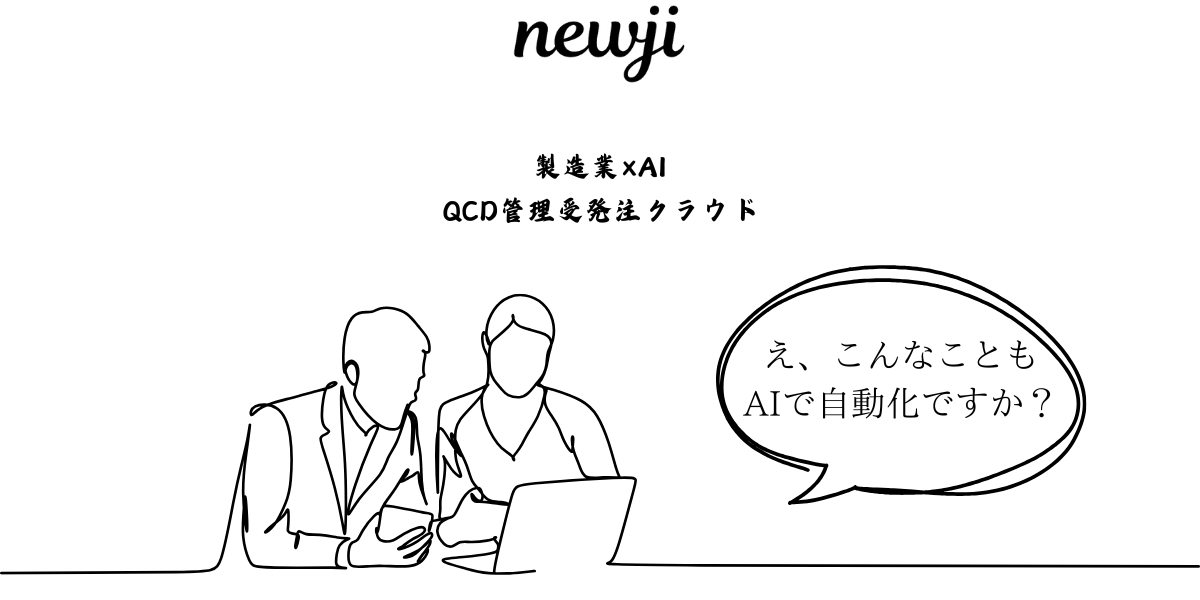
Observation of damage and fracture surfaces of metal materials, elucidation of causes of damage, and how to utilize them for countermeasures
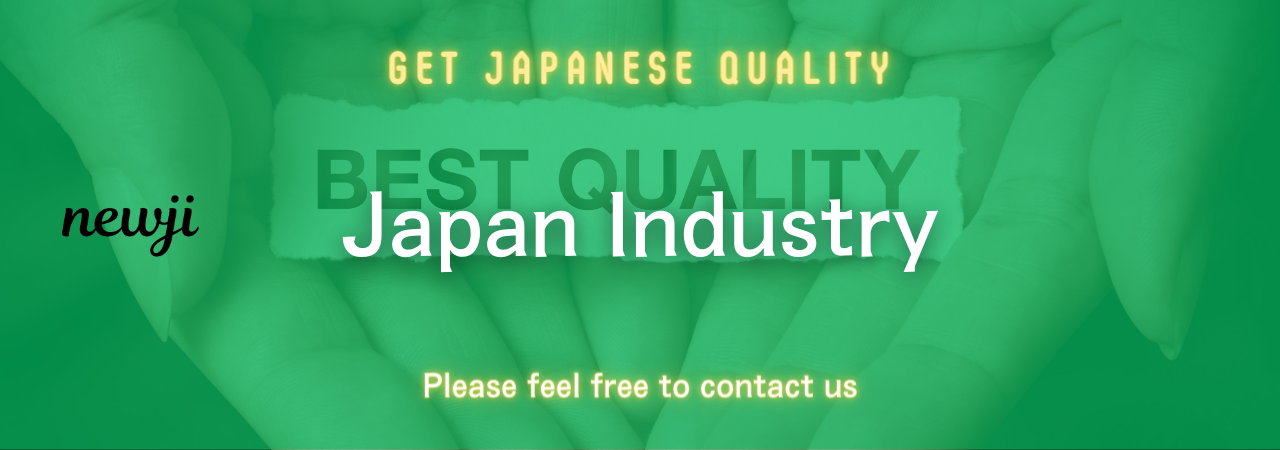
目次
Understanding Damage and Fracture in Metal Materials
The study of metal materials and their potential for damage and fracture is an essential aspect of material science and engineering.
Understanding how and why metals fail is crucial for advancing industrial designs, improving manufacturing processes, and ensuring the safety and longevity of metal structures.
This exploration includes examining damaged surfaces, determining the causes of failure, and devising strategies to prevent future mishaps.
Observation of Damage and Fracture Surfaces
Observing the surfaces of damaged or fractured metal samples provides valuable insights into the failure mechanisms at play.
Different metals show varying surface characteristics when they fail, depending on their composition, processing history, and the conditions under which they were used.
For example, a brittle fracture often presents a flat and shiny surface, indicative of a sudden break with little plastic deformation.
In contrast, ductile fractures typically exhibit dimpled surfaces, where the material has undergone noticeable deformation before failure.
These dimples are usually the result of void coalescence due to microstructural defects.
Detailed microscopic examinations, such as scanning electron microscopy (SEM), are employed to analyze these surfaces.
Such studies can reveal microstructural elements like grain boundaries, inclusions, and voids that contribute to the material’s performance and failure.
The ability to relate these microscopic features to the macroscopic failure of a component is a significant aspect of damage analysis.
Causes of Metal Damage
Several factors lead to metal damage and fracture.
These include mechanical stresses beyond the material’s strength, corrosion, fatigue, and adverse environmental conditions.
Understanding these causes is key to preventing future failures.
Mechanical overloading occurs when a material is subjected to forces exceeding its yield strength.
This can cause permanent deformation or even fracture.
In other cases, cyclic loading, or fatigue, can lead to failure after repeated applications of stress, even if the stress levels are below the tensile strength of the material.
Corrosion is another significant factor, particularly in environments where metals are exposed to moisture, chemicals, or harsh weather conditions.
Corrosion can weaken a metal’s structure by creating pits and cracks that serve as initiation sites for fracture.
Lastly, environmental conditions like extreme temperatures can alter a material’s properties, making it more susceptible to cracking or sudden failure.
For instance, high temperatures can lead to a phenomenon known as thermal fatigue, while low temperatures can cause some metals to become brittle.
Elucidating the Causes of Damage
Identifying the root causes of metal damage involves a combination of visual inspection, experimental data, and analytical models.
One common method is to perform a fracture analysis, where engineers analyze the fracture surface and the surrounding area to determine the type of failure.
They also take samples from undamaged parts of the material for chemical analysis to check for impurities or composition flaws.
Additionally, simulating the conditions leading to the failure helps in confirming the suspected causes.
For mechanical failures, engineers may recreate stress conditions in controlled environments to see how the material behaves.
By coupling these experimental observations with statistical data and computational models, professionals can accurately pinpoint why a failure occurred.
Such thorough analyses not only help in understanding past failures but also provide data critical for designing more resilient materials.
Utilizing Observations for Countermeasures
The information gathered from studying fracture surfaces and elucidating damage causes is invaluable for developing preventive strategies.
For instance, if a particular alloy is found to be susceptible to fatigue, engineers can alter its chemical composition or adjust the processing techniques to enhance its fatigue resistance.
Alternatively, surface treatments such as coatings can be applied to protect metals from corrosive environments.
Design improvements can also stem from damage observations.
If a structural component has failed due to an unexpected stress concentration, redesigning it with smoother transitions and eliminating sharp corners can mitigate future failures.
On a broader scale, these insights inform industry standards and guidelines.
Regulations can require certain testing methods or material specifications to ensure components meet specific safety thresholds.
Future Directions in Damage Prevention
As technology progresses, there are increasing opportunities to enhance the study and prevention of metal damage.
Advanced simulation tools, incorporating artificial intelligence and machine learning, offer capabilities for predicting material performance under different conditions.
These tools can process complex data sets and recognize patterns indicative of potential failures before they occur in real-world applications.
Furthermore, innovations in material science, like the development of new alloys or composites, provide pathways to circumvent traditional limitations of metals.
These materials can offer superior properties tailored for specific applications, such as higher strength or resistance to specific environmental factors.
By fostering collaboration between academia, industry, and regulatory bodies, new strategies can be created to tackle the complex challenges of metal damage.
In conclusion, the observation of damage and fracture surfaces in metals, combined with a thorough understanding of failure causes, plays a vital role in enhancing material performance and safety.
The insights gained from these studies lead to better engineering practices, improved safety standards, and innovations in material design and processing.
Keeping abreast of new developments in this field will be crucial for industries that rely on the durability and integrity of metal structures.
資料ダウンロード
QCD管理受発注クラウド「newji」は、受発注部門で必要なQCD管理全てを備えた、現場特化型兼クラウド型の今世紀最高の受発注管理システムとなります。
ユーザー登録
受発注業務の効率化だけでなく、システムを導入することで、コスト削減や製品・資材のステータス可視化のほか、属人化していた受発注情報の共有化による内部不正防止や統制にも役立ちます。
NEWJI DX
製造業に特化したデジタルトランスフォーメーション(DX)の実現を目指す請負開発型のコンサルティングサービスです。AI、iPaaS、および先端の技術を駆使して、製造プロセスの効率化、業務効率化、チームワーク強化、コスト削減、品質向上を実現します。このサービスは、製造業の課題を深く理解し、それに対する最適なデジタルソリューションを提供することで、企業が持続的な成長とイノベーションを達成できるようサポートします。
製造業ニュース解説
製造業、主に購買・調達部門にお勤めの方々に向けた情報を配信しております。
新任の方やベテランの方、管理職を対象とした幅広いコンテンツをご用意しております。
お問い合わせ
コストダウンが利益に直結する術だと理解していても、なかなか前に進めることができない状況。そんな時は、newjiのコストダウン自動化機能で大きく利益貢献しよう!
(β版非公開)