- お役立ち記事
- Occurrence and prevention of defects
Occurrence and prevention of defects
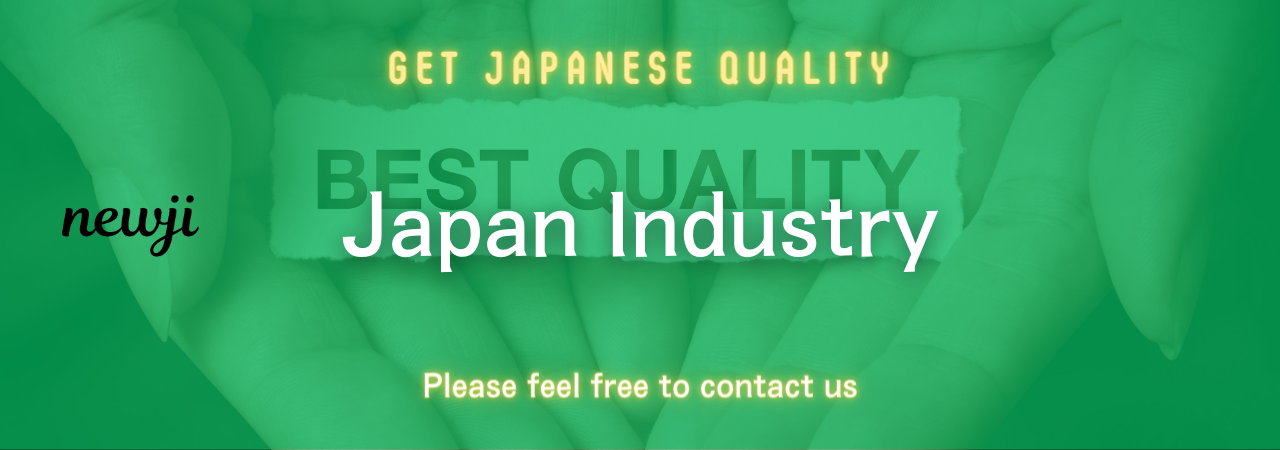
目次
Understanding Defects: What Are They?
In any manufacturing or production process, defects are inevitable.
A defect is any anomaly or imperfection that prevents a product from meeting its intended quality standards.
These imperfections can arise from various factors, including errors in design, material, or workmanship.
Understanding the nature of defects is essential to identifying and implementing effective preventive measures.
Defects not only affect the overall quality of the product but can also lead to increased costs, customer dissatisfaction, and even safety concerns.
Hence, recognizing their occurrence and understanding how to prevent them is crucial for maintaining high standards in any production environment.
Types of Defects
The first step in addressing defects is to categorize them.
Generally, defects fall into three main categories:
1. **Design Defects**: These occur when the design specifications themselves are flawed.
If a product is designed in such a way that it is inherently unsafe or unable to achieve its intended purpose, it is considered a design defect.
2. **Manufacturing Defects**: These defects arise during the production process.
Even if a product is designed correctly, mistakes in manufacturing, such as incorrect assembly or the use of substandard materials, can lead to defects.
3. **Material Defects**: Sometimes, defects can be traced back to the materials used in production.
If the raw materials are of poor quality or inappropriate for the product, they can compromise the entire manufacturing process, leading to defective products.
Each type of defect requires specific attention and strategies for prevention.
Why Defects Occur
Understanding the causes of defects is essential for developing effective prevention strategies.
Several factors contribute to the occurrence of defects in a manufacturing process.
Human Errors
Human errors are a major contributing factor to defects.
These errors can occur at any stage of the production process, from design to assembly.
Mistakes in calculations, oversight in quality checks, or lack of proper training are common examples.
Ensuring that the workforce is well-trained and vigilant can help in minimizing human errors.
Process Variability
Variability in the production process can lead to defects.
Inconsistencies in machine operation, variations in environmental conditions, or deviations from set procedures can alter the quality of the final product.
Standardizing processes and maintaining strict control measures can help in reducing variability.
Poor Quality Materials
The quality of materials used in production directly affects the quality of the final product.
Using inferior materials or sourcing from unreliable suppliers increases the likelihood of defects.
Maintaining strong relationships with reputable suppliers and implementing stringent quality checks on incoming materials can mitigate this risk.
Lack of Quality Control
Without proper quality control measures, defects are more likely to go undetected until it is too late.
An absence of regular inspections, audits, and testing means that defects may not be identified until the products are in the hands of consumers.
A robust quality control system is essential to detect and address defects promptly.
Preventing Defects
Preventing defects is far more beneficial than dealing with them after they occur.
Here are some effective strategies to reduce the occurrence of defects:
Invest in Training and Education
Training employees thoroughly and continuously is crucial for minimizing human errors.
Educated workers are more aware of potential pitfalls and better equipped to handle unexpected issues.
Regular training sessions and up-to-date educational programs ensure that the workforce remains knowledgeable and skilled.
Implement Standard Operating Procedures (SOPs)
Written SOPs provide clear guidelines for each step of the production process.
They minimize process variability by ensuring everyone performs tasks in a consistent manner.
Regularly reviewing and updating these procedures ensures they remain relevant and effective.
Use Quality Raw Materials
Always source materials from reliable and reputable suppliers.
Implement rigorous quality checks on all incoming materials to confirm they meet the required standards before use.
Investing in quality materials from the start is vital for producing defect-free products.
Enhance Quality Control Measures
A strong quality control system involves regular inspections, audits, and testing throughout the production process.
This system should be equipped to detect defects early, allowing for prompt corrective action.
Modern technologies such as automation and digital monitoring can enhance quality control efficiency.
Encourage a Culture of Continuous Improvement
Fostering a culture of continuous improvement is essential for long-term defect prevention.
Encourage employees at all levels to contribute ideas and solutions.
Regularly analyze past mistakes and successes, and apply the lessons learned to future projects.
The Benefits of Preventing Defects
The advantages of proactively preventing defects in production are substantial.
Businesses benefit from lower costs, as defect prevention can reduce waste and minimize labor and material expenses.
Customer satisfaction improves when consumers receive products that meet or exceed their expectations, fostering brand loyalty and repeat business.
Moreover, defect prevention contributes to safer products, reducing the risk of recalls and potential legal issues.
In conclusion, understanding and preventing defects is a dynamic process that requires constant vigilance and adaptation.
By recognizing the various types of defects, identifying their causes, and implementing effective prevention strategies, businesses can maintain high standards of quality, ensuring their success in the competitive market.
資料ダウンロード
QCD調達購買管理クラウド「newji」は、調達購買部門で必要なQCD管理全てを備えた、現場特化型兼クラウド型の今世紀最高の購買管理システムとなります。
ユーザー登録
調達購買業務の効率化だけでなく、システムを導入することで、コスト削減や製品・資材のステータス可視化のほか、属人化していた購買情報の共有化による内部不正防止や統制にも役立ちます。
NEWJI DX
製造業に特化したデジタルトランスフォーメーション(DX)の実現を目指す請負開発型のコンサルティングサービスです。AI、iPaaS、および先端の技術を駆使して、製造プロセスの効率化、業務効率化、チームワーク強化、コスト削減、品質向上を実現します。このサービスは、製造業の課題を深く理解し、それに対する最適なデジタルソリューションを提供することで、企業が持続的な成長とイノベーションを達成できるようサポートします。
オンライン講座
製造業、主に購買・調達部門にお勤めの方々に向けた情報を配信しております。
新任の方やベテランの方、管理職を対象とした幅広いコンテンツをご用意しております。
お問い合わせ
コストダウンが利益に直結する術だと理解していても、なかなか前に進めることができない状況。そんな時は、newjiのコストダウン自動化機能で大きく利益貢献しよう!
(Β版非公開)