- お役立ち記事
- OEM Manufacturing Cooler Boxes: Ensuring High-Performance Cooling
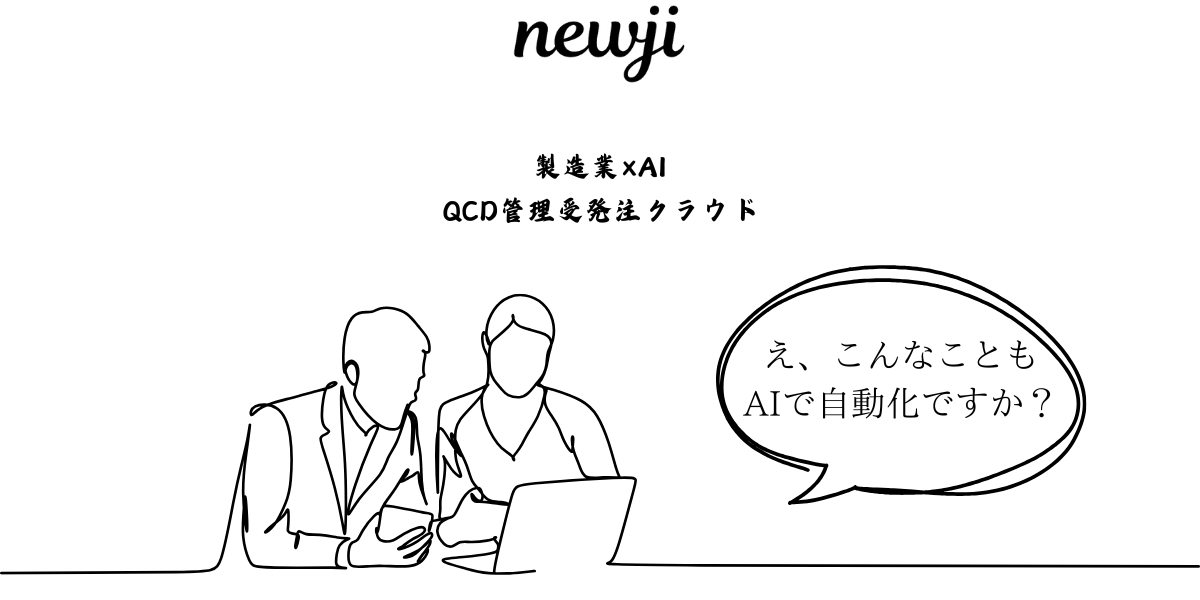
OEM Manufacturing Cooler Boxes: Ensuring High-Performance Cooling
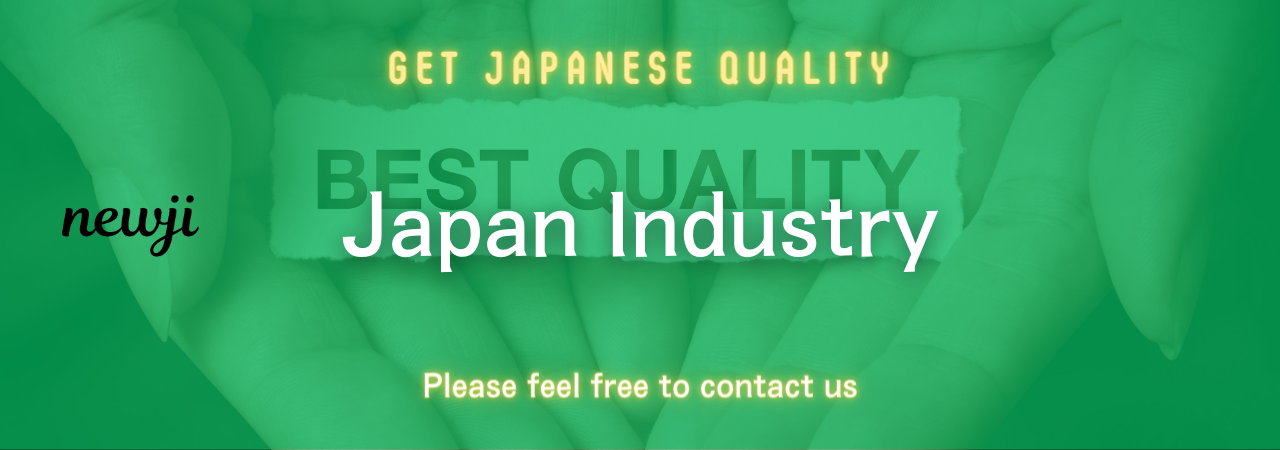
OEM manufacturing of cooler boxes plays a critical role in ensuring high-performance cooling solutions for a variety of applications.
Whether these cooler boxes are used for camping trips, transporting perishable goods, or storing medical supplies, the efficiency and reliability of the cooling system are paramount.
In this article, we will delve into the intricacies of OEM manufacturing in the context of cooler boxes, highlighting the importance of high-quality materials, advanced insulation technologies, and the benefits of customization.
目次
The Basics of OEM Manufacturing
OEM stands for Original Equipment Manufacturer.
This term refers to companies that produce parts and equipment that may be marketed by another manufacturer.
In the case of cooler boxes, OEM manufacturers design and create these products, which are then branded and sold by other companies.
This process allows the developing company to focus on their strengths while leveraging the manufacturing expertise of the OEM partner.
Why Choose OEM Manufacturing for Cooler Boxes?
Several reasons make OEM manufacturing a preferred choice for cooler boxes:
Firstly, it provides access to specialized manufacturing capabilities and technologies.
This ensures the production of high-quality, durable cooler boxes that perform well even under challenging conditions.
Secondly, it allows companies to save time and resources, as they do not need to invest in setting up their own manufacturing facilities.
Lastly, OEM partners often have extensive experience and knowledge in their niche markets, leading to innovative and efficient product designs.
Key Components of High-Performance Cooler Boxes
To ensure high-performance cooling, several critical components must be considered in the design and manufacturing of cooler boxes.
Advanced Insulation Materials
The efficiency of a cooler box largely depends on its insulation.
High-performance cooler boxes typically use advanced insulation materials such as polyurethane foam or vacuum-sealed panels.
These materials provide superior thermal resistance, keeping the contents cooler for longer periods.
Durable Construction
Cooler boxes must be built to withstand rough handling and various environmental conditions.
OEM manufacturers use high-quality plastics, such as polyethylene or polypropylene, for the outer shell.
These materials offer excellent durability, UV resistance, and impact strength.
Sealing Mechanisms
A critical aspect of cooler box design is ensuring an airtight seal.
High-performance cooler boxes incorporate robust sealing mechanisms, such as rubber gaskets, to minimize air exchange.
This feature helps maintain the internal temperature and extends the cooling duration.
User-Friendly Features
To enhance the user experience, cooler boxes come with a range of convenient features.
These may include ergonomic handles, easy-to-use latches, and integrated cup holders.
Some advanced models also feature built-in thermometers, wheels for easy transport, and even solar-powered charging capabilities.
The Benefits of Customization
One of the significant advantages of OEM manufacturing is the ability to customize cooler boxes according to specific requirements.
Customization allows brands to differentiate their products in the market and cater to niche customer needs.
Branding Opportunities
OEM manufacturing gives companies the flexibility to incorporate their branding elements into the cooler box design.
This includes adding logos, color schemes, and custom graphics.
Strong branding helps build a recognizable and trusted brand image in the market.
Design Flexibility
OEM manufacturers offer various design options, enabling brands to tailor the sizes, shapes, and features of their cooler boxes.
This ensures the final product meets the specific needs and preferences of their target audience.
Technological Integration
With continuous advancements in technology, cooler boxes can be equipped with smart features.
OEM manufacturers can integrate sensors, GPS tracking, and Bluetooth connectivity to provide real-time updates on the cooler’s condition.
These technological enhancements greatly benefit industries such as medical transport and perishable goods logistics.
Quality Control and Testing
To ensure the reliability and performance of cooler boxes, stringent quality control and testing are essential steps in the OEM manufacturing process.
These practices help identify potential issues and guarantee that the cooler boxes meet the highest standards.
Material Testing
Quality control begins with rigorous testing of raw materials.
This ensures that only high-grade materials are used in the production process.
Tests for impact resistance, thermal conductivity, and UV resistance are commonly conducted.
Performance Testing
OEM manufacturers subject the cooler boxes to various performance tests to evaluate their cooling efficiency, durability, and overall functionality.
These tests may include thermal retention trials, drop tests, and environmental simulations.
Compliance with Standards
To meet industry regulations and standards, cooler boxes undergo thorough inspections and certifications.
Compliance with standards such as FDA, NSF, and ISO ensures that the cooler boxes are safe for use, especially in sensitive applications like food storage and medical transport.
Sustainability in OEM Manufacturing
With growing environmental concerns, sustainability has become a key consideration in OEM manufacturing.
Cooler box manufacturers are increasingly adopting eco-friendly practices to minimize their environmental footprint.
Use of Recycled Materials
Many OEM manufacturers are incorporating recycled materials into their cooler box production.
This reduces reliance on virgin resources and lowers the overall environmental impact.
Energy-Efficient Manufacturing Processes
Adopting energy-efficient manufacturing processes is another important step towards sustainability.
OEM manufacturers implement measures such as using renewable energy sources, optimizing production lines, and reducing waste.
End-of-Life Management
To promote a circular economy, manufacturers are exploring end-of-life management solutions for cooler boxes.
This includes designing products that are easy to disassemble and recycle, and offering take-back programs to ensure proper disposal.
OEM manufacturing of cooler boxes is a versatile and efficient way to produce high-performance cooling solutions.
By leveraging advanced materials, robust designs, and customization options, OEM partners help companies deliver top-quality cooler boxes to their customers.
With a focus on quality control, sustainability, and technological innovation, the future of OEM-manufactured cooler boxes looks bright.
資料ダウンロード
QCD調達購買管理クラウド「newji」は、調達購買部門で必要なQCD管理全てを備えた、現場特化型兼クラウド型の今世紀最高の購買管理システムとなります。
ユーザー登録
調達購買業務の効率化だけでなく、システムを導入することで、コスト削減や製品・資材のステータス可視化のほか、属人化していた購買情報の共有化による内部不正防止や統制にも役立ちます。
NEWJI DX
製造業に特化したデジタルトランスフォーメーション(DX)の実現を目指す請負開発型のコンサルティングサービスです。AI、iPaaS、および先端の技術を駆使して、製造プロセスの効率化、業務効率化、チームワーク強化、コスト削減、品質向上を実現します。このサービスは、製造業の課題を深く理解し、それに対する最適なデジタルソリューションを提供することで、企業が持続的な成長とイノベーションを達成できるようサポートします。
オンライン講座
製造業、主に購買・調達部門にお勤めの方々に向けた情報を配信しております。
新任の方やベテランの方、管理職を対象とした幅広いコンテンツをご用意しております。
お問い合わせ
コストダウンが利益に直結する術だと理解していても、なかなか前に進めることができない状況。そんな時は、newjiのコストダウン自動化機能で大きく利益貢献しよう!
(Β版非公開)