- お役立ち記事
- OEM Manufacturing of Aluminum Products to Meet Diverse Needs
OEM Manufacturing of Aluminum Products to Meet Diverse Needs
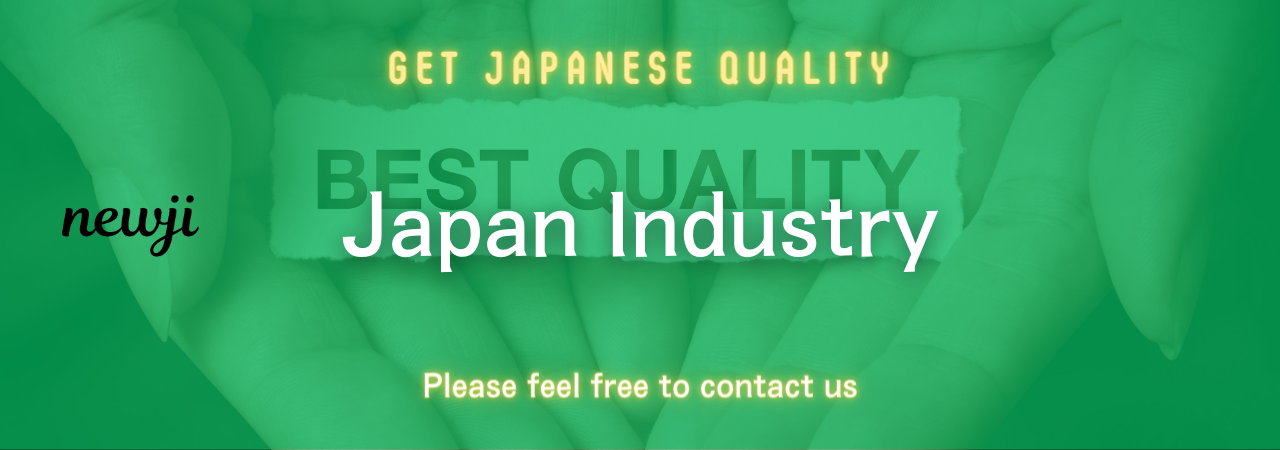
When it comes to creating high-quality aluminum products to meet the diverse needs of various industries, OEM manufacturing stands out as a valuable solution.
Original Equipment Manufacturers (OEM) possess the expertise, technology, and flexibility to produce aluminum components and products that align with specific requirements, ensuring high performance, durability, and cost-efficiency.
目次
What is OEM Manufacturing?
OEM manufacturing involves producing parts or products that are then sold under another company’s brand name.
In the case of aluminum products, OEM manufacturers take on the responsibility of designing, manufacturing, and often even optimizing the production process, to create components that perfectly fit the end user’s needs.
This approach allows companies to focus on their core business while leveraging the specialized skills and capabilities of OEM manufacturers.
The Benefits of Aluminum in Manufacturing
Aluminum is renowned for its versatility and myriad of beneficial properties.
Lightweight and Strong
One of the primary reasons aluminum is favored in manufacturing is its exceptional strength-to-weight ratio.
It is significantly lighter than steel but still provides strength and durability.
This makes it ideal for applications that require robust yet lightweight materials, such as automotive parts, aerospace components, and consumer electronics.
Corrosion Resistance
Aluminum naturally forms a protective oxide layer when exposed to air.
This makes it highly resistant to corrosion, ensuring long-lasting performance even in harsh environments.
As a result, aluminum is frequently used in outdoor and marine applications where resistance to weather conditions is critical.
Thermal and Electrical Conductivity
Aluminum boasts excellent thermal and electrical conductivity.
It is often used in heat exchangers, electrical transmission lines, and electronic devices.
This enhances its functionality across various industries, contributing to its widespread adoption.
Recyclability
Aluminum is 100% recyclable without losing its inherent properties.
Recycling aluminum saves a significant amount of energy compared to producing new metal, making it an eco-friendly option.
This aligns with growing environmental consciousness and sustainability goals.
Industries That Benefit From OEM Aluminum Manufacturing
Automotive Industry
The automotive industry extensively uses aluminum in the production of various components such as engine blocks, transmission cases, and body panels.
OEM manufacturers provide tailored solutions that help automotive companies reduce vehicle weight, improve fuel efficiency, and enhance overall performance.
Aerospace Industry
In aerospace, the need for lightweight yet strong materials is paramount.
Aluminum’s properties make it a go-to material for aircraft structures, including wing panels, fuselage parts, and landing gear components.
OEM manufacturers ensure precision and reliability in producing aerospace-grade aluminum parts.
Construction Industry
From window frames to roofing materials, aluminum plays a significant role in modern construction.
Its durability, aesthetic appeal, and resistance to corrosion make it an ideal choice for building facades and structural elements.
OEM manufacturers deliver customized aluminum solutions that meet stringent building codes and architectural requirements.
Consumer Electronics
Aluminum is prevalent in the consumer electronics sector, used in the manufacturing of smartphone housings, laptop bodies, and other gadgets.
OEM manufacturers provide sleek, durable, and lightweight aluminum components that enhance the user experience and device longevity.
The OEM Manufacturing Process for Aluminum Products
Design and Engineering
OEM manufacturing starts with a comprehensive design and engineering phase.
Engineers and designers work closely with clients to understand their specific requirements and objectives.
Advanced software is used to create detailed models and simulations, ensuring the final product meets all specifications.
Prototyping
Before full-scale production, prototypes are developed to validate the design.
These prototypes undergo rigorous testing to assess their performance, durability, and functionality.
Feedback from this phase is used to refine the design, ensuring optimal results in the final product.
Materials Selection
Choosing the right aluminum alloy is crucial to achieving desired properties.
OEM manufacturers have extensive knowledge about different alloys and their applications.
They select the most suitable material based on factors like strength, weight, corrosion resistance, and formability.
Production
With the design finalized and materials selected, the production phase begins.
Modern OEM manufacturing facilities are equipped with advanced machinery and technology to ensure precision and efficiency.
Processes such as extrusion, casting, or machining are employed to shape the aluminum into the desired components.
Quality Control
Quality control is an integral part of OEM manufacturing.
Throughout the production process, stringent quality checks are conducted to ensure every component meets the highest standards.
This includes dimensional inspections, material tests, and performance evaluations.
Choosing the Right OEM Manufacturer
Experience and Expertise
When selecting an OEM manufacturer for aluminum products, consider their experience and expertise in the field.
Look for a company with a proven track record of delivering high-quality aluminum components to various industries.
Technical Capabilities
Assess the manufacturer’s technical capabilities, including their machinery, technology, and production processes.
A manufacturer with state-of-the-art equipment and a commitment to innovation will likely deliver superior results.
Customization and Flexibility
Choose an OEM manufacturer that offers customization and flexibility to meet your specific requirements.
The ability to adapt to unique needs and provide tailored solutions is a hallmark of a reliable OEM partner.
Environmental Responsibility
Consider the manufacturer’s commitment to environmental sustainability.
Opt for a company that prioritizes eco-friendly practices, such as recycling and energy-efficient production methods.
Conclusion
OEM manufacturing of aluminum products is a strategic approach that caters to the diverse needs of various industries.
With its numerous benefits, including lightweight strength, corrosion resistance, and recyclability, aluminum is an excellent choice for a wide range of applications.
By partnering with experienced and capable OEM manufacturers, companies can achieve high-performance, cost-efficient, and sustainable solutions for their aluminum product requirements.
資料ダウンロード
QCD調達購買管理クラウド「newji」は、調達購買部門で必要なQCD管理全てを備えた、現場特化型兼クラウド型の今世紀最高の購買管理システムとなります。
ユーザー登録
調達購買業務の効率化だけでなく、システムを導入することで、コスト削減や製品・資材のステータス可視化のほか、属人化していた購買情報の共有化による内部不正防止や統制にも役立ちます。
NEWJI DX
製造業に特化したデジタルトランスフォーメーション(DX)の実現を目指す請負開発型のコンサルティングサービスです。AI、iPaaS、および先端の技術を駆使して、製造プロセスの効率化、業務効率化、チームワーク強化、コスト削減、品質向上を実現します。このサービスは、製造業の課題を深く理解し、それに対する最適なデジタルソリューションを提供することで、企業が持続的な成長とイノベーションを達成できるようサポートします。
オンライン講座
製造業、主に購買・調達部門にお勤めの方々に向けた情報を配信しております。
新任の方やベテランの方、管理職を対象とした幅広いコンテンツをご用意しております。
お問い合わせ
コストダウンが利益に直結する術だと理解していても、なかなか前に進めることができない状況。そんな時は、newjiのコストダウン自動化機能で大きく利益貢献しよう!
(Β版非公開)