- お役立ち記事
- OEM Manufacturing of Cocktail Shakers for High-Quality Barware
月間76,176名の
製造業ご担当者様が閲覧しています*
*2025年3月31日現在のGoogle Analyticsのデータより
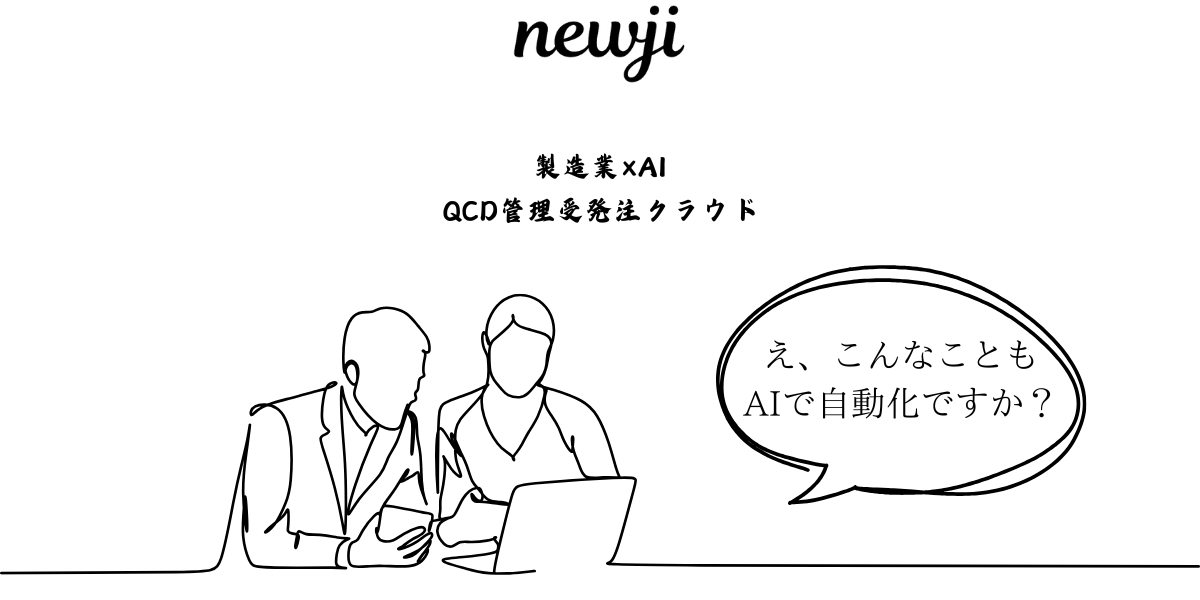
OEM Manufacturing of Cocktail Shakers for High-Quality Barware
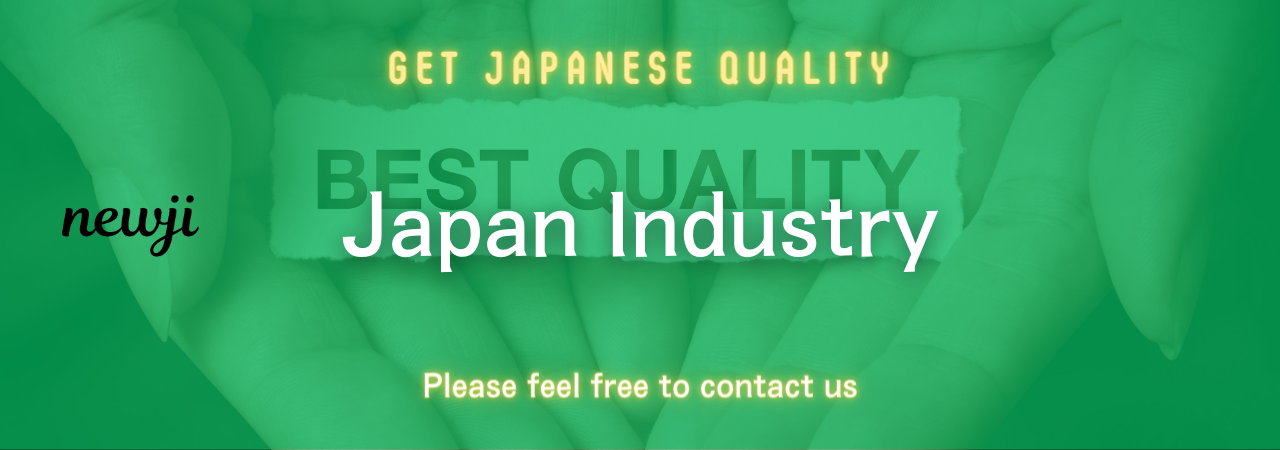
目次
What is OEM Manufacturing?
OEM stands for Original Equipment Manufacturer.
In simple terms, OEM manufacturing occurs when a company produces goods or components that are purchased by another company and retailed under its brand name.
This process allows the buying company to offer a product without having to handle the manufacturing itself.
OEM manufacturing is widespread in various industries, including electronics, automotive, and even kitchenware.
OEM Manufacturing in Barware Industry
In the barware industry, OEM manufacturing plays a crucial role.
Items like cocktail shakers are often produced by specialized manufacturers who have the expertise and equipment to create high-quality products.
These cocktail shakers are then branded and sold by well-known retailers and brands we trust.
By choosing OEM manufacturing, these brands can focus on design, marketing, and customer service without worrying about the complexities of production.
Why OEM Manufacturing for Cocktail Shakers?
OEM manufacturing is particularly advantageous for cocktail shakers for several reasons.
Expertise and Technology
Manufacturers who specialize in barware have the skills and technology needed to produce superior cocktail shakers.
They are updated with the latest trends and materials, ensuring that the final product is not only functional but also stylish.
With advanced machinery and skilled labor, OEM manufacturers can maintain high standards that align with a brand’s reputation for quality.
Cost-Effectiveness
Producing cocktail shakers in-house can be costly and time-consuming, especially for companies that do not have the necessary manufacturing capabilities.
OEM manufacturers can produce these items at a lower cost due to economies of scale.
They buy materials in bulk and have streamlined production processes that reduce waste and labor costs.
This allows retail brands to offer high-quality cocktail shakers at competitive prices while maintaining healthy profit margins.
Customization
One of the significant advantages of OEM manufacturing is the ability to customize products to meet specific brand needs.
Whether it’s adding a unique design, logo, or using a particular type of material, OEM manufacturers can create cocktail shakers that align perfectly with a brand’s identity.
This flexibility helps brands stand out in a crowded market and give consumers something unique.
Choosing the Right OEM Manufacturer
Selecting an OEM manufacturer for cocktail shakers involves careful consideration to ensure you get the best quality and service.
Here are some key factors to keep in mind:
Reputation
Research the manufacturer’s background and reputation.
Look for reviews from other clients and check if they have experience in producing barware.
A company with a good track record is more likely to deliver quality products and reliable service.
Quality Assurance
Ensure that the manufacturer follows strict quality control processes.
Ask about their quality standards and how they ensure each product meets these standards.
High-quality cocktail shakers are essential for customer satisfaction and brand reputation.
Communication and Flexibility
Effective communication is crucial when working with an OEM manufacturer.
Choose a manufacturer who is responsive and willing to accommodate your specific needs and requests.
Flexibility in production runs, customization options, and delivery schedules can make the manufacturing process smoother and more efficient.
Lead Time and Cost
Consider the lead time the manufacturer requires to produce and deliver the cocktail shakers.
Timely delivery is crucial, especially if you operate based on seasonal sales or special promotions.
Also, compare costs but don’t compromise on quality for a lower price.
A balance between cost and quality should be your goal.
The Production Process of OEM Cocktail Shakers
Understanding the production process can help you make informed decisions and have realistic expectations.
Design and Prototyping
The process usually starts with a design phase where your specifications are transformed into a digital model.
Prototyping follows, allowing you to see a sample of the product.
This step is crucial for making adjustments before mass production.
Material Selection
OEM manufacturers will work with you to select the best materials for your cocktail shakers.
This could include stainless steel, glass, or other types of metals and plastics, depending on your brand’s niche.
Production and Assembly
Once the design and materials are finalized, the production phase begins.
This involves cutting, shaping, and assembling different components of the cocktail shakers.
Highly specialized machinery and skilled labor ensure that each piece is crafted to perfection.
Quality Control
After production, each unit undergoes rigorous quality checks.
This ensures that the cocktail shakers meet all the specifications and standards agreed upon.
Only after passing these checks are the products packed and prepared for shipping.
Environmental Considerations
In today’s world, sustainability is a significant concern for both manufacturers and consumers.
When choosing an OEM manufacturer, consider their environmental policies.
Sustainable Materials
Opt for manufacturers who use sustainable materials.
For instance, stainless steel is not only durable but also recyclable, making it an excellent choice for eco-friendly cocktail shakers.
Energy-Efficient Production
Energy-efficient production methods can also make a significant difference.
Ask potential manufacturers about their energy usage and if they employ eco-friendly practices in their operations.
Conclusion
OEM manufacturing offers a plethora of benefits when it comes to producing high-quality cocktail shakers.
With expertise, advanced technology, and cost-effective production methods, OEM manufacturers enable brands to offer premium barware without the hassles of in-house production.
By carefully selecting the right OEM partner and focusing on quality and sustainability, brands can ensure they meet consumer demands and maintain a competitive edge in the market.
資料ダウンロード
QCD管理受発注クラウド「newji」は、受発注部門で必要なQCD管理全てを備えた、現場特化型兼クラウド型の今世紀最高の受発注管理システムとなります。
ユーザー登録
受発注業務の効率化だけでなく、システムを導入することで、コスト削減や製品・資材のステータス可視化のほか、属人化していた受発注情報の共有化による内部不正防止や統制にも役立ちます。
NEWJI DX
製造業に特化したデジタルトランスフォーメーション(DX)の実現を目指す請負開発型のコンサルティングサービスです。AI、iPaaS、および先端の技術を駆使して、製造プロセスの効率化、業務効率化、チームワーク強化、コスト削減、品質向上を実現します。このサービスは、製造業の課題を深く理解し、それに対する最適なデジタルソリューションを提供することで、企業が持続的な成長とイノベーションを達成できるようサポートします。
製造業ニュース解説
製造業、主に購買・調達部門にお勤めの方々に向けた情報を配信しております。
新任の方やベテランの方、管理職を対象とした幅広いコンテンツをご用意しております。
お問い合わせ
コストダウンが利益に直結する術だと理解していても、なかなか前に進めることができない状況。そんな時は、newjiのコストダウン自動化機能で大きく利益貢献しよう!
(β版非公開)