- お役立ち記事
- On-site improvement methods for achieving both “improved productivity” and “reduced costs”—Successful examples sought by management
On-site improvement methods for achieving both “improved productivity” and “reduced costs”—Successful examples sought by management
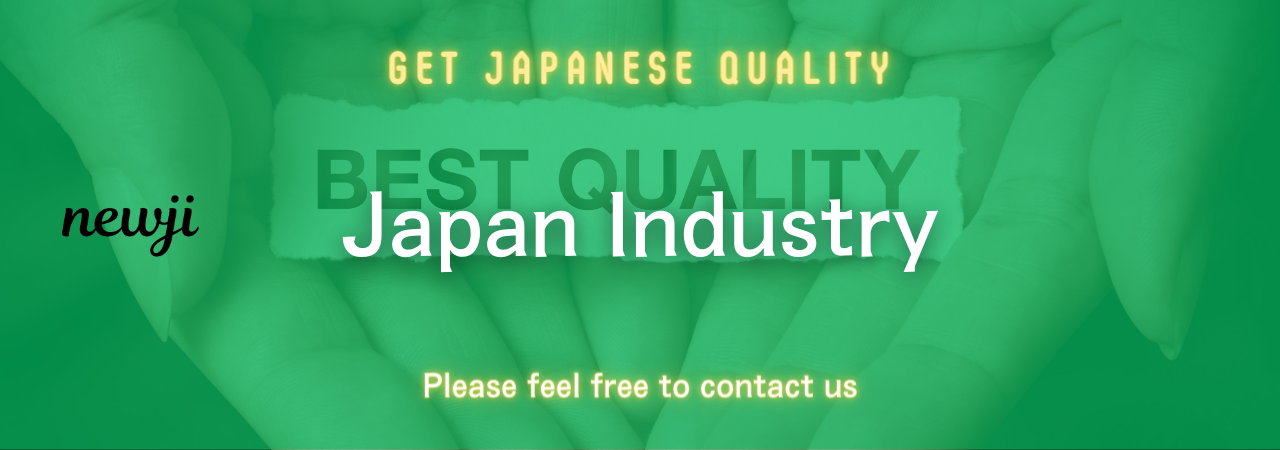
目次
Understanding On-Site Improvements
In today’s competitive business environment, companies are consistently looking for ways to enhance productivity while simultaneously reducing costs.
To achieve these dual objectives, many organizations are turning to on-site improvement methods that focus on optimizing processes and resources.
These methods are particularly appealing to management because they promise tangible benefits and sustainable growth.
On-site improvements involve making changes directly at the location where work is performed, rather than through external alterations or investments.
By leveraging existing resources more effectively, companies can achieve significant gains in efficiency without incurring substantial new expenses.
The Importance of Productivity and Cost Reduction
Productivity and cost reduction are critical components of successful business operations.
Improved productivity ensures that a company can produce more outputs with the same or fewer inputs, leading to increased profitability.
Simultaneously, reducing costs helps in maintaining a competitive edge, particularly in industries with thin profit margins.
Management is tasked with balancing these two objectives, aligning them with broader business strategies, and seeking ways to achieve them without compromising on quality or employee satisfaction.
The successful execution of on-site improvements can lead to impressive gains, creating a ripple effect across various departments and functions.
On-Site Improvement Methods
1. Lean Manufacturing
Lean manufacturing is one of the most well-known methodologies for on-site improvement.
It focuses on eliminating waste, optimizing processes, and enhancing value for the customer.
By identifying non-value-adding activities and removing them, companies can streamline operations and improve productivity.
Toyota, the pioneer of the Lean system, has effectively utilized this approach, becoming a role model for businesses worldwide.
By applying Lean principles, companies can identify inefficiencies, reduce cycle times, and create a culture of continuous improvement.
2. Six Sigma
Six Sigma is another powerful tool for on-site improvement.
This data-driven approach aims to improve quality by identifying and removing causes of defects and minimizing variability in manufacturing and business processes.
With a focus on reducing errors and improving consistency, Six Sigma enables organizations to enhance productivity and reduce costs.
Many industry leaders, such as GE and Motorola, have adopted Six Sigma to achieve operational excellence.
Implementing this methodology can lead to higher customer satisfaction, reduced waste, and better utilization of resources.
3. Total Quality Management (TQM)
Total Quality Management emphasizes customer satisfaction, continuous improvement, and employee involvement.
By fostering a culture where quality is everyone’s responsibility, TQM encourages organizations to focus on long-term success through customer focus and organizational involvement.
Famous examples of TQM in action include companies like Toyota and Ford.
These organizations have seen tremendous benefits by incorporating a quality-centric approach in their manufacturing and service processes.
4. Kaizen
Kaizen is a Japanese term meaning “continuous improvement” and is based on making small, incremental changes.
This philosophy engages employees at all levels to contribute suggestions and improvements in processes, ultimately leading to substantial performance gains.
By fostering a sense of ownership among employees, Kaizen can lead to heightened morale, greater innovation, and significant reductions in costs, as employees become more invested in the success of the business.
Successful Examples of On-Site Improvement
1. Toyota’s Lean Practices
Toyota has led the way in on-site improvement with its Lean manufacturing principles.
The company’s production system focuses on waste reduction, continuous improvement, and respect for people.
Toyota’s approach has resulted in increased efficiency, product reliability, and reduced costs across its operations.
Toyota’s Lean system has been so successful that it has become a standard for industries worldwide, seeking to replicate its triumphs in optimizing production processes.
2. General Electric’s Six Sigma Revolution
Under the leadership of Jack Welch, General Electric implemented Six Sigma across its diverse business portfolio.
This strategic focus on quality and process improvement resulted in significant cost savings, enhanced productivity, and customer satisfaction.
The successful adoption of Six Sigma allowed GE to experience rapid growth and become a global leader in multiple sectors.
3. Ford’s TQM Engagement
Ford Motor Company has successfully integrated Total Quality Management into its operations.
By prioritizing quality and customer satisfaction, Ford has reduced defects, improved reliability, and increased productivity.
Ford’s commitment to quality has allowed the company to compete effectively in the global automotive market while achieving cost reductions.
4. Nissan’s Kaizen Culture
Nissan has effectively employed Kaizen principles to drive continuous improvement in its manufacturing processes.
By empowering employees to suggest and implement changes, Nissan has seen increased innovation, efficiency, and cost savings.
The sense of collaboration fostered by Kaizen has strengthened Nissan’s competitive position and allowed it to adapt rapidly to industry changes.
Conclusion: Making On-Site Improvements Work for Your Business
On-site improvement methods are powerful tools for companies seeking to improve productivity and reduce costs.
By adopting these strategies—such as Lean manufacturing, Six Sigma, TQM, and Kaizen—organizations can achieve significant gains in efficiency and performance.
Ultimately, the key to successful on-site improvements lies in creating a culture of continuous optimization, where employees are engaged, processes are regularly evaluated, and management is committed to driving change.
With dedication and the right strategies, any organization can emulate the success stories of industry leaders and secure a prosperous future.
資料ダウンロード
QCD調達購買管理クラウド「newji」は、調達購買部門で必要なQCD管理全てを備えた、現場特化型兼クラウド型の今世紀最高の購買管理システムとなります。
ユーザー登録
調達購買業務の効率化だけでなく、システムを導入することで、コスト削減や製品・資材のステータス可視化のほか、属人化していた購買情報の共有化による内部不正防止や統制にも役立ちます。
NEWJI DX
製造業に特化したデジタルトランスフォーメーション(DX)の実現を目指す請負開発型のコンサルティングサービスです。AI、iPaaS、および先端の技術を駆使して、製造プロセスの効率化、業務効率化、チームワーク強化、コスト削減、品質向上を実現します。このサービスは、製造業の課題を深く理解し、それに対する最適なデジタルソリューションを提供することで、企業が持続的な成長とイノベーションを達成できるようサポートします。
オンライン講座
製造業、主に購買・調達部門にお勤めの方々に向けた情報を配信しております。
新任の方やベテランの方、管理職を対象とした幅広いコンテンツをご用意しております。
お問い合わせ
コストダウンが利益に直結する術だと理解していても、なかなか前に進めることができない状況。そんな時は、newjiのコストダウン自動化機能で大きく利益貢献しよう!
(Β版非公開)