- お役立ち記事
- On-site improvement plan for “inventory minimization”—Lead time shortening methods guided by management
On-site improvement plan for “inventory minimization”—Lead time shortening methods guided by management
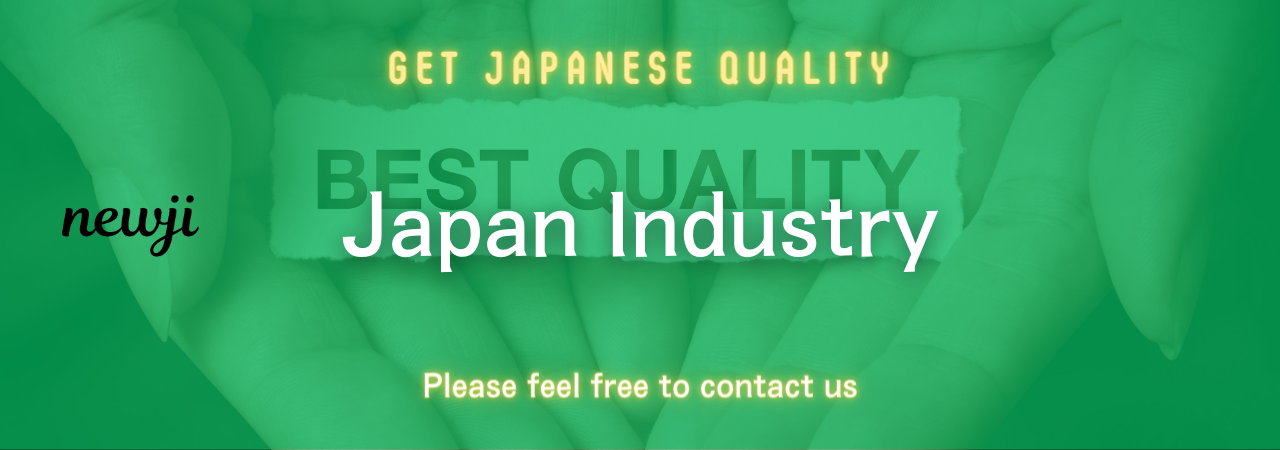
目次
Understanding Inventory Minimization
Inventory minimization is a crucial component in efficient supply chain management.
A key strategy focuses on reducing excess inventory to save costs and enhance business agility.
The principle is to maintain the lowest possible inventory levels without compromising production flow or customer satisfaction.
In essence, inventory minimization aims to improve cash flow and reduce the financial burden of holding excessive stock.
By minimizing unnecessary inventory, businesses can free up capital for other critical operations, lower storage costs, and reduce risks associated with unsold goods.
Benefits of Reducing Lead Times
Reducing lead times is integral to an effective inventory minimization strategy.
Shorter lead times mean faster production and delivery cycles, which can improve customer satisfaction and increase market competitiveness.
One significant benefit is the ability to respond swiftly to market demand fluctuations.
With minimized lead times, companies can produce and deliver products faster, meeting the consumers’ expectations promptly.
Furthermore, shorter lead times reduce the need for large safety stock since the lead time uncertainty is minimized.
Additionally, this approach helps in lowering inventory costs as companies purchase less raw material or components, which further aligns with just-in-time (JIT) delivery strategies.
Strategies for Shortening Lead Times
Streamline Processes
Streamlining internal processes is a fundamental strategy to reduce lead times.
Analyze every step from order processing to product delivery.
Eliminate any non-value-adding activities to speed up operations.
Automation tools can efficiently handle repetitive tasks, reducing processing time and errors.
For instance, implementing automated order processing systems can significantly decrease the time from order receipt to production initiation.
Enhance Supplier Relationships
Cultivating strong relationships with suppliers can have a direct impact on reducing lead times.
Engage in proactive communication to ensure they understand your demand patterns and lead time requirements.
Negotiate agreements that prioritize your orders to facilitate faster material delivery.
Consider establishing long-term partnerships with a few reliable suppliers rather than maintaining multiple transactional relationships.
It helps ensure committed service levels, and in urgent scenarios, partners may work to expedite your needs.
Optimize Inventory Management
Optimizing inventory management is crucial for minimizing lead times while keeping stock levels low.
Utilize inventory management software to accurately forecast demand and determine optimal reorder points and quantities.
Employing techniques like Economic Order Quantity (EOQ) can balance holding costs with ordering costs, reducing excess stock and enhancing cash flow.
Incorporating real-time inventory tracking can provide valuable insights into stock levels and movement, assisting in making swift replenishment decisions.
Invest in Supply Chain Technology
Investing in advanced supply chain technologies is essential to efficient lead time management.
Platforms with integrated supply chain management features offer better visibility, helping businesses identify bottlenecks or delays in the supply chain process.
Technology like the Internet of Things (IoT) can enable real-time tracking of shipments, which improves scheduling accuracy and reduces uncertainty.
Moreover, AI-powered analytics help in predicting demand patterns accurately, allowing manufacturers to proactively adjust their operations accordingly.
Implementing Continuous Improvement Practices
It’s vital to adopt a culture of continuous improvement to consistently minimize lead times and inventory levels.
Leverage methodologies like Lean and Six Sigma to identify inefficiencies in production processes and make incremental improvements.
Continually train employees on best practices and emerging technologies that contribute to reducing lead times.
Employee engagement in process improvements is crucial, as they often have insights on potential operational inefficiencies.
Conduct regular audits on supply chain processes and have dedicated teams focus on lead time reduction initiatives.
Benchmarking against industry standards and competitors can also provide direction for making necessary operational improvements.
Management’s Role in Inventory Minimization
Management plays a pivotal role in driving strategies for inventory minimization and reducing lead times.
They must set clear goals and KPIs aligned with inventory and lead time reduction objectives.
Regular review meetings to assess progress against these targets can keep teams focused and accountable.
A strong leadership commitment is required to foster collaboration across departments.
Supply chain, production, sales, and finance teams must work together to synchronize activities for optimum inventory levels and shortened lead times.
Additionally, management should be supportive of investing in the right technologies, training programs, and resources necessary to achieve inventory optimization goals.
Conclusion
In minimizing inventory while shortening lead times, companies can significantly enhance operational efficiency and responsiveness to market demands.
It requires well-coordinated efforts across the organization, from streamlining processes and enhancing supplier relationships to leveraging advanced technologies.
By focusing on continuous improvement and driving these changes from the management level, businesses can maintain competitive advantage, improve customer satisfaction, and achieve better financial performance through reduced inventory costs.
資料ダウンロード
QCD調達購買管理クラウド「newji」は、調達購買部門で必要なQCD管理全てを備えた、現場特化型兼クラウド型の今世紀最高の購買管理システムとなります。
ユーザー登録
調達購買業務の効率化だけでなく、システムを導入することで、コスト削減や製品・資材のステータス可視化のほか、属人化していた購買情報の共有化による内部不正防止や統制にも役立ちます。
NEWJI DX
製造業に特化したデジタルトランスフォーメーション(DX)の実現を目指す請負開発型のコンサルティングサービスです。AI、iPaaS、および先端の技術を駆使して、製造プロセスの効率化、業務効率化、チームワーク強化、コスト削減、品質向上を実現します。このサービスは、製造業の課題を深く理解し、それに対する最適なデジタルソリューションを提供することで、企業が持続的な成長とイノベーションを達成できるようサポートします。
オンライン講座
製造業、主に購買・調達部門にお勤めの方々に向けた情報を配信しております。
新任の方やベテランの方、管理職を対象とした幅広いコンテンツをご用意しております。
お問い合わせ
コストダウンが利益に直結する術だと理解していても、なかなか前に進めることができない状況。そんな時は、newjiのコストダウン自動化機能で大きく利益貢献しよう!
(Β版非公開)