- お役立ち記事
- On-site innovation method for press machines and injection molding machines using wireless sensor technology
月間77,185名の
製造業ご担当者様が閲覧しています*
*2025年2月28日現在のGoogle Analyticsのデータより
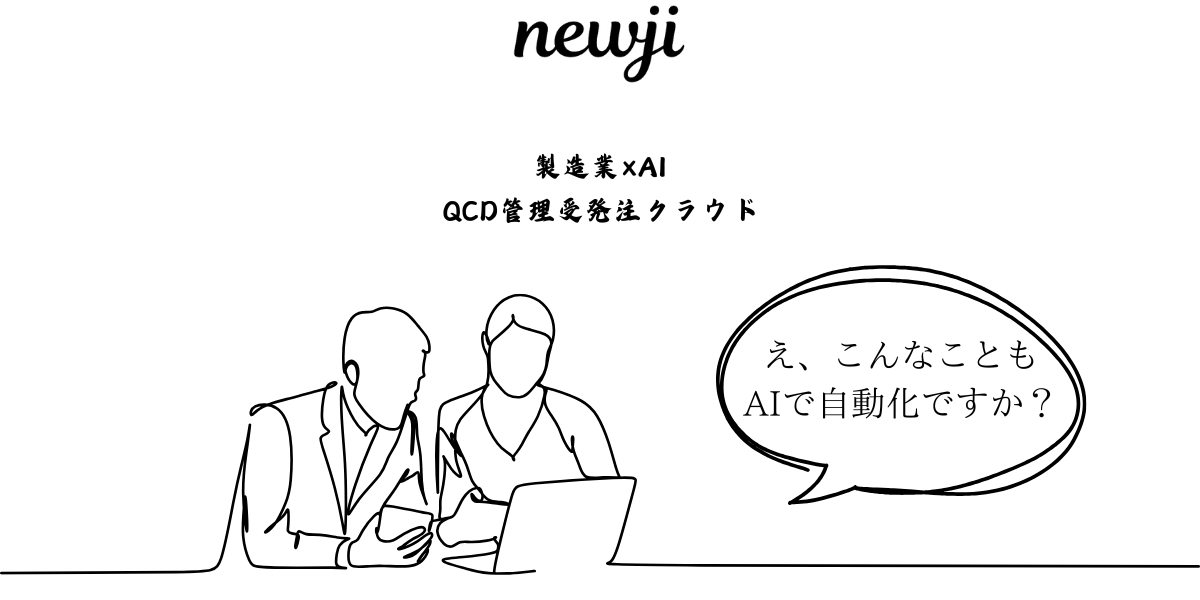
On-site innovation method for press machines and injection molding machines using wireless sensor technology
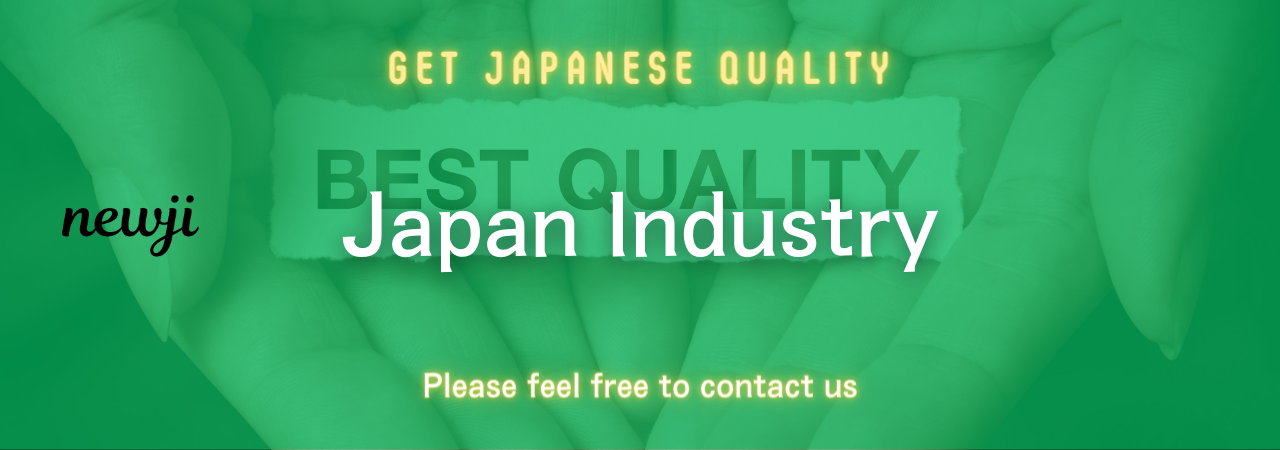
目次
Introduction to Wireless Sensor Technology
Wireless sensor technology has been a game changer in various industries, enhancing productivity and precision.
In the realm of manufacturing, especially in the use of press machines and injection molding machines, this technology holds immense potential for on-site innovation.
By integrating wireless sensors, manufacturers can collect real-time data that helps in monitoring machine performance, predicting maintenance, and improving overall efficiency.
What Are Press Machines and Injection Molding Machines?
Before delving into the innovative methods using wireless sensor technology, it’s essential to understand what press machines and injection molding machines are.
Press machines are utilized in metalworking to shape or cut metal by applying pressure.
They are pivotal in industries like automotive, construction, and electronics.
Injection molding machines, on the other hand, are used to produce parts by injecting material — typically plastic — into a mold.
This method is crucial in producing consistent and complex plastic components used in various industries including automotive, consumer goods, and aerospace.
The Role of Wireless Sensor Technology
Wireless sensor technology facilitates the collection of data without the need for cumbersome wiring or manual data collection processes.
This leads to a cleaner, safer work environment and reduces the risk of errors or omissions in data collection.
For press and injection molding machines, wireless sensors can monitor parameters such as temperature, pressure, vibration, and speed, ensuring machines operate at optimum conditions.
Monitoring Machine Health
By continuously monitoring machine health through wireless sensors, manufacturers can implement predictive maintenance strategies.
For example, if a sensor detects an unusual vibration pattern in a press machine, it can signal potential bearing failure.
This early warning system allows for timely maintenance, preventing costly breakdowns and minimizing downtime.
Enhancing Production Quality
Quality control is paramount in manufacturing, and any defects can lead to significant waste and cost.
With wireless sensors, operators can monitor process parameters in real-time and make necessary adjustments to maintain product quality.
In injection molding, for instance, sensors can measure mold temperature and material pressure, ensuring that components are made to precise specifications.
Optimizing Energy Consumption
One of the significant advantages of using wireless sensors in manufacturing is optimizing energy consumption.
Press machines and injection molding machines are heavy electricity consumers.
Sensors can detect idle states or inefficiencies, prompting operators to implement energy-saving measures.
This not only reduces operational costs but also aligns with environmental sustainability goals.
Case Studies of On-Site Innovation
Examining real-world applications of wireless sensor technology in press and injection molding machines showcases its transformative potential.
Automotive Industry
In the automotive industry, where both press and injection molding machines are extensively used, wireless sensors have streamlined operations.
By equipping these machines with sensors, manufacturers have achieved significant reductions in equipment downtime.
Predictive maintenance enabled by sensors has decreased unscheduled stoppages, increasing production efficiency and lowering repair costs.
Consumer Goods Manufacturing
Consumer goods manufacturers have adopted wireless sensor technology to enhance product quality.
For instance, in the production of plastic parts using injection molding machines, sensors have ensured consistent quality by maintaining optimal processing conditions.
This minimizes defects and rejects, thus increasing customer satisfaction and reducing waste.
Challenges and Future Prospects
While wireless sensor technology offers numerous benefits, implementing it in manufacturing does come with challenges.
Integration and Compatibility
Integrating wireless sensor technology with existing manufacturing systems can be complex and requires extensive planning.
Compatibility issues may arise, necessitating custom solutions or updates to legacy systems.
Data Management
As with any data-centric technology, managing the large volumes of data generated by wireless sensors can be daunting.
Manufacturers need robust data management systems to store, process, and analyze data effectively.
Future Prospects
The future of wireless sensor technology in press and injection molding machines looks promising.
With advancements in sensor accuracy, durability, and cost-effectiveness, more manufacturers are expected to adopt this technology.
The integration of artificial intelligence and machine learning could further enhance predictive capabilities, automating decision-making processes and optimizing manufacturing operations.
Conclusion
Wireless sensor technology presents a viable method for on-site innovation in press and injection molding machines.
Through enhanced monitoring, predictive maintenance, and energy optimization, manufacturers can achieve improved efficiency and quality while reducing operational costs.
Despite challenges, the continuous evolution of this technology is set to revolutionize manufacturing processes, paving the way for smarter, more sustainable production methods.
資料ダウンロード
QCD管理受発注クラウド「newji」は、受発注部門で必要なQCD管理全てを備えた、現場特化型兼クラウド型の今世紀最高の受発注管理システムとなります。
ユーザー登録
受発注業務の効率化だけでなく、システムを導入することで、コスト削減や製品・資材のステータス可視化のほか、属人化していた受発注情報の共有化による内部不正防止や統制にも役立ちます。
NEWJI DX
製造業に特化したデジタルトランスフォーメーション(DX)の実現を目指す請負開発型のコンサルティングサービスです。AI、iPaaS、および先端の技術を駆使して、製造プロセスの効率化、業務効率化、チームワーク強化、コスト削減、品質向上を実現します。このサービスは、製造業の課題を深く理解し、それに対する最適なデジタルソリューションを提供することで、企業が持続的な成長とイノベーションを達成できるようサポートします。
製造業ニュース解説
製造業、主に購買・調達部門にお勤めの方々に向けた情報を配信しております。
新任の方やベテランの方、管理職を対象とした幅広いコンテンツをご用意しております。
お問い合わせ
コストダウンが利益に直結する術だと理解していても、なかなか前に進めることができない状況。そんな時は、newjiのコストダウン自動化機能で大きく利益貢献しよう!
(β版非公開)