- お役立ち記事
- On-site measures to reduce man-hours sought by management—improvement methods to increase work efficiency
月間76,176名の
製造業ご担当者様が閲覧しています*
*2025年3月31日現在のGoogle Analyticsのデータより
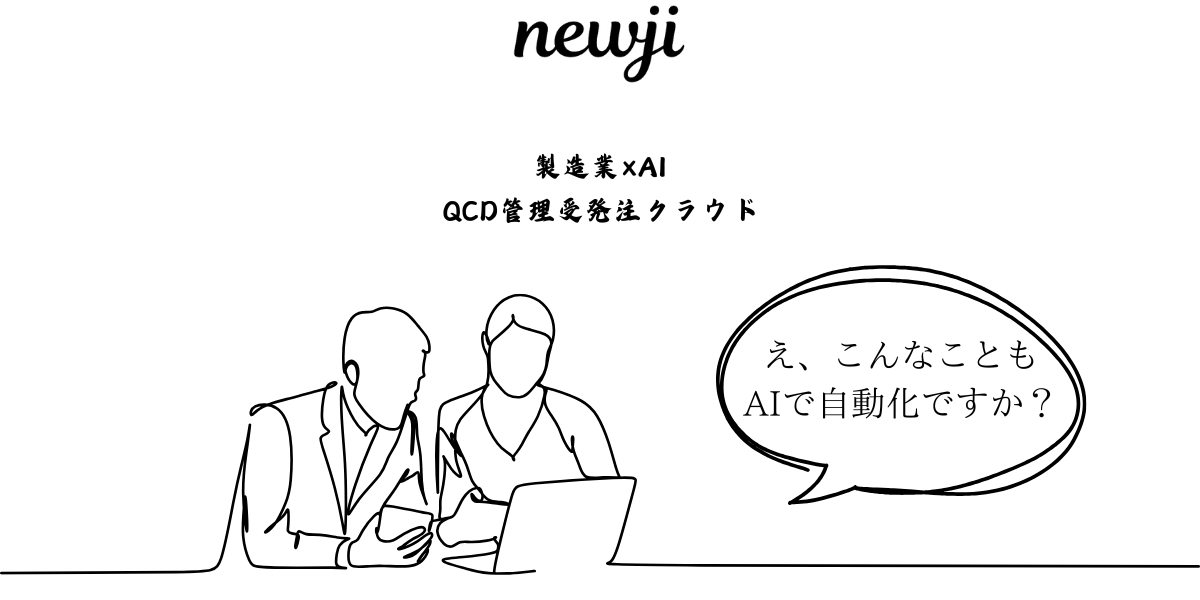
On-site measures to reduce man-hours sought by management—improvement methods to increase work efficiency
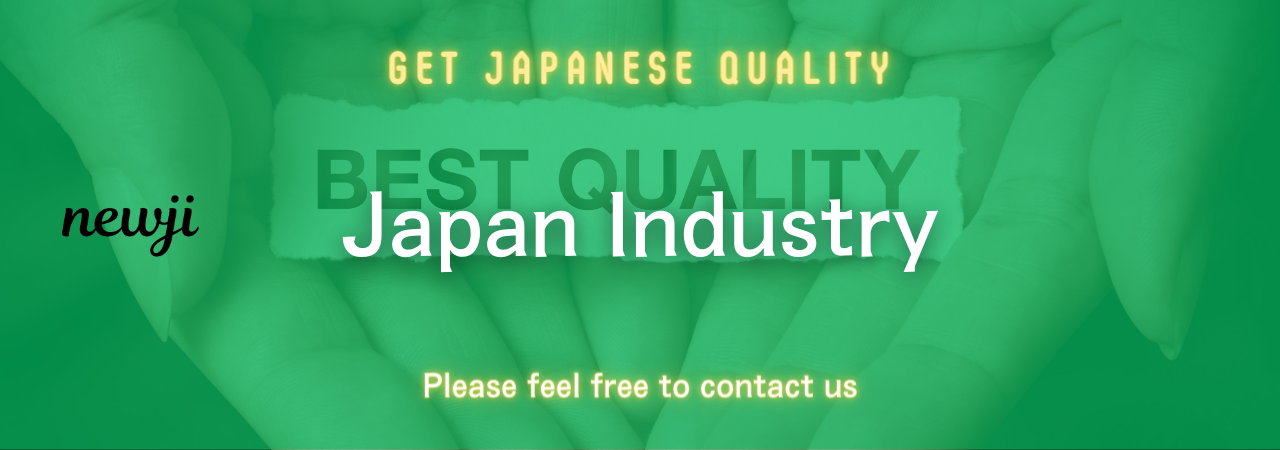
目次
Understanding the Need for On-Site Measures to Reduce Man-Hours
In today’s competitive business environment, companies are constantly seeking ways to improve efficiency and reduce costs.
One of the most effective ways to achieve this is by reducing man-hours on site.
Man-hours refer to the total number of hours worked by employees, and minimizing these can lead to significant savings and increased productivity.
Management feels the pressure to find solutions that not only reduce man-hours but also maintain or improve the quality of work.
Why Reducing Man-Hours is Important
Reducing man-hours is crucial for several reasons.
First and foremost, it directly impacts the bottom line by reducing labor costs.
In industries where labor is a significant expense, even a small reduction in man-hours can lead to substantial financial savings.
Moreover, by optimizing the use of man-hours, companies can reallocate resources to more strategic initiatives.
Efficiency gains also lead to better use of employee skills and talents.
When employees aren’t bogged down by time-consuming tasks, they can focus on higher-priority work, adding more value to the company.
This also contributes to employee satisfaction as they engage in more meaningful tasks that match their skills and interests.
Effective Strategies to Reduce Man-Hours
1. Implementing Technology Solutions
One of the most straightforward ways to reduce man-hours is by leveraging technology.
Automation tools, for instance, can perform repetitive tasks that would otherwise take up significant employee time.
Software solutions for scheduling and task management can streamline processes, reducing the time spent on organizing work.
Additionally, smart technology such as AI and machine learning can analyze work patterns, suggesting efficiency improvements.
These technologies can also predict maintenance needs in advance, reducing downtime and the hours spent on unplanned repairs.
2. Streamlining Processes
Process improvement is key to reducing man-hours effectively.
Conducting a thorough review of existing processes can identify bottlenecks and areas for improvement.
Methods such as Lean and Six Sigma provide frameworks to eliminate waste and enhance workflow efficiency.
Simplifying communication channels and decision-making processes also contributes to fewer man-hours.
Clear communication ensures that employees understand their tasks and can execute them without unnecessary delays.
3. Training and Development
Investing in training and development is another strategy to reduce on-site man-hours.
When employees are equipped with the right skills, they can complete tasks faster and with higher competence.
Ongoing training helps staff stay updated with the latest industry practices and technology, which in turn enhances productivity.
Cross-training employees is another effective measure.
Having a workforce that can handle multiple roles reduces the dependency on individual workers and allows for more flexible scheduling.
4. Enhancing Employee Engagement
Engaged employees tend to be more productive, reducing the man-hours needed to complete tasks.
Creating a supportive workplace culture where employees feel valued can lead to enhanced motivation and efficiency.
Encouraging feedback and involving employees in decision-making can provide insights into practical ways to cut down on hours while improving output quality.
Engaged employees often come up with creative solutions to increase efficiency.
Implementing Work Efficiency Improvement Methods
1. Adopting Flexible Work Arrangements
Flexible work arrangements like remote-working and flexible hours can lead to better work-life balance for employees, increasing their productivity and efficiency.
Remote work eliminates commute time, which increases available work time, while flexible schedules can help employees work during their most productive hours.
2. Setting Clear and Achievable Goals
Having clear, measurable goals enables employees to focus efforts on tasks that truly matter, reducing wasted time on unimportant activities.
Management should work to set realistic targets and guidelines that align with the company’s broader objectives.
Regular accountability checks ensure that everyone remains on track to meet these objectives efficiently.
3. Encouraging Small Breaks
Encouraging employees to take small breaks might seem counterproductive to reducing man-hours, but breaks prevent burnout and maintain high levels of productivity.
Short, planned breaks allow workers to rest and refocus, improving overall performance and efficiency when they return to work tasks.
Conclusion: Balancing Efficiency with Quality
In conclusion, reducing on-site man-hours is a critical goal for management seeking increased workplace efficiency and cost savings.
By implementing technology solutions, streamlining processes, and investing in employee training, companies can achieve this goal.
Moreover, strategies such as enhancing employee engagement and adopting flexible work arrangements can further contribute to man-hour reductions.
While the focus is on efficiency, it is vital that quality is maintained to ensure customer satisfaction and business success.
By balancing efficiency enhancements with quality considerations, companies can thrive in today’s competitive marketplace.
資料ダウンロード
QCD管理受発注クラウド「newji」は、受発注部門で必要なQCD管理全てを備えた、現場特化型兼クラウド型の今世紀最高の受発注管理システムとなります。
ユーザー登録
受発注業務の効率化だけでなく、システムを導入することで、コスト削減や製品・資材のステータス可視化のほか、属人化していた受発注情報の共有化による内部不正防止や統制にも役立ちます。
NEWJI DX
製造業に特化したデジタルトランスフォーメーション(DX)の実現を目指す請負開発型のコンサルティングサービスです。AI、iPaaS、および先端の技術を駆使して、製造プロセスの効率化、業務効率化、チームワーク強化、コスト削減、品質向上を実現します。このサービスは、製造業の課題を深く理解し、それに対する最適なデジタルソリューションを提供することで、企業が持続的な成長とイノベーションを達成できるようサポートします。
製造業ニュース解説
製造業、主に購買・調達部門にお勤めの方々に向けた情報を配信しております。
新任の方やベテランの方、管理職を対象とした幅広いコンテンツをご用意しております。
お問い合わせ
コストダウンが利益に直結する術だと理解していても、なかなか前に進めることができない状況。そんな時は、newjiのコストダウン自動化機能で大きく利益貢献しよう!
(β版非公開)