- お役立ち記事
- Operation and Maintenance of Casting Machines in Steel Factories
月間76,176名の
製造業ご担当者様が閲覧しています*
*2025年3月31日現在のGoogle Analyticsのデータより
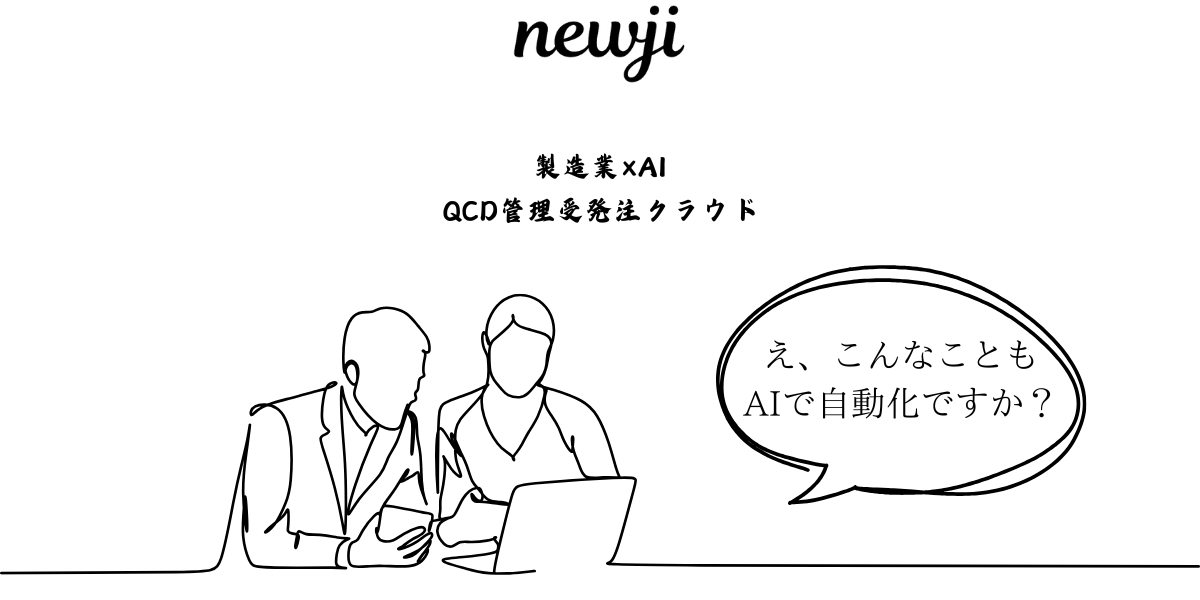
Operation and Maintenance of Casting Machines in Steel Factories
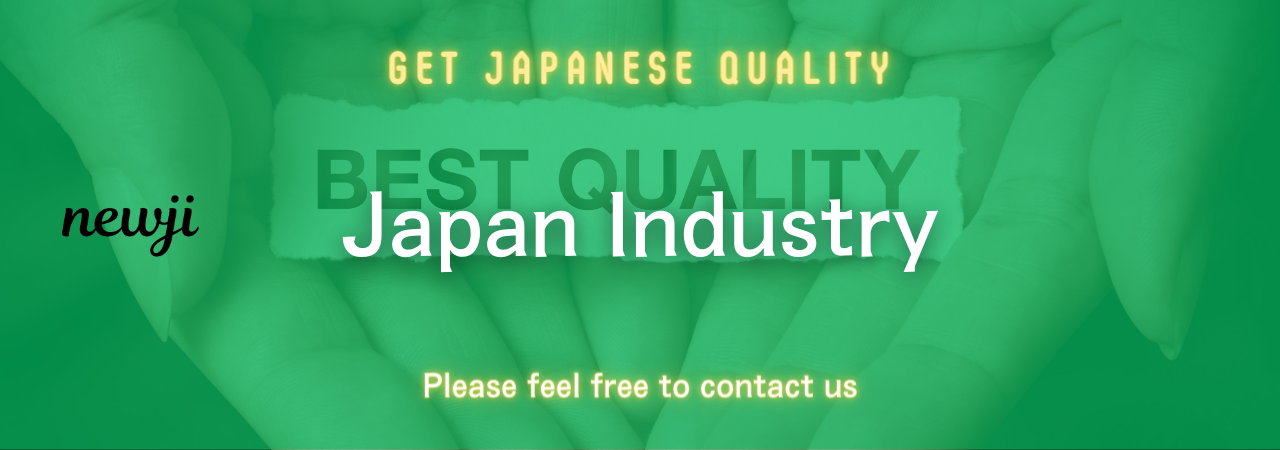
目次
Understanding Casting Machines in Steel Factories
Casting machines play a crucial role in steel factories.
They are essential in shaping molten steel into desired forms, which later undergo further processing.
In understanding their operation and maintenance, it is important to familiarize oneself with their function, design, and significance within the steel production process.
What Are Casting Machines?
Casting machines are specialized equipment used in the metal industry to convert molten metal into semi-finished shapes.
These shapes include billets, blooms, and slabs, which are then processed into final products like sheets, beams, and bars.
In steel factories, continuous casting machines are predominantly used due to their efficiency and ability to produce high-quality steel.
Types of Casting Machines
There are several types of casting machines used in steel production.
The most common are:
1. **Continuous Casting Machines**: These machines are widely used in modern steel factories.
They continuously extract steel from a ladle and solidify it into long strands without interruption.
This process improves efficiency and reduces waste.
2. **Vertical Casting Machines**: Vertical machines pour molten steel from a height, allowing it to harden as it descends.
The final solid shape is often used for structures requiring significant strength.
3. **Horizontal Casting Machines**: These machines produce long steel products in a horizontal orientation.
They are suitable for manufacturing steel pipes and rods.
Operation of Casting Machines
To operate casting machines effectively, thorough understanding and meticulous planning are required.
The process typically involves the following steps:
1. **Preparation**: Before beginning the casting operation, operators must ensure the mold and machine components are ready.
This includes verifying the alignment, temperature, and condition of the casting mold.
2. **Pouring Steel**: The molten steel is carefully poured into the casting machine through a tundish, a reservoir that regulates flow into the mold.
3. **Cooling and Solidification**: As the molten steel moves through the mold, it undergoes cooling and starts to solidify into the desired shape.
Cooling methods vary, including water sprays or immersion.
4. **Cutting and Transporting**: Once the steel has solidified, it is cut into specified lengths and transported for further processing or storage.
Importance of Maintenance
Regular maintenance of casting machines is crucial for ensuring efficient and safe operation.
Without proper upkeep, machines can suffer from wear and tear, leading to costly downtimes and production losses.
Maintenance tasks include:
1. **Routine Inspections**: Frequent inspections help identify components that need repair or replacement, preventing minor issues from escalating into major problems.
2. **Cleaning**: Removing steel residues and other buildups is crucial to preventing blockages and maintaining the accuracy of the casting mold.
3. **Lubrication**: Providing adequate lubrication ensures smooth operation of moving parts, reducing friction and wear.
4. **Calibration and Adjustments**: Regularly calibrating machines ensures they operate at optimal performance, producing high-quality steel efficiently.
Challenges in Operation and Maintenance
While casting machines are indispensable in steel production, they come with certain challenges:
1. **Technological Demands**: Modern casting machines require operators and maintenance personnel to have considerable technical expertise.
Ongoing training is necessary to keep up with technological advancements.
2. **Material Wear**: The intense heat and pressure involved in the casting process can lead to wear and damage of machine parts over time, necessitating careful monitoring.
3. **Energy Consumption**: Casting machines are energy-intensive, and factories must find a balance between production efficiency and energy use, considering the impact on operational costs.
Future Trends in Casting Machine Technology
Advancements in technology present exciting opportunities for the future of casting machines in steel factories:
1. **Automation and AI**: Automated systems and artificial intelligence can improve precision and reduce human error in machine operation.
They also facilitate predictive maintenance, enabling timely repairs and minimizing downtime.
2. **Eco-friendly Solutions**: As environmental concerns mount, the steel industry is exploring eco-friendly casting technologies.
These include systems with lower energy consumption and reduced emissions.
3. **3D Printing**: Although still in the experimental stage for steel production, 3D printing offers potential for more customized shapes and reduced material waste.
Conclusion
Casting machines are fundamental to the steel manufacturing process, shaping raw metal into products used across various industries.
Understanding their operation and maintenance is essential for optimizing productivity and ensuring safety in steel factories.
While challenges exist, ongoing innovations offer promising solutions, enhancing the efficiency, sustainability, and capabilities of casting processes.
By embracing new technologies and prioritizing regular maintenance, steel factories can continue providing high-quality materials to support global infrastructure and development.
資料ダウンロード
QCD管理受発注クラウド「newji」は、受発注部門で必要なQCD管理全てを備えた、現場特化型兼クラウド型の今世紀最高の受発注管理システムとなります。
ユーザー登録
受発注業務の効率化だけでなく、システムを導入することで、コスト削減や製品・資材のステータス可視化のほか、属人化していた受発注情報の共有化による内部不正防止や統制にも役立ちます。
NEWJI DX
製造業に特化したデジタルトランスフォーメーション(DX)の実現を目指す請負開発型のコンサルティングサービスです。AI、iPaaS、および先端の技術を駆使して、製造プロセスの効率化、業務効率化、チームワーク強化、コスト削減、品質向上を実現します。このサービスは、製造業の課題を深く理解し、それに対する最適なデジタルソリューションを提供することで、企業が持続的な成長とイノベーションを達成できるようサポートします。
製造業ニュース解説
製造業、主に購買・調達部門にお勤めの方々に向けた情報を配信しております。
新任の方やベテランの方、管理職を対象とした幅広いコンテンツをご用意しております。
お問い合わせ
コストダウンが利益に直結する術だと理解していても、なかなか前に進めることができない状況。そんな時は、newjiのコストダウン自動化機能で大きく利益貢献しよう!
(β版非公開)