- お役立ち記事
- Optimal Equipment Selection for High Precision in Deburring
Optimal Equipment Selection for High Precision in Deburring
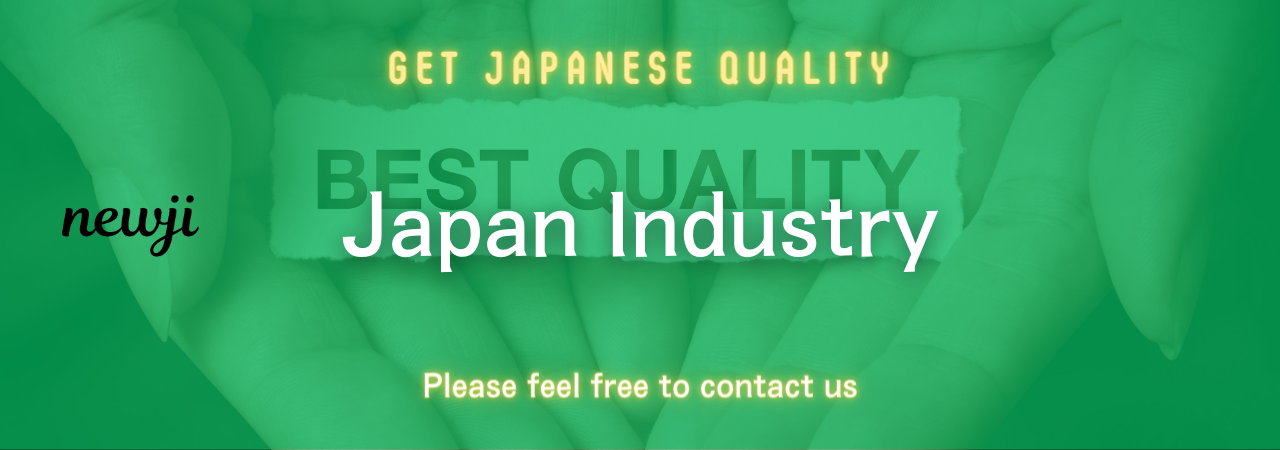
Choosing the right equipment for high-precision deburring is essential for achieving a smooth finish on manufactured components. Deburring involves removing unwanted burrs — small, rough edges or protrusions — that can occur after machining, welding, or other manufacturing processes. Selecting the most suitable equipment ensures efficiency, quality, and cost-effectiveness in manufacturing.
目次
Understanding Deburring and Its Importance
Deburring is a crucial step in the manufacturing process. It ensures that the final product is free from sharp edges and irregularities that can affect performance or safety. Burrs can cause parts to malfunction, diminish the aesthetic quality, or even lead to injuries. So, maintaining a smooth surface is not just about appearance but also about functionality and safety.
Different Types of Deburring Processes
There are various deburring processes available, each with its own set of advantages and suitability for different applications.
Manual Deburring
Manual deburring is one of the oldest and simplest methods. It involves using hand tools like files, sandpaper, and scrapers to remove burrs. Although it allows for fine detailing, manual deburring is labor-intensive and time-consuming. It’s best suited for small production batches or intricate parts that require a personal touch.
Mechanical Deburring
Mechanical deburring uses machines like tumblers, vibratory finishers, and abrasive brushes to remove burrs. This method is more consistent and faster than manual deburring. It’s ideal for larger production runs and parts that can withstand mechanical stress. The main drawback is that it might not reach very intricate areas.
Thermal Deburring
Thermal deburring, also known as burnishing, uses heat to burn off burrs. This process involves placing the part in a chamber and exposing it to an explosive mixture of gases. The high temperature vaporizes the burrs. Thermal deburring is effective for hard-to-reach areas but can be costly and requires special safety measures.
Chemical Deburring
Chemical deburring uses chemicals to dissolve burrs. This method is precise and can handle complex shapes and hard-to-reach areas. It’s suitable for delicate parts and provides a smooth finish. However, the chemicals can be hazardous and require proper handling and disposal.
Electrochemical Deburring
Electrochemical deburring combines electrical and chemical processes to remove burrs. It involves submerging the part in an electrolyte solution and applying an electric current to dissolve the burrs. This method is highly accurate and suitable for intricate and delicate parts. However, it requires specialized equipment and safety precautions.
Key Factors to Consider When Selecting Deburring Equipment
Choosing the optimal deburring equipment involves assessing various factors to match the specific needs of your manufacturing process.
Material Type
The type of material you are working with significantly impacts the choice of deburring equipment. Soft materials like aluminum may require different tools compared to harder materials like stainless steel. Ensure that the equipment you select is compatible with the material’s properties.
Part Geometry
The shape and complexity of the part also dictate the choice of deburring equipment. Intricate and delicate parts may require non-mechanical methods like chemical or electrochemical deburring, whereas simple shapes can be effectively deburred using mechanical methods.
Production Volume
Your production volume plays a crucial role in equipment selection. For high-volume production runs, automated mechanical deburring or thermal deburring may be more cost-effective and time-efficient. For low-volume or customized parts, manual or semi-automated methods might be preferable.
Precision and Tolerance
The required precision and tolerance levels affect the choice of deburring equipment. Processes like electrochemical deburring offer high precision and are suitable for components with tight tolerances. Ensure that the chosen method meets the required quality standards.
Cost and Budget
Budget constraints also influence equipment selection. Automated and high-precision deburring methods tend to be more expensive. Weigh the benefits of the equipment against the investment to determine the most cost-effective solution.
Benefits of High Precision in Deburring
Achieving high precision in deburring offers numerous benefits beyond just a smooth finish.
Improved Product Quality
High-precision deburring enhances the overall quality of the product. It ensures that all parts fit together seamlessly, reducing the risk of assembly issues and improving product performance.
Enhanced Durability
Removing burrs reduces stress concentrations and prevents premature wear or failure of parts. This leads to enhanced durability and longer product life.
Better Aesthetics
A burr-free surface provides a clean and professional appearance. This is particularly important for consumer products where aesthetics play a vital role in customer satisfaction.
Compliance with Standards
Many industries have stringent quality standards that require deburring. High-precision deburring ensures compliance with these standards, preventing costly rework or rejects.
Conclusion
Selecting the right equipment for high-precision deburring is a critical aspect of the manufacturing process. By carefully considering factors such as material type, part geometry, production volume, precision requirements, and budget, manufacturers can choose the most suitable deburring method.
High-precision deburring not only improves product quality and durability but also enhances aesthetics and ensures compliance with industry standards. Investing in the right deburring equipment is essential for achieving operational efficiency and producing top-quality products.
資料ダウンロード
QCD調達購買管理クラウド「newji」は、調達購買部門で必要なQCD管理全てを備えた、現場特化型兼クラウド型の今世紀最高の購買管理システムとなります。
ユーザー登録
調達購買業務の効率化だけでなく、システムを導入することで、コスト削減や製品・資材のステータス可視化のほか、属人化していた購買情報の共有化による内部不正防止や統制にも役立ちます。
NEWJI DX
製造業に特化したデジタルトランスフォーメーション(DX)の実現を目指す請負開発型のコンサルティングサービスです。AI、iPaaS、および先端の技術を駆使して、製造プロセスの効率化、業務効率化、チームワーク強化、コスト削減、品質向上を実現します。このサービスは、製造業の課題を深く理解し、それに対する最適なデジタルソリューションを提供することで、企業が持続的な成長とイノベーションを達成できるようサポートします。
オンライン講座
製造業、主に購買・調達部門にお勤めの方々に向けた情報を配信しております。
新任の方やベテランの方、管理職を対象とした幅広いコンテンツをご用意しております。
お問い合わせ
コストダウンが利益に直結する術だと理解していても、なかなか前に進めることができない状況。そんな時は、newjiのコストダウン自動化機能で大きく利益貢献しよう!
(Β版非公開)