- お役立ち記事
- Optimal Equipment Selection to Improve Productivity in Spinning
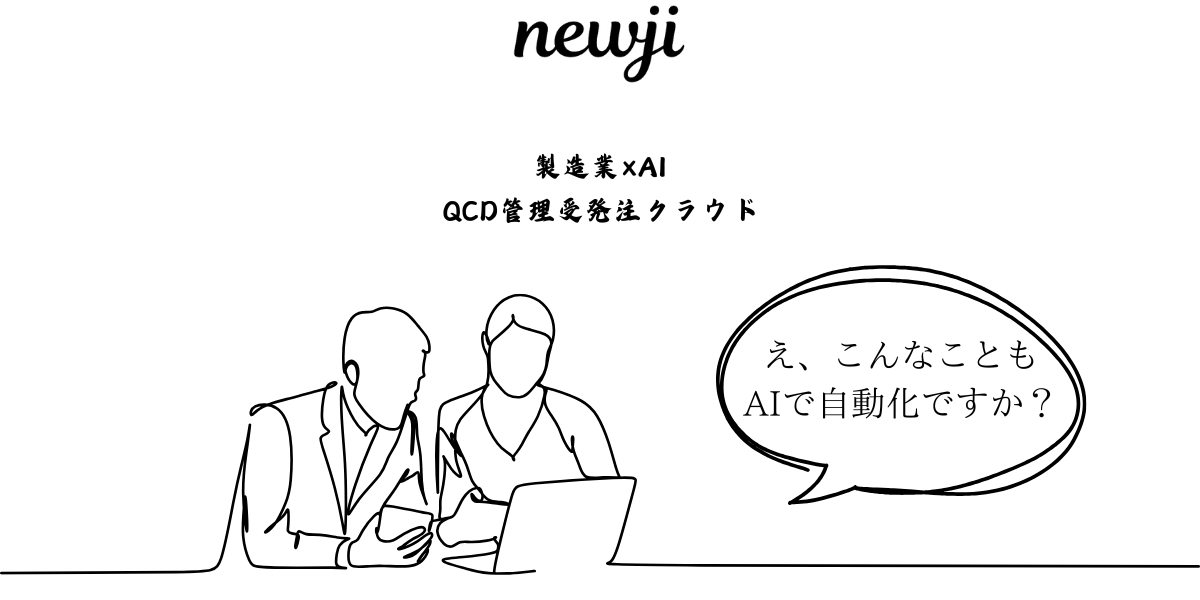
Optimal Equipment Selection to Improve Productivity in Spinning
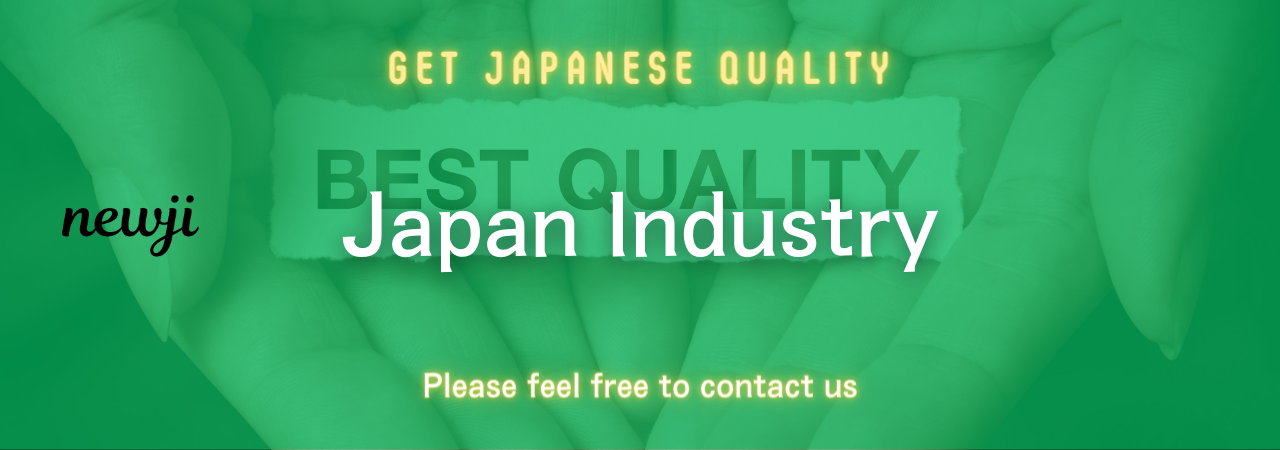
In the textile industry, productivity is directly linked to the efficiency of the equipment used.
Choosing the right machinery is crucial for any spinning mill that aims to maintain high production levels and superior quality.
Let’s explore the key factors that influence the optimal selection of spinning equipment and how each component contributes to improved productivity.
目次
Understanding the Basics of Spinning Equipment
Spinning involves converting raw fibers into yarn.
The process is intricate, involving various stages such as carding, drawing, roving, and spinning.
Each of these stages requires specific machinery, and the right combination ensures smooth operation and high-quality output.
Carding Machines
Carding is the initial stage where fibers are separated and aligned to form a web.
Modern carding machines come with features like auto-leveler control systems, which maintain consistent sliver weight.
Choosing a carding machine with an efficient auto-leveler can significantly enhance quality and productivity.
Drawing Frames
Drawing frames combine several slivers into one, ensuring better fiber alignment.
Advanced drawing frames come with auto-stop mechanisms that halt operations when there’s a break in the sliver, reducing waste and downtime.
Opting for drawing frames with high precision and automated features can continuously improve yarn quality and production speed.
Roving Frames
Roving frames reduce the thickness of the sliver and add a slight twist to form roving.
Modern roving frames are equipped with programmable logic controllers (PLCs) and automated doffing systems.
These features minimize human intervention, reducing errors and boosting productivity.
Spinning Machines
The final stage involves the use of spinning machines, where the rovings are stretched and twisted to form yarn.
Ring spinning, open-end spinning, and air-jet spinning are popular types.
The choice depends on the type of yarn required.
Advanced spinning machines often have features like online monitoring systems and energy-efficient motors.
These machines can lead to considerable savings in energy costs and enhance overall production rates.
Factors to Consider for Optimal Equipment Selection
Selecting the right spinning equipment involves evaluating several factors.
Here’s a breakdown of the most critical considerations:
Production Capacity
Before investing in new equipment, it’s essential to assess the required production capacity.
High-capacity machines are beneficial for large-scale operations but may not be cost-effective if the demand is low.
Balancing between the scale of operations and machine capacity ensures optimal efficiency.
Flexibility and Versatility
The textile market is dynamic, with fashion trends changing frequently.
Investing in versatile machinery that can adapt to different types of fibers and yarns can provide an edge.
Machines that offer easy changeover between different operations help in quickly responding to market demands without significant downtime.
Energy Efficiency
Energy costs can significantly impact the profitability of a spinning mill.
Modern machines are designed to be energy-efficient, often featuring advanced motors and drives.
Choosing energy-efficient equipment reduces operational costs and aligns with sustainable practices.
Automation and Technology
The level of automation in machinery plays a vital role in productivity.
Automation reduces manual labor, minimizes errors, and enhances consistency.
Technological advancements like IoT integration allow for real-time monitoring and predictive maintenance, further optimizing operations.
Quality of Output
The end goal of any spinning operation is to produce high-quality yarn.
Machines with precision controls, superior build quality, and advanced features ensure consistency and superior yarn quality.
Investing in well-engineered machinery can yield significant long-term benefits.
Cost Considerations
While it’s tempting to opt for the cheapest options, considering the total cost of ownership is essential.
This includes initial purchase cost, maintenance expenses, energy consumption, and potential downtime.
High-quality, reliable machines often have higher upfront costs but lower long-term expenses, proving more cost-effective.
The Role of Maintenance in Productivity
Even the best machinery can’t perform optimally without regular maintenance.
Maintaining equipment ensures that it operates at peak efficiency and reduces the likelihood of unexpected breakdowns.
Preventive Maintenance
Scheduled preventive maintenance involves regular inspection and servicing of machinery.
This can include tasks like lubricating moving parts, checking for wear and tear, and replacing worn components.
A robust preventive maintenance program can significantly extend the lifespan of equipment and maintain consistent production levels.
Predictive Maintenance
Predictive maintenance leverages advanced technologies like IoT sensors and data analytics to predict potential failures before they occur.
By continuously monitoring the condition of equipment, it’s possible to address issues proactively.
Implementing predictive maintenance can minimize downtime and associated costs, thereby improving productivity.
Training and Skill Development
Having advanced machinery is only beneficial if the workforce is skilled in operating and maintaining it.
Regular training programs ensure that operators are proficient in using the equipment to its full potential.
Operator Training
Comprehensive training programs for operators cover the basics of machine operation, troubleshooting, and best practices.
Skilled operators can maximize efficiency, reduce errors, and maintain high production standards.
Maintenance Training
Training maintenance personnel is equally important.
They should be adept at performing regular inspections, diagnosing issues, and carrying out necessary repairs.
Well-trained maintenance staff can significantly enhance machine longevity and reliability.
Conclusion
Optimal equipment selection is a multifaceted process that involves assessing production capacity, flexibility, energy efficiency, automation, and overall cost.
Regular maintenance and skill development further enhance the benefits of choosing the right machinery.
By carefully considering these factors, spinning mills can achieve higher productivity, superior yarn quality, and sustainable operations.
資料ダウンロード
QCD調達購買管理クラウド「newji」は、調達購買部門で必要なQCD管理全てを備えた、現場特化型兼クラウド型の今世紀最高の購買管理システムとなります。
ユーザー登録
調達購買業務の効率化だけでなく、システムを導入することで、コスト削減や製品・資材のステータス可視化のほか、属人化していた購買情報の共有化による内部不正防止や統制にも役立ちます。
NEWJI DX
製造業に特化したデジタルトランスフォーメーション(DX)の実現を目指す請負開発型のコンサルティングサービスです。AI、iPaaS、および先端の技術を駆使して、製造プロセスの効率化、業務効率化、チームワーク強化、コスト削減、品質向上を実現します。このサービスは、製造業の課題を深く理解し、それに対する最適なデジタルソリューションを提供することで、企業が持続的な成長とイノベーションを達成できるようサポートします。
オンライン講座
製造業、主に購買・調達部門にお勤めの方々に向けた情報を配信しております。
新任の方やベテランの方、管理職を対象とした幅広いコンテンツをご用意しております。
お問い合わせ
コストダウンが利益に直結する術だと理解していても、なかなか前に進めることができない状況。そんな時は、newjiのコストダウン自動化機能で大きく利益貢献しよう!
(Β版非公開)