- お役立ち記事
- Optimal Purchasing Methods and Technical Considerations for Ion Beam Etching OEM
Optimal Purchasing Methods and Technical Considerations for Ion Beam Etching OEM
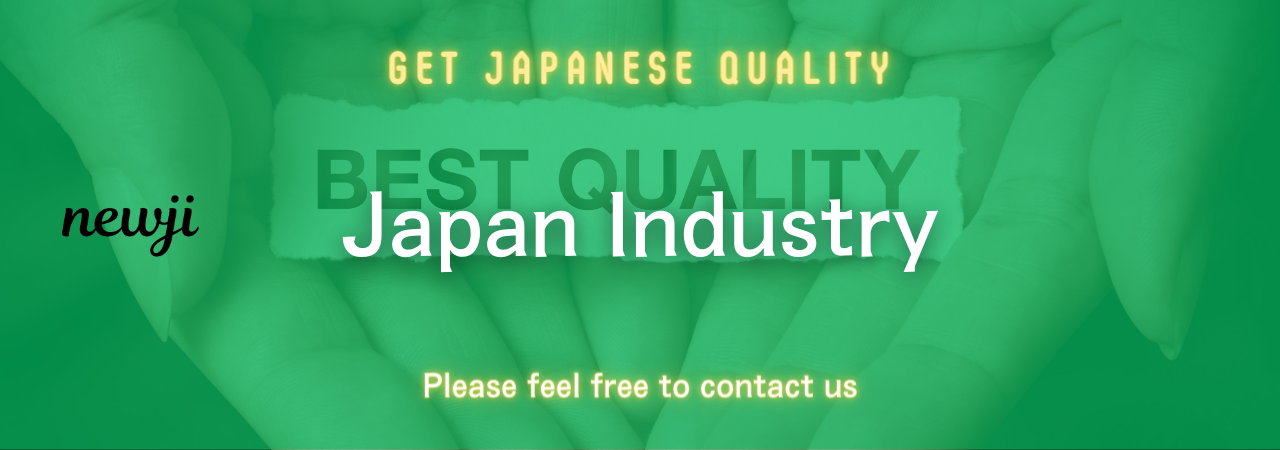
Understanding the optimal purchasing methods and technical considerations for ion beam etching OEM is crucial for businesses in the semiconductor and microelectronics industries.
This technology, known for its precision and efficiency, is increasingly in demand.
Let’s delve into the key factors that can help organizations make informed decisions when procuring ion beam etching equipment.
目次
What is Ion Beam Etching?
Ion beam etching, also known as ion milling, is a process used to remove material from a target substrate using a beam of ions.
It is commonly employed in the fabrication of semiconductor devices, microelectromechanical systems (MEMS), and other microelectronics.
The technique is valued for its ability to produce highly precise and clean etching results, making it ideal for applications that require intricate patterns and designs.
Key Factors in Purchasing Ion Beam Etching Equipment
When looking to purchase ion beam etching equipment from an Original Equipment Manufacturer (OEM), several factors should be taken into consideration.
These factors ensure that the equipment meets the specific needs of your application and maximizes return on investment.
1. Technical Specifications
One of the primary factors to consider is the technical specifications of the ion beam etching equipment.
Make sure to evaluate:
– Beam Energy: Different applications may require varying ion beam energies.
– Beam Uniformity: Consistent beam uniformity is essential for high-precision etching.
– Throughput: Assess the equipment’s processing speed and capability to handle your production volume.
2. Customization Options
Not all ion beam etching applications are the same.
Look for OEMs that offer customization options to tailor the equipment to your specific needs.
This may include specialized fixtures, unique chamber sizes, and custom software modifications.
3. Reliability and Maintenance
Consider the reliability of the ion beam etching equipment.
Opt for OEMs with a proven track record of producing durable and dependable machines.
Additionally, evaluate the maintenance requirements and availability of spare parts.
A reliable machine with minimal maintenance downtime will ensure smooth production processes.
4. Support and Training
Purchasing ion beam etching equipment is a significant investment.
Ensure that the OEM provides comprehensive support and training.
This can include installation assistance, user training, and ongoing technical support to address any issues that may arise.
5. Cost Considerations
While cost is always a consideration, it is essential to balance price with quality.
Cheaper equipment may cut corners, leading to higher long-term costs in terms of repairs, maintenance, and lower production quality.
Evaluate the total cost of ownership, not just the initial price.
6. Reviews and References
One of the best ways to gauge the reliability and performance of ion beam etching equipment is by seeking reviews and references from other customers.
Look for testimonials and case studies to understand better how the equipment performs in real-world applications.
Technical Considerations for Ion Beam Etching
To ensure the success of your ion beam etching processes, it’s essential to consider several technical factors.
These considerations will help you optimize the performance and precision of your etching operations.
1. Substrate Selection
The choice of substrate material is critical in ion beam etching.
Different materials respond differently to ion bombardment, affecting etching quality and precision.
Common materials include silicon, glass, metals, and polymers.
Ensure that your chosen substrate is compatible with the ion beam etching process.
2. Masking Materials
Masks are used to define the patterns to be etched onto the substrate.
Selecting the right masking material is crucial for achieving precise results.
Materials such as photoresist, metal films, and dielectric layers are commonly used.
Ensure that the masking material can withstand ion bombardment without degradation.
3. Process Parameters
Optimizing process parameters such as ion beam energy, angle, and etching time is essential for achieving desired results.
Fine-tuning these parameters can help improve etching precision, minimize damage to the substrate, and enhance overall efficiency.
4. Vacuum Environment
Ion beam etching requires a controlled vacuum environment to ensure accurate ion delivery and minimal contamination.
Investing in high-quality vacuum systems and regularly maintaining them is essential for consistent performance.
5. End-Point Detection
End-point detection is a technique used to monitor the progress of the etching process in real-time.
This allows for precise control and stopping of the etching process once the desired depth is reached.
Various methods, such as optical emission spectroscopy and secondary ion mass spectrometry, can be used for end-point detection.
Advantages of Ion Beam Etching
Ion beam etching offers several advantages that make it a preferred choice for many microelectronics applications.
1. High Precision
Ion beam etching provides exceptional precision, allowing for the creation of intricate patterns and structures.
This makes it ideal for applications that require fine features and tight tolerances.
2. Minimal Damage
Compared to other etching techniques, ion beam etching minimizes damage to the substrate.
This is particularly important for delicate materials and applications where maintaining structural integrity is crucial.
3. Versatility
Ion beam etching is versatile and can be used with various materials, including metals, semiconductors, and insulators.
This flexibility makes it suitable for a wide range of applications in different industries.
4. Clean Process
Ion beam etching is a clean process that produces minimal by-products and waste.
This reduces the risk of contamination and ensures a high-quality end product.
Conclusion
Purchasing ion beam etching equipment from an OEM requires careful consideration of various factors, including technical specifications, customization options, reliability, and support.
Understanding the technical considerations for ion beam etching, such as substrate selection, masking materials, and process parameters, is essential for achieving optimal results.
By evaluating these factors and making informed decisions, businesses can ensure successful implementation and maximize the benefits of ion beam etching technology.
資料ダウンロード
QCD調達購買管理クラウド「newji」は、調達購買部門で必要なQCD管理全てを備えた、現場特化型兼クラウド型の今世紀最高の購買管理システムとなります。
ユーザー登録
調達購買業務の効率化だけでなく、システムを導入することで、コスト削減や製品・資材のステータス可視化のほか、属人化していた購買情報の共有化による内部不正防止や統制にも役立ちます。
NEWJI DX
製造業に特化したデジタルトランスフォーメーション(DX)の実現を目指す請負開発型のコンサルティングサービスです。AI、iPaaS、および先端の技術を駆使して、製造プロセスの効率化、業務効率化、チームワーク強化、コスト削減、品質向上を実現します。このサービスは、製造業の課題を深く理解し、それに対する最適なデジタルソリューションを提供することで、企業が持続的な成長とイノベーションを達成できるようサポートします。
オンライン講座
製造業、主に購買・調達部門にお勤めの方々に向けた情報を配信しております。
新任の方やベテランの方、管理職を対象とした幅広いコンテンツをご用意しております。
お問い合わせ
コストダウンが利益に直結する術だと理解していても、なかなか前に進めることができない状況。そんな時は、newjiのコストダウン自動化機能で大きく利益貢献しよう!
(Β版非公開)