- お役立ち記事
- Optimal Purchasing Strategies and Technical Considerations for Aluminum Castings
月間76,176名の
製造業ご担当者様が閲覧しています*
*2025年3月31日現在のGoogle Analyticsのデータより
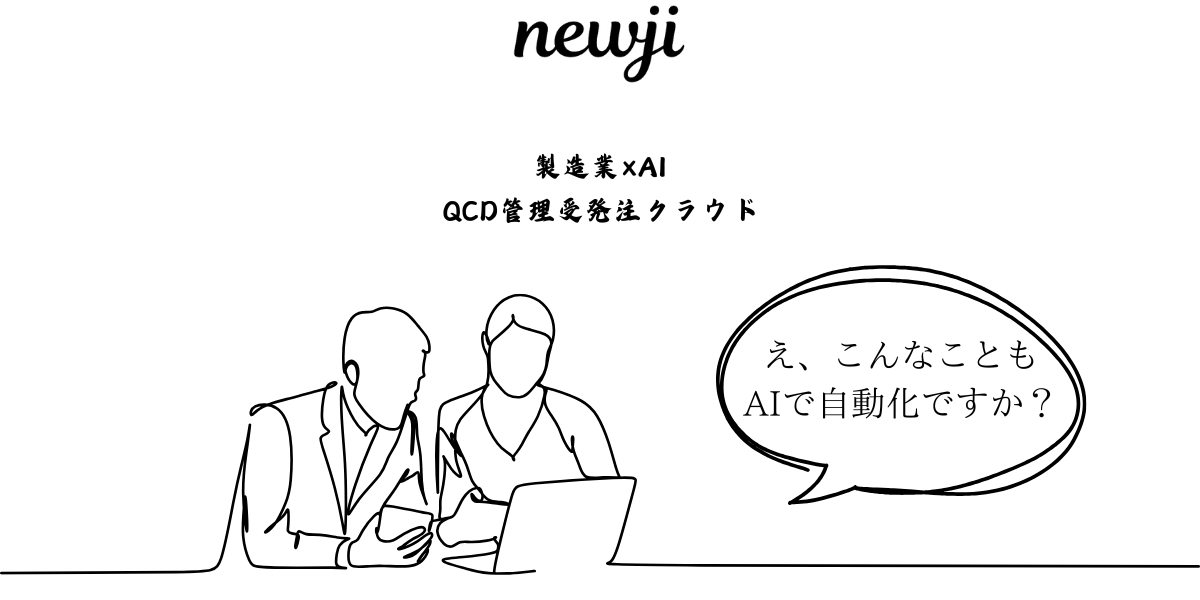
Optimal Purchasing Strategies and Technical Considerations for Aluminum Castings
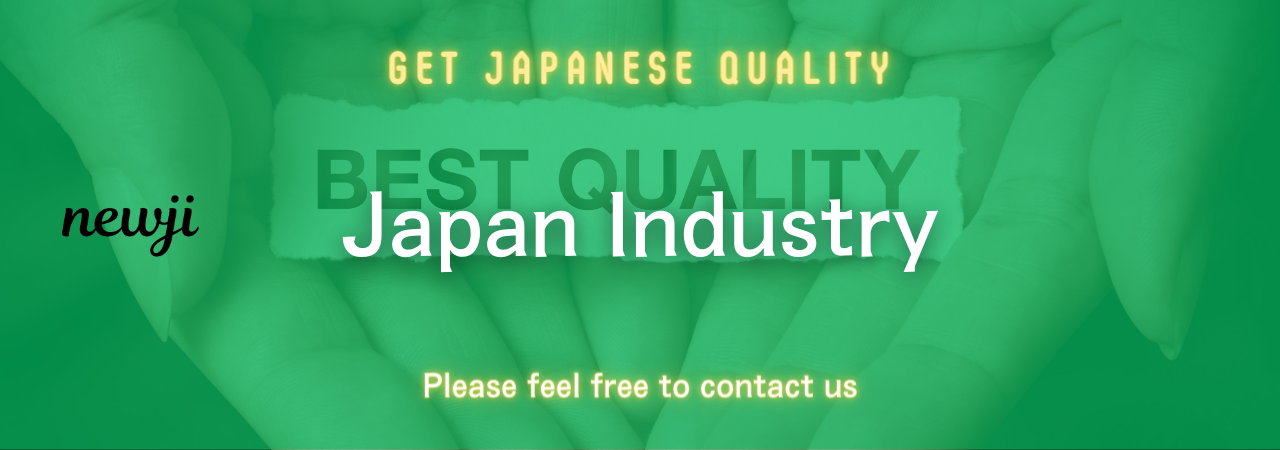
When embarking on a project that requires aluminum castings, understanding optimal purchasing strategies and technical considerations can prove invaluable.
Aluminum castings are utilized across various industries due to their lightweight nature, resistance to corrosion, and excellent strength-to-weight ratio.
By navigating the procurement process effectively, businesses can ensure they receive high-quality components that meet their specific needs.
目次
Understanding Aluminum Castings
Aluminum castings involve pouring molten aluminum into a mold to shape it into a desired form.
This process allows for intricate designs and complex geometries that would be difficult to achieve with other manufacturing methods.
Aluminum castings are widely used in automotive, aerospace, marine, and consumer electronics industries.
Types of Aluminum Casting Methods
There are several casting methods, each with distinct advantages:
Sand Casting
Sand casting utilizes a mold made of sand and is one of the oldest casting techniques.
While it is relatively less expensive, it is suitable for producing large, heavy parts with simple designs.
Die Casting
Die casting involves forcing molten aluminum into a steel mold under high pressure.
This method yields parts with excellent surface finishes and high dimensional accuracy, making it ideal for intricate and high-volume production.
Permanent Mold Casting
Permanent mold casting uses reusable molds typically made of steel.
It is suitable for medium to high-volume production and provides good mechanical properties and surface finishes.
Investment Casting
Investment casting involves creating a wax pattern coated with a ceramic shell that forms the mold.
After melting the wax, molten aluminum is poured into the mold.
This technique offers superior dimensional accuracy and is well-suited for complex designs.
Technical Considerations for Aluminum Castings
Alloy Selection
Selecting the right aluminum alloy is crucial as it impacts the mechanical properties, corrosion resistance, and machinability of the final product.
Commonly used alloys include A356, 6061, and 7075.
Understanding the requirements of your application will guide you in choosing the appropriate alloy.
Tolerances and Surface Finishes
Ensuring that the casting process can meet required tolerances and surface finishes is critical.
Die casting typically provides the best finishes, while sand casting may require additional machining.
Knowing your application’s tolerance and surface requirements will inform your choice of casting method.
Heat Treatment
Heat treatment can enhance the mechanical properties of aluminum castings.
Processes such as annealing, solution heat treatment, and precipitation hardening can be applied.
Consulting with a metallurgist to determine the best heat treatment process for your needs is advisable.
Design Considerations
Designing parts for casting involves understanding geometric constraints.
Incorporating features like draft angles to facilitate mold release, and avoiding sharp corners to reduce stress concentrations, can improve the casting’s integrity and manufacturability.
Optimal Purchasing Strategies
Supplier Selection
Choosing the right supplier is pivotal.
Evaluating potential suppliers based on their experience, quality control measures, and capacity to meet your volume needs is essential.
Requesting samples and visiting their facilities can provide insight into their capabilities.
Cost Considerations
Balancing cost with quality is crucial.
Obtaining multiple quotes, understanding the cost drivers such as alloy choice and casting method, and negotiating terms can help in achieving cost-effective procurement.
It’s also important to factor in post-casting processes such as machining and finishing when assessing overall costs.
Lead Time Management
Understanding lead times is vital for project planning.
Communicating your timeline needs and any potential fluctuations with the supplier can ensure that you receive your castings when necessary.
Establishing a clear production schedule and milestones can mitigate delays.
Quality Assurance
Implementing robust quality assurance measures is key.
Specifying inspection and testing requirements, such as X-ray inspection, dye penetration testing, and dimensional checks, ensures the castings meet your standards.
Collaborating with your supplier to establish quality control protocols can prevent defects and non-conformities.
Technological Advancements in Aluminum Castings
3D Printing and Rapid Prototyping
The integration of 3D printing and rapid prototyping in the casting process allows for quicker and more cost-effective production of prototypes and small-batch parts.
This technology can significantly reduce lead times and enhance design flexibility.
Advanced Simulation Software
Advanced simulation software aids in predicting and optimizing casting processes.
By simulating mold filling, solidification, and potential defect formation, engineers can refine designs and reduce trial-and-error iterations, resulting in higher-quality castings.
Automated Casting Systems
Automation in aluminum casting, such as robotic pouring and automated mold handling, can improve consistency and reduce human error.
These systems enhance production efficiency and the reliability of the castings produced.
Navigating the world of aluminum castings requires a strategic approach, understanding the various technical considerations, and leveraging the advancements in casting technology.
By selecting the right alloy, choosing the appropriate casting method, and implementing robust quality control, businesses can procure high-quality aluminum castings that meet their specific needs.
Furthermore, working closely with reliable suppliers and staying informed about industry advancements will contribute to the success of your projects utilizing aluminum castings.
資料ダウンロード
QCD管理受発注クラウド「newji」は、受発注部門で必要なQCD管理全てを備えた、現場特化型兼クラウド型の今世紀最高の受発注管理システムとなります。
ユーザー登録
受発注業務の効率化だけでなく、システムを導入することで、コスト削減や製品・資材のステータス可視化のほか、属人化していた受発注情報の共有化による内部不正防止や統制にも役立ちます。
NEWJI DX
製造業に特化したデジタルトランスフォーメーション(DX)の実現を目指す請負開発型のコンサルティングサービスです。AI、iPaaS、および先端の技術を駆使して、製造プロセスの効率化、業務効率化、チームワーク強化、コスト削減、品質向上を実現します。このサービスは、製造業の課題を深く理解し、それに対する最適なデジタルソリューションを提供することで、企業が持続的な成長とイノベーションを達成できるようサポートします。
製造業ニュース解説
製造業、主に購買・調達部門にお勤めの方々に向けた情報を配信しております。
新任の方やベテランの方、管理職を対象とした幅広いコンテンツをご用意しております。
お問い合わせ
コストダウンが利益に直結する術だと理解していても、なかなか前に進めることができない状況。そんな時は、newjiのコストダウン自動化機能で大きく利益貢献しよう!
(β版非公開)