- お役立ち記事
- Optimal solutions for manufacturing industries to realize environmentally friendly production
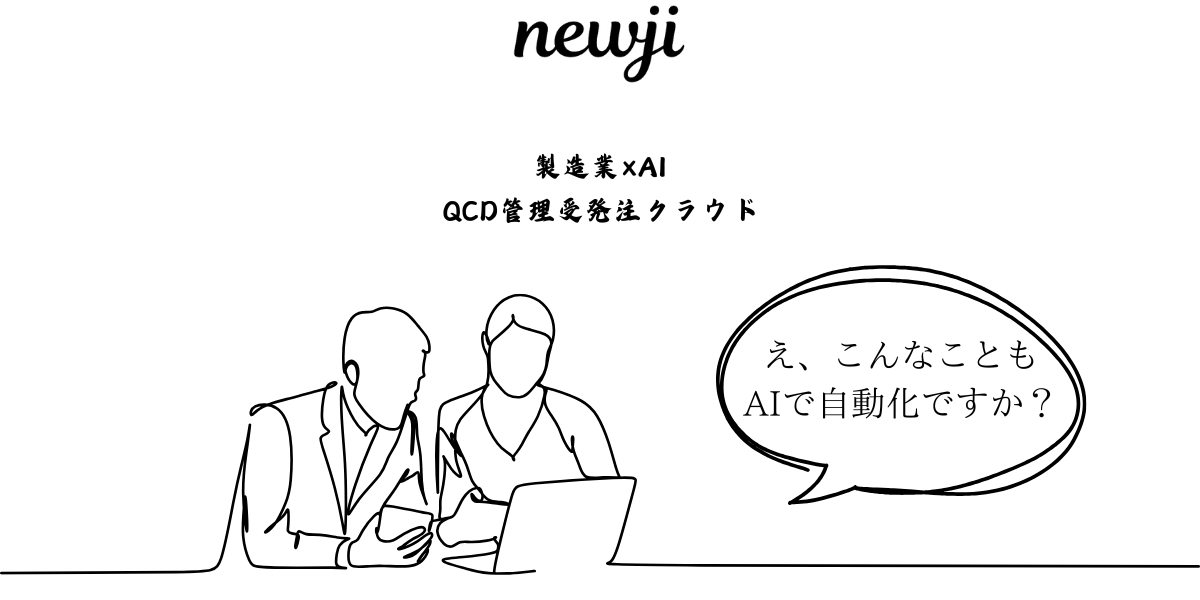
Optimal solutions for manufacturing industries to realize environmentally friendly production
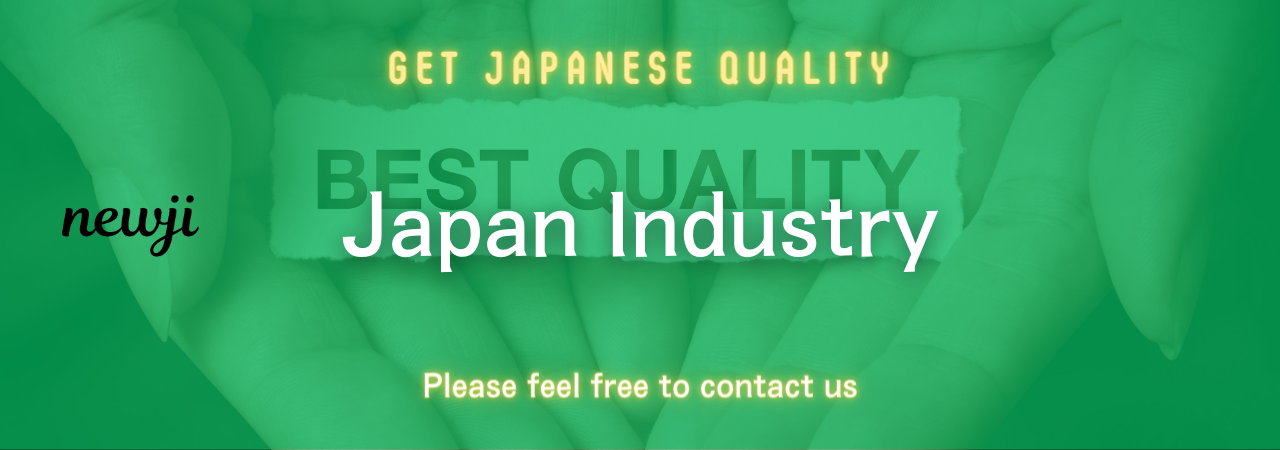
目次
Introduction to Environmentally Friendly Production
The manufacturing industry is pivotal to the global economy, providing jobs and essential materials worldwide.
However, one of the challenges it faces today is the need to reduce its environmental impact.
As industrial activities increase, so do concerns about pollution, resource depletion, and climate change.
Consumers and regulators are pushing for more sustainable practices.
This presents both a challenge and an opportunity for the manufacturing sector to adopt greener strategies.
Understanding Environmental Impact in Manufacturing
Before delving into solutions, it’s crucial to understand the primary environmental impacts of manufacturing.
These impacts include high energy consumption, waste production, emissions of greenhouse gases, and pollution of air and water resources.
The extensive use of raw materials leads to resource depletion and affects biodiversity.
Addressing these issues involves implementing significant changes at every stage of the manufacturing process, from sourcing raw materials to production, distribution, and product disposal.
The Role of Energy Efficiency
Energy efficiency is a fundamental aspect of reducing the environmental footprint in manufacturing.
Most industrial processes rely on significant energy inputs, often derived from fossil fuels, which contribute to greenhouse gas emissions.
To minimize these effects, manufacturers are investing in technology and practices that enhance energy efficiency.
This includes upgrading machinery to more energy-efficient models, incorporating renewable energy sources like wind and solar, and employing smarter energy management systems that reduce wastage.
For instance, process optimization through automation can lead to more predictable and stable energy requirements, decreasing overall consumption.
Minimizing Waste Production
A major component of environmentally friendly manufacturing is waste reduction.
Industries can implement a circular economy approach, where materials are reused, recycled, or repurposed instead of being discarded as waste.
This strategy not only conserves resources but also reduces the demand for raw material extraction.
Manufacturers can also optimize supply chain management to minimize waste during production.
This involves using lean manufacturing techniques to streamline operations, such as just-in-time production which reduces excess inventory and potential waste.
Furthermore, utilizing recycled materials in production processes can significantly lower the environmental impact.
Emission Reduction Strategies
Manufacturing is a significant contributor to emissions that affect air quality and contribute to climate change.
Addressing this requires an integrated approach to managing air pollutants and carbon emissions.
Technological innovations, such as cleaner production techniques and the use of more environmentally friendly inputs, can help reduce emissions.
Implementing advanced filtration technologies can also capture harmful particles before they are released into the environment.
Moreover, carbon capture and storage (CCS) technologies are becoming a viable solution for industries aiming to offset their carbon footprint.
Water and Resource Management
Water is another critical resource in the manufacturing industry.
Ensuring efficient water use can greatly enhance environmental sustainability efforts.
This involves reducing water consumption through process redesigns and reusing water where possible.
Implementing water treatment and recycling systems can help maintain water quality and availability.
Industries are also encouraged to adopt sustainable sourcing for raw materials.
By choosing biodegradable and non-toxic materials, manufacturers can reduce environmental harm.
An emphasis on renewable and responsibly sourced materials can pave the way for sustainable production processes.
The Role of Innovation and Technology
Innovation plays a crucial role in achieving environmentally friendly manufacturing.
Investing in research and development can lead to new materials, processes, and technologies that are more sustainable.
Digitalization and Industry 4.0 technologies, such as the Internet of Things (IoT), big data, and artificial intelligence, allow for smarter decision-making and precise monitoring of manufacturing processes, enhancing efficiency and sustainability.
These technologies enable predictive maintenance, which reduces unexpected downtimes and machine wear, thus lowering energy and material use.
Employee Training and Engagement
While technology and innovation are vital, the human element plays an essential role in transforming manufacturing practices.
Training employees in sustainable practices ensures that environmental initiatives are effectively implemented.
Encouraging a culture of sustainability within organizations can motivate employees to contribute creatively to green goals.
Incorporating sustainability into corporate strategies and involving employees at all levels instigates accountable practices throughout the organization.
Engaged and informed employees are more likely to identify and implement improvements in everyday operations.
Regulatory Compliance and Partnerships
Regulatory frameworks around the world are becoming more stringent in demanding sustainable practices from manufacturers.
Compliance with these regulations is not only mandatory but also beneficial in establishing credibility and trust with stakeholders and consumers.
Proactively aligning with international standards such as ISO 14001 for environmental management systems enhances operational sustainability.
Additionally, forming partnerships with other businesses, government bodies, and non-governmental organizations (NGOs) can accelerate the transition to more sustainable manufacturing.
Collaborations can lead to shared technologies, resources, and infrastructure that support environmental objectives.
Incentives and Financial Implications
There are financial incentives for manufacturers who adopt environmentally friendly practices.
Governments often offer tax breaks, subsidies, and grants for initiatives aimed at reducing greenhouse gases and improving sustainability.
Implementing these practices not only aligns with regulatory requirements but frequently results in cost savings through improved efficiency and reduced waste.
In conclusion, transitioning to environmentally friendly production involves a multifaceted approach.
It requires the commitment of resources to adopt new technologies, enhance efficiencies, reduce emissions, and engage employees.
When industries embrace an environmental mindset, they not only meet regulatory and consumer expectations but also contribute to a sustainable future for the planet.
資料ダウンロード
QCD調達購買管理クラウド「newji」は、調達購買部門で必要なQCD管理全てを備えた、現場特化型兼クラウド型の今世紀最高の購買管理システムとなります。
ユーザー登録
調達購買業務の効率化だけでなく、システムを導入することで、コスト削減や製品・資材のステータス可視化のほか、属人化していた購買情報の共有化による内部不正防止や統制にも役立ちます。
NEWJI DX
製造業に特化したデジタルトランスフォーメーション(DX)の実現を目指す請負開発型のコンサルティングサービスです。AI、iPaaS、および先端の技術を駆使して、製造プロセスの効率化、業務効率化、チームワーク強化、コスト削減、品質向上を実現します。このサービスは、製造業の課題を深く理解し、それに対する最適なデジタルソリューションを提供することで、企業が持続的な成長とイノベーションを達成できるようサポートします。
オンライン講座
製造業、主に購買・調達部門にお勤めの方々に向けた情報を配信しております。
新任の方やベテランの方、管理職を対象とした幅広いコンテンツをご用意しております。
お問い合わせ
コストダウンが利益に直結する術だと理解していても、なかなか前に進めることができない状況。そんな時は、newjiのコストダウン自動化機能で大きく利益貢献しよう!
(Β版非公開)