- お役立ち記事
- Optimal Tolerance Design and Cost Optimization for Machine Components
月間76,176名の
製造業ご担当者様が閲覧しています*
*2025年3月31日現在のGoogle Analyticsのデータより
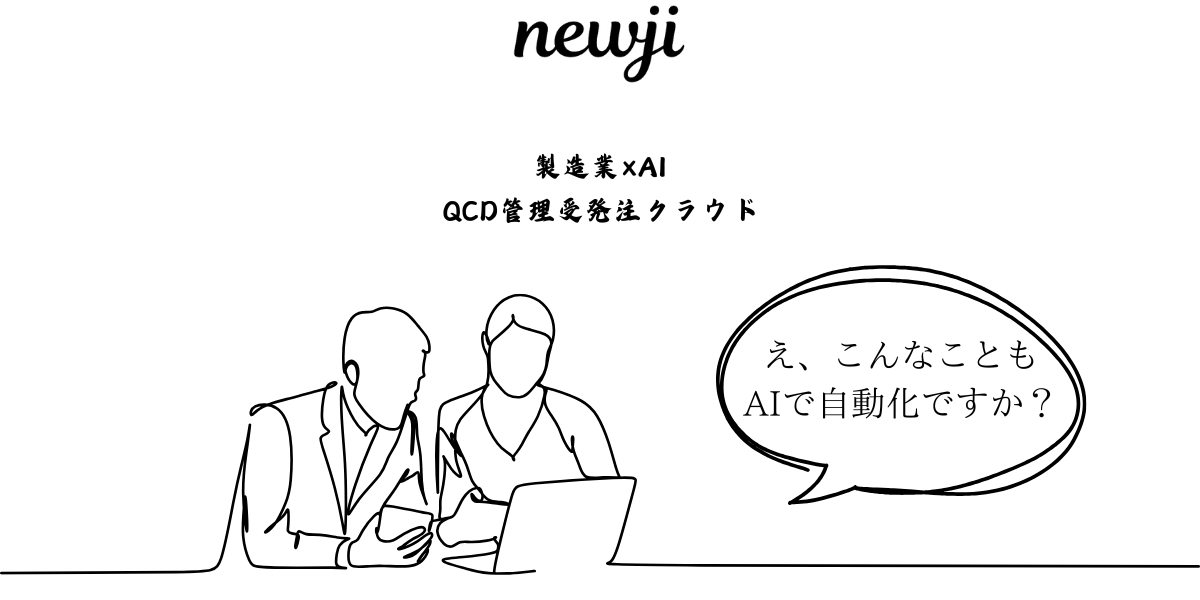
Optimal Tolerance Design and Cost Optimization for Machine Components
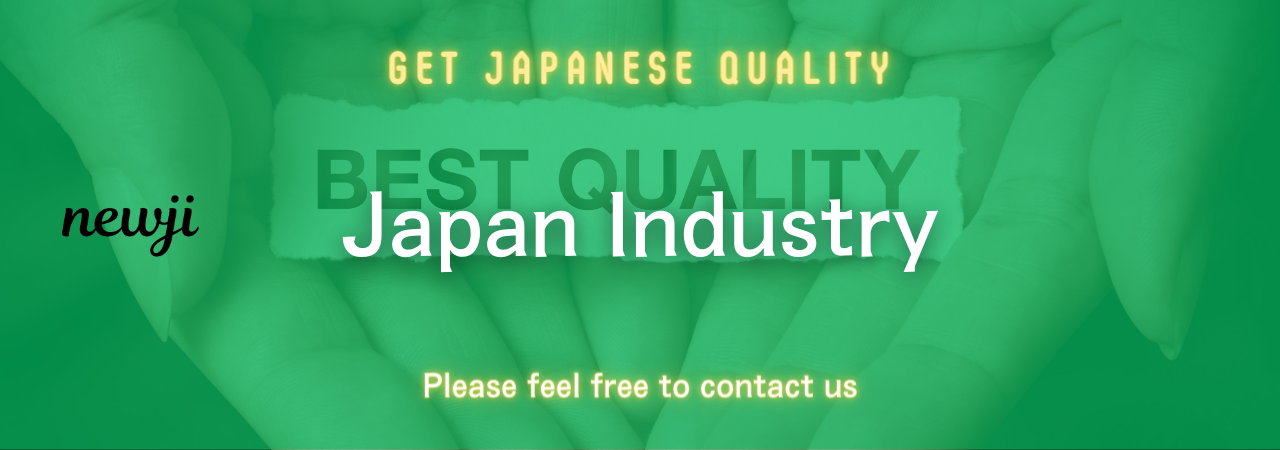
目次
Understanding Tolerance Design in Machine Components
Tolerance design is a crucial aspect when it comes to manufacturing machine components.
It refers to the allowable limits of variation in a physical dimension.
These variances ensure that parts will fit and function properly with one another when assembled.
Getting tolerance design right is fundamental to the performance and durability of machine components.
Tolerance can be thought of as the “room for error” allowed in the production of a part.
If the part is not within its specified tolerances, it may not fit properly with other components, resulting in performance issues or even system failure.
Thus, proper tolerance design not only guarantees the functionality and reliability of the components but also ensures cost-effectiveness in production and maintenance.
The Importance of Optimal Tolerance Design
Optimal tolerance design plays a critical role in achieving product quality and reducing manufacturing costs.
When tolerances are too tight, manufacturing becomes more complicated and expensive.
It may require more precision, higher-quality materials, or additional time to produce.
On the other hand, overly loose tolerances may lead to parts that do not fit or function as desired, leading to potential failures and costly adjustments.
Therefore, it is essential to strike a balance between precision and cost.
Engineers must consider this balance to avoid costly over-specification without risking the quality and performance of the components.
This balance ensures that the necessary expenses are justified by increased component reliability and reduced production rework or scrap rates.
Techniques for Tolerance Design and Analysis
There are several techniques available for tolerance design and analysis.
These techniques help engineers predict how variations in individual component dimensions will affect an assembly’s overall performance.
Statistical Tolerance Analysis
Statistical tolerance analysis uses statistical methods to predict the variation of an assembly’s overall dimensions.
This approach helps in understanding how the variability in component manufacturing affects the final product.
Using statistical tolerance analysis, engineers can determine which parts significantly impact the assembly when there’s variation.
This allows for setting more reasonable tolerance limits that do not overly burden the manufacturing process.
Worst-Case Tolerance Analysis
Worst-case tolerance analysis is often employed when the highest levels of reliability and safety are required.
This method assumes that all part dimensions are at their tolerance limits simultaneously.
Although conservative and sometimes costly, this approach ensures that the assembly functions as intended under the most extreme conditions.
Monte Carlo Simulation
Monte Carlo simulations use random sampling techniques to model uncertainty in tolerance design.
This statistical approach can simulate numerous scenarios reflecting real-world variations in part dimensions.
Monte Carlo simulations are advantageous because they provide insights into how variations affect not only the dimensions but also the performance of the assembly.
This data aids in making informed decisions about where to allocate tighter tolerances economically.
Cost Optimization in Tolerance Design
Cost optimization in manufacturing is always a primary goal, and tolerance design directly influences production costs.
Cost optimization involves finding a balance between achieving the desired product quality while minimizing production costs.
Material Cost
The choice of material plays a significant role in tolerance design.
High-tolerance components often require high-quality materials, which are more expensive.
However, by wisely selecting materials that meet performance criteria without unnecessarily inflating costs, significant savings can be realized.
Manufacturing Process
The manufacturing process also impacts cost efficiency.
Different processes have different capabilities in achieving precise tolerances.
Selecting the most suitable and cost-effective manufacturing techniques is crucial.
For example, CNC machining provides excellent precision but might not be necessary for less critical components that can be produced through casting.
Choosing the right process helps keep costs in check while maintaining necessary quality levels.
Inspection and Quality Control
Managing inspection and quality control processes is another key aspect.
More strict tolerances mean more extensive inspection and testing, which can raise costs.
By implementing efficient inspection techniques and focusing on critical dimensions, costs can be managed effectively.
Strategies for Improving Tolerance Design and Cost Optimization
Implementing certain strategies can significantly improve the process of tolerance design and cost optimization.
Collaborative Design Approach
Engage cross-functional teams in the design process, including design engineers, production engineers, and quality assurance experts.
A collaborative approach ensures all perspective views are considered, leading to more feasible design solutions.
Utilizing Advanced Software Tools
Leverage advanced CAD and CAE tools that allow for detailed modeling and simulation.
These tools can aid in tolerance analysis and validation without the need for building costly prototypes.
Iterative Testing and Feedback Loop
Creating a feedback loop with a continuous test and iterate approach enables engineers to adjust and optimize the design, ensuring that tolerances are aligned with functional needs and cost objectives.
Conclusion
Optimal tolerance design and cost optimization are pivotal in manufacturing efficient and reliable machine components.
By understanding the balance between precision and cost, and utilizing effective analysis techniques, manufacturers can produce high-quality products while keeping expenses under control.
Through strategic planning, collaboration, and the use of advanced tools, companies can achieve their goals of improved product performance and operational efficiency.
資料ダウンロード
QCD管理受発注クラウド「newji」は、受発注部門で必要なQCD管理全てを備えた、現場特化型兼クラウド型の今世紀最高の受発注管理システムとなります。
ユーザー登録
受発注業務の効率化だけでなく、システムを導入することで、コスト削減や製品・資材のステータス可視化のほか、属人化していた受発注情報の共有化による内部不正防止や統制にも役立ちます。
NEWJI DX
製造業に特化したデジタルトランスフォーメーション(DX)の実現を目指す請負開発型のコンサルティングサービスです。AI、iPaaS、および先端の技術を駆使して、製造プロセスの効率化、業務効率化、チームワーク強化、コスト削減、品質向上を実現します。このサービスは、製造業の課題を深く理解し、それに対する最適なデジタルソリューションを提供することで、企業が持続的な成長とイノベーションを達成できるようサポートします。
製造業ニュース解説
製造業、主に購買・調達部門にお勤めの方々に向けた情報を配信しております。
新任の方やベテランの方、管理職を対象とした幅広いコンテンツをご用意しております。
お問い合わせ
コストダウンが利益に直結する術だと理解していても、なかなか前に進めることができない状況。そんな時は、newjiのコストダウン自動化機能で大きく利益貢献しよう!
(β版非公開)