- お役立ち記事
- Optimal Tool Selection and Processing Conditions for Hard and Brittle Materials
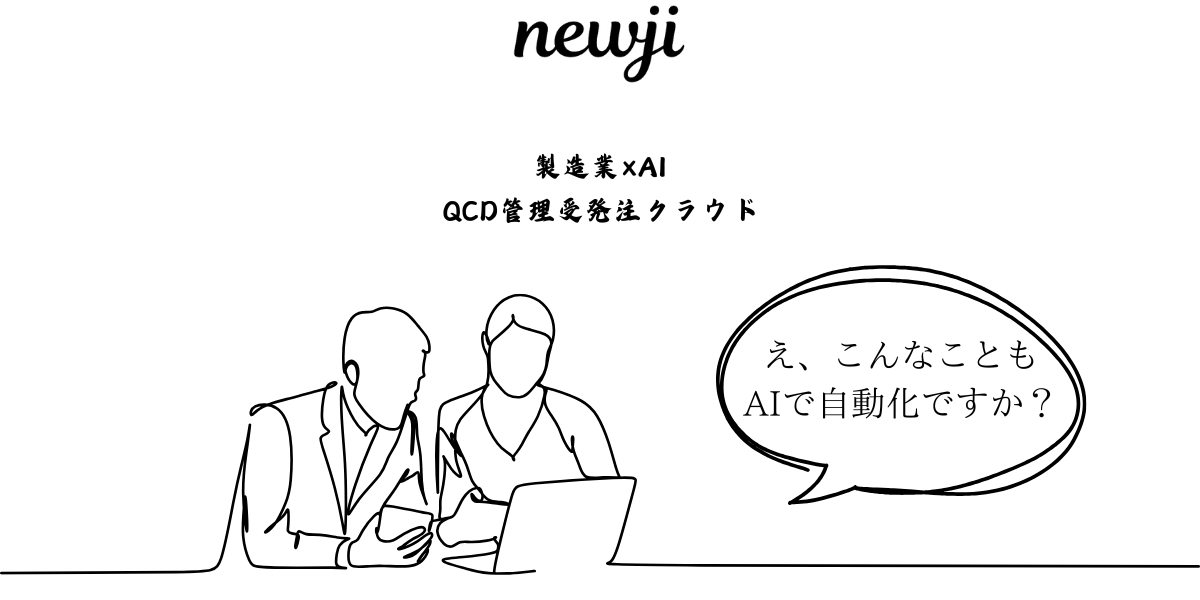
Optimal Tool Selection and Processing Conditions for Hard and Brittle Materials
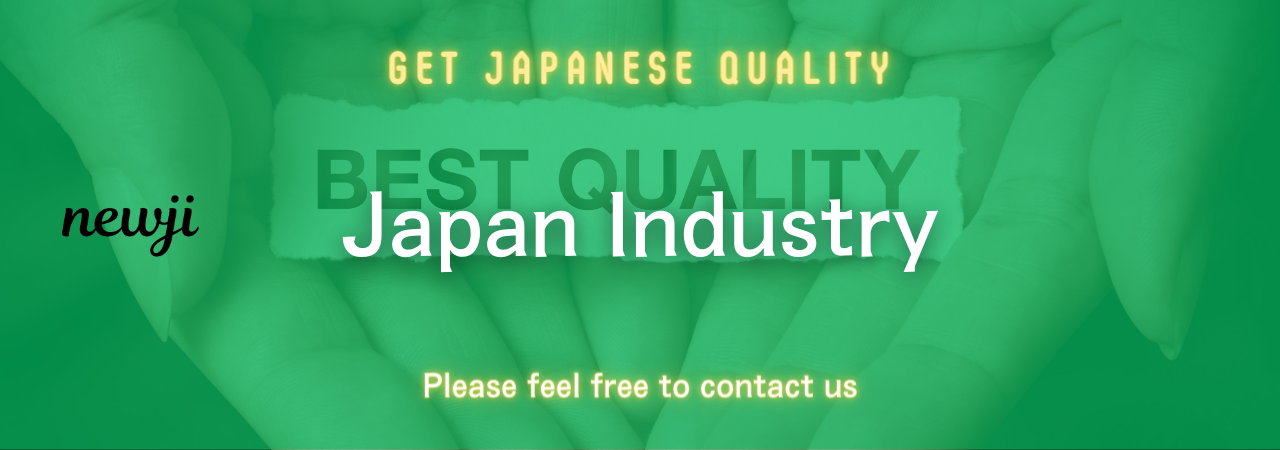
When it comes to machining hard and brittle materials, the right choice of tools and processing conditions is critical.
Hard and brittle materials, like ceramics, glass, and certain metals, present unique challenges in machining due to their tendencies to fracture easily.
This article will guide you through the optimal tools and processing conditions to achieve the best results.
目次
Understanding Hard and Brittle Materials
Characteristics of Hard and Brittle Materials
Hard and brittle materials possess high hardness levels and little to no plastic deformation.
Their high hardness means they resist wear and scratch well, making them ideal for demanding applications.
However, their brittleness makes them prone to cracking under stress, posing significant challenges during machining.
Common Hard and Brittle Materials
Some common examples of hard and brittle materials include:
– Ceramics (alumina, silicon carbide)
– Glass (borosilicate, soda-lime)
– Hardened metals (tungsten carbide, tool steels)
Understanding the properties of these materials helps in selecting the appropriate tools and processing conditions.
Choosing the Right Tools
Diamond Tools
Diamond tools are a top choice for machining hard and brittle materials due to their extreme hardness and wear resistance.
They provide excellent cutting performance and achieve high precision and surface finish.
Typical diamond tools include:
– Diamond-coated end mills
– Diamond grinding wheels
– Diamond-tipped cutting tools
CBN Tools
Cubic Boron Nitride (CBN) tools are another excellent option.
CBN is second only to diamond in hardness, making it suitable for machining ferrous hard materials like hardened steel.
CBN tools offer good wear resistance and thermal stability, which helps improve tool life and machining accuracy.
Carbide Tools
Carbide tools are cost-effective and effective for machining hard materials with less than extreme hardness.
They are suitable for applications that do not require the exceptional hardness of diamond or CBN tools.
Polycrystalline diamond (PCD) and polycrystalline cubic boron nitride (PCBN) inserts fall under this category and offer a balance between cost and performance.
Optimal Processing Conditions
Low Cutting Speed
Maintaining a low cutting speed is crucial when machining hard and brittle materials.
High cutting speeds can generate excessive heat, leading to thermal damage and potential cracking in the workpiece.
Using low speeds minimizes the risk of inducing thermal stresses and improves tool life.
Constant Tool Engagement
Ensuring constant tool engagement with the workpiece reduces the likelihood of sudden stress points that cause cracks.
Smooth and continuous cuts distribute the forces evenly, preventing localized stress concentrations.
Coolant Usage
Coolant plays a critical role in machining hard and brittle materials.
It helps in two key ways: reducing heat generation and flushing away debris from the cutting zone.
Water-based coolants are commonly used as they provide excellent thermal conductivity and help dissipate heat effectively.
Vibration Control
Minimizing vibration is essential for precision machining of hard and brittle materials.
Excessive vibrations can lead to poor surface finishes and potential fractures.
Using vibration-damping strategies, such as rigid machine setups and balanced tooling, can help achieve better results.
Advanced Techniques for Improved Machining
Ultrasonic Machining
Ultrasonic machining uses high-frequency vibrations to assist in the cutting process.
These vibrations help reduce cutting forces, lower heat generation, and improve surface finish.
Ultrasonic machining is particularly effective for delicate and intricate features in hard and brittle materials.
Laser-Assisted Machining
Laser-assisted machining involves using a laser to preheat the material before cutting.
The localized heating softens the material, reducing cutting forces and improving machinability.
This technique is beneficial for extremely hard materials that are challenging to machine conventionally.
Electrical Discharge Machining (EDM)
EDM uses electrical sparks to erode material from the workpiece.
It is highly effective for machining hard and brittle materials, especially those with complex shapes and fine details.
EDM provides excellent precision and surface finish, making it a popular choice for intricate components.
Conclusion
Machining hard and brittle materials requires careful consideration of tool selection and processing conditions.
Diamond, CBN, and carbide tools each offer distinct advantages, depending on the specific requirements.
Adopting optimal processing conditions, such as low cutting speeds, constant tool engagement, and effective coolant usage, helps achieve better results.
Advanced techniques like ultrasonic machining, laser-assisted machining, and EDM offer innovative solutions for handling the unique challenges posed by hard and brittle materials.
By understanding and applying these principles, you can optimize machining performance, enhance product quality, and extend tool life.
資料ダウンロード
QCD調達購買管理クラウド「newji」は、調達購買部門で必要なQCD管理全てを備えた、現場特化型兼クラウド型の今世紀最高の購買管理システムとなります。
ユーザー登録
調達購買業務の効率化だけでなく、システムを導入することで、コスト削減や製品・資材のステータス可視化のほか、属人化していた購買情報の共有化による内部不正防止や統制にも役立ちます。
NEWJI DX
製造業に特化したデジタルトランスフォーメーション(DX)の実現を目指す請負開発型のコンサルティングサービスです。AI、iPaaS、および先端の技術を駆使して、製造プロセスの効率化、業務効率化、チームワーク強化、コスト削減、品質向上を実現します。このサービスは、製造業の課題を深く理解し、それに対する最適なデジタルソリューションを提供することで、企業が持続的な成長とイノベーションを達成できるようサポートします。
オンライン講座
製造業、主に購買・調達部門にお勤めの方々に向けた情報を配信しております。
新任の方やベテランの方、管理職を対象とした幅広いコンテンツをご用意しております。
お問い合わせ
コストダウンが利益に直結する術だと理解していても、なかなか前に進めることができない状況。そんな時は、newjiのコストダウン自動化機能で大きく利益貢献しよう!
(Β版非公開)