- お役立ち記事
- Optimization and efficiency of assembly processes in manufacturing
月間76,176名の
製造業ご担当者様が閲覧しています*
*2025年3月31日現在のGoogle Analyticsのデータより
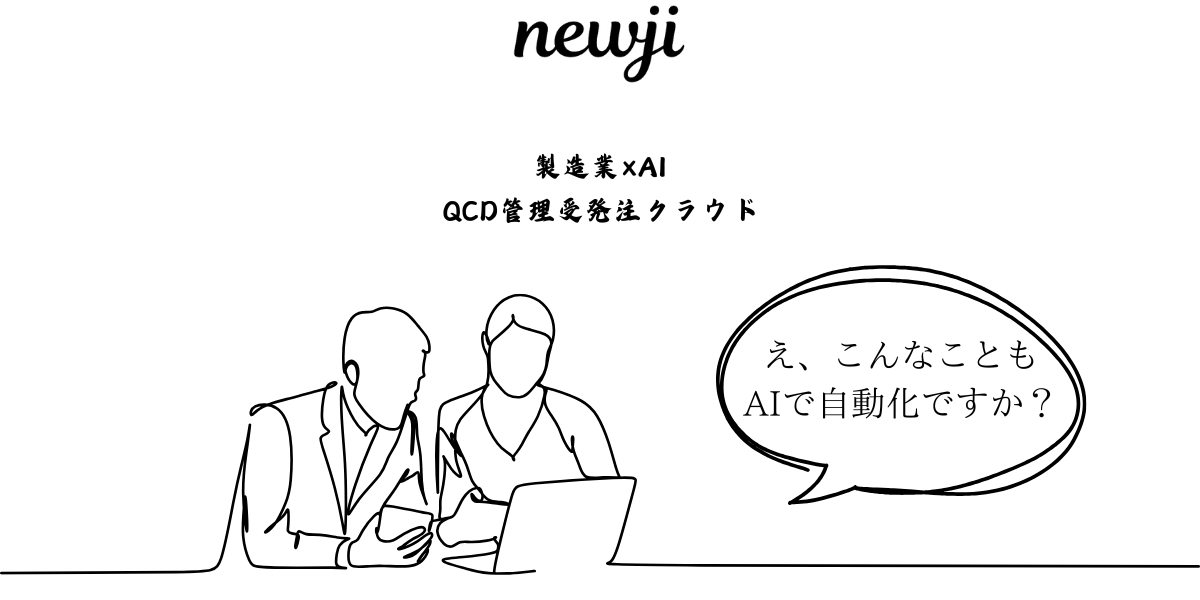
Optimization and efficiency of assembly processes in manufacturing
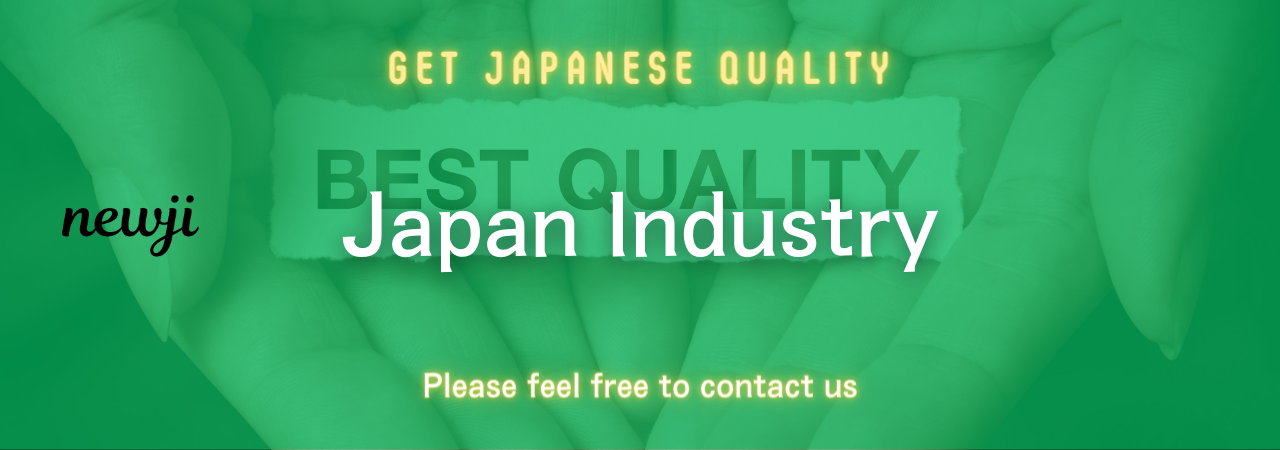
In the world of manufacturing, optimization and efficiency of assembly processes are crucial to maintaining competitiveness.
Producing high-quality products at a lower cost with faster throughput is the goal of any manufacturer.
In this article, we will explore various strategies and techniques to achieve these objectives.
From the use of automation to lean manufacturing principles, understanding these methods will help boost performance on the production floor.
目次
Understanding Assembly Process Optimization
Optimization of assembly processes involves improving each step to minimize time and resources while maximizing output.
This may include reconfiguring existing methods, integrating new technologies, and training staff more effectively.
The ultimate aim is to streamline operations and reduce inefficiencies.
Analyzing Current Processes
The first step in optimization is understanding the current processes.
Conducting a thorough analysis helps identify bottlenecks and areas where time and resources are wasted.
Detailed scrutiny of each process can uncover hidden issues that might not be apparent at first glance.
Using tools like Value Stream Mapping (VSM) can provide a visual representation of the flow of materials and information, helping pinpoint areas for improvement.
Setting Specific Goals
Once the analysis is complete, it is essential to set specific, measurable goals.
Whether aiming to reduce cycle time, cut costs, or improve quality, clear objectives provide direction for improvement efforts.
Goals should be realistic and achievable, yet challenging enough to drive significant enhancements.
Implementing Automation
Automation plays a critical role in optimizing assembly processes.
By incorporating advanced machinery and robotics, manufacturers can significantly increase speed and precision.
Automated systems can handle repetitive tasks more efficiently than human workers, reducing the risk of errors and improving consistency.
Types of Automation
There are several types of automation that can be implemented in manufacturing:
1. **Fixed Automation:** Best suited for high-volume production with little variation, such as assembly lines for automobiles.
2. **Programmable Automation:** Suitable for batch processes where the equipment must be reprogrammed for different tasks.
3. **Flexible Automation:** Ideal for environments where product design frequently changes, as it allows for quick adjustments.
Advantages of Automation
Using automation in manufacturing offers numerous benefits:
– **Increased Productivity:** Machines can operate continuously without breaks, leading to higher output.
– **Enhanced Precision:** Automation reduces human errors, ensuring product consistency and quality.
– **Cost Savings:** Though initial setup can be expensive, long-term savings are realized through reduced labor costs and increased efficiency.
Lean Manufacturing Techniques
Lean manufacturing principles focus on eliminating waste and improving workflow.
Originally developed by Toyota, these techniques are now widely adopted across various industries.
Five Key Principles
1. **Define Value:** Understand what the customer values in your product.
2. **Map the Value Stream:** Identify all steps in the process and eliminate those that don’t add value.
3. **Create Flow:** Ensure smooth progress from start to finish without interruptions.
4. **Establish Pull:** Manufacture based on customer demand to avoid overproduction.
5. **Pursue Perfection:** Continuously seek ways to improve processes.
Common Lean Tools
Several tools can help implement lean principles:
– **5S Methodology:** Organize the workspace for efficiency and effectiveness. The five steps are Sort, Set in order, Shine, Standardize, and Sustain.
– **Kaizen:** Continuous, incremental improvements involving all employees.
– **Kanban:** Visual scheduling system that controls the flow of materials and work.
Employee Training and Involvement
While technology and methodologies are crucial, human elements cannot be overlooked.
Training employees in new processes and involving them in the optimization journey can lead to significant improvements.
Engaged and knowledgeable staff are more likely to identify and solve problems quickly.
Training Programs
Well-structured training programs can bring employees up to speed with new technologies and processes.
Regular workshops, online courses, and hands-on training can be effective.
Encouraging cross-training, where employees learn different roles, creates a more flexible and resilient workforce.
Encouraging Participation
Involving employees in decision-making processes fosters a sense of ownership and accountability.
Employees on the front lines often have valuable insights into potential improvements.
Regular meetings and feedback sessions can create a collaborative environment where everyone works towards common goals.
Continuous Monitoring and Improvement
Optimization is not a one-time effort.
Continuous monitoring and periodic assessments are essential to sustain gains and identify new opportunities for improvement.
Using Key Performance Indicators (KPIs) helps track progress and measure the effectiveness of implemented changes.
Regular Audits
Conducting regular audits of the assembly process ensures that standards are maintained.
Audits can help uncover deviations from established procedures, allowing for corrective actions to be taken promptly.
Adapting to Change
The manufacturing landscape is constantly evolving with new technologies and market demands.
Being adaptable and responsive to changes ensures that your processes remain optimized.
Staying updated with industry trends and being open to new approaches can provide a competitive edge.
In conclusion, achieving optimization and efficiency in assembly processes is a multifaceted endeavor involving a thorough analysis of current practices, the integration of automation, adherence to lean manufacturing principles, and ongoing employee engagement and training.
By setting clear goals and continuously seeking ways to improve, manufacturers can enhance productivity, reduce costs, and ensure high-quality outputs.
Keeping pace with technological advancements and adapting to change will further solidify the foundations for a successful and efficient manufacturing operation.
資料ダウンロード
QCD管理受発注クラウド「newji」は、受発注部門で必要なQCD管理全てを備えた、現場特化型兼クラウド型の今世紀最高の受発注管理システムとなります。
ユーザー登録
受発注業務の効率化だけでなく、システムを導入することで、コスト削減や製品・資材のステータス可視化のほか、属人化していた受発注情報の共有化による内部不正防止や統制にも役立ちます。
NEWJI DX
製造業に特化したデジタルトランスフォーメーション(DX)の実現を目指す請負開発型のコンサルティングサービスです。AI、iPaaS、および先端の技術を駆使して、製造プロセスの効率化、業務効率化、チームワーク強化、コスト削減、品質向上を実現します。このサービスは、製造業の課題を深く理解し、それに対する最適なデジタルソリューションを提供することで、企業が持続的な成長とイノベーションを達成できるようサポートします。
製造業ニュース解説
製造業、主に購買・調達部門にお勤めの方々に向けた情報を配信しております。
新任の方やベテランの方、管理職を対象とした幅広いコンテンツをご用意しております。
お問い合わせ
コストダウンが利益に直結する術だと理解していても、なかなか前に進めることができない状況。そんな時は、newjiのコストダウン自動化機能で大きく利益貢献しよう!
(β版非公開)