- お役立ち記事
- Optimization and introduction of new technology in the production process of ceramic products
月間77,185名の
製造業ご担当者様が閲覧しています*
*2025年2月28日現在のGoogle Analyticsのデータより
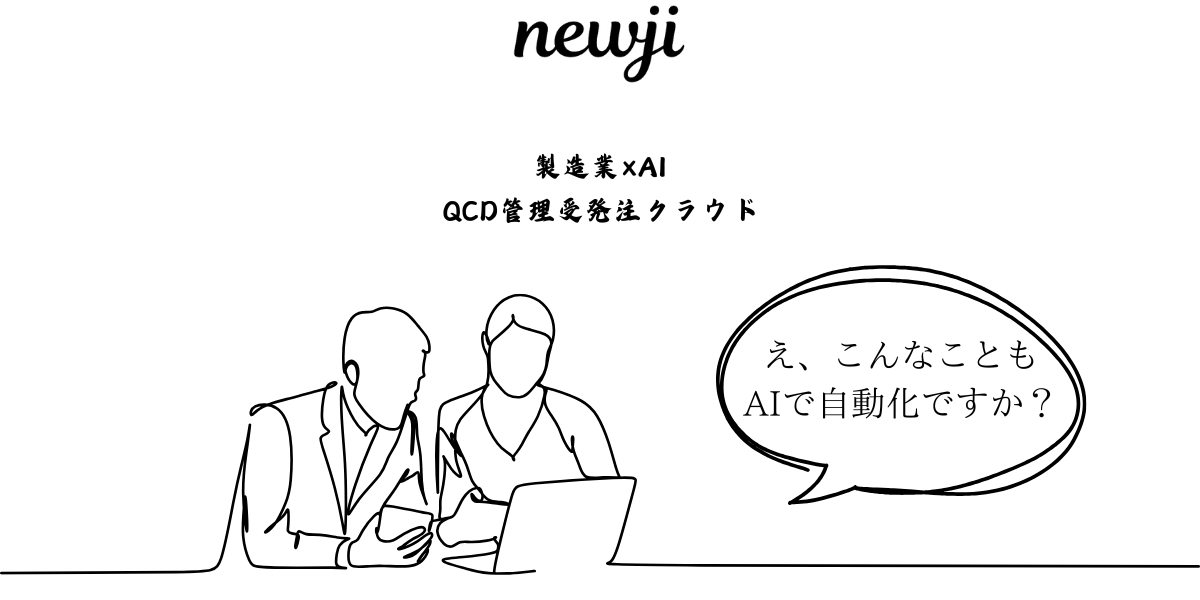
Optimization and introduction of new technology in the production process of ceramic products
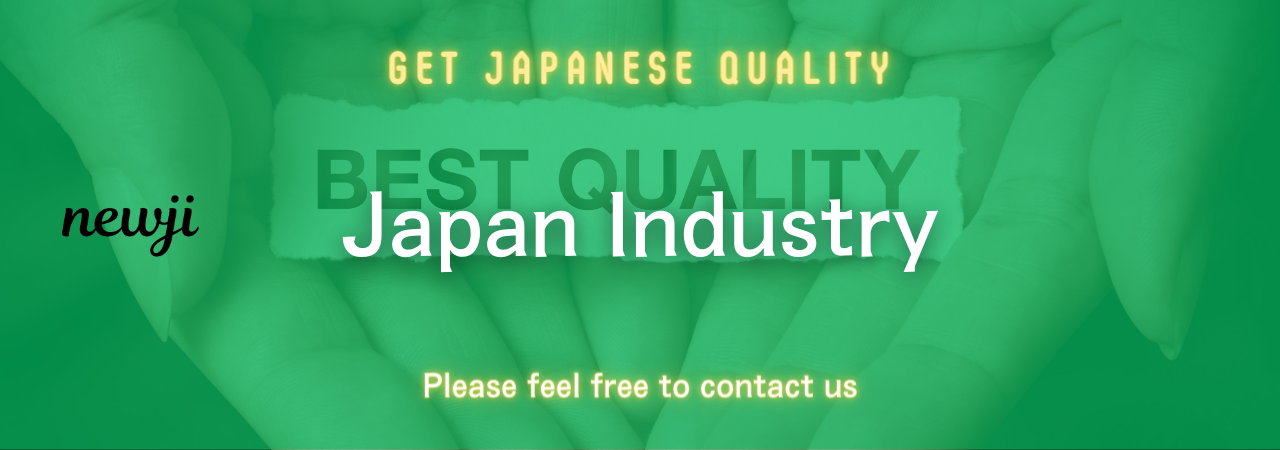
目次
Introduction to Ceramic Production
Ceramic products have been a part of human culture for thousands of years, offering durability, versatility, and decorative richness.
From ancient pottery to modern-day tiles and electronic components, ceramics continue to play a vital role in various industries.
The production process of ceramic products, however, can be quite complex.
It involves several stages, including raw material preparation, shaping, drying, and firing.
Each step is crucial and requires precision to ensure the final product’s quality.
With the advent of new technology, manufacturers now have the opportunity to optimize their production processes, leading to increased efficiency and reduced costs.
Technological Innovations in Ceramic Manufacturing
The introduction of new technologies in ceramic production has revolutionized the way these products are manufactured.
One of the most significant innovations is the use of automated machinery and robotics.
Automated systems have significantly improved the accuracy and speed of shaping, glazing, and firing processes.
Robots are particularly beneficial in handling repetitive tasks, reducing human error, and enhancing safety in the workplace.
Another critical technological advancement is the deployment of 3D printing in ceramic production.
3D printing has enabled manufacturers to create intricate designs with ease, allowing for greater customization and innovation.
This technology reduces material waste and shortens the time required to bring new products to market.
Raw Material Optimization
Before any shaping or firing can occur, raw materials must be carefully selected and prepared.
New technologies have made it possible to optimize the composition of raw materials, enhancing the quality and properties of finished ceramic products.
Advanced analytical tools allow manufacturers to perform detailed assessments of raw materials, ensuring that only the best are used in production.
Using software for material composition analysis, manufacturers can experiment with different formulas to achieve the desired product characteristics.
These tools can also predict how materials will behave during firing, reducing the risk of defects and improving overall product quality.
Enhancing the Drying and Firing Stages
Drying and firing are crucial stages in ceramic production, where the shaped clay is transformed into a hard, finished product.
The introduction of controlled drying environments and advanced kiln technologies has significantly improved these processes.
Modern kilns are equipped with sensors and computer control systems that provide precise temperature regulation.
This ensures that each ceramic item is fired under optimal conditions, reducing energy consumption and minimizing the risk of defects.
In addition, enhanced drying technologies use controlled humidity and temperature environments to prevent cracking and warping.
These innovations shorten drying times and increase the uniformity of the final product, resulting in high-quality ceramics.
Leveraging Data Analytics for Process Optimization
Data analytics is another powerful tool that manufacturers are using to optimize their ceramic production processes.
By collecting and analyzing data from various stages of production, manufacturers can identify inefficiencies, predict potential issues, and implement corrective measures.
Data-driven insights enable businesses to track production metrics such as energy usage, material waste, and production time.
With this information, manufacturers can make informed decisions about where to focus their efforts for process improvement.
Predictive maintenance is another area where data analytics offers significant benefits.
By monitoring the performance of machinery and predicting when maintenance is required, manufacturers can prevent unforeseen breakdowns, reducing downtime and enhancing productivity.
Embracing Eco-friendly Practices
Sustainability is increasingly important in modern manufacturing.
Ceramic producers are adopting eco-friendly practices to minimize their environmental impact.
Advanced technologies allow manufacturers to use less energy and reduce emissions during the firing process.
For instance, innovative kiln designs recover and reuse heat, leading to significant energy savings.
Water conservation technologies are also being implemented, recycling water used during production and minimizing pollution.
The use of eco-friendly glazes and coatings further reduces the environmental footprint of ceramic products.
Conclusion
The optimization and introduction of new technology in the production process of ceramic products are transforming the industry.
From automated machinery and 3D printing to data analytics and eco-friendly practices, these innovations lead to enhanced efficiency, reduced costs, and superior product quality.
As the industry continues to evolve, manufacturers that embrace these advancements will stay competitive and responsive to market demands.
By leveraging technology, ceramic producers can continue to meet the needs of consumers while promoting sustainable and efficient production practices.
資料ダウンロード
QCD管理受発注クラウド「newji」は、受発注部門で必要なQCD管理全てを備えた、現場特化型兼クラウド型の今世紀最高の受発注管理システムとなります。
ユーザー登録
受発注業務の効率化だけでなく、システムを導入することで、コスト削減や製品・資材のステータス可視化のほか、属人化していた受発注情報の共有化による内部不正防止や統制にも役立ちます。
NEWJI DX
製造業に特化したデジタルトランスフォーメーション(DX)の実現を目指す請負開発型のコンサルティングサービスです。AI、iPaaS、および先端の技術を駆使して、製造プロセスの効率化、業務効率化、チームワーク強化、コスト削減、品質向上を実現します。このサービスは、製造業の課題を深く理解し、それに対する最適なデジタルソリューションを提供することで、企業が持続的な成長とイノベーションを達成できるようサポートします。
製造業ニュース解説
製造業、主に購買・調達部門にお勤めの方々に向けた情報を配信しております。
新任の方やベテランの方、管理職を対象とした幅広いコンテンツをご用意しております。
お問い合わせ
コストダウンが利益に直結する術だと理解していても、なかなか前に進めることができない状況。そんな時は、newjiのコストダウン自動化機能で大きく利益貢献しよう!
(β版非公開)