- お役立ち記事
- Optimization and Maintenance of Rolling Mills in Steel Factories
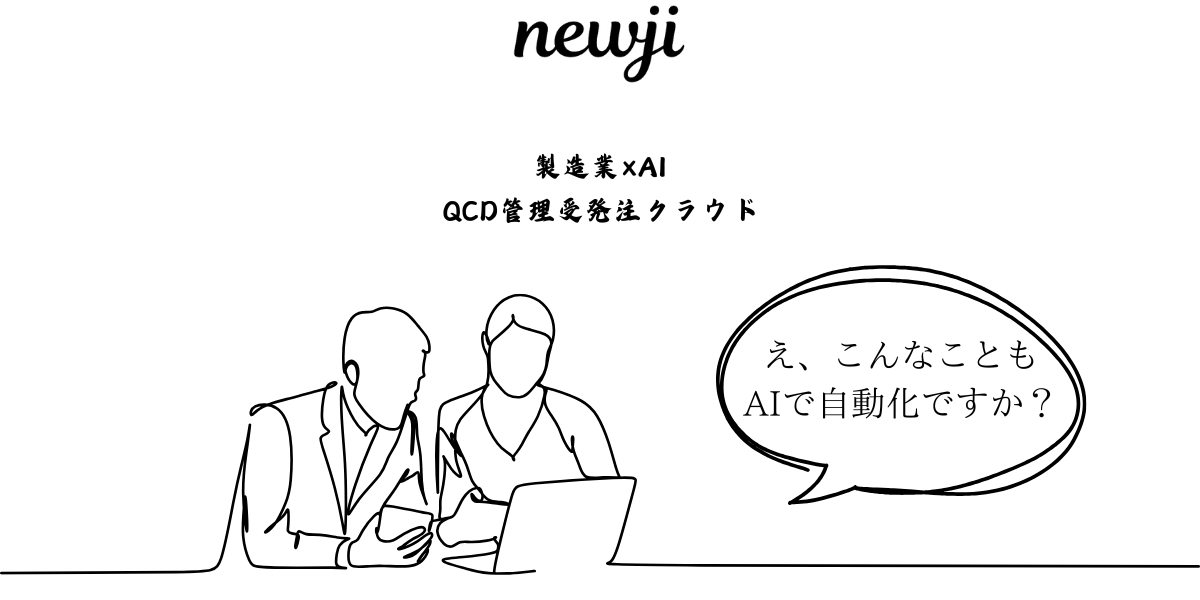
Optimization and Maintenance of Rolling Mills in Steel Factories
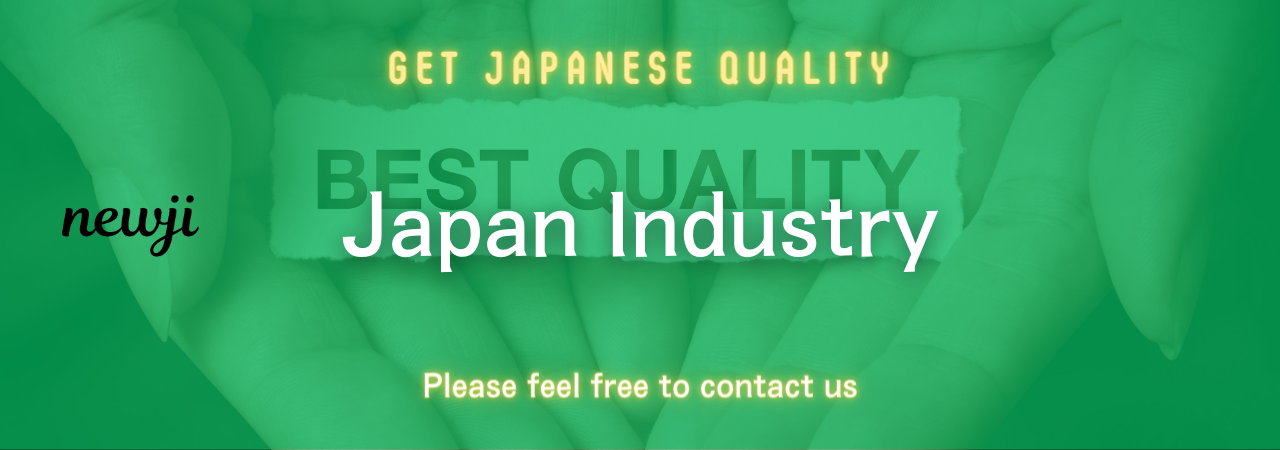
目次
Introduction to Rolling Mills
Rolling mills are crucial components in steel factories, serving as essential tools for shaping and forming metals into desired sizes and finishes.
These machines play a pivotal role in the production process, transforming raw steel into usable products such as sheets, bars, and wires through a series of mechanical operations.
Understanding the importance of optimizing and maintaining these mills is vital for enhancing productivity, ensuring quality, and minimizing downtime.
Why Optimization is Important
Optimization of rolling mills focuses on improving their efficiency and output.
Efficient operation means producing the maximum amount of product with the least amount of resources and time.
By optimizing these machines, steel factories can reduce energy consumption, increase throughput, and maintain consistent product quality.
One aspect of optimization includes the precise control of rolling temperatures, speed, and pressures.
Proper adjustments in these parameters can prevent defects such as warping or cracking, which can lead to costly rework or waste.
Additionally, efficient roll ‘pass’ designs can help in minimizing the material loss, thus optimizing the yield.
Cost Reduction and Energy Efficiency
In the competitive field of steel manufacturing, reducing costs is crucial.
Optimization helps in lowering operational costs by enhancing energy efficiency.
Advanced technologies and practices, like using variable frequency drives and efficient motor controls, can significantly cut down energy consumption in rolling mills.
Implementing predictive maintenance strategies further aids in anticipating equipment failures before they occur, thus saving on repair costs and preventing downtime.
The use of data analytics and IoT can be instrumental in predicting wear and tear on parts, allowing for timely maintenance and replacing worn components before they cause major disruptions.
Methods of Rolling Mill Optimization
Several techniques can be employed to optimize rolling mills. One effective method is process automation.
Integrating automation systems allows for precise control over the rolling process, reducing the likelihood of human error and increasing repeatability.
Additionally, employing computer modeling and simulation can aid in trialing new processes virtually, allowing for improvements without disrupting actual production.
This can lead to enhanced roll pass designs and better roll sequencing.
Advanced Materials and Technologies
The introduction of advanced materials for rolls, such as high-chromium alloys, can provide longer roll life, reducing the frequency of roll changes and downtime.
Innovative technologies like laser and ultrasonic measurement tools can offer real-time quality control, ensuring that products meet stringent specifications throughout the production process.
Furthermore, the integration of machine learning and artificial intelligence can lead to smarter systems capable of self-optimization.
These technologies can analyze vast amounts of data to suggest process enhancements, leading to continuously improving operations.
Maintenance Practices for Rolling Mills
Regular maintenance of rolling mills is essential for avoiding unexpected breakdowns and maintaining optimum performance.
This involves a proactive approach, focusing on both routine and predictive maintenance strategies.
Routine Maintenance
Routine maintenance includes regular checks and servicing of essential components such as bearings, gears, and rolls.
It involves lubrication, tightening, and adjustment of moving parts to ensure smooth operation.
Scheduled inspections can detect early signs of wear or damage, thus preventing extensive damage and potential failure.
Cleaning is another crucial aspect, as accumulated debris can lead to overheating and increased wear.
Ensuring that cooling systems are functioning correctly also helps in maintaining the integrity of the equipment.
Predictive Maintenance
Predictive maintenance leverages modern technology to anticipate problems before they manifest fully.
This approach uses sensors and IoT devices to continuously monitor equipment conditions.
Vibration analysis, oil analysis, and thermography are used to detect anomalies well in advance.
Software solutions collecting and analyzing data can alert maintenance teams to potential issues, allowing for timely intervention.
This predictive capability can significantly extend the lifespan of equipment and improve overall plant efficiency.
Challenges in Optimization and Maintenance
Implementing and maintaining optimized processes is not without its challenges.
Factors such as the high initial cost of advanced technologies and the need for skilled personnel can be barriers.
Companies must weigh the long-term benefits of optimization against the upfront investments.
Complex integration of new technology with existing setups may also require extensive training for the workforce, but this investment can pay off in improved skills and process understanding.
Furthermore, balancing production demands with maintenance schedules requires careful planning to avoid unnecessary production delays.
Effective communication and coordination are essential in ensuring that maintenance activities are conducted efficiently without impacting output adversely.
Conclusion
Optimization and maintenance of rolling mills in steel factories are critical for sustaining efficient and profitable operations.
By adopting advanced technologies and thorough maintenance practices, steel producers can ensure high-quality production, enhance their competitiveness, and reduce operational costs.
With continuous advancements in technology and a strong focus on predictive maintenance, the future of rolling mills looks promising, offering new opportunities for innovation and efficiency in the steel industry.
資料ダウンロード
QCD調達購買管理クラウド「newji」は、調達購買部門で必要なQCD管理全てを備えた、現場特化型兼クラウド型の今世紀最高の購買管理システムとなります。
ユーザー登録
調達購買業務の効率化だけでなく、システムを導入することで、コスト削減や製品・資材のステータス可視化のほか、属人化していた購買情報の共有化による内部不正防止や統制にも役立ちます。
NEWJI DX
製造業に特化したデジタルトランスフォーメーション(DX)の実現を目指す請負開発型のコンサルティングサービスです。AI、iPaaS、および先端の技術を駆使して、製造プロセスの効率化、業務効率化、チームワーク強化、コスト削減、品質向上を実現します。このサービスは、製造業の課題を深く理解し、それに対する最適なデジタルソリューションを提供することで、企業が持続的な成長とイノベーションを達成できるようサポートします。
オンライン講座
製造業、主に購買・調達部門にお勤めの方々に向けた情報を配信しております。
新任の方やベテランの方、管理職を対象とした幅広いコンテンツをご用意しております。
お問い合わせ
コストダウンが利益に直結する術だと理解していても、なかなか前に進めることができない状況。そんな時は、newjiのコストダウン自動化機能で大きく利益貢献しよう!
(Β版非公開)