- お役立ち記事
- Optimization and partnership of bevel tooth grinding technology for aircraft engine gear parts
月間77,185名の
製造業ご担当者様が閲覧しています*
*2025年2月28日現在のGoogle Analyticsのデータより
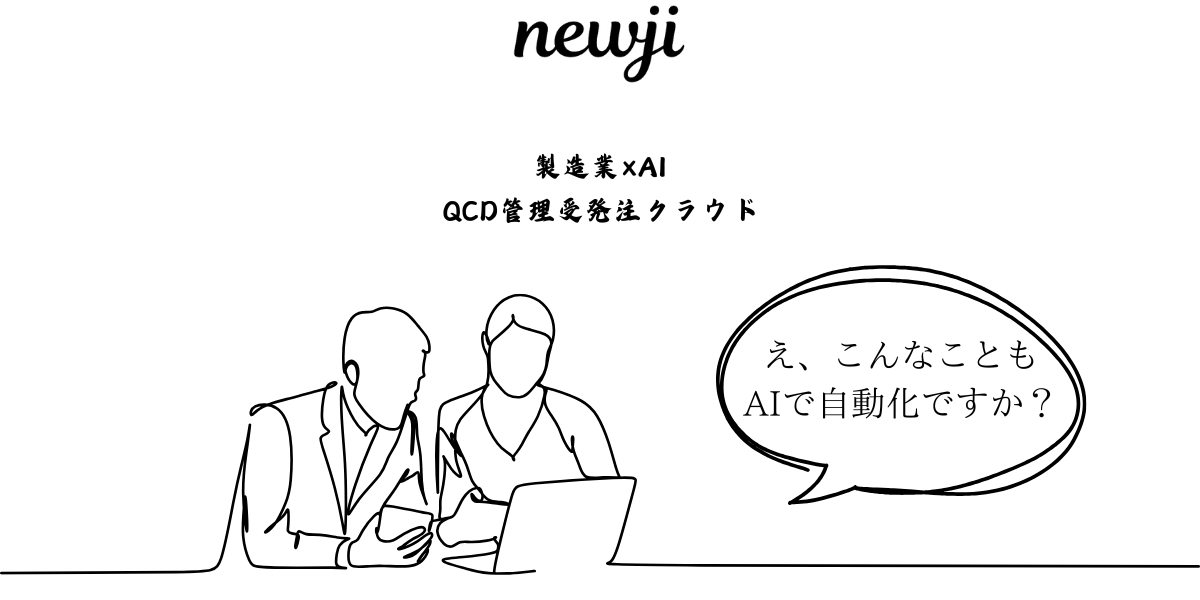
Optimization and partnership of bevel tooth grinding technology for aircraft engine gear parts
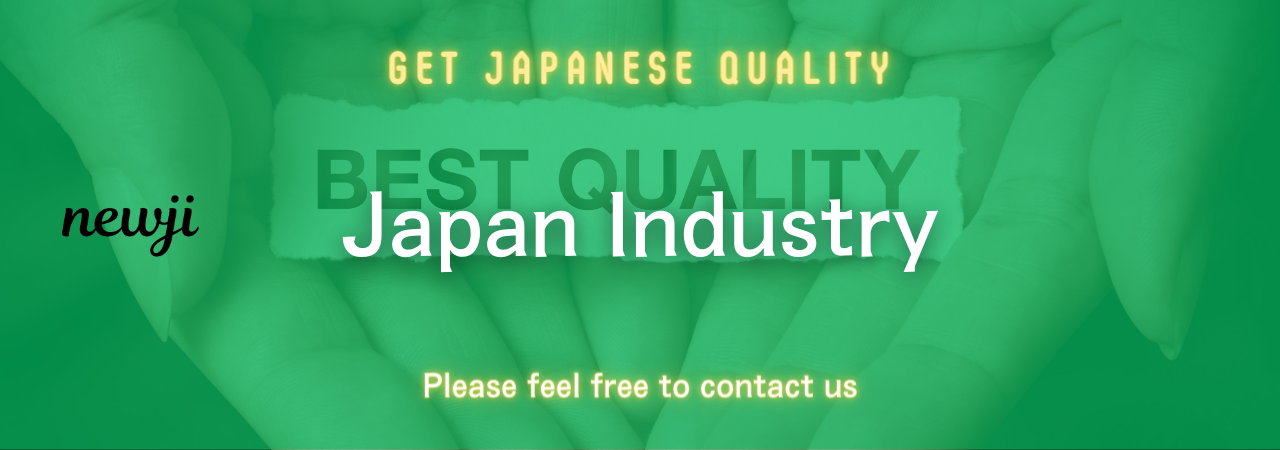
目次
Understanding Bevel Tooth Grinding Technology
Bevel tooth grinding technology is an advanced method used in the production of precisely machined gear parts, which are essential in various industrial applications, including aircraft engines.
It involves removing material from a gear with a beveled edge in order to achieve the desired shape and finish.
This technology is crucial for ensuring that gear parts have the required strength, efficiency, and durability necessary for high-performance engines.
The primary goal of bevel tooth grinding technology is to produce gears that meet stringent quality requirements.
These requirements include tight tolerances, smooth surfaces, and precise dimensions.
This is particularly important in the aerospace industry, where the reliability and safety of engine components are paramount.
The Importance of Optimization
Optimization in bevel tooth grinding involves modifying and adjusting the grinding process to achieve the best possible results.
This includes improving efficiency, reducing production time, and minimizing waste.
Optimization ensures that each gear part produced is of the highest quality while maintaining cost-effectiveness.
Additionally, optimization helps in reducing wear and tear on grinding equipment, resulting in longer equipment life and reduced maintenance costs.
This benefits manufacturers by improving production uptime and reducing operational costs over time.
One of the primary methods of optimizing bevel tooth grinding is through the implementation of advanced simulation software and automated processes.
These tools enable manufacturers to carefully plan, simulate, and tweak the grinding process before actual production commences.
Simulation Software
Simulation software plays a vital role in optimizing bevel tooth grinding processes.
Before actual machining occurs, engineers can use the software to model and simulate the grinding process, identifying potential issues and areas for improvement.
This preemptive analysis allows for fine-tuning the process to eliminate inefficiencies and to ensure the highest possible quality of the finished product.
Through simulation, manufacturers can test different grinding parameters, including speed, feed rate, and grinding wheel characteristics, without stopping production.
This leads to a more agile manufacturing process that can quickly adapt to new demands or changes in production requirements.
Automated Processes
Automation is another crucial component in optimizing bevel tooth grinding technology.
By employing automated systems, manufacturers can ensure consistent quality across all produced gear parts.
Automated grinding machines can operate with higher precision than manual methods, resulting in reduced defects and increased production efficiency.
Machines equipped with sensors and control systems can monitor grinding processes in real-time, making adjustments as needed to ensure optimal performance.
This real-time monitoring helps prevent costly mistakes and ensures that production goals are consistently met.
Partnership for Enhanced Grinding Technology
The partnership between equipment manufacturers, software developers, and aerospace companies is essential for advancing bevel tooth grinding technology.
Collaboration between these entities can lead to significant improvements in gear manufacturing processes and the components they produce for aircraft engines.
Equipment Manufacturers
Manufacturers of grinding equipment collaborate with aerospace companies to design machines capable of meeting the specific needs of aircraft engine gear production.
By working closely with these companies, equipment manufacturers can develop machines that address unique challenges, making the creation of intricate and precise gear components more feasible.
These partnerships also facilitate an ongoing exchange of ideas and technologies, allowing for the continuous refinement of product offerings and staying ahead in a competitive industry.
Software Developers
The contribution of software developers cannot be overlooked in the realm of bevel tooth grinding.
Developers work with aeronautic engineers to create simulations and control software that improve the grinding process.
This collaboration results in more robust simulation tools and control systems that enhance the overall efficiency and precision of grinding operations.
Software developers also bring innovations in data analytics, allowing for the analysis of vast amounts of production data.
This analysis can provide further insights into process optimization, defect prevention, and predictive maintenance.
Aerospace Companies
Aerospace companies play a critical role by providing the requirements and standards that gear manufacturing must meet.
Their feedback helps guide the development of optimized grinding technologies and processes.
Collaborating with equipment and software developers ensures that these technologies address specific needs and challenges unique to the aerospace industry.
Future Trends in Bevel Tooth Grinding Technology
The future of bevel tooth grinding technology for aircraft engine gear parts will likely see significant advancements driven by new technologies and materials.
With ongoing research and development, we can expect the introduction of even more precise grinding machines and intelligent systems that further optimize production processes.
Additive manufacturing might integrate with traditional gear machining, providing new avenues for complex component designs.
This integration could revolutionize how gears are manufactured, offering unmatched levels of precision and customization.
Furthermore, the push toward environmentally sustainable manufacturing practices will probably influence the development of grinding technologies.
Future bevel tooth grinding will likely involve processes that are more energy-efficient and produce less waste, contributing to a greener manufacturing ecosystem.
In summary, the optimization and partnership in bevel tooth grinding technology are pivotal for creating high-quality gear parts essential in modern aircraft engines.
Technological advancements, collaboration between industry players, and an eye toward the future will ensure continued progress in this critical field.
資料ダウンロード
QCD管理受発注クラウド「newji」は、受発注部門で必要なQCD管理全てを備えた、現場特化型兼クラウド型の今世紀最高の受発注管理システムとなります。
ユーザー登録
受発注業務の効率化だけでなく、システムを導入することで、コスト削減や製品・資材のステータス可視化のほか、属人化していた受発注情報の共有化による内部不正防止や統制にも役立ちます。
NEWJI DX
製造業に特化したデジタルトランスフォーメーション(DX)の実現を目指す請負開発型のコンサルティングサービスです。AI、iPaaS、および先端の技術を駆使して、製造プロセスの効率化、業務効率化、チームワーク強化、コスト削減、品質向上を実現します。このサービスは、製造業の課題を深く理解し、それに対する最適なデジタルソリューションを提供することで、企業が持続的な成長とイノベーションを達成できるようサポートします。
製造業ニュース解説
製造業、主に購買・調達部門にお勤めの方々に向けた情報を配信しております。
新任の方やベテランの方、管理職を対象とした幅広いコンテンツをご用意しております。
お問い合わせ
コストダウンが利益に直結する術だと理解していても、なかなか前に進めることができない状況。そんな時は、newjiのコストダウン自動化機能で大きく利益貢献しよう!
(β版非公開)