- お役立ち記事
- Optimization guide for RIE (reactive ion etching) technology that process engineers in the semiconductor industry should know
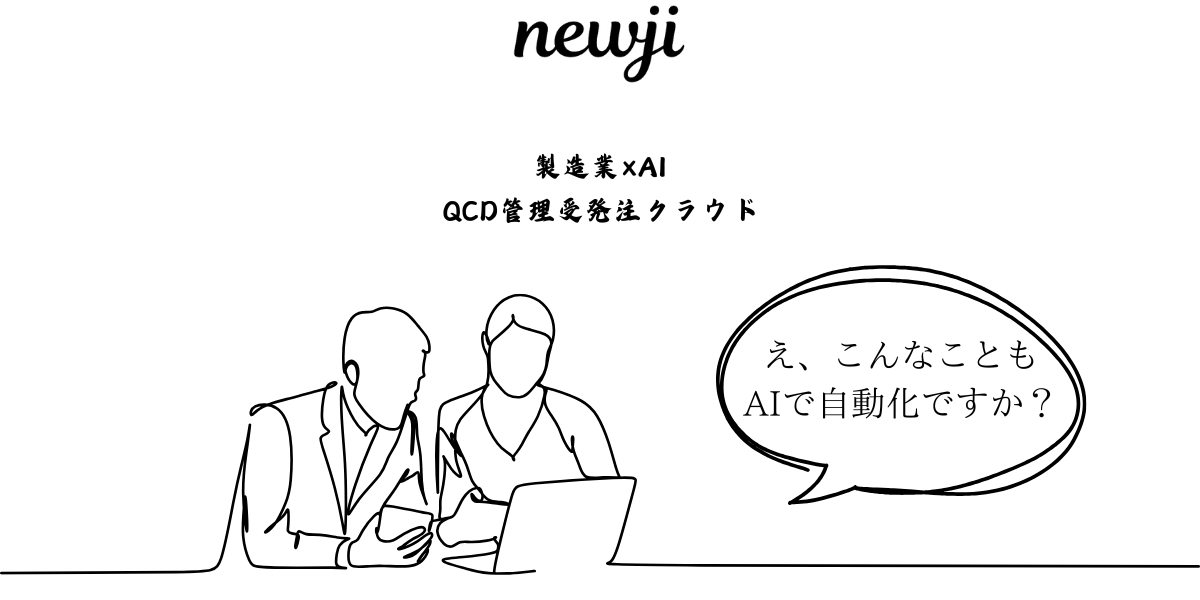
Optimization guide for RIE (reactive ion etching) technology that process engineers in the semiconductor industry should know
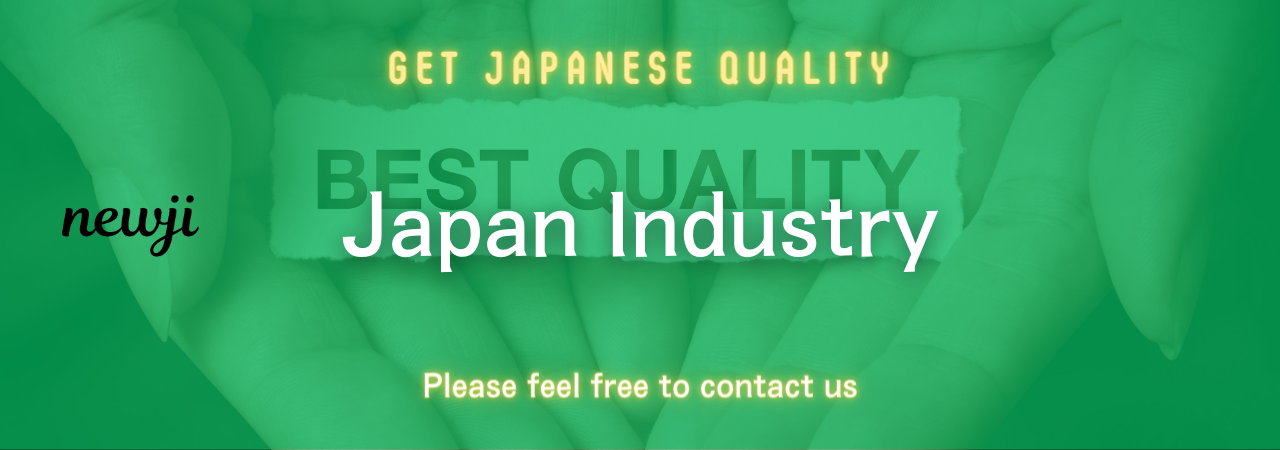
目次
Understanding Reactive Ion Etching (RIE)
Reactive Ion Etching (RIE) is a highly influential technology in the semiconductor industry, enabling precise microfabrication processes.
It is a critical technique used to etch microscopic patterns onto semiconductor wafers, a fundamental step in creating integrated circuits and various electronic devices.
RIE uses chemically reactive plasma to remove material deposited on wafers, providing a unique combination of physical bombardment and chemical reactions.
This process is instrumental in defining minute geometries in semiconductors, making it a cornerstone in modern electronic device manufacturing.
The Principles of RIE Technology
In RIE, a plasma is generated by applying a radio frequency (RF) electromagnetic field to a low-pressure gas.
The ions generated in the plasma are accelerated towards the material surface by an electric field, effectively etching the surface.
The process involves two primary mechanisms: physical sputtering and chemical reaction.
Physical sputtering is achieved by high-energy ions bombarding the target material, while the chemical component involves reactive species created in the plasma reacting with the surface material to form volatile compounds.
These volatile compounds are then removed from the etching chamber, ensuring precise material removal.
Advantages of RIE in the Semiconductor Industry
RIE offers several advantages that make it indispensable for semiconductor fabrication.
One of its most significant advantages is anisotropic etching, which allows for highly directional material removal.
This feature is vital for achieving sharp and vertical etching profiles, essential for the miniaturization of semiconductor components.
Moreover, RIE provides excellent control over etching parameters, such as etch rate and selectivity.
This control means that process engineers can precisely adjust conditions to suit different materials and application needs, ensuring high-quality results.
RIE also allows for selective etching, enabling process engineers to target specific materials while leaving others untouched.
This capability is crucial for creating intricate multi-layered semiconductor designs that require varying material properties.
Challenges in RIE Optimization
Despite its advantages, RIE poses several challenges in its optimization.
The process parameters, such as plasma power, pressure, gas flow rates, and electrode configuration, must be meticulously controlled to ensure consistent etching results.
One of the primary challenges is achieving uniformity across the wafer.
Non-uniformity can lead to inconsistencies in device performance and yield, making it essential for process engineers to carefully balance etching parameters to maintain uniformity.
Another challenge is managing the trade-off between etch rate and selectivity.
While high etch rates are desirable for throughput, they may compromise selectivity, affecting the protection of underlying layers.
Additionally, maintaining clean chamber conditions is crucial, as any contaminants can adversely affect the etching process, introducing defects.
Key Strategies for Optimizing RIE Processes
To optimize RIE processes, process engineers must focus on several key strategies.
First, careful selection of process gases is vital.
Different gases can create varied reactive species in the plasma, impacting etch rate, selectivity, and surface finish.
For instance, fluorine-based gases are preferred for silicon etching due to their high reactivity and capability to form volatile compounds with silicon.
Another strategy involves optimizing plasma parameters.
Adjusting RF power, pressure, and gas flow rates can significantly impact etching performance.
Process engineers must fine-tune these parameters to balance etch rates, selectivity, and uniformity for their specific applications.
Implementing temperature control is another crucial aspect.
Temperature variations during etching can influence the chemical reaction rates, affecting etching profiles and surface roughness.
Stable temperature control ensures consistency in etching outcomes.
Advancements in RIE Technology
Continuous advancements in RIE technology aim to overcome existing challenges and enhance process capabilities.
Recent developments include the evolution of inductively coupled plasma (ICP) RIE, a variant providing greater control over ion bombardment and chemical reactions.
ICP RIE systems utilize separate power sources for plasma generation and ion acceleration, offering enhanced etching anisotropy and control.
This advancement allows for higher aspect ratio etching, essential for technologies like MEMS (Micro-Electro-Mechanical Systems) and advanced node semiconductor manufacturing.
Furthermore, developments in endpoint detection techniques have improved etching accuracy.
Real-time monitoring and control systems enable process engineers to detect the completion of the etching process precisely, minimizing the risk of over-etching or under-etching.
Future Prospects of RIE in Semiconductor Manufacturing
As semiconductor technology continues to advance, the role of RIE in manufacturing is set to grow even more significant.
With the push towards ever-smaller component sizes and complex architectures, the precision and adaptability of RIE processes will become increasingly vital.
Future developments may focus on integrating advanced AI-based control systems to further enhance process accuracy and reduce human intervention.
This integration can potentially push the boundaries of semiconductor manufacturing to new levels of efficiency and capability.
Additionally, the trend towards environmentally friendly manufacturing practices may see innovations in RIE that reduce the use of hazardous materials and improve energy efficiency.
Conclusion
Reactive Ion Etching remains a powerful and indispensable tool in the semiconductor industry.
Its ability to precisely define intricate patterns and structures on semiconductor wafers makes it critical for the production of cutting-edge electronic devices.
While challenges in its optimization exist, employing strategic approaches and keeping abreast of technological advancements can help process engineers make the most of RIE technology.
As the industry evolves, RIE will undoubtedly play a pivotal role in shaping the future of semiconductor manufacturing.
資料ダウンロード
QCD調達購買管理クラウド「newji」は、調達購買部門で必要なQCD管理全てを備えた、現場特化型兼クラウド型の今世紀最高の購買管理システムとなります。
ユーザー登録
調達購買業務の効率化だけでなく、システムを導入することで、コスト削減や製品・資材のステータス可視化のほか、属人化していた購買情報の共有化による内部不正防止や統制にも役立ちます。
NEWJI DX
製造業に特化したデジタルトランスフォーメーション(DX)の実現を目指す請負開発型のコンサルティングサービスです。AI、iPaaS、および先端の技術を駆使して、製造プロセスの効率化、業務効率化、チームワーク強化、コスト削減、品質向上を実現します。このサービスは、製造業の課題を深く理解し、それに対する最適なデジタルソリューションを提供することで、企業が持続的な成長とイノベーションを達成できるようサポートします。
オンライン講座
製造業、主に購買・調達部門にお勤めの方々に向けた情報を配信しております。
新任の方やベテランの方、管理職を対象とした幅広いコンテンツをご用意しております。
お問い合わせ
コストダウンが利益に直結する術だと理解していても、なかなか前に進めることができない状況。そんな時は、newjiのコストダウン自動化機能で大きく利益貢献しよう!
(Β版非公開)