- お役立ち記事
- Optimization of Cooling Processes in Steel Factories for Improved Quality
月間76,176名の
製造業ご担当者様が閲覧しています*
*2025年3月31日現在のGoogle Analyticsのデータより
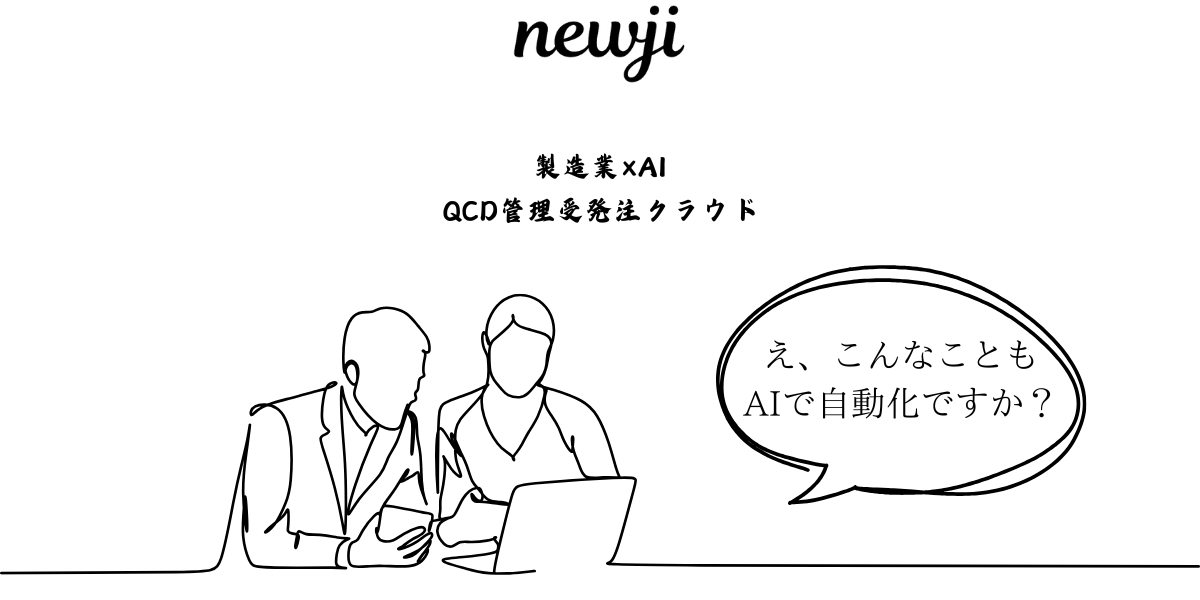
Optimization of Cooling Processes in Steel Factories for Improved Quality
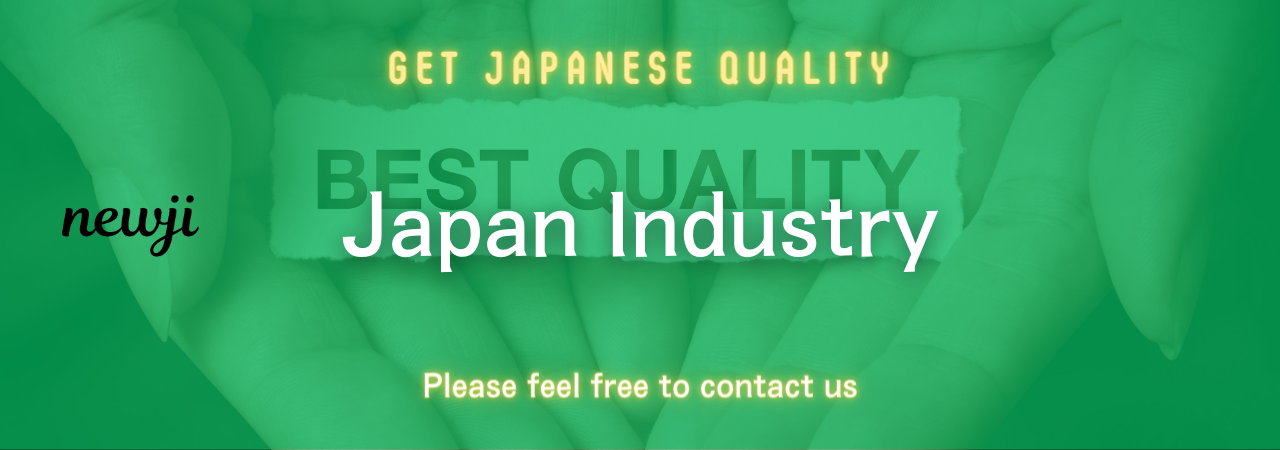
目次
Understanding the Cooling Process in Steel Production
Steel production involves several critical stages, and one of them is the cooling process.
The cooling process is essential for determining the quality and characteristics of the final steel product.
During steel manufacturing, molten steel is shaped into solid forms like bars, sheets, or beams, which are then left to cool down under controlled conditions.
The cooling process in steel factories is not just about bringing the temperature down.
It is a sophisticated procedure that impacts the internal structure, strength, and durability of the steel.
Different cooling rates can lead to variations in the hardness and toughness of the final product.
Hence, optimizing the cooling process is vital for improving the quality of steel.
Importance of Optimizing Cooling Processes
Optimization of cooling processes in steel factories focuses on achieving the ideal mechanical properties in steel.
Properly cooled steel results in better performance in construction, automotive, and machinery applications.
Inefficient cooling can lead to defects, increased costs, and reduced product lifespan.
One primary goal of optimizing cooling is to reduce internal stresses that can cause warping or cracking.
It also helps in achieving the desired microstructure that dictates the steel’s hardness and flexibility.
By optimizing cooling, steel manufacturers can produce a more consistent and reliable product that meets industry standards and customer expectations.
Factors Affecting Cooling Rates
Several factors influence the cooling rate in steel manufacturing.
The choice of cooling method, such as air cooling, water cooling, or oil quenching, significantly impacts the final product.
Each method has its own rate of heat extraction and leaves behind a distinct microstructure in the steel.
The thickness and shape of the steel piece play a role too.
Thicker sections require a slower cooling rate to avoid internal stress, while thinner pieces may cool too quickly, leading to undesired brittleness.
Moreover, the chemical composition of the steel affects how the material behaves during cooling.
Certain alloying elements can require specific cooling treatments to achieve the desired properties.
Technological Advances in Steel Cooling
With advancements in technology, steel manufacturers are now equipped with sophisticated systems to control and optimize cooling processes.
Automated control systems monitor temperature changes and adjust cooling rates in real time.
These systems use sensors and feedback loops to ensure precise temperature control.
Computational models and simulations are also used to predict the behavior of steel during cooling.
These technologies help in understanding how different cooling rates and methods affect the steel’s microstructure and mechanical properties.
Additionally, facilities are integrating artificial intelligence and machine learning algorithms to enhance cooling process efficiency.
These technologies can analyze large data sets to identify patterns and predict optimal cooling conditions for different types of steel.
Benefits of Optimal Cooling in Steel Manufacturing
Implementing optimal cooling processes in steel production brings multiple benefits.
Firstly, it leads to higher-quality steel with improved mechanical properties.
This ensures better performance and longevity of steel products, which is crucial for critical applications like construction and infrastructure.
Secondly, optimized cooling helps in minimizing waste and reducing costs.
By preventing defects and ensuring uniformity in products, manufacturers can significantly cut down on reprocessing and material wastage.
This also lowers the environmental impact, aligning with sustainable production practices.
Moreover, enhanced cooling processes can lead to energy savings.
Efficient use of cooling technologies and strategies reduces energy consumption, which is beneficial for both cost savings and environmental conservation.
This also supports factories in their goals for tighter energy management and lower carbon footprints.
Challenges in Optimizing Cooling Processes
Despite the clear advantages, optimizing cooling processes in steel manufacturing comes with its own set of challenges.
One major hurdle is the complexity of the steel microstructure, which requires precise control to achieve desired outcomes.
Manufacturers must also manage the delicate balance between cooling speed and structural integrity.
Too fast a cooling rate can lead to cracking, while too slow a rate may not achieve the hardness required.
In addition, upgrading existing facilities with modern cooling technologies requires significant investment.
Integration of new systems means retraining staff and reshaping operational strategies, which can be resource-intensive.
Furthermore, keeping up with rapid technological changes and implementing them effectively is a challenge for many steel producers.
Future of Cooling Process Optimization
Looking ahead, the future of cooling process optimization in steel factories appears promising with ongoing research and development.
Emerging technologies like smart factories, powered by the Internet of Things (IoT), promise even more precise control over cooling processes.
IoT devices can provide real-time data and insights, allowing manufacturers to make informed decisions about cooling strategies instantly.
There is also a growing trend towards developing more sustainable cooling methods to reduce environmental impact.
Innovations in coolants, processes, and energy-efficient systems are paving the way for more environmentally friendly steel production.
Collaboration between researchers, manufacturers, and technology providers is essential to advance this field.
In conclusion, optimizing the cooling process in steel factories is a crucial step in improving product quality and manufacturing efficiency.
By addressing the challenges and embracing new technologies, steel manufacturers can enhance their competitive edge and meet evolving industry standards.
資料ダウンロード
QCD管理受発注クラウド「newji」は、受発注部門で必要なQCD管理全てを備えた、現場特化型兼クラウド型の今世紀最高の受発注管理システムとなります。
ユーザー登録
受発注業務の効率化だけでなく、システムを導入することで、コスト削減や製品・資材のステータス可視化のほか、属人化していた受発注情報の共有化による内部不正防止や統制にも役立ちます。
NEWJI DX
製造業に特化したデジタルトランスフォーメーション(DX)の実現を目指す請負開発型のコンサルティングサービスです。AI、iPaaS、および先端の技術を駆使して、製造プロセスの効率化、業務効率化、チームワーク強化、コスト削減、品質向上を実現します。このサービスは、製造業の課題を深く理解し、それに対する最適なデジタルソリューションを提供することで、企業が持続的な成長とイノベーションを達成できるようサポートします。
製造業ニュース解説
製造業、主に購買・調達部門にお勤めの方々に向けた情報を配信しております。
新任の方やベテランの方、管理職を対象とした幅広いコンテンツをご用意しております。
お問い合わせ
コストダウンが利益に直結する術だと理解していても、なかなか前に進めることができない状況。そんな時は、newjiのコストダウン自動化機能で大きく利益貢献しよう!
(β版非公開)