- お役立ち記事
- Optimization of Exhaust Manifold Design and Manufacturing
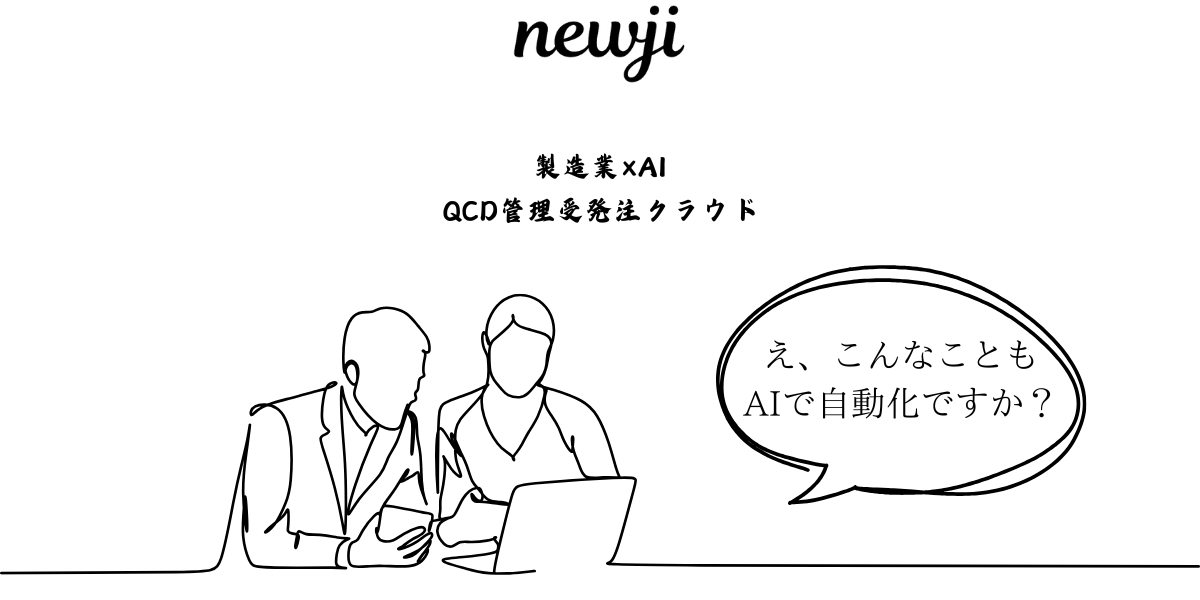
Optimization of Exhaust Manifold Design and Manufacturing
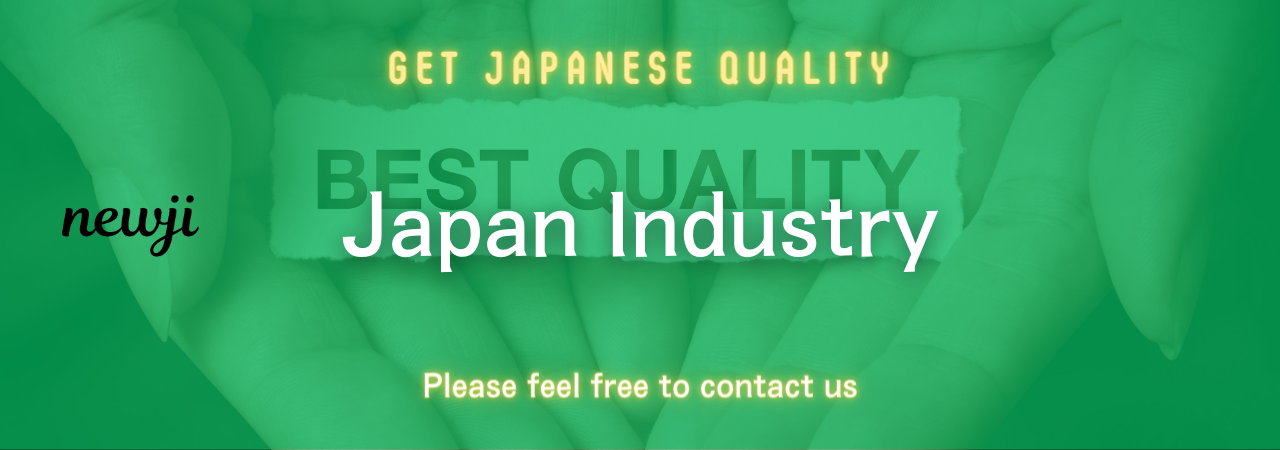
The optimization of exhaust manifold design and manufacturing plays a crucial role in enhancing the efficiency and performance of an engine. An exhaust manifold is a component that collects exhaust gases from the engine’s cylinders and directs them to the exhaust system. Innovations in materials, design, and manufacturing techniques have paved the way for significant improvements. Let’s delve into the details of how these advancements contribute to optimizing exhaust manifold design and manufacturing.
目次
Understanding the Significance of Exhaust Manifolds
The exhaust manifold is a vital component in the engine’s exhaust system. Its primary function is to collect exhaust gases from multiple cylinders and funnel them into a single pipe. This process needs to be efficient to ensure optimal engine performance and fuel efficiency.
A poorly designed exhaust manifold can lead to various issues such as increased backpressure, poor engine performance, and increased fuel consumption. Therefore, optimizing its design and manufacturing is essential to maximize the engine’s efficiency and minimize emissions.
Factors Influencing Exhaust Manifold Design
Several factors influence the design of an exhaust manifold, and addressing these factors is essential in the optimization process.
Material Selection
Material selection plays a crucial role in the performance of an exhaust manifold. The materials must withstand high temperatures and resist corrosion. Common materials used include cast iron, stainless steel, and high-temperature alloys. Each of these materials has its advantages and drawbacks, making the choice dependent on the specific application and performance requirements.
Thermal Efficiency
Thermal efficiency is another important factor to consider. The exhaust manifold must be designed to dissipate heat effectively. Poor thermal management can lead to overheating and damage to the engine. Advanced designs include features such as thermal barriers and heat shields to manage the high temperatures.
Flow Dynamics
The flow dynamics within the exhaust manifold significantly impact the overall performance. The geometry of the manifold must ensure smooth and efficient flow of exhaust gases. Sharp bends, abrupt changes in cross-section, and other design flaws can cause turbulence and increased backpressure. Computational fluid dynamics (CFD) simulations are often used to optimize the flow characteristics.
Advancements in Manufacturing Techniques
Modern manufacturing techniques have greatly contributed to the optimization of exhaust manifold design. These advancements have led to improvements in precision, efficiency, and overall performance.
3D Printing
3D printing, or additive manufacturing, has revolutionized exhaust manifold production. This technique allows for the creation of complex geometries that were previously difficult or impossible to manufacture using traditional methods. 3D printing also enables rapid prototyping, reducing the time and cost associated with developing new designs.
Computer-Aided Design (CAD)
Computer-Aided Design (CAD) software is extensively used in the design of exhaust manifolds. CAD allows engineers to create highly detailed and accurate models of the manifold. These models can be easily modified and optimized based on performance simulations and testing results.
Advanced Welding Techniques
Advanced welding techniques have improved the durability and performance of exhaust manifolds. Techniques such as laser welding and friction stir welding create strong, high-quality joints. These methods also minimize thermal distortion, which can negatively impact the manifold’s performance.
Testing and Validation
Testing and validation are critical stages in the optimization process. These stages ensure that the designed and manufactured exhaust manifold meets all performance and durability requirements.
Performance Testing
Performance testing involves evaluating the exhaust manifold under real-world conditions. This includes testing for factors such as backpressure, flow efficiency, and thermal management. Performance testing helps identify any design flaws that need to be addressed.
Durability Testing
Durability testing assesses the manifold’s ability to withstand prolonged exposure to high temperatures and stress. It ensures that the material and construction can handle the demands of the engine over its lifetime. Fatigue testing and thermal cycling are common methods used in durability testing.
Emissions Testing
Optimizing the exhaust manifold contributes to reducing emissions. Emissions testing involves measuring the levels of pollutants released by the engine. A well-designed exhaust manifold can improve the efficiency of the catalytic converter and other emissions control systems.
The Future of Exhaust Manifold Optimization
The future of exhaust manifold optimization looks promising with ongoing advancements in materials science, manufacturing techniques, and simulation technologies.
Smart Materials
The development of smart materials that can adapt to changing conditions is an exciting area of research. These materials can offer improved thermal management and durability, leading to more efficient exhaust manifolds.
Artificial Intelligence and Machine Learning
Artificial intelligence (AI) and machine learning (ML) are being integrated into the design and optimization process. These technologies can analyze vast amounts of data to identify patterns and optimize designs. AI and ML can significantly reduce the time required for design iterations and testing.
Environmentally Friendly Solutions
As environmental regulations become stricter, there is a growing focus on developing exhaust manifolds that help reduce emissions. This includes exploring alternatives to traditional materials and incorporating advanced catalytic technologies.
Optimizing exhaust manifold design and manufacturing is a continuous process that involves a deep understanding of material science, engineering principles, and innovative manufacturing techniques. By addressing factors like material selection, thermal efficiency, and flow dynamics, and leveraging modern technologies such as 3D printing, CAD, and AI, it is possible to develop exhaust manifolds that enhance engine performance, improve fuel efficiency, and reduce emissions. The future of exhaust manifold optimization holds great potential, promising even greater advancements and environmental benefits.
資料ダウンロード
QCD調達購買管理クラウド「newji」は、調達購買部門で必要なQCD管理全てを備えた、現場特化型兼クラウド型の今世紀最高の購買管理システムとなります。
ユーザー登録
調達購買業務の効率化だけでなく、システムを導入することで、コスト削減や製品・資材のステータス可視化のほか、属人化していた購買情報の共有化による内部不正防止や統制にも役立ちます。
NEWJI DX
製造業に特化したデジタルトランスフォーメーション(DX)の実現を目指す請負開発型のコンサルティングサービスです。AI、iPaaS、および先端の技術を駆使して、製造プロセスの効率化、業務効率化、チームワーク強化、コスト削減、品質向上を実現します。このサービスは、製造業の課題を深く理解し、それに対する最適なデジタルソリューションを提供することで、企業が持続的な成長とイノベーションを達成できるようサポートします。
オンライン講座
製造業、主に購買・調達部門にお勤めの方々に向けた情報を配信しております。
新任の方やベテランの方、管理職を対象とした幅広いコンテンツをご用意しております。
お問い合わせ
コストダウンが利益に直結する術だと理解していても、なかなか前に進めることができない状況。そんな時は、newjiのコストダウン自動化機能で大きく利益貢献しよう!
(Β版非公開)