- お役立ち記事
- Optimization of Inline Machining Systems in Production Lines
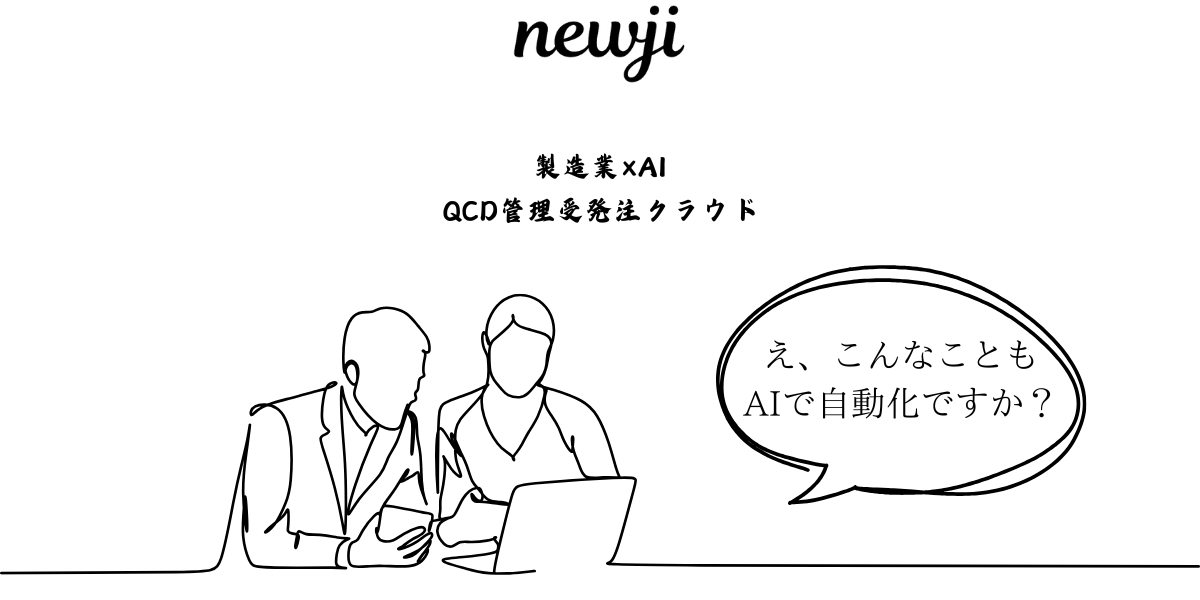
Optimization of Inline Machining Systems in Production Lines
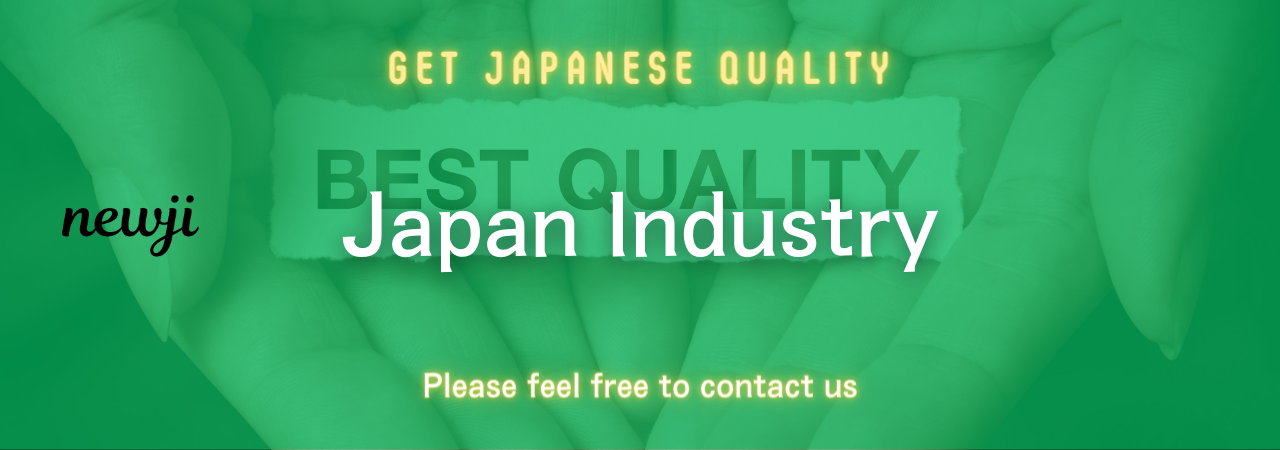
目次
Understanding Inline Machining Systems
Inline machining systems are an integral part of modern production lines.
These systems are designed to perform various machining operations without the need to remove the workpiece from the production line setup.
By integrating machining processes directly into the line, manufacturers can streamline operations, reduce cycle times, and enhance overall efficiency.
Inline machining systems combine multiple machining capabilities in one system.
These can include milling, drilling, turning, and more.
The objective is to handle complex parts easily and to ensure quality and consistency throughout the production process.
Advantages of Inline Machining Systems
Implementing inline machining systems comes with several benefits.
They enhance the speed and efficiency of production processes by allowing operations to occur simultaneously with other production activities.
This synchronization minimizes delays and boosts throughput.
Moreover, inline systems help in reducing labor costs.
Since tasks that were previously performed manually are now automated, the need for human intervention decreases.
This not only cuts labor expenses but also reduces the likelihood of human error in operations.
Inline machining systems also improve product quality.
Automated precision reduces variations between components and enhances the consistency of the end products.
As a result, manufacturers can achieve higher quality standards, which can lead to increased customer satisfaction and lower rejection rates.
Challenges in Optimizing Inline Machining Systems
Despite the advantages, optimizing inline machining systems can be challenging.
One common issue is the initial setup cost.
These systems require a significant upfront investment, including purchasing the machinery, integrating it into existing lines, and training staff.
Maintenance is another critical factor.
Inline systems are complex and require regular maintenance to function effectively.
Unexpected downtime due to maintenance issues can disrupt the entire production line, impacting productivity and delivery schedules.
Another challenge is the limited flexibility in handling new or unique product designs.
Inline systems are often tailor-made for mass production of particular products.
Any change in product design might require a reconfiguration of the entire system, which can be time-consuming and costly.
Strategies for Optimization
To overcome these challenges and optimize inline machining systems, manufacturers can adopt several strategies.
First, investing in advanced technology and machinery is vital.
Machines with the latest technology not only deliver improved performance but also offer better compatibility with different materials and part designs.
Additionally, manufacturers should focus on robust training programs for staff.
Operators and technicians must be adequately trained to use, maintain, and troubleshoot inline machining systems.
This training can go a long way in minimizing downtime and ensuring smooth operations.
Regular maintenance and monitoring are also crucial.
Implementing predictive maintenance strategies can help in anticipating potential machine failures and preventing unexpected downtime.
IoT devices and sensors can be used for real-time monitoring and data collection, allowing for timely maintenance interventions.
Finally, collaboration with equipment suppliers and integrators can provide valuable insights and support.
Suppliers can offer expertise in optimizing system performance, recommending suitable upgrades, and advising on best practices.
Integrating Inline Machining with Other Production Technologies
To achieve full optimization, inline machining systems should be integrated with other production technologies.
For example, combining inline machining with automation and robotics can further enhance productivity.
Robots can handle the movement of workpieces between different machining stations, improving cycle times and reducing manual handling.
Using advanced software solutions for process planning and control is also beneficial.
These solutions can manage and optimize workflow, quality control, and production scheduling.
When integrated properly, they ensure that both machines and human resources are used effectively.
Moreover, adopting lean manufacturing principles can significantly improve the efficacy of inline machining systems.
These principles focus on eliminating waste, reducing non-value-added activities, and improving process flow.
Aligning inline machining systems with these principles can create more efficient, cost-effective production lines.
The Future of Inline Machining Systems
As technology evolves, so will inline machining systems.
The future promises even more innovative solutions that will further improve production efficiency.
For instance, the emergence of digital twins could revolutionize inline machining.
Digital twins are virtual replicas of physical assets that allow for simulation and optimization of production processes in a digital environment.
This technology can help predict and mitigate potential issues before they occur in the real world.
Furthermore, continuous advancements in materials and cutting tools will enhance the capabilities of inline machining systems.
These innovations can lead to faster processing times, greater flexibility, and higher precision.
The integration of artificial intelligence and machine learning with inline machining systems is another area of potential growth.
AI can analyze vast datasets to identify patterns and insights that can lead to improved decision-making and operational efficiency.
In conclusion, while optimizing inline machining systems in production lines presents certain challenges, the benefits outweigh these hurdles.
By investing in state-of-the-art technology, training, maintenance, and collaboration, manufacturers can unlock significant efficiency gains.
Furthermore, integrating these systems with other advanced technologies holds immense potential for transforming modern manufacturing landscapes.
資料ダウンロード
QCD調達購買管理クラウド「newji」は、調達購買部門で必要なQCD管理全てを備えた、現場特化型兼クラウド型の今世紀最高の購買管理システムとなります。
ユーザー登録
調達購買業務の効率化だけでなく、システムを導入することで、コスト削減や製品・資材のステータス可視化のほか、属人化していた購買情報の共有化による内部不正防止や統制にも役立ちます。
NEWJI DX
製造業に特化したデジタルトランスフォーメーション(DX)の実現を目指す請負開発型のコンサルティングサービスです。AI、iPaaS、および先端の技術を駆使して、製造プロセスの効率化、業務効率化、チームワーク強化、コスト削減、品質向上を実現します。このサービスは、製造業の課題を深く理解し、それに対する最適なデジタルソリューションを提供することで、企業が持続的な成長とイノベーションを達成できるようサポートします。
オンライン講座
製造業、主に購買・調達部門にお勤めの方々に向けた情報を配信しております。
新任の方やベテランの方、管理職を対象とした幅広いコンテンツをご用意しております。
お問い合わせ
コストダウンが利益に直結する術だと理解していても、なかなか前に進めることができない状況。そんな時は、newjiのコストダウン自動化機能で大きく利益貢献しよう!
(Β版非公開)