- お役立ち記事
- Optimization of Intake Manifold Design and Manufacturing
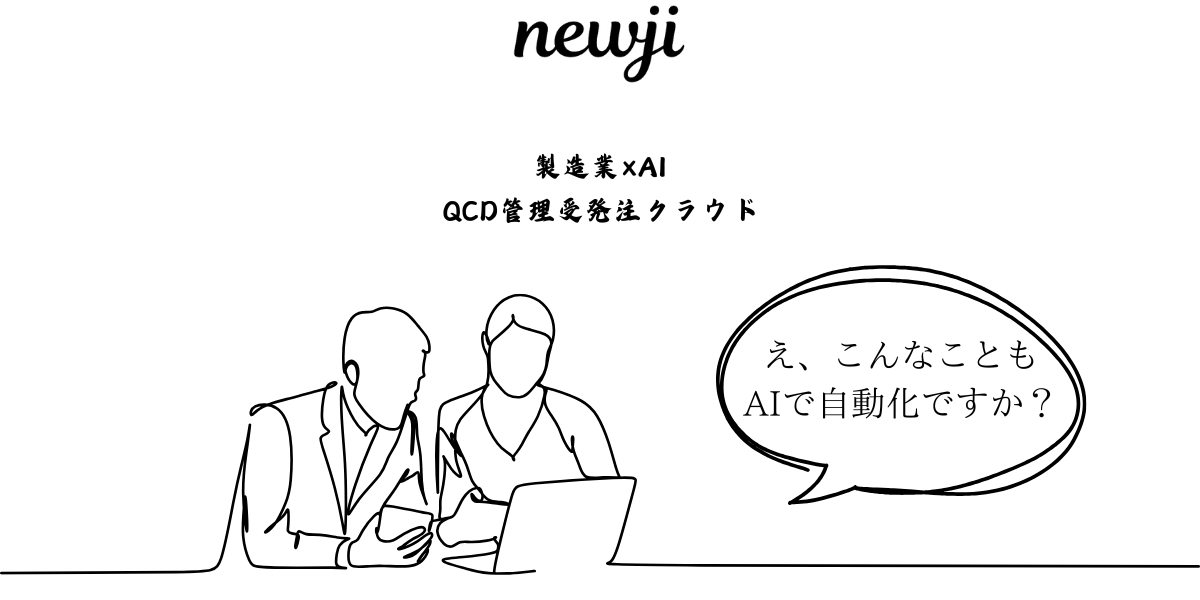
Optimization of Intake Manifold Design and Manufacturing
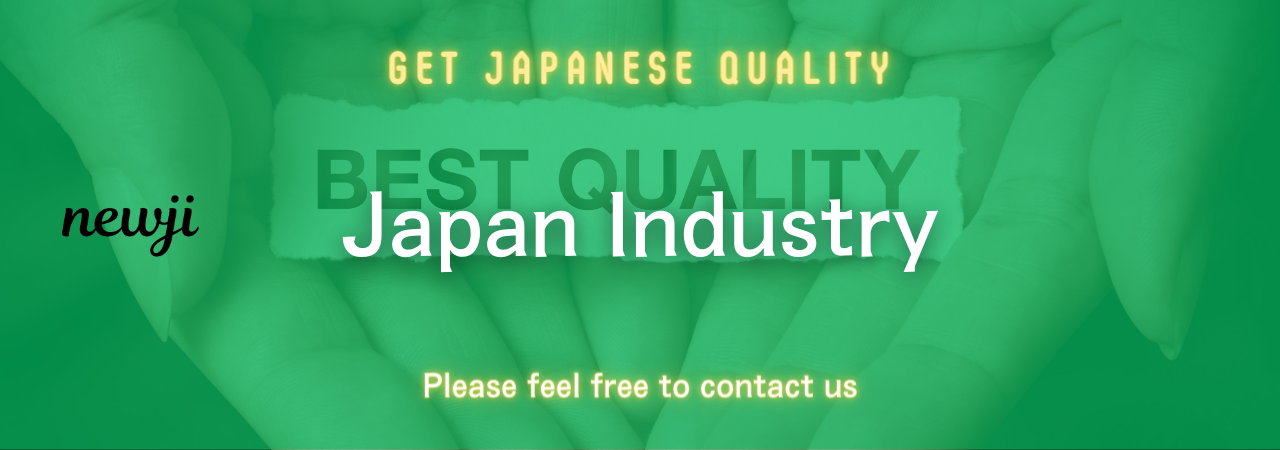
The intake manifold is a crucial component in an internal combustion engine.
It is responsible for evenly distributing the air-fuel mixture to each cylinder.
Getting its design and manufacturing right can result in significant improvements in engine performance and efficiency.
目次
What is an Intake Manifold?
The intake manifold is like an air highway that delivers air to the engine’s combustion chambers.
It sits on top of the engine and connects the carburetor or throttle body to the cylinder heads.
Its main role is to ensure that each cylinder receives the right amount of air-fuel mixture.
This ensures optimal combustion and, ultimately, enhances engine performance.
Importance of Design Optimization
Optimizing the design of the intake manifold is vital for many reasons.
A well-designed manifold can improve airflow, which enhances engine efficiency and power output.
Enhancing Airflow
The primary objective of optimizing the intake manifold design is to improve airflow.
The smoother and faster the airflow, the better the engine performs.
Designs that reduce airflow resistance help in achieving better fuel economy and power output.
Ensuring Air Distribution
Another critical aspect is the even distribution of air to all cylinders.
Uniform air distribution ensures that each cylinder operates under identical conditions.
This results in more consistent power delivery and reduces engine knocking or misfires.
Material Selection
The choice of material for the intake manifold is crucial.
Lightweight yet sturdy materials like aluminum or composite plastics are often preferred.
These materials help in reducing the overall weight of the engine while ensuring durability and thermal resistance.
Manufacturing Techniques
Various manufacturing techniques are employed to produce intake manifolds, each with its own set of advantages and drawbacks.
Die Casting
Die casting is a popular method for producing aluminum intake manifolds.
In this process, molten aluminum is poured into a mold, which is then cooled and solidified.
Die casting allows for high precision and smooth finishes, which are crucial for optimal airflow.
Injection Molding
Injection molding is a technique often used for creating composite plastic intake manifolds.
In this process, melted plastic is injected into a mold under high pressure.
Injection molding offers great design flexibility and is ideal for producing intricate shapes and designs.
3D Printing
3D printing is an emerging technology in the manufacturing of intake manifolds.
It allows for the rapid production of prototypes and complex designs that are difficult to achieve with traditional methods.
3D printing also enables quick iterations and testing, leading to faster optimization cycles.
Simulation and Testing
Computer-aided design (CAD) software plays a pivotal role in the optimization of intake manifold designs.
Engineers can use simulation tools to model airflow and identify areas of improvement.
Once a design is finalized, physical prototypes are created and subjected to rigorous testing to ensure performance meets the desired standards.
Computational Fluid Dynamics (CFD)
CFD simulations are used to analyze the airflow within the intake manifold.
By modeling the flow of air, engineers can identify bottlenecks or areas of turbulence.
CFD simulations help in making design adjustments that enhance airflow and improve performance.
Wind Tunnel Testing
Wind tunnel testing is another method used to evaluate intake manifold designs.
Prototypes are tested in a controlled environment to measure airflow rates and distribution.
This real-world testing complements CFD simulations and provides valuable data for further optimization.
Environmental Considerations
Environmental regulations are becoming increasingly stringent, necessitating the need for intake manifold designs that meet emission standards.
Optimized designs can contribute to better combustion efficiency, which reduces harmful emissions.
Additionally, the choice of materials and manufacturing processes should also consider environmental impacts.
Future Trends
The future of intake manifold design and manufacturing looks promising with advancements in technology.
Integration with Smart Technologies
The integration of smart sensors and control systems within the intake manifold can lead to adaptive performance enhancements.
These smart technologies can monitor airflow in real-time and make adjustments to optimize engine performance and efficiency.
Advanced Materials
Research is ongoing into the use of advanced materials like carbon fiber composites and lightweight alloys.
These materials offer superior strength-to-weight ratios, further enhancing the performance and efficiency of the intake manifold.
AI and Machine Learning
Artificial Intelligence (AI) and Machine Learning (ML) are set to play a significant role in the optimization process.
These technologies can analyze vast amounts of data from simulations and testing, enabling more precise design adjustments and faster optimization cycles.
Optimizing the design and manufacturing of intake manifolds is essential for achieving better engine performance, efficiency, and compliance with environmental regulations.
Advancements in materials, manufacturing techniques, and technologies like AI and machine learning are paving the way for innovations in this critical component of internal combustion engines.
With continuous improvements, the future of intake manifold design looks both exciting and promising.
資料ダウンロード
QCD調達購買管理クラウド「newji」は、調達購買部門で必要なQCD管理全てを備えた、現場特化型兼クラウド型の今世紀最高の購買管理システムとなります。
ユーザー登録
調達購買業務の効率化だけでなく、システムを導入することで、コスト削減や製品・資材のステータス可視化のほか、属人化していた購買情報の共有化による内部不正防止や統制にも役立ちます。
NEWJI DX
製造業に特化したデジタルトランスフォーメーション(DX)の実現を目指す請負開発型のコンサルティングサービスです。AI、iPaaS、および先端の技術を駆使して、製造プロセスの効率化、業務効率化、チームワーク強化、コスト削減、品質向上を実現します。このサービスは、製造業の課題を深く理解し、それに対する最適なデジタルソリューションを提供することで、企業が持続的な成長とイノベーションを達成できるようサポートします。
オンライン講座
製造業、主に購買・調達部門にお勤めの方々に向けた情報を配信しております。
新任の方やベテランの方、管理職を対象とした幅広いコンテンツをご用意しております。
お問い合わせ
コストダウンが利益に直結する術だと理解していても、なかなか前に進めることができない状況。そんな時は、newjiのコストダウン自動化機能で大きく利益貢献しよう!
(Β版非公開)