- お役立ち記事
- Optimization of the firing process in the ceramic industry and its effective management method
月間77,185名の
製造業ご担当者様が閲覧しています*
*2025年2月28日現在のGoogle Analyticsのデータより
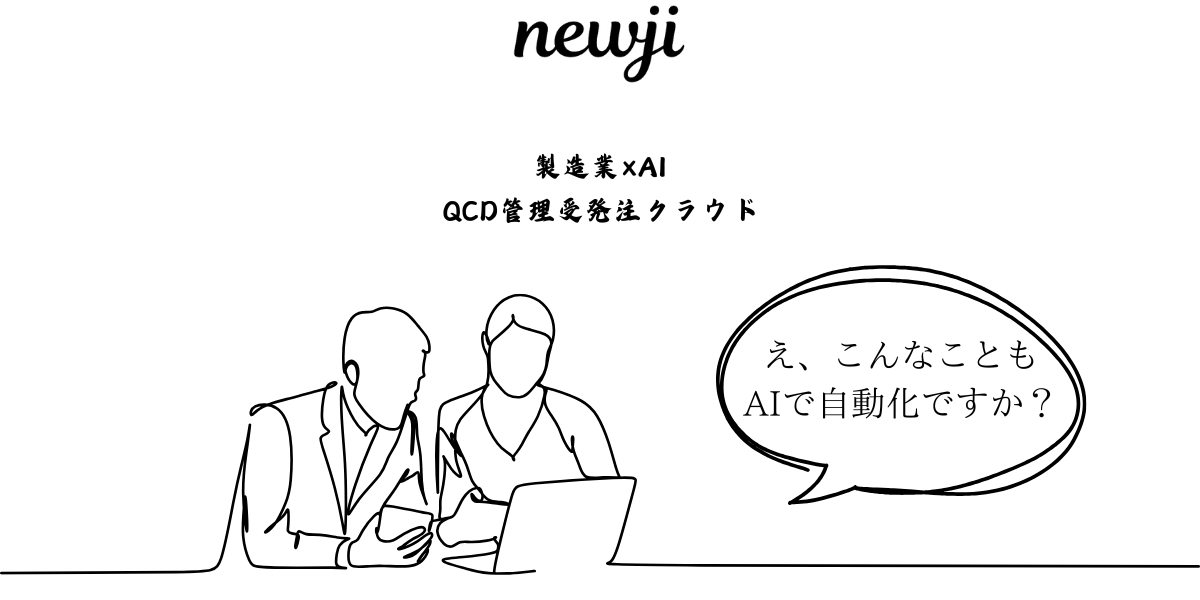
Optimization of the firing process in the ceramic industry and its effective management method
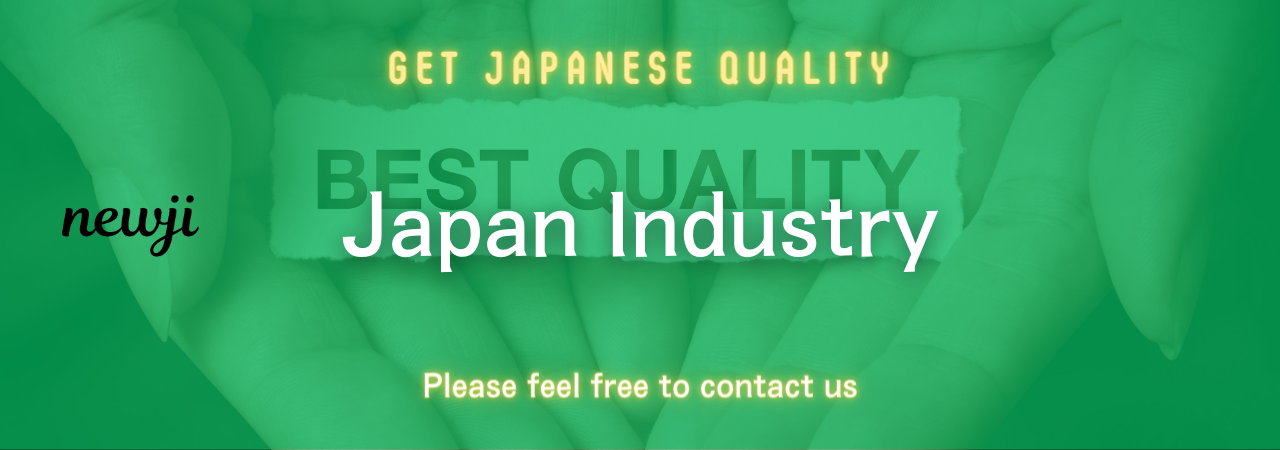
目次
Understanding the Firing Process in the Ceramic Industry
The firing process in the ceramic industry is a critical stage that significantly impacts the final product quality, strength, and color.
This process involves heating shaped ceramic materials to high temperatures in a kiln to induce necessary chemical reactions.
During firing, raw clay transforms into what is known as ceramic.
This transformation not only strengthens the material but also develops its aesthetic qualities, making efficient firing essential for any successful ceramic production.
In essence, the firing process can be divided into different stages.
Firstly, there is the drying stage, followed by the chemical reactions taking place at various temperatures, and finally, the cooling down phase.
Any inefficiencies or mishandlings in these stages can lead to defects like warping, cracking, or an uneven finish.
Key Stages of the Firing Process
Drying Stage
Before firing begins, the clay body must be dried thoroughly.
Excess moisture in ceramic pieces can cause explosive steam formation once inside the kiln.
Therefore, it is crucial to ensure that the clay has dried evenly to prevent cracks or ‘blowouts’, where the piece can break or explode.
Heating Stage
The heating stage involves a gradual increase in temperature.
Controlled heating ensures that volatile components are driven out smoothly.
This phase includes the ignition of any organic material present, causing burnout and contributing to the ceramic’s strength.
Chemical Reactions at High Temperatures
As the temperature rises, several chemical reactions occur.
Around 850°C, quartz in the clay changes structure, known as quartz inversion, which incites expansion that can cause cracking if heating is too rapid.
At higher temperatures, vitrification starts, where the materials become glassy and liquid, sealing the pores and waterproofing the ceramics.
Cooling Stage
Proper cooling is as vital as the heating process.
Cooling too rapidly can cause thermal shock, leading to cracks or fractures.
Controlled cooling ensures that the ceramic piece retains its structural integrity and aesthetic quality.
Optimizing Firing Process for Better Results
Optimization in the firing process is about ensuring efficiency in temperature control, minimizing energy use, reducing costs, and improving product quality.
Here are some methods to achieve an optimized firing process:
Regular Kiln Maintenance
Periodic maintenance of the kiln is necessary to avoid any disruptions during firing.
It ensures the equipment is operating at optimum efficiency, which contributes significantly to energy conservation and consistency in product quality.
Using Proper Firing Schedules
Developing and following accurate firing schedules tailored to the specific needs of the ceramic materials being fired can optimize results.
Each type of ceramic material may require different temperature ranges and durations to achieve the desired vitrification and strength.
Energy Efficiency Measures
Adopting energy-efficient practices within the firing process can lead to substantial cost savings.
This might include using kilns designed for better insulation, recirculating air to maintain heat, or employing automated systems to regulate temperature precisely.
Implementing Process Control Systems
Advanced technological systems aid in rigorous process controls during firing.
Sensors and computer systems can monitor the kiln environment and adjust temperatures automatically, ensuring that each firing phase occurs correctly.
Effective Management Methods for the Firing Process
Effective management of the firing process includes strategic planning and personnel management, as well as implementing technology for better tracking and outcomes.
Training and Skill Development
Training kiln operators to understand and react to the intricacies of firing processes is vital.
Knowledgeable operators can identify potential issues early, optimize kiln performance, and ensure consistent quality of output.
Investing in Technology
Utilizing technology such as advanced kiln controllers or software that tracks firing cycles can improve the efficiency and quality control of the firing process.
Technology streamlines operations and minimizes disruptions caused by human error.
Continuous Improvement Practices
Adopting continuous improvement practices in the firing process can drive efficiency.
Regularly reviewing and updating firing practices to incorporate new insights or techniques can lead to better energy use and higher quality ceramics.
Conclusion
Optimizing the firing process in the ceramic industry is fundamental to attaining high-quality results.
Through proper kiln maintenance, efficient firing schedules, energy conservation strategies, and advanced technology, the ceramic manufacturing process can be significantly improved.
Effective management ensures not only the quality of the production but also supports the industry’s sustainable growth by reducing energy consumption and enhancing product output.
For any ceramic business aiming for excellence, these optimization strategies are crucial in fostering both efficiency and innovation.
資料ダウンロード
QCD管理受発注クラウド「newji」は、受発注部門で必要なQCD管理全てを備えた、現場特化型兼クラウド型の今世紀最高の受発注管理システムとなります。
ユーザー登録
受発注業務の効率化だけでなく、システムを導入することで、コスト削減や製品・資材のステータス可視化のほか、属人化していた受発注情報の共有化による内部不正防止や統制にも役立ちます。
NEWJI DX
製造業に特化したデジタルトランスフォーメーション(DX)の実現を目指す請負開発型のコンサルティングサービスです。AI、iPaaS、および先端の技術を駆使して、製造プロセスの効率化、業務効率化、チームワーク強化、コスト削減、品質向上を実現します。このサービスは、製造業の課題を深く理解し、それに対する最適なデジタルソリューションを提供することで、企業が持続的な成長とイノベーションを達成できるようサポートします。
製造業ニュース解説
製造業、主に購買・調達部門にお勤めの方々に向けた情報を配信しております。
新任の方やベテランの方、管理職を対象とした幅広いコンテンツをご用意しております。
お問い合わせ
コストダウンが利益に直結する術だと理解していても、なかなか前に進めることができない状況。そんな時は、newjiのコストダウン自動化機能で大きく利益貢献しよう!
(β版非公開)