- お役立ち記事
- Optimization strategies for MRP (Material Requirements Planning) that production management departments should keep in mind
月間76,176名の
製造業ご担当者様が閲覧しています*
*2025年3月31日現在のGoogle Analyticsのデータより
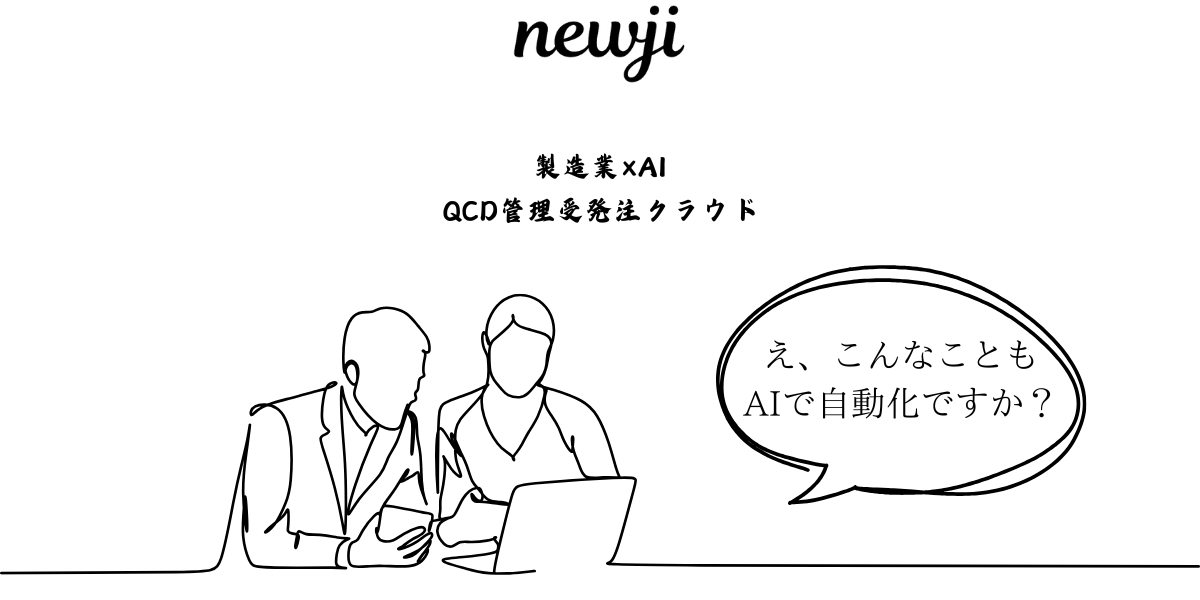
Optimization strategies for MRP (Material Requirements Planning) that production management departments should keep in mind
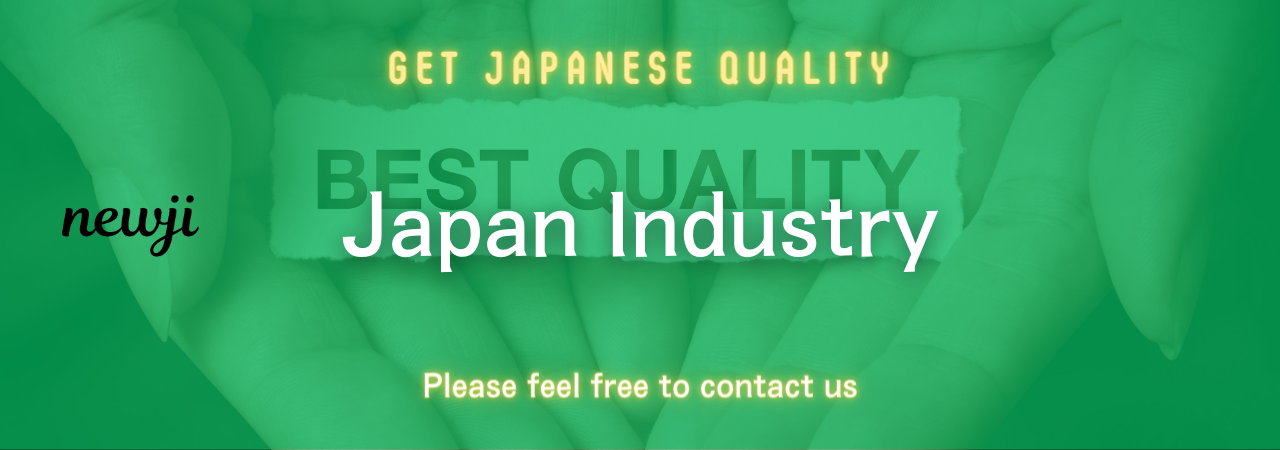
目次
Understanding MRP and Its Importance
Material Requirements Planning (MRP) is a systematic method used for managing manufacturing processes.
At its core, MRP helps ensure that materials and products are readily available for production, minimizing inventory levels and optimizing manufacturing schedules.
For production management departments, mastering MRP is critical to streamline operations, enhance efficiency, and reduce costs.
MRP involves the planning of materials needed for production, scheduling product assembly, and ensuring that components and materials meet the demands of production cycles.
Proper implementation of MRP enables manufacturers to meet customer demands efficiently while minimizing waste.
Key Objectives of MRP
The primary objectives of MRP systems include inventory control, production planning, and scheduling.
The system effectively allows businesses to strike a balance between these elements to optimize production processes.
By achieving these objectives, production management departments can ensure on-time delivery, improve product quality, and lower operational costs.
Inventory Control
One of the primary goals of MRP is to maintain optimal levels of inventory.
Too much inventory results in increased holding costs, while too little can lead to production delays and unmet customer demands.
An effective MRP system helps in forecasting demand accurately, thus maintaining inventory at levels that support smooth production without excess stock.
Production Planning and Scheduling
MRP assists in developing precise production schedules that coordinate the manufacturing process.
By aligning material procurement with production timelines, businesses can ensure that processes flow seamlessly without interruption.
This synchronization leads to higher productivity and more reliable lead times.
Strategies for Optimizing MRP
With a solid understanding of MRP objectives, production departments can now look at optimization strategies.
Optimizing MRP is crucial to improving supply chain efficiency and competitiveness.
Here are some strategies that departments should consider for optimizing MRP:
Accurate Demand Forecasting
Accurate demand forecasting is a cornerstone for an effective MRP system.
By leveraging historical data, market trends, and advanced analytical tools, production managers can predict future demand more precisely.
This enables the department to adjust inventory levels accordingly, reducing the risk of overproduction or stockouts.
Regular System Updates
Keeping the MRP system updated with accurate and current data is essential for optimization.
This includes updating inventory levels, supplier lead times, and production capacity regularly.
By ensuring data accuracy, production management can prevent errors and inefficiencies in the planning process.
Supplier Collaboration
Building strong relationships with suppliers can significantly enhance MRP efficiency.
Collaborative efforts such as sharing forecasts and establishing clear communication channels help align the supply chain with production needs.
Timely material sourcing and reduced lead times can be achieved with robust supplier partnerships.
Implementing Lean Manufacturing Principles
Incorporating lean manufacturing principles with MRP can lead to significant improvements.
By focusing on waste reduction, continuous improvement, and efficient resource use, production management can optimize processes and lower costs.
Lean principles emphasize value creation and can be integrated with MRP to enhance overall production efficiency.
Utilizing Advanced Technologies
In the age of digitalization, incorporating technologies such as Artificial Intelligence (AI) and Machine Learning (ML) into MRP systems can provide a competitive edge.
These technologies enable real-time data analysis and predictive insights, allowing for more informed decision-making and quicker response times.
Automation of routine MRP tasks can also free up resources for more strategic endeavors.
Challenges in MRP Implementation
While MRP offers numerous benefits, implementation can come with challenges that production management must address.
Understanding these challenges is vital to successfully optimizing MRP systems.
Data Quality and Integrity
The accuracy of an MRP system heavily relies on the quality of data fed into it.
Inconsistent or incorrect data can lead to inefficiencies and disruptions in the supply chain.
Ensuring data integrity and regular audits can mitigate these risks and enhance system reliability.
System Complexity
MRP systems can be complex to set up and manage, particularly for large organizations with extensive supply chains.
Employees need sufficient training to understand and operate the system effectively.
Investing in user-friendly software and comprehensive training programs can ease the complexity associated with MRP systems.
Change Management
Implementing or updating an MRP system often requires significant changes in processes and workflows.
Resistance to change can be a major hurdle.
A change management plan that includes clear communication, training, and support can facilitate a smoother transition and adoption.
Conclusion
Optimizing Material Requirements Planning (MRP) is essential for effective production management.
With accurate demand forecasting, regular system updates, supplier collaboration, lean principles, and advanced technologies, production departments can significantly improve their MRP systems.
While challenges exist, understanding and addressing them leads to smoother implementations and greater returns on investment.
For production management departments, focusing on MRP optimization translates to operational excellence, higher customer satisfaction, and a stronger competitive position in the market.
資料ダウンロード
QCD管理受発注クラウド「newji」は、受発注部門で必要なQCD管理全てを備えた、現場特化型兼クラウド型の今世紀最高の受発注管理システムとなります。
ユーザー登録
受発注業務の効率化だけでなく、システムを導入することで、コスト削減や製品・資材のステータス可視化のほか、属人化していた受発注情報の共有化による内部不正防止や統制にも役立ちます。
NEWJI DX
製造業に特化したデジタルトランスフォーメーション(DX)の実現を目指す請負開発型のコンサルティングサービスです。AI、iPaaS、および先端の技術を駆使して、製造プロセスの効率化、業務効率化、チームワーク強化、コスト削減、品質向上を実現します。このサービスは、製造業の課題を深く理解し、それに対する最適なデジタルソリューションを提供することで、企業が持続的な成長とイノベーションを達成できるようサポートします。
製造業ニュース解説
製造業、主に購買・調達部門にお勤めの方々に向けた情報を配信しております。
新任の方やベテランの方、管理職を対象とした幅広いコンテンツをご用意しております。
お問い合わせ
コストダウンが利益に直結する術だと理解していても、なかなか前に進めることができない状況。そんな時は、newjiのコストダウン自動化機能で大きく利益貢献しよう!
(β版非公開)