- お役立ち記事
- Optimization technology and efficiency techniques in plastic molding methods [Industry commentary]
月間77,185名の
製造業ご担当者様が閲覧しています*
*2025年2月28日現在のGoogle Analyticsのデータより
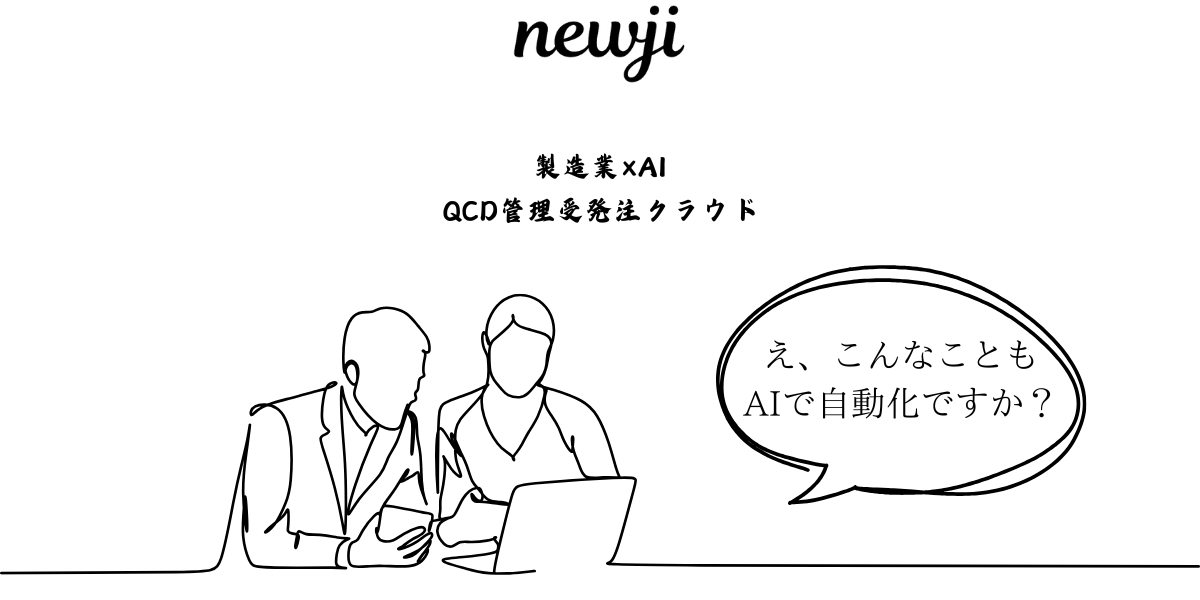
Optimization technology and efficiency techniques in plastic molding methods [Industry commentary]
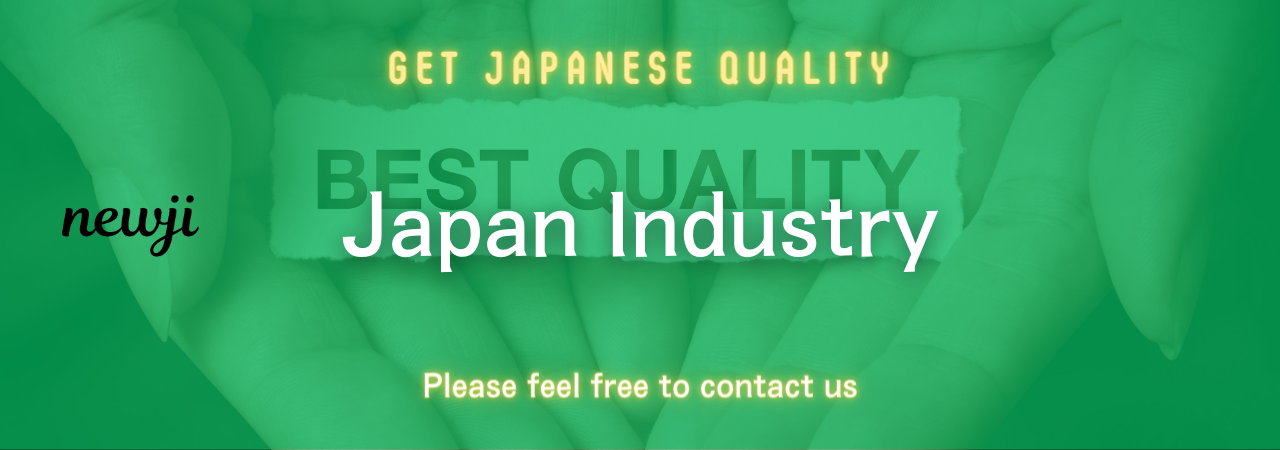
Plastic molding is a cornerstone in the manufacturing industry, shaping everyday products and complex components alike.
In an era where efficiency is crucial, exploring optimization technology and efficiency techniques in plastic molding methods becomes imperative for industries seeking to maximize productivity while minimizing waste and environmental impact.
目次
Understanding Plastic Molding
Plastic molding is a process that involves the shaping of plastic materials into desired forms or parts.
Various techniques fall under plastic molding, each suited for different applications and materials.
The most commonly used methods include injection molding, extrusion molding, blow molding, rotational molding, and compression molding.
Injection Molding
Injection molding is perhaps the most prevalent plastic molding technique.
It involves injecting molten plastic into a steel or aluminum mold under high pressure.
Once the plastic cools, it takes the shape of the mold cavity.
Extrusion Molding
Extrusion molding involves pushing molten plastic through a die to create long continuous shapes, such as pipes and sheets.
This method is ideal for producing items with a consistent cross-section.
Blow Molding
Blow molding is primarily used for creating hollow plastic products like bottles and containers.
The process involves inflating a heated plastic tube until it fills a mold and forms the desired shape.
Optimization Technology in Plastic Molding
Optimization technology in plastic molding seeks to refine the process to improve product quality, reduce cycle times, and enhance energy efficiency.
These technologies integrate advanced tools and software that monitor and adjust molding processes in real time.
Advanced Simulation Software
One key optimization tool is simulation software, which allows engineers to create virtual models of plastic parts and the molding process.
By simulating different scenarios, engineers can predict and mitigate issues like warping, shrinkage, and other defects before production starts.
This not only saves time but also reduces material waste and cost.
Sensor Technology and Data Analytics
Embedding sensors into mold systems to gather data on temperature, pressure, and humidity leads to more precise control over the molding process.
Data analytics then interpret this information, offering insights that facilitate process adjustments on-the-fly.
This dynamic control helps maintain consistent quality while minimizing rejects and rework.
Automated Equipment
The integration of automated machinery, such as robotic arms and conveyor systems, enhances the efficiency of plastic molding operations.
Automation reduces cycle times by performing tasks more quickly and accurately than manual labor.
Moreover, it minimizes human error and ensures a safer working environment.
Efficiency Techniques in Plastic Molding
Efficiency techniques focus on refining operational practices and utilizing innovative technologies to enhance productivity while conserving resources.
Lean Manufacturing Principles
Implementing lean manufacturing principles in plastic molding helps eliminate non-value-added activities.
By streamlining operations, reducing inventory, and improving workflow, manufacturers can significantly enhance production efficiency and quality.
Energy-Efficient Machinery
Investing in energy-efficient machinery reduces power consumption, resulting in lower operational costs and a smaller carbon footprint.
Modern equipment is designed to optimize energy use, employing technologies like variable frequency drives and efficient heating elements.
Material Selection and Recycling
Choosing the right material for a specific application can improve the efficiency of the molding process.
Using recycled plastics and bioplastics not only supports sustainability but can also lead to cost savings.
Manufacturers are increasingly incorporating recycling techniques to recover and reuse scrap materials, thereby minimizing waste.
Cycle Time Reduction
Reducing cycle time is critical for increasing productivity in plastic molding.
Techniques such as optimizing cooling times, utilizing quick-change tooling, and refining mold design can substantially decrease the time it takes to produce each part.
A focus on reducing cycle time leads to a direct increase in output without sacrificing quality.
Challenges in Optimization and Efficiency
Despite advancements in technology and techniques, several challenges persist in optimizing plastic molding processes.
Complexity of Processes
The complexity of the molding process means that even small deviations can impact product quality.
As manufacturers strive for efficiency, maintaining tight control over variables becomes increasingly challenging.
High Initial Costs
Investing in advanced technology, such as automated systems and high-tech machinery, requires significant capital.
While these investments often yield long-term savings, the upfront costs can be a barrier for smaller companies.
Skilled Workforce
Implementing advanced optimization and efficiency techniques requires skilled operators and engineers.
Training staff to effectively manage and maintain these systems can be a hurdle, particularly in regions with limited access to technical education.
The Future of Plastic Molding
The future of plastic molding is poised to embrace further advancements in technology and methodology.
As environmental concerns grow, the industry is likely to see a shift towards more sustainable practices, including biodegradable materials and innovative recycling solutions.
Digital Twins and AI Integration
The rise of digital twins and artificial intelligence (AI) is set to redefine optimization in plastic molding.
Digital twins allow manufacturers to create virtual replicas of physical processes, enabling real-time monitoring and adjustments.
AI can further enhance this by analyzing data to optimize operations and predict maintenance needs.
Customization and Flexibility
Demand for customized products will drive the need for flexible molding solutions.
Manufacturers will look for methods that can quickly adapt to different designs without significant downtime, ensuring they can meet customer demands efficiently.
In conclusion, optimization technology and efficiency techniques are revolutionizing plastic molding methods, driving improvements in quality, cost savings, and environmental sustainability.
As the industry evolves, embracing these advancements will be key to remaining competitive in a rapidly changing market.
資料ダウンロード
QCD管理受発注クラウド「newji」は、受発注部門で必要なQCD管理全てを備えた、現場特化型兼クラウド型の今世紀最高の受発注管理システムとなります。
ユーザー登録
受発注業務の効率化だけでなく、システムを導入することで、コスト削減や製品・資材のステータス可視化のほか、属人化していた受発注情報の共有化による内部不正防止や統制にも役立ちます。
NEWJI DX
製造業に特化したデジタルトランスフォーメーション(DX)の実現を目指す請負開発型のコンサルティングサービスです。AI、iPaaS、および先端の技術を駆使して、製造プロセスの効率化、業務効率化、チームワーク強化、コスト削減、品質向上を実現します。このサービスは、製造業の課題を深く理解し、それに対する最適なデジタルソリューションを提供することで、企業が持続的な成長とイノベーションを達成できるようサポートします。
製造業ニュース解説
製造業、主に購買・調達部門にお勤めの方々に向けた情報を配信しております。
新任の方やベテランの方、管理職を対象とした幅広いコンテンツをご用意しております。
お問い合わせ
コストダウンが利益に直結する術だと理解していても、なかなか前に進めることができない状況。そんな時は、newjiのコストダウン自動化機能で大きく利益貢献しよう!
(β版非公開)