- お役立ち記事
- Optimize alternative procurement processes to help purchasing departments ensure stability of material supply
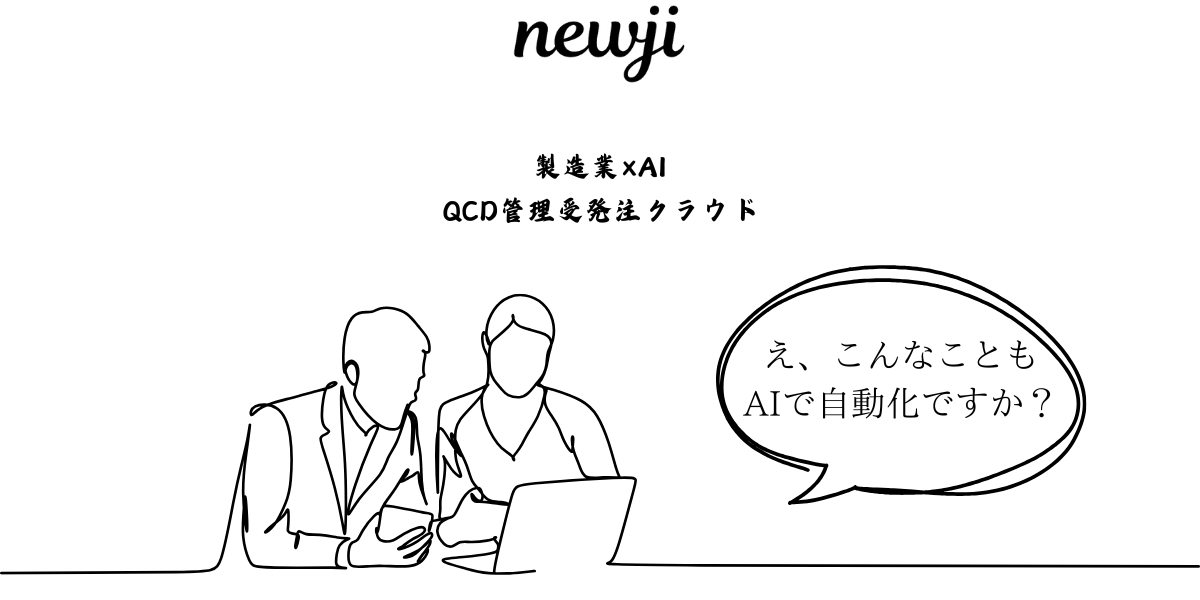
Optimize alternative procurement processes to help purchasing departments ensure stability of material supply
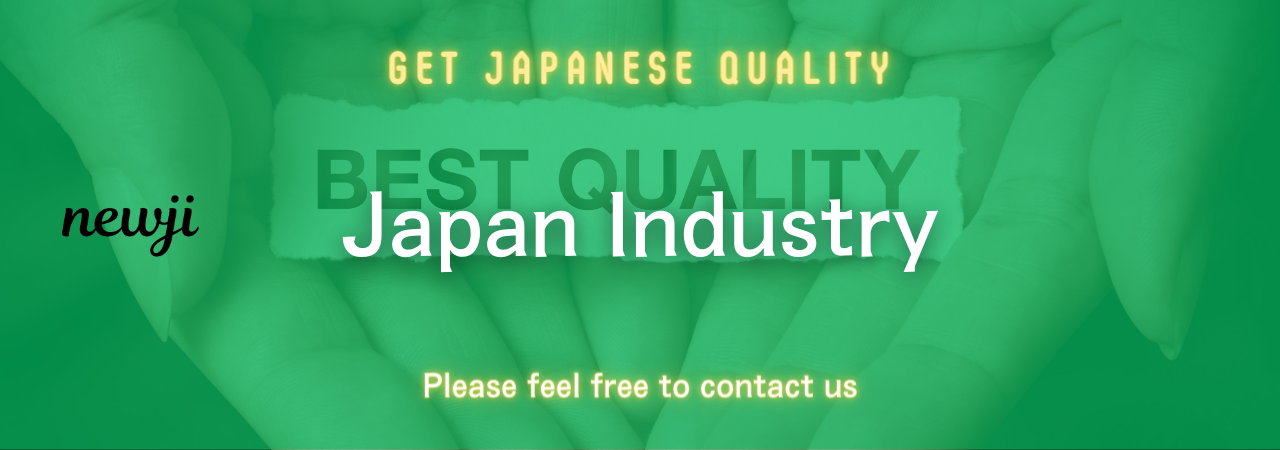
目次
Understanding Alternative Procurement Processes
Procurement is a crucial function in any organization, responsible for acquiring goods and services necessary for daily operations.
Traditional procurement methods have been used for decades to streamline this process.
However, in today’s dynamic business environment, unforeseen disruptions can occur that challenge these conventional approaches.
This is where alternative procurement processes come into play.
Alternative procurement processes refer to a range of methods and strategies employed to source materials and services outside the standard procedure.
These processes are designed to provide flexibility and adaptability, ensuring the continuous supply of necessary materials even in challenging circumstances.
By optimizing these alternative processes, purchasing departments can significantly enhance their capability to maintain stability in material supply.
The Importance of Stability in Material Supply
Having a stable supply of materials is essential for organizations to operate smoothly.
Interruptions or delays in material supply can lead to production halts, increased costs, and ultimately, dissatisfied customers.
Therefore, purchasing departments must prioritize strategies that ensure the uninterrupted flow of materials.
Stability in material supply also plays a pivotal role in maintaining relationships with suppliers.
When organizations are reliable in their orders and negotiations, it enhances trust and collaboration, leading to better deals and improved terms.
Thus, implementing alternative procurement processes can act as a safety net that safeguards against disruptions and maintains these crucial relationships.
Methods for Optimizing Alternative Procurement Processes
There are several strategies that organizations can implement to optimize their alternative procurement processes.
These methods focus on flexibility, risk management, and strategic planning.
Diversifying Supplier Base
One of the effective strategies is to diversify the supplier base.
Relying on a single supplier can be risky, as any disruption with that supplier can impact the entire supply chain.
By working with multiple suppliers, organizations can mitigate this risk and have backup options in case of any issues.
Implementing Strategic Sourcing
Strategic sourcing involves a detailed analysis of the procurement process to align it with the organization’s overall objectives.
It includes identifying cost-effective suppliers, understanding market dynamics, and evaluating risks.
Through strategic sourcing, purchasing departments can develop more resilient and adaptive procurement strategies.
Leveraging Technology
Incorporating technology into procurement processes can offer significant advantages.
Procurement software and platforms enable real-time tracking and data analysis, allowing purchasing departments to make informed decisions quickly.
Using predictive analytics, organizations can anticipate potential disruptions and plan accordingly.
Building Strong Supplier Relationships
Strong relationships with suppliers are key to a stable material supply chain.
By fostering open communication and collaboration, purchasing departments can work more closely with suppliers.
This ensures that any changes in demand or supply chain issues are addressed proactively.
Risk Assessment and Management
Identifying potential risks in the supply chain is crucial for developing effective alternative procurement processes.
Risks could include geopolitical factors, natural disasters, or market volatility.
By conducting thorough risk assessments, organizations can devise contingency plans that allow them to react swiftly when disruptions occur.
Benefits of Optimizing Alternative Procurement Processes
Optimizing alternative procurement processes offers several benefits, contributing to an organization’s overall efficiency and competitiveness.
Firstly, it provides greater flexibility, enabling organizations to adapt to changing conditions swiftly.
This agility is crucial in a world where supply chains are increasingly complex and vulnerable to disruptions.
Secondly, optimized processes can lead to cost savings.
By having a diverse supplier base and utilizing strategic sourcing, organizations can negotiate better prices and terms.
Technology-driven procurement can also identify efficiencies that reduce costs.
Thirdly, it enhances risk management capabilities.
Organizations that proactively prepare for disruptions are better positioned to maintain operations without significant setbacks.
This resilience is a competitive advantage in today’s fast-paced markets.
Finally, optimized procurement processes improve supplier relationships.
Reliable and strategic interactions foster trust and cooperation, leading to better service, innovation, and strategic partnerships.
Conclusion
In conclusion, optimizing alternative procurement processes is essential for purchasing departments aiming to ensure the stability of material supply.
As the business landscape continues to evolve, organizations must adapt their procurement strategies to address potential disruptions proactively.
By diversifying the supplier base, implementing strategic sourcing, leveraging technology, building robust supplier relationships, and conducting risk assessments, organizations can create a resilient procurement framework.
The benefits are clear: increased flexibility, cost savings, enhanced risk management, and improved supplier relationships.
Purchasing departments that embrace these strategies will be better equipped to maintain operations smoothly, satisfy customer demand, and thrive in a competitive environment.
As such, focusing on alternative procurement processes is not just beneficial but vital for long-term success.
資料ダウンロード
QCD調達購買管理クラウド「newji」は、調達購買部門で必要なQCD管理全てを備えた、現場特化型兼クラウド型の今世紀最高の購買管理システムとなります。
ユーザー登録
調達購買業務の効率化だけでなく、システムを導入することで、コスト削減や製品・資材のステータス可視化のほか、属人化していた購買情報の共有化による内部不正防止や統制にも役立ちます。
NEWJI DX
製造業に特化したデジタルトランスフォーメーション(DX)の実現を目指す請負開発型のコンサルティングサービスです。AI、iPaaS、および先端の技術を駆使して、製造プロセスの効率化、業務効率化、チームワーク強化、コスト削減、品質向上を実現します。このサービスは、製造業の課題を深く理解し、それに対する最適なデジタルソリューションを提供することで、企業が持続的な成長とイノベーションを達成できるようサポートします。
オンライン講座
製造業、主に購買・調達部門にお勤めの方々に向けた情報を配信しております。
新任の方やベテランの方、管理職を対象とした幅広いコンテンツをご用意しております。
お問い合わせ
コストダウンが利益に直結する術だと理解していても、なかなか前に進めることができない状況。そんな時は、newjiのコストダウン自動化機能で大きく利益貢献しよう!
(Β版非公開)