- お役立ち記事
- Optimizing Blow Molding: Balancing Efficiency and Quality
Optimizing Blow Molding: Balancing Efficiency and Quality
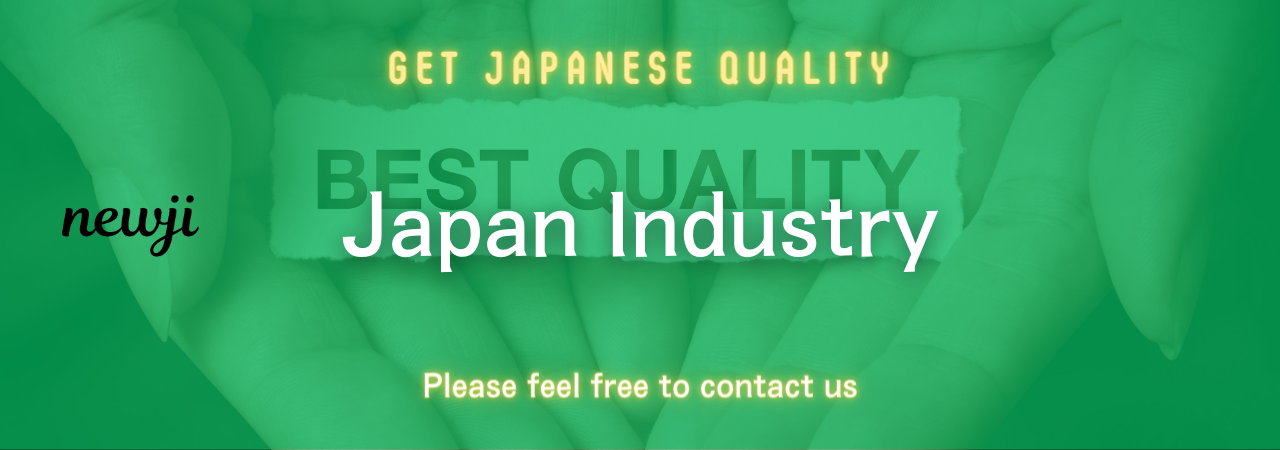
Blow molding is a fascinating process that transforms plastic into everyday items like bottles and containers.
Optimizing this process can significantly improve both efficiency and quality, which are crucial for any manufacturing operation.
This article will explore various ways to achieve this balance.
目次
Understanding the Blow Molding Process
Blow molding involves heating plastic until it becomes a molten state and then blowing it into a mold to form a hollow object.
There are three main types of blow molding: extrusion blow molding, injection blow molding, and injection stretch blow molding.
Each method has its own advantages and uses.
Understanding these methods helps in identifying areas where efficiency and quality can be optimized.
Extrusion Blow Molding
In extrusion blow molding, a plastic parison (tube) is extruded and then clamped into a mold.
Air is then blown into the parison, inflating it to take the shape of the mold.
This method is often used for making larger containers like jugs and fuel tanks.
Injection Blow Molding
Injection blow molding starts with preforming a heated plastic material into a preform.
The preform is then transferred to a blow mold where air is injected, causing the preform to expand to the shape of the mold.
This method is ideal for producing high-quality, small to medium-sized bottles and jars.
Injection Stretch Blow Molding
This method involves stretching the plastic preform both axially and radially before blowing air into it.
This results in stronger containers, often used for carbonated beverage bottles.
Improving Energy Efficiency
Energy consumption is a significant factor in the blow molding process.
Optimizing energy efficiency can thus lead to considerable cost savings and reduced environmental impact.
Machine Efficiency
Modern blow molding machines are designed to consume less energy.
If you are using older equipment, consider upgrading to newer, more energy-efficient models.
Preventative maintenance also ensures machines run efficiently, reducing downtime and energy wastage.
Insulation and Heat Management
Proper insulation of heating elements can minimize energy loss.
Improving the heat management systems in your blow molding machines allows for more precise control, ensuring less energy is wasted.
Enhancing Quality Control
Consistent quality is essential for customer satisfaction and regulatory compliance.
Optimizing quality control processes ensures that every product meets stringent standards.
Automated Inspection Systems
Automated inspection systems can be integrated into the production line to monitor and detect defects in real-time.
High-speed cameras and sensors can catch defects that are sometimes missed by the human eye, ensuring a higher quality output.
Material Selection
The choice of plastic resin can drastically affect the final product quality.
Consult with material scientists and suppliers to find the most suitable resin for your specific application, ensuring it meets all functional and aesthetic requirements.
Optimizing Production Speed
A faster production line means more products can be made in less time.
However, increasing speed should not compromise quality.
Cycle Time Reduction
Cycle time in blow molding refers to the total time taken for one complete cycle of producing a molded item.
Analyzing each component of this cycle can reveal areas where time can be cut without sacrificing quality.
Reducing mold cooling time, for example, can enhance speed.
Process Automation
Integrating more automation into the blow molding process can significantly speed up production.
Automated systems can handle tasks more quickly and accurately than human operators, from loading materials to packaging the final product.
Reducing Waste and Recycling
Waste reduction is not only good for the environment but also for your bottom line.
Optimizing the blow molding process to minimize waste can have substantial benefits.
Material Reuse
Scrap plastic from the blow molding process can often be recycled and reused.
Regrinding and blending scrap with virgin material can produce high-quality products while reducing material costs.
Precision Molding
Precision in the blow molding process minimizes waste by ensuring that only the necessary amount of plastic is used.
Advanced computer-aided design (CAD) software allows for precise mold creation, reducing excess material use.
Employee Training and Skill Development
Well-trained employees are essential for optimizing the blow molding process.
Regular training programs keep staff updated on the latest technologies and best practices.
Regular Training Sessions
Organize regular training sessions focusing on machine operation, maintenance, and quality control.
Keeping the workforce engaged and knowledgeable ensures a more efficient production line.
Encourage Continuous Improvement
Create a culture that encourages continuous improvement.
Employees should be empowered to suggest and implement process optimizations.
Setting up teams to analyze production data and develop improvements can lead to substantial efficiency gains.
Leveraging Data Analytics
Finally, data analytics can provide invaluable insights into the blow molding process.
By collecting and analyzing production data, you can identify inefficiencies and areas for improvement.
Real-time Monitoring
Implementing real-time monitoring systems can help track various parameters, such as temperature, pressure, and cycle time.
Analyzing this data allows for timely adjustments, ensuring optimal performance.
Predictive Maintenance
Data analytics can also be used for predictive maintenance.
By analyzing patterns and historical data, you can predict when a machine might fail and perform maintenance before it does.
This reduces downtime and maintains production efficiency.
Conclusion
Optimizing blow molding involves a multifaceted approach, focusing on improving energy efficiency, enhancing quality control, and speeding up production.
Reducing waste and fostering a skilled workforce are equally critical.
Leveraging data analytics can provide the insights needed for continual process improvement.
Balancing efficiency and quality in the blow molding process ensures sustainable growth and customer satisfaction, making it a worthwhile investment.
資料ダウンロード
QCD調達購買管理クラウド「newji」は、調達購買部門で必要なQCD管理全てを備えた、現場特化型兼クラウド型の今世紀最高の購買管理システムとなります。
ユーザー登録
調達購買業務の効率化だけでなく、システムを導入することで、コスト削減や製品・資材のステータス可視化のほか、属人化していた購買情報の共有化による内部不正防止や統制にも役立ちます。
NEWJI DX
製造業に特化したデジタルトランスフォーメーション(DX)の実現を目指す請負開発型のコンサルティングサービスです。AI、iPaaS、および先端の技術を駆使して、製造プロセスの効率化、業務効率化、チームワーク強化、コスト削減、品質向上を実現します。このサービスは、製造業の課題を深く理解し、それに対する最適なデジタルソリューションを提供することで、企業が持続的な成長とイノベーションを達成できるようサポートします。
オンライン講座
製造業、主に購買・調達部門にお勤めの方々に向けた情報を配信しております。
新任の方やベテランの方、管理職を対象とした幅広いコンテンツをご用意しております。
お問い合わせ
コストダウンが利益に直結する術だと理解していても、なかなか前に進めることができない状況。そんな時は、newjiのコストダウン自動化機能で大きく利益貢献しよう!
(Β版非公開)