- お役立ち記事
- Optimizing Clean Processes in Manufacturing with CIP Implementation
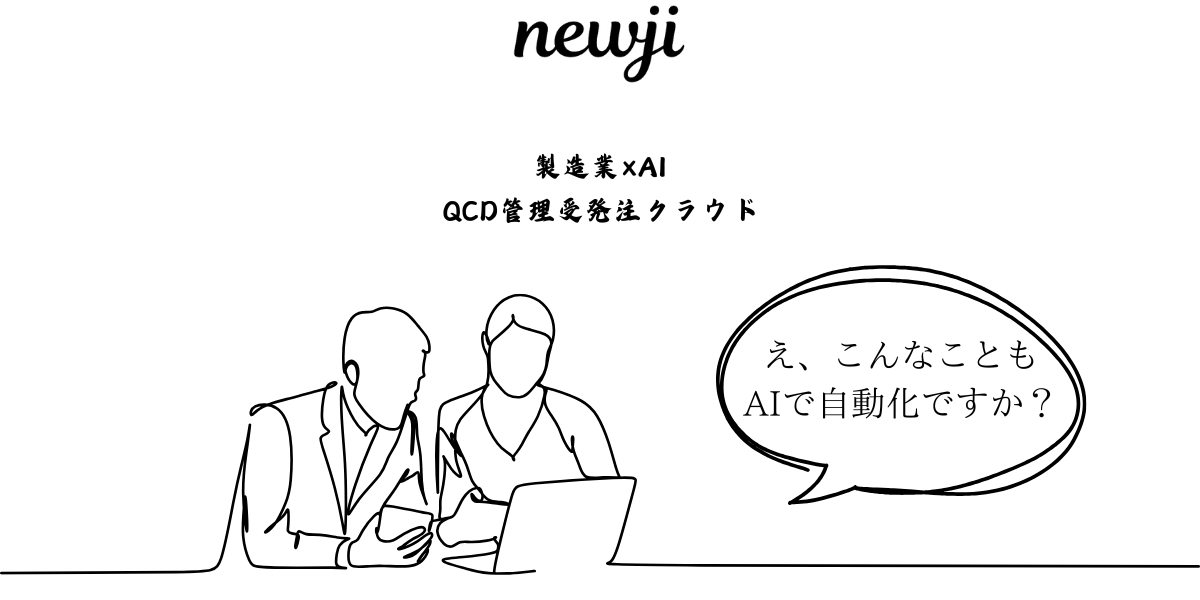
Optimizing Clean Processes in Manufacturing with CIP Implementation
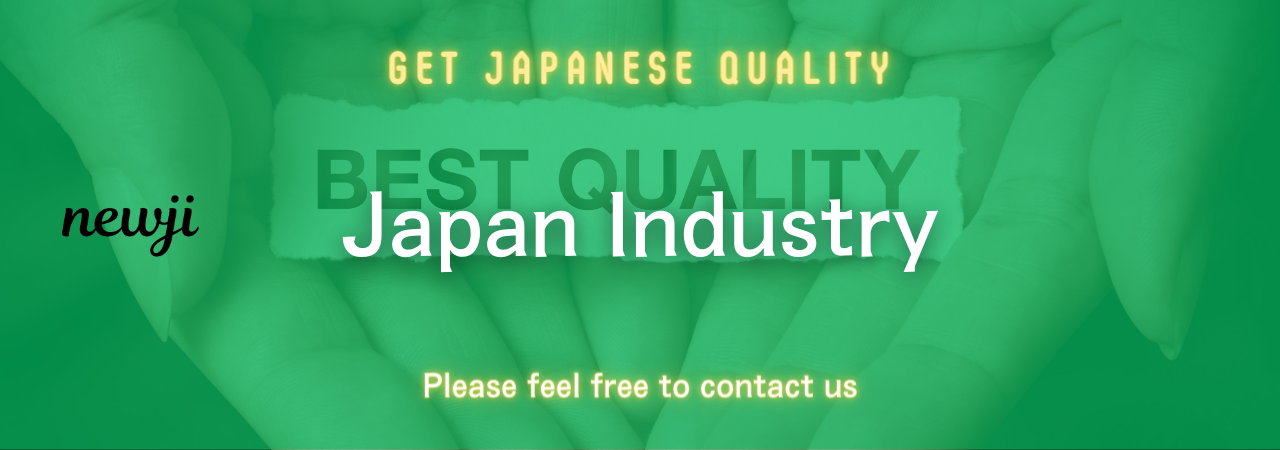
In today’s competitive manufacturing landscape, efficiency is crucial for maintaining a leading edge.
Industries are turning toward innovative methods to enhance their processes and ensure high-quality output.
One effective strategy is the implementation of Clean-in-Place (CIP) systems.
CIP is a method of cleaning the interior surfaces of pipes, vessels, and other equipment without disassembling them.
This article dives deep into how CIP implementation can optimize clean processes in manufacturing.
目次
Understanding CIP Systems
What is CIP?
Clean-in-Place (CIP) is an automated method of industrial cleaning.
CIP systems are designed to clean the internal surfaces of production equipment efficiently.
Unlike traditional cleaning methods, CIP does not require dismantling machinery, thus saving time and reducing labor costs.
This automated process utilizes a flush of cleaning agents, followed by a rinse with water, ensuring thorough sanitation.
Key Components of CIP Systems
Several components form the backbone of a CIP system:
1. **Cleaning Solutions**
2. **Delivery Systems**
3. **Control Units**
Cleaning solutions often comprise detergents and sanitizers, tailored to remove specific contaminants.
Delivery systems ensure these solutions reach all parts of the equipment.
Control units monitor and regulate parameters such as temperature, flow rate, and concentration of cleaning agents.
Advantages of Implementing CIP in Manufacturing
Efficiency and Time-Saving
One of the primary advantages of CIP systems is the significant reduction in cleaning time.
Manufacturers can clean their equipment without disassembly, which drastically reduces downtime.
This leads to higher production rates and increased efficiency.
Consistency and Reliability
CIP systems offer a consistent and reliable cleaning process.
Manual cleaning can be prone to human error, but CIP systems ensure that each cycle is uniform.
This consistency is critical for industries such as pharmaceuticals and food manufacturing, where hygiene standards are stringent.
Cost-Effectiveness
Although the initial investment in CIP systems can be high, the long-term benefits outweigh the costs.
Reduced labor, shorter cleaning times, and extended equipment lifespan contribute to overall cost savings.
Moreover, efficient use of cleaning agents minimizes waste, further cutting down expenses.
CIP in Different Manufacturing Industries
Food and Beverage Industry
In the food and beverage industry, hygiene is paramount.
CIP systems help maintain the cleanliness of mixing tanks, pipelines, and filling machines.
This ensures product safety and compliance with health regulations.
For instance, dairy manufacturers use CIP to avoid contamination and preserve the quality of milk and dairy products.
Pharmaceutical Industry
In pharmaceutical manufacturing, contamination can lead to serious health risks.
CIP systems ensure that reactors, fermenters, and transfer lines are sterile.
This is vital for maintaining product integrity and meeting regulatory requirements.
Automated cleaning also helps in reducing the risk of cross-contamination between different batches.
Brewing Industry
CIP systems play a crucial role in the brewing industry by maintaining the cleanliness of fermentation tanks and bottling lines.
A clean brewing process is essential to producing high-quality beer free from unwanted tastes and microorganisms.
CIP systems help achieve this consistently and efficiently.
Steps to Implement CIP Systems
Assess Your Needs
Before implementing a CIP system, it’s essential to assess your specific needs.
Consider the type of contaminants you need to clean, the surfaces involved, and the required hygiene standards.
This assessment will help in selecting the appropriate CIP system and cleaning agents.
Design and Planning
Effective CIP systems require careful design and planning.
Identify the equipment that needs cleaning, and plan the arrangement of the CIP system accordingly.
Ensure that the system is compatible with your existing infrastructure for seamless integration.
Installation and Training
Once you have your design and plan in place, proceed with the installation.
It’s crucial to work with experienced engineers to ensure the system is installed correctly and safely.
After installation, conduct training sessions for your staff to familiarize them with the new system.
This will ensure they can operate it efficiently and handle any troubleshooting if needed.
Validation and Monitoring
After the CIP system is up and running, validate its effectiveness.
Regularly monitor the cleaning process to ensure it meets the required standards.
Use testing and feedback mechanisms to fine-tune the system for optimal performance.
Best Practices for Maintaining CIP Systems
Regular Maintenance
Like any other system, CIP systems require regular maintenance to function effectively.
Scheduled inspections and preventive maintenance can help identify and resolve potential issues before they escalate.
Record Keeping
Maintain detailed records of every CIP cycle, including parameters like temperature, duration, and chemical concentrations.
These records are valuable for troubleshooting and ensuring compliance with industry regulations.
Continuous Improvement
Always look for ways to improve your CIP processes.
Stay updated with the latest advancements in cleaning agents and CIP technology.
Incorporate feedback from staff and periodic audits to refine your cleaning protocols continually.
Optimizing clean processes in manufacturing with CIP implementation is a strategic move that can significantly enhance efficiency, consistency, and safety in diverse industries.
By understanding CIP systems and following best practices, manufacturers can maintain high hygiene standards, reduce downtime, and achieve cost savings, thereby securing a competitive advantage in their markets.
資料ダウンロード
QCD調達購買管理クラウド「newji」は、調達購買部門で必要なQCD管理全てを備えた、現場特化型兼クラウド型の今世紀最高の購買管理システムとなります。
ユーザー登録
調達購買業務の効率化だけでなく、システムを導入することで、コスト削減や製品・資材のステータス可視化のほか、属人化していた購買情報の共有化による内部不正防止や統制にも役立ちます。
NEWJI DX
製造業に特化したデジタルトランスフォーメーション(DX)の実現を目指す請負開発型のコンサルティングサービスです。AI、iPaaS、および先端の技術を駆使して、製造プロセスの効率化、業務効率化、チームワーク強化、コスト削減、品質向上を実現します。このサービスは、製造業の課題を深く理解し、それに対する最適なデジタルソリューションを提供することで、企業が持続的な成長とイノベーションを達成できるようサポートします。
オンライン講座
製造業、主に購買・調達部門にお勤めの方々に向けた情報を配信しております。
新任の方やベテランの方、管理職を対象とした幅広いコンテンツをご用意しております。
お問い合わせ
コストダウンが利益に直結する術だと理解していても、なかなか前に進めることができない状況。そんな時は、newjiのコストダウン自動化機能で大きく利益貢献しよう!
(Β版非公開)