- お役立ち記事
- Optimizing Control Systems in Manufacturing with DCS Implementation
Optimizing Control Systems in Manufacturing with DCS Implementation
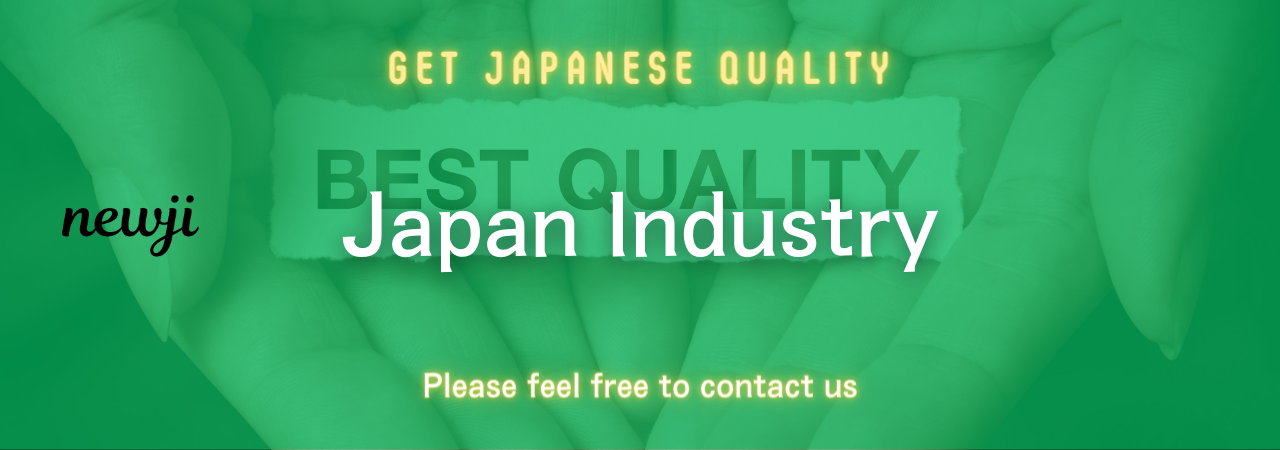
In today’s manufacturing landscape, maintaining an efficient and reliable control system is crucial for success.
One of the most effective ways to optimize these systems is through the implementation of Distributed Control Systems (DCS).
DCS provides a robust solution by decentralizing control and offering better management capabilities.
目次
Understanding Distributed Control Systems
Distributed Control Systems, or DCS, are automated control systems that are dispersed throughout a manufacturing facility.
Instead of having a single centralized control unit, a DCS divides the control tasks into smaller, more manageable pieces, which are then distributed across various locations.
Each section of the production process can be monitored and controlled independently.
This distributed nature helps in improving reliability and response times.
Furthermore, it allows for better management of complex processes.
Benefits of Implementing DCS in Manufacturing
1. Enhanced Reliability and Redundancy
One of the primary advantages of DCS is the increase in reliability.
By distributing the control functions, the system ensures that no single point of failure can disrupt the entire operation.
If one component fails, other parts of the system can continue to operate, ensuring uninterrupted production.
2. Improved Process Control
DCS offers refined process control capabilities.
Since control functions are spread out, each segment of the manufacturing process can be fine-tuned more precisely.
This leads to improved efficiency, better product quality, and reduced waste.
3. Scalability and Flexibility
As your manufacturing needs grow, DCS provides the flexibility to scale operations.
Adding new control points or reconfiguring existing ones is straightforward, making it easier to adapt to changing production demands.
4. Better Data Management
DCS systems are designed to handle large amounts of data from various control points.
They offer real-time data collection and analysis, which aids in making informed decisions.
This data-centric approach can lead to significant improvements in productivity and efficiency.
Steps to Implementing a DCS
1. Assessing Your Current System
The first step in implementing a DCS is to conduct a thorough assessment of your current control system.
Identify areas where DCS can bring the most benefits.
Understand the limitations of your existing setup and outline the specific needs of your manufacturing process.
2. Selecting the Right DCS
There are various DCS options available on the market.
Selecting the right one depends on your specific requirements.
Consider factors such as scalability, compatibility with existing equipment, and support services.
Consulting with an expert can help in making an informed decision.
3. Planning the Integration
Planning is crucial for successful DCS implementation.
Develop a detailed plan that outlines the steps involved in integrating the new system with your existing operations.
Ensure that you have a clear timeline and that all stakeholders are on board.
4. Training Your Team
Implementing a new control system means that your team will need to be trained on how to use it.
Provide comprehensive training programs to ensure that everyone understands how to operate the new system efficiently.
5. Testing and Calibration
Before going live, conduct extensive testing and calibration.
This step helps in identifying and correcting any issues that may arise.
Ensure that the system is operating as expected and that all control points are functioning correctly.
Overcoming Challenges in DCS Implementation
1. Initial Costs
One of the barriers to DCS implementation is the initial cost.
However, the long-term benefits often outweigh the upfront investment.
Consider the potential ROI in terms of improved efficiency, reduced downtime, and better product quality.
2. Integration with Legacy Systems
Integrating DCS with existing legacy systems can be challenging.
Ensuring compatibility and seamless integration is key.
Working with experienced professionals can help in overcoming these hurdles.
3. Cybersecurity Concerns
With the rise of connected systems, cybersecurity is a significant concern.
Implementing robust security measures is essential to protect your DCS from potential threats.
Regular updates and security protocols can help in maintaining a secure system.
Conclusion
Optimizing control systems in manufacturing with DCS implementation offers numerous benefits.
From enhanced reliability and improved process control to better data management and scalability, DCS can revolutionize your manufacturing operations.
Careful planning, thorough assessment, and proper training are crucial for successful implementation.
While there are challenges to overcome, the long-term advantages make DCS a worthwhile investment for any manufacturing facility.
By embracing this technology, you can achieve higher efficiency, better product quality, and a more resilient manufacturing process.
資料ダウンロード
QCD調達購買管理クラウド「newji」は、調達購買部門で必要なQCD管理全てを備えた、現場特化型兼クラウド型の今世紀最高の購買管理システムとなります。
ユーザー登録
調達購買業務の効率化だけでなく、システムを導入することで、コスト削減や製品・資材のステータス可視化のほか、属人化していた購買情報の共有化による内部不正防止や統制にも役立ちます。
NEWJI DX
製造業に特化したデジタルトランスフォーメーション(DX)の実現を目指す請負開発型のコンサルティングサービスです。AI、iPaaS、および先端の技術を駆使して、製造プロセスの効率化、業務効率化、チームワーク強化、コスト削減、品質向上を実現します。このサービスは、製造業の課題を深く理解し、それに対する最適なデジタルソリューションを提供することで、企業が持続的な成長とイノベーションを達成できるようサポートします。
オンライン講座
製造業、主に購買・調達部門にお勤めの方々に向けた情報を配信しております。
新任の方やベテランの方、管理職を対象とした幅広いコンテンツをご用意しております。
お問い合わせ
コストダウンが利益に直結する術だと理解していても、なかなか前に進めることができない状況。そんな時は、newjiのコストダウン自動化機能で大きく利益貢献しよう!
(Β版非公開)