- お役立ち記事
- Optimizing Control Systems in Manufacturing with DCS Implementation
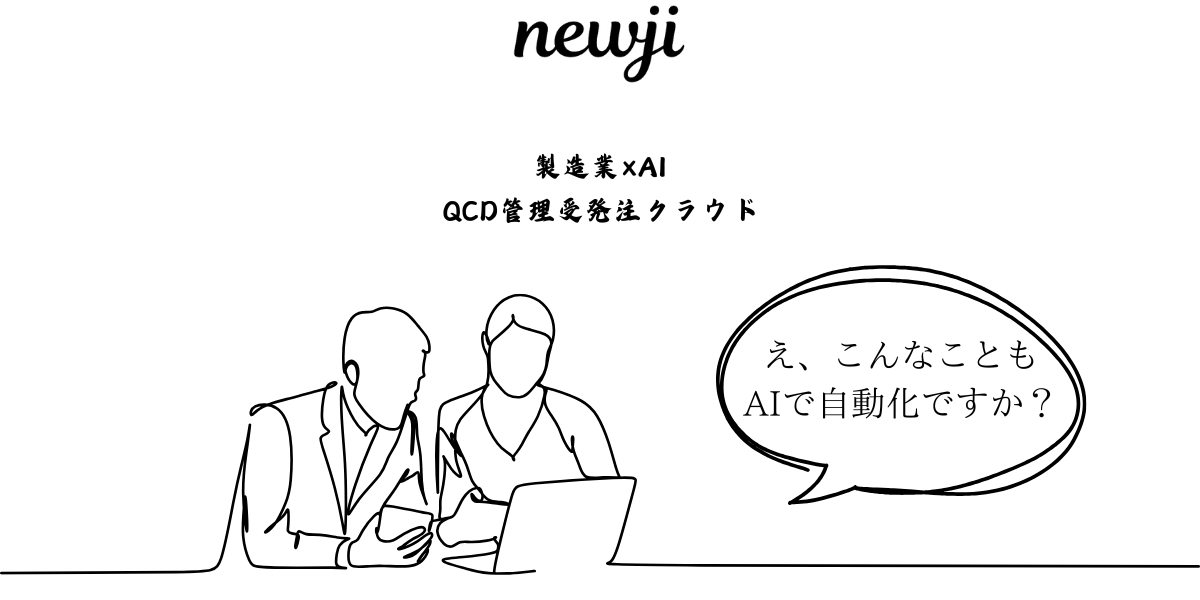
Optimizing Control Systems in Manufacturing with DCS Implementation
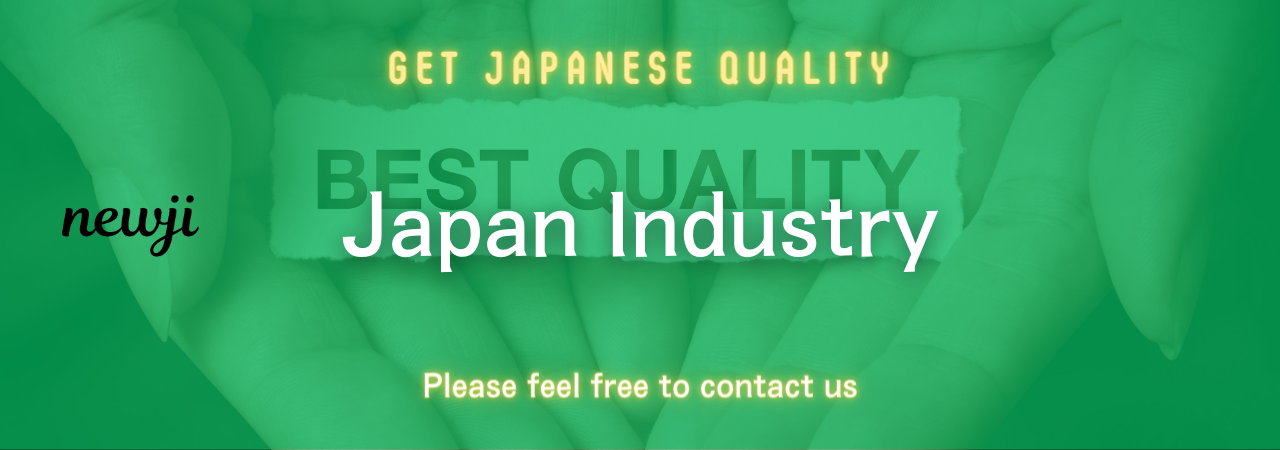
Control systems play a crucial role in the efficiency of manufacturing processes. Through the years, industries have continually sought ways to optimize these systems to ensure precision, reliability, and cost-effectiveness. One of the most effective strategies for achieving this optimization is by implementing Distributed Control Systems (DCS). This article explores how DCS implementation can optimize control systems in manufacturing.
目次
What is a Distributed Control System (DCS)?
A Distributed Control System (DCS) is a control system in which the controller elements are distributed throughout the system, rather than being centralized in one location.
These systems integrate and manage different parts of a manufacturing process using a network of interconnected controllers and computers.
DCS systems are extensively used in industries like chemical manufacturing, power generation, and food processing.
They provide a systematic approach to monitoring and controlling various functions and processes in a plant, thereby enhancing efficiency and productivity.
Advantages of DCS in Manufacturing
Improved Reliability and Availability
One of the standout benefits of DCS is its high reliability and availability.
Instead of relying on a central controller, the distributed nature allows for redundancies.
If one controller fails, others can assume its role, thus minimizing the risk of complete system failure and downtime.
Enhanced Scalability
DCS systems are highly scalable.
This means that as a manufacturing plant grows or introduces new processes, the control system can easily be expanded.
This scalability ensures that the manufacturing operations continue smoothly, without the need for an entire system overhaul.
Flexibility in Control
With DCS, manufacturers can control different processes within the same system.
This flexibility is particularly beneficial for industries that require complex and varied operations.
It also allows for easier modifications and adjustments to the control system as processes evolve.
Real-time Data Processing
Real-time data processing is another significant advantage of DCS implementation.
By continuously collecting and analyzing data from various parts of the manufacturing process, manufacturers can make informed decisions quickly.
This leads to improved process control and efficiency.
Cost Efficiency
Implementing a DCS can lead to substantial cost savings.
The system’s ability to optimize processes reduces waste, lowers energy consumption, and minimizes downtime.
Although the initial investment might be significant, the long-term cost benefits are substantial.
How to Implement DCS in Manufacturing
Assessment and Planning
The initial step in implementing a DCS is to assess the current control systems and identify areas for improvement.
This involves analyzing existing processes, pinpointing inefficiencies, and understanding specific requirements.
A comprehensive plan should then be developed, outlining the goals, budget, and timeline for the DCS implementation.
Design and Configuration
In the design phase, the DCS architecture is created to suit the plant’s specific needs.
This includes selecting appropriate hardware and software components, as well as configuring the system to facilitate smooth communication between different controllers.
Attention to detail is critical during this phase to ensure that the system meets all operational requirements.
Installation and Integration
Once the design is finalized, the next step is to install and integrate the system.
This may involve upgrading or replacing existing equipment, setting up network connections, and ensuring that all components are properly configured.
Integration must be performed carefully to avoid disrupting ongoing manufacturing processes.
Testing and Validation
After installation, rigorous testing is necessary to validate the system’s functionality.
This includes performing various operational tests to ensure that the DCS behaves as expected under different conditions.
Any issues identified during this phase should be addressed promptly to ensure smooth operation once the system goes live.
Training and Support
Proper training for personnel is essential for the successful implementation of a DCS.
Operators and technicians must be familiar with the system’s operations and troubleshooting procedures.
Ongoing support and maintenance are also crucial to address any issues that may arise and to keep the system operating efficiently.
Case Studies: Successful DCS Implementation in Manufacturing
Case Study 1: Chemical Manufacturing Plant
A large chemical manufacturing plant implemented a DCS to enhance control over its intricate production processes.
The system’s real-time data processing capabilities allowed operators to monitor and adjust processes more effectively.
As a result, the plant experienced a significant reduction in waste and downtime, leading to considerable cost savings.
Case Study 2: Food Processing Industry
In the food processing industry, a company implemented a DCS to manage its diverse and complex operations.
The flexibility of the DCS allowed the company to control different processes within the same system, improving overall efficiency.
Additionally, the real-time data insights helped in maintaining stringent quality standards.
Case Study 3: Power Generation Plant
A power generation plant faced challenges with outdated control systems that led to frequent downtime and high maintenance costs.
By implementing a DCS, the plant achieved improved reliability and availability, with the system’s redundancy features significantly reducing the risk of complete system failure.
This led to enhanced operational efficiency and lower maintenance costs.
Challenges in DCS Implementation
Despite the numerous benefits, implementing a DCS is not without challenges.
Initial Cost
The initial investment for DCS implementation can be substantial, which may be a barrier for some companies.
However, the long-term benefits often outweigh the initial costs.
Complex Integration
Integrating a DCS into an existing system can be complex and may require significant changes to current infrastructure.
Careful planning and execution are necessary to mitigate any disruptions.
Training Requirements
Personnel must be adequately trained to operate and maintain the new system.
This may involve a steep learning curve, particularly if the existing system is vastly different from the DCS.
Conclusion
Implementing a Distributed Control System (DCS) in manufacturing can lead to significant improvements in efficiency, reliability, and cost-effectiveness.
By understanding the advantages and challenges associated with DCS, manufacturers can better plan and execute its implementation.
Through strategic assessment, design, installation, and ongoing support, DCS can transform manufacturing operations and pave the way for future growth and success.
資料ダウンロード
QCD調達購買管理クラウド「newji」は、調達購買部門で必要なQCD管理全てを備えた、現場特化型兼クラウド型の今世紀最高の購買管理システムとなります。
ユーザー登録
調達購買業務の効率化だけでなく、システムを導入することで、コスト削減や製品・資材のステータス可視化のほか、属人化していた購買情報の共有化による内部不正防止や統制にも役立ちます。
NEWJI DX
製造業に特化したデジタルトランスフォーメーション(DX)の実現を目指す請負開発型のコンサルティングサービスです。AI、iPaaS、および先端の技術を駆使して、製造プロセスの効率化、業務効率化、チームワーク強化、コスト削減、品質向上を実現します。このサービスは、製造業の課題を深く理解し、それに対する最適なデジタルソリューションを提供することで、企業が持続的な成長とイノベーションを達成できるようサポートします。
オンライン講座
製造業、主に購買・調達部門にお勤めの方々に向けた情報を配信しております。
新任の方やベテランの方、管理職を対象とした幅広いコンテンツをご用意しております。
お問い合わせ
コストダウンが利益に直結する術だと理解していても、なかなか前に進めることができない状況。そんな時は、newjiのコストダウン自動化機能で大きく利益貢献しよう!
(Β版非公開)