- お役立ち記事
- Optimizing Data Collection in Manufacturing Processes with IoT Devices
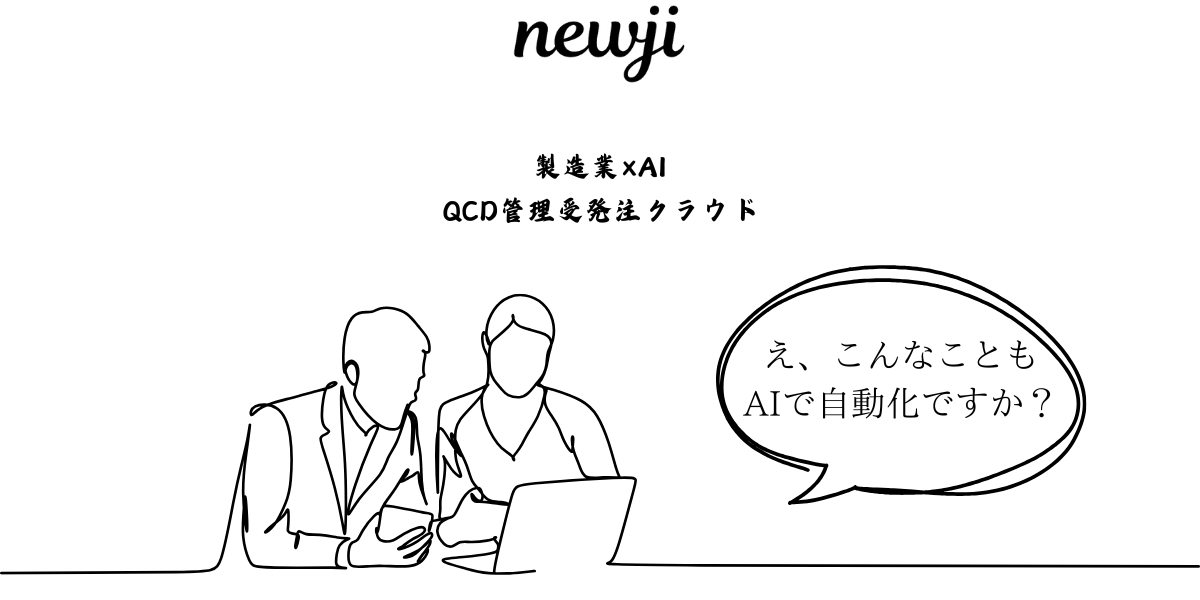
Optimizing Data Collection in Manufacturing Processes with IoT Devices
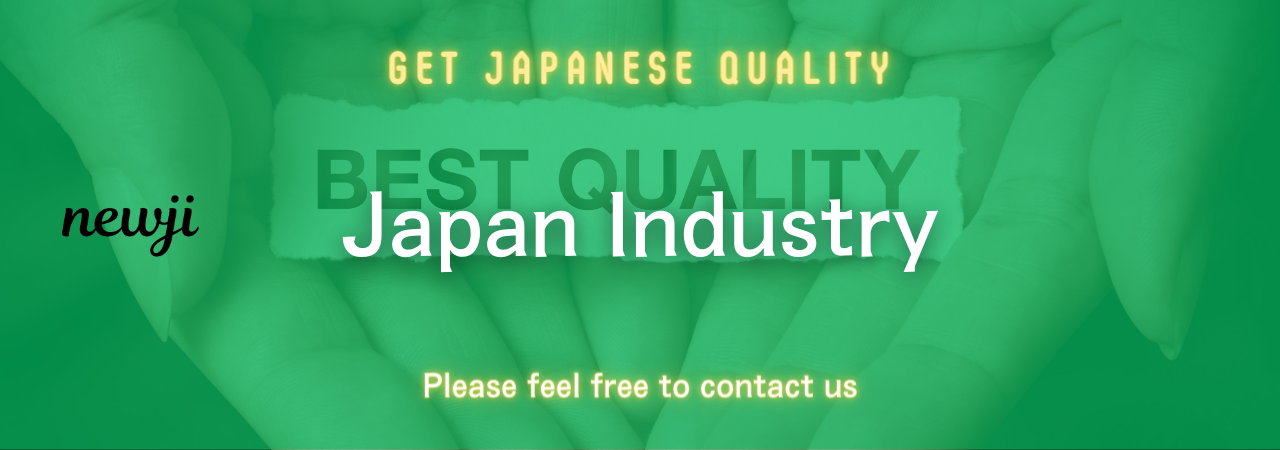
The manufacturing industry is evolving rapidly with the integration of new technologies. One of the most influential advancements is the use of IoT (Internet of Things) devices in optimizing data collection processes.
IoT devices are tools embedded with sensors and software that can connect and exchange data over the internet.
These devices have enabled manufacturers to collect, analyze, and act on data more efficiently than ever before.
目次
What is IoT?
To understand the impact of IoT on manufacturing processes, it’s essential to know what IoT actually is.
IoT refers to a network of connected devices that communicate and share data with each other.
These devices range from everyday household items like smart fridges to complex industrial machines.
In the context of manufacturing, IoT devices can include sensors, RFID tags, and actuators, among other things.
The Role of IoT in Manufacturing
The role of IoT in manufacturing cannot be overstated.
These devices gather data from various stages of the production process, allowing for real-time monitoring and analysis.
This data is crucial for making informed decisions, reducing downtime, and improving overall efficiency.
Enhancing Quality Control
IoT devices play a significant role in enhancing quality control.
Sensors can monitor the quality of raw materials and finished products in real-time.
This allows for immediate detection of defects and ensures that the products meet the required standards.
Automated systems can even halt production if they detect subpar quality, reducing waste and ensuring customer satisfaction.
Reducing Downtime
Another essential benefit of IoT in manufacturing is the reduction of downtime.
Predictive maintenance is made possible through the data collected by IoT devices.
By analyzing this data, manufacturers can predict when equipment is likely to fail and perform maintenance before it actually happens.
This proactive approach minimizes unexpected downtime and keeps the production line running smoothly.
Improving Supply Chain Management
IoT devices also improve supply chain management.
Incorporating IoT technology in the supply chain allows for real-time tracking of materials and products.
RFID tags and GPS devices can provide accurate information about the location and condition of shipments.
This transparency helps in better inventory management and reduces the risk of stockouts and overstock.
Optimizing Energy Usage
Energy consumption is a critical factor in manufacturing.
IoT devices enable manufacturers to monitor and optimize energy usage across the production process.
Sensors can provide real-time data on energy consumption, allowing for adjustments to be made to reduce waste and lower costs.
Energy-efficient practices not only save money but also contribute to environmental sustainability.
Data-Driven Decision Making
The data collected by IoT devices is invaluable for decision-making.
Manufacturers can analyze this data to gain insights into various aspects of the production process.
These insights can help in identifying bottlenecks, optimizing operations, and improving product design.
Real-Time Analytics
Real-time analytics provided by IoT devices enable manufacturers to respond quickly to changes in the production process.
This agility is crucial in a fast-paced industry where delays can be costly.
With real-time data, manufacturers can make instantaneous adjustments, ensuring that the production process remains efficient and effective.
Historical Data Analysis
In addition to real-time data, IoT devices also collect historical data.
This data can be analyzed to identify trends and patterns over time.
By studying historical data, manufacturers can forecast future demands, plan for seasonal variations, and make informed decisions about equipment upgrades.
Challenges in Implementing IoT in Manufacturing
While the benefits of IoT in manufacturing are significant, there are also challenges to consider.
Implementing IoT technology requires a substantial investment in both hardware and software.
Additionally, integrating IoT devices with existing systems can be complex and time-consuming.
Data Security
One of the primary concerns with IoT implementation is data security.
The increased connectivity of IoT devices also increases the risk of cyber-attacks.
Manufacturers must ensure that their data is protected and that their networks are secure.
Implementing strong encryption and access controls can help mitigate these risks.
Interoperability
Interoperability is another challenge in IoT implementation.
Different IoT devices may use different communication protocols, making it difficult for them to work together seamlessly.
Standardizing communication protocols and ensuring compatibility between devices can help overcome this challenge.
Skills and Training
The successful implementation of IoT in manufacturing also requires skilled personnel.
Manufacturers need to invest in training their workforce to handle and maintain IoT devices.
This may involve hiring new talent or providing existing employees with additional training.
The Future of IoT in Manufacturing
The future of IoT in manufacturing looks promising.
As technology continues to advance, the capabilities of IoT devices will only improve.
This will lead to even greater efficiencies and cost savings for manufacturers.
Advancements in AI and Machine Learning
One exciting development is the integration of AI and machine learning with IoT devices.
These technologies can analyze the data collected by IoT devices in more sophisticated ways, providing deeper insights and automating decision-making.
For example, AI algorithms can predict equipment failures with greater accuracy, improving maintenance schedules and reducing downtime.
5G Connectivity
The advent of 5G connectivity will also play a significant role in the future of IoT in manufacturing.
With faster data transmission speeds and lower latency, 5G will enable even more real-time monitoring and control.
This will enhance the ability to make instantaneous adjustments and improve overall efficiency.
In conclusion, the integration of IoT devices in manufacturing processes is transforming the industry.
From improving quality control to reducing downtime and optimizing energy usage, the benefits are substantial.
While there are challenges to consider, the potential for increased efficiency and cost savings makes IoT a valuable investment for manufacturers.
With advancements in technology, the future of IoT in manufacturing holds even greater promise.
資料ダウンロード
QCD調達購買管理クラウド「newji」は、調達購買部門で必要なQCD管理全てを備えた、現場特化型兼クラウド型の今世紀最高の購買管理システムとなります。
ユーザー登録
調達購買業務の効率化だけでなく、システムを導入することで、コスト削減や製品・資材のステータス可視化のほか、属人化していた購買情報の共有化による内部不正防止や統制にも役立ちます。
NEWJI DX
製造業に特化したデジタルトランスフォーメーション(DX)の実現を目指す請負開発型のコンサルティングサービスです。AI、iPaaS、および先端の技術を駆使して、製造プロセスの効率化、業務効率化、チームワーク強化、コスト削減、品質向上を実現します。このサービスは、製造業の課題を深く理解し、それに対する最適なデジタルソリューションを提供することで、企業が持続的な成長とイノベーションを達成できるようサポートします。
オンライン講座
製造業、主に購買・調達部門にお勤めの方々に向けた情報を配信しております。
新任の方やベテランの方、管理職を対象とした幅広いコンテンツをご用意しております。
お問い合わせ
コストダウンが利益に直結する術だと理解していても、なかなか前に進めることができない状況。そんな時は、newjiのコストダウン自動化機能で大きく利益貢献しよう!
(Β版非公開)