- お役立ち記事
- Optimizing Equipment Procurement for Improved Measurement Accuracy
Optimizing Equipment Procurement for Improved Measurement Accuracy
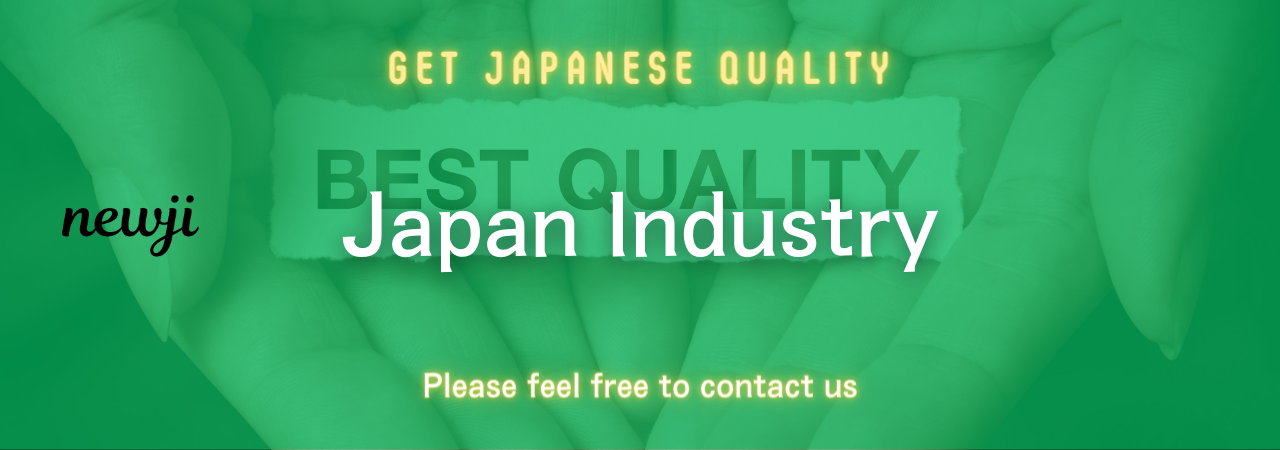
目次
Understanding Equipment Procurement
Procuring equipment is an essential aspect of any organization’s operations, especially for those dealing with complex measurements and data analysis.
Procurement isn’t merely about purchasing; it encompasses identifying needs, selecting the appropriate vendors, negotiating contracts, and maintaining relationships for future needs.
When done strategically, equipment procurement can significantly enhance measurement accuracy and, consequently, overall operational efficiency.
The Importance of Accuracy in Measurements
Measurement accuracy is vital in fields like manufacturing, engineering, research, and healthcare where precision can affect product quality, safety, and compliance with regulatory standards.
Inaccurate measurements can lead to errors that may result in product recalls, costly reworks, and even legal issues.
Therefore, optimizing equipment procurement with an eye on improving measurement accuracy can prevent these pitfalls.
Identifying Key Equipment Needs
The first step in optimizing procurement is to understand the specific measurement needs of your organization.
This involves assessing current equipment capabilities and recognizing areas where accuracy needs improvement.
Are current instruments providing the precision required, or is there room for upgrades?
Listing precise specifications, such as resolution, range, and sensitivity, will guide procurement in selecting the best-suited equipment.
Engaging with Stakeholders
Effective procurement strategies involve engaging with stakeholders across various departments.
Engineers, technicians, quality assurance personnel, and procurement specialists should collaborate to ensure that everyone has the necessary input on equipment requirements.
Regular meetings and communication help in understanding the practical challenges faced on the ground, which might not be evident to procurement teams alone.
Evaluating Vendor Options
Once the equipment needs are clearly defined, the next step involves evaluating potential vendors.
Quality, reliability, and reputation of vendors should be critically assessed.
Does the vendor offer equipment that meets the set specifications?
Is there after-sale support, including training and maintenance?
Vendors who provide full support, including calibration and technical assistance, are often more beneficial in the long run.
Cost Vs. Quality Considerations
While cost-effectiveness is a crucial factor, it should not overshadow quality concerns.
Cheaper equipment may initially seem more appealing, but if it fails to deliver accurate measurements, the potential costs associated with errors could outweigh the savings.
Focus on the total cost of ownership, including maintenance, repairs, and lifecycle rather than just the upfront cost.
Ensuring Compliance and Standards
In regulated industries, ensuring compliance with industry standards and regulations is non-negotiable.
Procurement must ensure that all equipment meets national and international standards and certifications.
This not only ensures measurement accuracy but also aids in maintaining operational credibility and avoiding possible penalties.
Training and Skill Development
New equipment often comes with a learning curve.
Providing adequate training for users is crucial for maximizing the new equipment’s capabilities.
Training must cover usage, maintenance, and troubleshooting to avoid any mishaps that can affect measurement accuracy.
Consider involving vendor-provided training programs, which are designed to cover all aspects comprehensively.
Regular Calibration and Maintenance
Once installed, regular calibration and maintenance routines are necessary to maintain equipment at peak performance.
Calibration ensures that the equipment’s performance remains aligned with the required measurement accuracy.
Scheduling regular maintenance checks prevents unexpected breakdowns and extends the equipment’s useful life.
Data Management and Analysis
Utilizing advanced data management and analysis tools can also contribute to improving measurement accuracy.
Ensure your organization leverages software solutions that can integrate seamlessly with the equipment to process and analyze data efficiently.
Data analytics tools help in identifying measurement drift and potential anomalies, thus guiding timely corrective actions.
Reviewing Procurement Processes
Regular reviews of procurement processes are essential for continual improvement and adaptation to changing organizational needs and technological advancements.
Feedback from equipment users should be solicited and analyzed.
Consider implementing a system of metrics and KPIs to evaluate procurement efficiency, accuracy improvements, and equipment performance.
Strategic Partnerships
Forming strategic partnerships with key vendors can offer significant benefits.
Long-term relationships encourage vendors to invest in understanding your requirements in depth, often leading to customized solutions that enhance measurement accuracy.
Such partnerships may also offer favorable terms and priority in service and support.
Conclusion
Optimizing equipment procurement for improved measurement accuracy involves a multi-faceted approach.
From understanding specific needs and engaging stakeholders, to training personnel and forming strategic vendor partnerships, each step is critical.
By focusing on these strategies, organizations can ensure they procure the right equipment, leading to enhanced measurement accuracy and successful operational outcomes.
Always aim to balance cost, quality, compliance, and user competency to meet the highest standards.
資料ダウンロード
QCD調達購買管理クラウド「newji」は、調達購買部門で必要なQCD管理全てを備えた、現場特化型兼クラウド型の今世紀最高の購買管理システムとなります。
ユーザー登録
調達購買業務の効率化だけでなく、システムを導入することで、コスト削減や製品・資材のステータス可視化のほか、属人化していた購買情報の共有化による内部不正防止や統制にも役立ちます。
NEWJI DX
製造業に特化したデジタルトランスフォーメーション(DX)の実現を目指す請負開発型のコンサルティングサービスです。AI、iPaaS、および先端の技術を駆使して、製造プロセスの効率化、業務効率化、チームワーク強化、コスト削減、品質向上を実現します。このサービスは、製造業の課題を深く理解し、それに対する最適なデジタルソリューションを提供することで、企業が持続的な成長とイノベーションを達成できるようサポートします。
オンライン講座
製造業、主に購買・調達部門にお勤めの方々に向けた情報を配信しております。
新任の方やベテランの方、管理職を対象とした幅広いコンテンツをご用意しております。
お問い合わせ
コストダウンが利益に直結する術だと理解していても、なかなか前に進めることができない状況。そんな時は、newjiのコストダウン自動化機能で大きく利益貢献しよう!
(Β版非公開)